What is PCB Impedance and Why Does It Matter?
PCB impedance refers to the opposition to the flow of electrical current through the copper traces on a printed circuit board (PCB). It is a critical factor in high-speed digital designs, as well as in analog circuits that deal with radio frequency (RF) signals. Controlling PCB impedance is essential for ensuring signal integrity, minimizing reflections, and preventing crosstalk between adjacent traces.
When a signal travels along a trace on a PCB, it encounters resistance, capacitance, and inductance. These factors combine to create the characteristic impedance of the trace. If the impedance of the trace does not match the impedance of the source and the load, signal reflections can occur, leading to distortion, noise, and potential signal integrity issues.
The Importance of Impedance Matching
Impedance matching is the process of designing PCB traces to have a specific characteristic impedance that matches the impedance of the source and the load. This is typically done by controlling the width, thickness, and spacing of the traces, as well as the properties of the PCB substrate material.
Proper impedance matching is crucial for several reasons:
- Signal Integrity: Matched impedances minimize signal reflections, ensuring that the signal reaches its destination with minimal distortion.
- Reduced EMI: Impedance-controlled traces help reduce electromagnetic interference (EMI) by minimizing the amount of energy radiated from the traces.
- Faster Signal Propagation: Matched impedances allow signals to propagate faster along the traces, enabling higher-speed communication.
- Improved Reliability: By reducing signal reflections and EMI, impedance control contributes to the overall reliability of the electronic system.
Factors Affecting PCB Impedance
Several factors influence the characteristic impedance of a PCB trace. Understanding these factors is essential for designing impedance-controlled traces.
Trace Geometry
The geometry of the trace, including its width, thickness, and cross-sectional shape, plays a significant role in determining its characteristic impedance. In general, wider traces have lower impedance, while narrower traces have higher impedance. The thickness of the trace also affects impedance, with thicker traces having lower impedance than thinner traces.
PCB Substrate Material
The properties of the PCB substrate material, such as its dielectric constant (Dk) and dissipation factor (Df), impact the characteristic impedance of the traces. Materials with higher Dk values, such as FR-4, result in lower impedance traces compared to materials with lower Dk values, like Rogers laminates.
Trace Spacing
The spacing between adjacent traces affects their mutual capacitance and inductance, which in turn influences their characteristic impedance. Traces that are closer together have higher mutual capacitance and lower impedance, while traces that are farther apart have lower mutual capacitance and higher impedance.
Stackup Configuration
The arrangement of signal layers, ground planes, and power planes in a PCB stackup can also impact trace impedance. The presence of ground and power planes near signal traces can affect their characteristic impedance by altering the effective dielectric constant of the surrounding medium.
Calculating PCB Trace Impedance
To design impedance-controlled traces, it is necessary to calculate the required trace width and spacing for a given target impedance and PCB stackup. Several methods can be used for this purpose, ranging from simple equations to sophisticated field solver simulations.
Microstrip Trace Impedance Calculation
Microstrip traces are PCB traces that run on an outer layer of the board, with a ground plane beneath them. The characteristic impedance of a microstrip trace can be approximated using the following equation:
Z₀ = 87 / √(ɛᵣ + 1.41) × ln(5.98 × h / (0.8 × w + t))
Where:
– Z₀ is the characteristic impedance in ohms (Ω)
– ɛᵣ is the relative dielectric constant of the substrate material
– h is the height of the substrate between the trace and the ground plane in mils
– w is the width of the trace in mils
– t is the thickness of the trace in mils
Stripline Trace Impedance Calculation
Stripline traces are PCB traces that run on an inner layer of the board, sandwiched between two ground planes. The characteristic impedance of a stripline trace can be approximated using the following equation:
Z₀ = 60 / √ɛᵣ × ln(4 × h / (0.67 × π × (0.8 × w + t)))
Where:
– Z₀ is the characteristic impedance in ohms (Ω)
– ɛᵣ is the relative dielectric constant of the substrate material
– h is the height of the substrate between the trace and the ground planes in mils
– w is the width of the trace in mils
– t is the thickness of the trace in mils
Field Solver Simulations
For more accurate impedance calculations, especially in complex PCB stackups or when dealing with differential traces, field solver simulations can be used. These simulations use numerical methods to solve Maxwell’s equations and calculate the electromagnetic fields surrounding the traces. Popular field solver software includes:
- Keysight ADS
- Ansys HFSS
- Cadence Sigrity
- Mentor Graphics HyperLynx
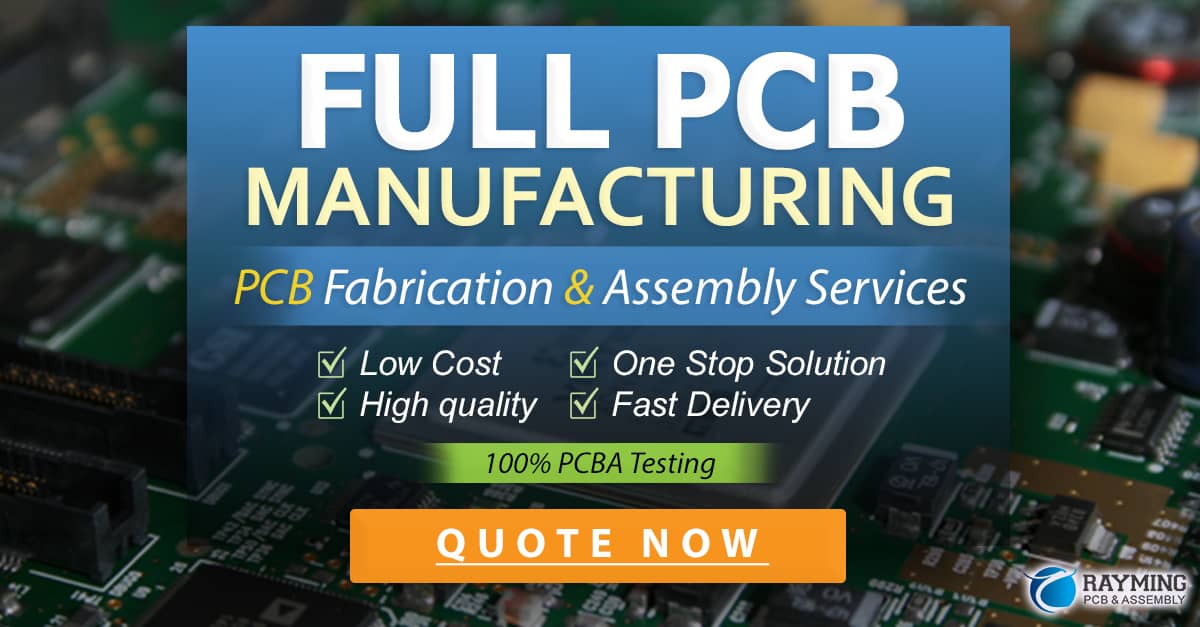
Implementing Impedance Control in PCB Design
To successfully implement impedance control in a PCB design, follow these steps:
- Determine the target impedance for your traces based on the requirements of your application and the components being used.
- Choose a suitable PCB substrate material with known dielectric properties (Dk and Df) that can accommodate your desired trace geometry and impedance.
- Design your PCB stackup, considering the number of layers, the arrangement of signal, ground, and power planes, and the spacing between them.
- Calculate the required trace width and spacing for your target impedance using the appropriate equations or field solver simulations.
- Create a set of PCB design rules that specify the trace width, spacing, and routing constraints for each impedance-controlled net in your design.
- Route your PCB, adhering to the design rules and ensuring that your traces maintain a consistent impedance throughout their length.
- Perform post-layout simulations to verify that your routed traces meet the target impedance and signal integrity requirements.
- Communicate your impedance control requirements to your PCB fabricator, specifying the target impedance, trace geometry, and any special manufacturing considerations.
Impedance Control Manufacturing Considerations
Achieving accurate impedance control in a manufactured PCB requires close collaboration with your PCB fabricator. Several manufacturing factors can affect the impedance of your traces, and it is essential to communicate your requirements clearly to ensure the best possible results.
Copper Thickness Tolerance
The thickness of the copper traces on your PCB can vary due to manufacturing tolerances. This variation can affect the impedance of your traces, so it is important to specify the acceptable copper thickness tolerance to your fabricator. Typically, a tolerance of ±10% is acceptable for most impedance-controlled designs.
Dielectric Thickness Tolerance
The thickness of the PCB substrate material between the traces and the ground or power planes can also vary due to manufacturing tolerances. This variation can impact the impedance of your traces, so it is crucial to specify the acceptable dielectric thickness tolerance to your fabricator. A tolerance of ±10% is usually sufficient for most designs.
Etching Process Control
The etching process used to remove unwanted copper from the PCB can affect the width and shape of your traces, which in turn can impact their impedance. To minimize this effect, your fabricator should use a well-controlled etching process, such as liquid photoimageable (LPI) solder mask or direct imaging (DI) dry film.
Impedance Testing
To verify that your manufactured PCB meets your impedance requirements, your fabricator should perform impedance testing on a sample of your boards. This testing typically involves using a time-domain reflectometer (TDR) to measure the characteristic impedance of your traces and compare it to your specified target impedance.
FAQ
1. What is the difference between microstrip and stripline traces?
Microstrip traces run on the outer layers of a PCB, with a ground plane beneath them. Stripline traces run on the inner layers of a PCB, sandwiched between two ground planes. Microstrip traces are easier to route and have lower manufacturing costs, but they are more susceptible to EMI and have higher dispersion than stripline traces.
2. Can I use the same trace width for all my impedance-controlled traces?
Not necessarily. The required trace width for a given target impedance depends on several factors, including the PCB substrate material, the trace thickness, and the spacing between the trace and the ground or power planes. It is important to calculate the appropriate trace width for each impedance-controlled net in your design.
3. What is the typical impedance for high-speed digital signals?
The typical impedance for high-speed digital signals, such as those used in HDMI, USB, and PCIe interfaces, is 100 Ω differential or 50 Ω single-ended.
4. Can I use FR-4 for impedance-controlled designs?
Yes, FR-4 is a popular choice for impedance-controlled designs due to its low cost and wide availability. However, FR-4 has higher dielectric losses and a more variable Dk compared to high-performance materials like Rogers laminates. This can make it more challenging to achieve tight impedance control and maintain signal integrity at very high frequencies.
5. How do I specify my impedance control requirements to my PCB fabricator?
To specify your impedance control requirements, provide your PCB fabricator with a detailed stackup diagram that includes the target impedance for each controlled layer, the trace geometry (width, thickness, and spacing), and the acceptable tolerances for copper thickness and dielectric thickness. Also, specify any special requirements for the etching process, such as the use of LPI solder mask or DI dry film. Finally, request impedance testing on a sample of your manufactured boards to verify that they meet your requirements.
Factor | Effect on Impedance |
---|---|
Trace Width | Wider traces have lower impedance; narrower traces have higher impedance |
Trace Thickness | Thicker traces have lower impedance; thinner traces have higher impedance |
Dielectric Constant (Dk) | Higher Dk results in lower impedance; lower Dk results in higher impedance |
Dielectric Thickness | Thicker dielectric results in higher impedance; thinner dielectric results in lower impedance |
Trace Spacing | Closer spacing results in higher mutual capacitance and lower impedance; wider spacing results in lower mutual capacitance and higher impedance |
PCB Material | Typical Dk | Typical Df | Comments |
---|---|---|---|
FR-4 | 4.2 – 4.5 | 0.02 | Low cost, widely available, suitable for most applications |
Rogers 4350B | 3.48 | 0.0037 | Low loss, stable Dk, suitable for high-frequency applications |
Isola I-Tera MT40 | 3.45 – 3.60 | 0.0030 | Low loss, stable Dk, suitable for high-speed digital applications |
Nelco N4000-13 SI | 3.7 | 0.009 | Low loss, stable Dk, suitable for high-speed digital and RF applications |
By understanding the factors that affect PCB impedance, calculating trace geometries, and working closely with your PCB fabricator, you can successfully implement impedance control in your designs and ensure optimal signal integrity and reliability.
0 Comments