Introduction to PCB Fabrication
Printed Circuit Board (PCB) fabrication is the process of creating electronic circuits by etching conductive pathways onto a non-conductive substrate. PCBs are essential components in virtually all electronic devices, from simple consumer gadgets to complex industrial equipment. The PCB fabrication process involves several steps, each requiring precise control and adherence to strict quality standards to ensure the final product’s reliability and functionality.
In this comprehensive article, we will explore the various aspects of PCB fabrication, including the materials used, the manufacturing process, quality control measures, and the latest trends and technologies in the industry.
Materials Used in PCB Fabrication
Substrate Materials
The substrate is the foundation of a PCB, providing a stable and insulating base for the conductive pathways. The most common substrate materials used in PCB fabrication are:
- FR-4: A composite material made of woven fiberglass cloth and epoxy resin, offering excellent mechanical and electrical properties.
- Polyimide: A high-performance polymer known for its superior heat resistance and flexibility, ideal for applications requiring high reliability.
- Ceramic: Used in high-frequency and high-power applications due to its excellent thermal conductivity and low dielectric loss.
Conductive Materials
Conductive materials are used to create the pathways that carry electrical signals between components on the PCB. The most common conductive materials are:
- Copper: The primary choice for PCB fabrication due to its excellent electrical conductivity, thermal conductivity, and cost-effectiveness.
- Gold: Used in high-reliability applications or for surface finishes to prevent oxidation and improve solderability.
- Silver: Employed in specialized applications requiring high conductivity and low resistance.
Solder Mask and Silkscreen
- Solder Mask: A thin layer of polymer applied to the PCB surface to protect the copper traces from oxidation and prevent solder bridges during the assembly process.
- Silkscreen: A printed layer of text and symbols on the PCB surface that aids in component placement and identification during assembly and troubleshooting.
The PCB Fabrication Process
Design and Layout
The PCB fabrication process begins with the design and layout of the circuit. Engineers use specialized software to create schematic diagrams and translate them into physical layouts, determining the placement of components and routing of conductive pathways.
Substrate Preparation
The substrate material is cut to the desired size and cleaned to remove any contaminants that may affect the adhesion of the conductive material.
Copper Lamination
A thin layer of copper is laminated onto the substrate using heat and pressure. The copper layer can be applied to one or both sides of the substrate, depending on the design requirements.
Photoresist Application
A light-sensitive polymer, called photoresist, is applied to the copper layer. The photoresist is then exposed to UV light through a photomask, which contains the circuit pattern.
Etching
The exposed copper is etched away using a chemical solution, leaving behind the desired conductive pathways. The remaining photoresist is then removed, revealing the final circuit pattern.
Drilling
Holes are drilled through the PCB to accommodate through-hole components and provide interconnections between layers in multi-layer boards.
Plating
The drilled holes and exposed copper traces are plated with a thin layer of copper, followed by additional metals such as tin, nickel, or gold, to improve conductivity and protect against oxidation.
Solder Mask and Silkscreen Application
The solder mask is applied to the PCB surface and cured using UV light. The silkscreen is then printed onto the solder mask, providing component placement and identification information.
Surface Finish
A surface finish, such as HASL (Hot Air Solder Leveling), ENIG (Electroless Nickel Immersion Gold), or OSP (Organic Solderability Preservative), is applied to the exposed copper to prevent oxidation and enhance solderability.
Electrical Testing
The completed PCB undergoes electrical testing to ensure that all connections are properly formed and that the board functions as intended.
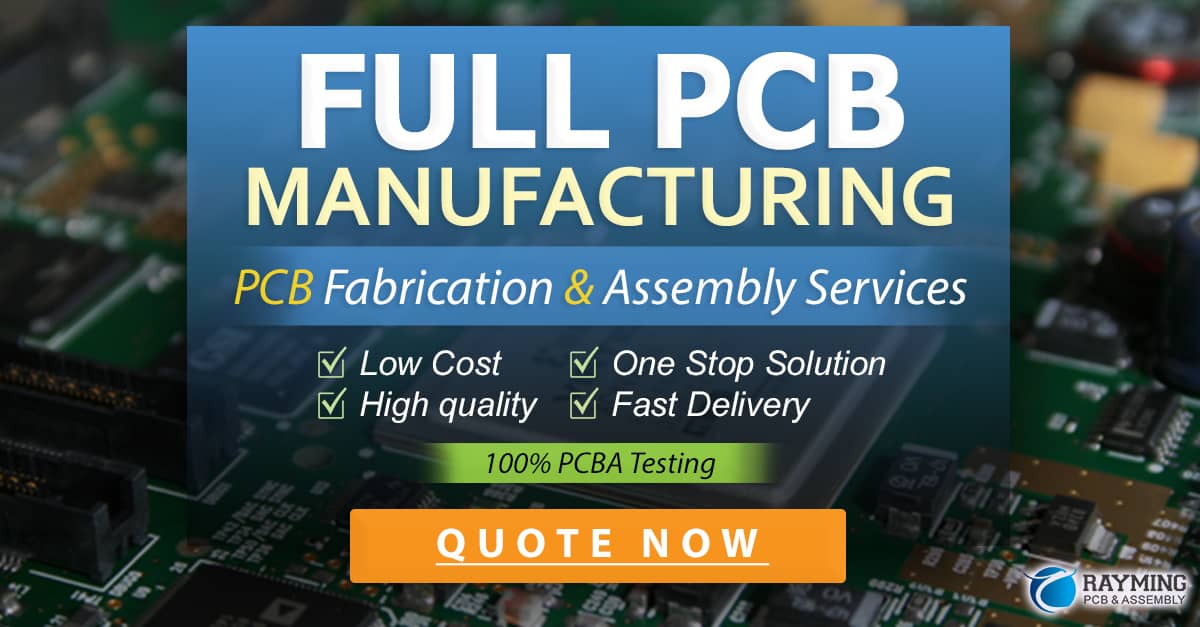
Quality Control in PCB Fabrication
Quality control is critical in PCB fabrication to ensure the reliability and performance of the final product. Several measures are implemented throughout the manufacturing process to maintain high-quality standards:
- Visual Inspection: Automated optical inspection (AOI) systems and manual visual inspections are used to identify defects such as shorts, opens, and misalignments.
- Electrical Testing: Flying probe tests, in-circuit tests, and functional tests are performed to verify the electrical integrity of the PCB.
- Microsectioning: Cross-sections of the PCB are examined under a microscope to assess the quality of plating, lamination, and drilling.
- Environmental Testing: PCBs are subjected to temperature cycling, humidity exposure, and vibration tests to ensure their durability and reliability in various operating conditions.
Latest Trends and Technologies in PCB Fabrication
The PCB fabrication industry is continually evolving to meet the demands of increasingly complex and miniaturized electronic devices. Some of the latest trends and technologies in PCB fabrication include:
- High-Density Interconnect (HDI): HDI PCBs feature finer pitch components, smaller vias, and thinner traces to accommodate the growing need for miniaturization and high-speed signal transmission.
- Embedded Components: Passive components, such as resistors and capacitors, are embedded within the PCB substrate to save space and improve signal integrity.
- Flexible and Rigid-Flex PCBs: Flexible PCBs and rigid-flex combinations offer increased design freedom and improved reliability in applications requiring flexibility or space constraints.
- 3D Printing: Additive manufacturing techniques are being explored for rapid prototyping and low-volume production of PCBs with complex geometries.
- Advanced Materials: New substrate and conductive materials, such as high-frequency laminates and graphene, are being developed to meet the demands of emerging technologies like 5G and the Internet of Things (IoT).
Frequently Asked Questions (FAQ)
1. What is the difference between a single-layer and a multi-layer PCB?
A single-layer PCB has conductive traces on only one side of the substrate, while a multi-layer PCB has conductive traces on both sides and additional internal layers. Multi-layer PCBs offer higher component density, improved signal integrity, and better EMI/RFI shielding compared to single-layer PCBs.
2. What is the role of vias in PCB fabrication?
Vias are conductive pathways that connect different layers of a multi-layer PCB. They allow electrical signals to pass between layers and facilitate more efficient routing of traces. Vias can be through-hole (extending through the entire board thickness) or blind/buried (connecting only certain layers).
3. What is the purpose of a solder mask in PCB fabrication?
A solder mask is a protective layer applied to the PCB surface to insulate the copper traces from accidental solder bridging during the assembly process. It also protects the traces from oxidation and environmental damage, while providing a contrasting background for the silkscreen legends.
4. How are PCBs tested for quality and reliability?
PCBs undergo several testing methods to ensure quality and reliability:
– Visual inspection using automated optical inspection (AOI) systems and manual checks
– Electrical testing, including flying probe tests, in-circuit tests, and functional tests
– Microsectioning to examine cross-sections of the PCB under a microscope
– Environmental testing, such as temperature cycling, humidity exposure, and vibration tests
5. What are the benefits of using flexible or rigid-flex PCBs?
Flexible and rigid-flex PCBs offer several advantages over traditional rigid PCBs:
– Increased design freedom, allowing for more complex and space-saving layouts
– Improved reliability, as they can withstand flexing and vibration without cracking or breaking
– Reduced weight and size, making them ideal for portable and wearable devices
– Simplified assembly, as they can replace multiple rigid PCBs and connectors with a single, integrated solution
Conclusion
PCB fabrication is a complex and multi-faceted process that plays a crucial role in the production of electronic devices. By understanding the materials, manufacturing steps, quality control measures, and latest trends in PCB fabrication, engineers and designers can create more reliable, efficient, and innovative electronic products.
As the demand for smaller, faster, and more complex electronic devices continues to grow, the PCB fabrication industry will need to adapt and innovate to meet these challenges. By embracing new technologies and materials, PCB manufacturers can stay at the forefront of this ever-evolving field and contribute to the advancement of electronic systems across a wide range of industries.
PCB Fabrication Process Steps | Description |
---|---|
Design and Layout | Creating schematic diagrams and physical layouts using specialized software |
Substrate Preparation | Cutting and cleaning the substrate material |
Copper Lamination | Applying a thin layer of copper to the substrate using heat and pressure |
Photoresist Application | Applying a light-sensitive polymer to the copper layer and exposing it to UV light through a photomask |
Etching | Removing the exposed copper using a chemical solution, leaving behind the desired conductive pathways |
Drilling | Creating holes through the PCB to accommodate components and provide interconnections between layers |
Plating | Applying a thin layer of copper and additional metals to the drilled holes and exposed traces |
Solder Mask and Silkscreen | Applying a protective solder mask and printing component placement and identification information |
Surface Finish | Applying a surface finish to the exposed copper to prevent oxidation and enhance solderability |
Electrical Testing | Verifying the electrical integrity and functionality of the completed PCB |
0 Comments