Introduction to PCB Drafting
Printed Circuit Board (PCB) drafting is a crucial process in the design and manufacture of electronic devices. It involves creating detailed drawings and schematics that provide a clear visual representation of the PCB layout, components, and connections. Adhering to established drafting standards ensures that PCB designs are accurate, consistent, and easily understood by all stakeholders involved in the manufacturing process.
In this article, we will explore five essential drafting standards that every PCB designer should follow to create high-quality PCB drawings.
1. Standardized Layer Naming and Stacking
1.1 Layer Naming Conventions
One of the fundamental aspects of PCB drafting is maintaining a consistent and standardized layer naming convention. Each layer in the PCB design should have a clear and descriptive name that reflects its purpose. Common layer names include:
- Top Layer (Top)
- Bottom Layer (Bottom)
- Ground Plane (GND)
- Power Plane (PWR)
- Signal Layers (Signal 1, Signal 2, etc.)
- Solder Mask Top (SMT)
- Solder Mask Bottom (SMB)
- Silkscreen Top (SST)
- Silkscreen Bottom (SSB)
Using consistent layer names throughout the design process helps to avoid confusion and ensures that all team members are on the same page.
1.2 Layer Stacking Order
In addition to standardized layer naming, it is essential to follow a proper layer stacking order. The layer stacking order defines the sequence in which the layers are arranged in the PCB. A typical layer stacking order for a four-layer PCB might look like this:
- Top Layer
- Ground Plane
- Power Plane
- Bottom Layer
The layer stacking order can vary depending on the specific requirements of the PCB design, such as signal integrity, power distribution, and EMI/EMC considerations. It is crucial to document and communicate the layer stacking order to the manufacturing team to ensure the correct fabrication of the PCB.
2. Schematic Symbol and Footprint Libraries
2.1 Schematic Symbol Libraries
Schematic symbol libraries are collections of graphical representations of electronic components used in the schematic design of a PCB. These symbols provide a visual abstraction of the component’s functionality and pin configuration. When creating schematic symbols, consider the following guidelines:
- Use industry-standard symbols whenever possible
- Ensure that the symbol accurately represents the component’s pin configuration
- Include relevant component information, such as part number and value
- Maintain consistent symbol sizing and orientation
Having a well-organized and standardized schematic symbol library streamlines the design process and improves the overall quality of the schematic.
2.2 Footprint Libraries
Footprint libraries contain the physical representations of components used in the PCB layout. A footprint defines the dimensions, pad sizes, and placement of a component on the PCB. When creating footprint libraries, keep the following points in mind:
- Use accurate component dimensions based on manufacturer datasheets
- Ensure that pad sizes and spacing comply with the component’s specifications
- Include relevant silkscreen information, such as component outlines and pin labels
- Maintain consistent footprint naming conventions
Having a comprehensive and accurate footprint library is essential for proper component placement and manufacturability of the PCB.
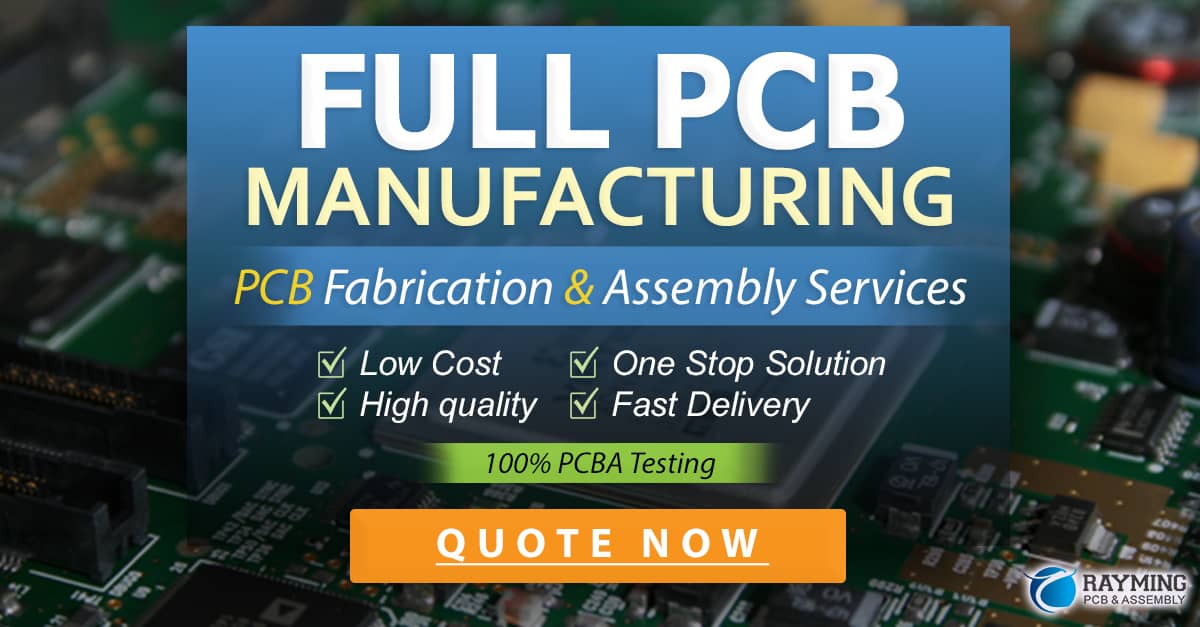
3. Dimensional Accuracy and Tolerances
3.1 Dimensional Accuracy
Dimensional accuracy is critical in PCB drafting to ensure that the manufactured board meets the intended design specifications. When creating PCB drawings, consider the following aspects of dimensional accuracy:
- Board outline dimensions
- Component placement coordinates
- Hole sizes and locations
- Trace widths and spacings
It is essential to use precise measurements and adhere to the specified dimensions to avoid manufacturing issues and ensure proper fit and functionality of the PCB.
3.2 Tolerances
Tolerances are the acceptable variations in dimensions that can occur during the manufacturing process. PCB designers must take into account the tolerances specified by the manufacturer to ensure that the PCB can be fabricated reliably. Common tolerances to consider include:
- Board outline tolerance
- Hole size tolerance
- Copper thickness tolerance
- Solder mask alignment tolerance
Incorporating appropriate tolerances into the PCB design helps to accommodate manufacturing variations and improves the overall yield and reliability of the final product.
4. Clearance and Creepage Distances
4.1 Clearance
Clearance refers to the minimum distance between conductive features on a PCB, such as traces, pads, and vias. Adequate clearance is necessary to prevent short circuits and ensure the electrical integrity of the board. When designing a PCB, consider the following clearance guidelines:
- Minimum trace-to-trace clearance
- Minimum trace-to-pad clearance
- Minimum pad-to-pad clearance
- Clearance between different voltage levels
The required clearance distances depend on factors such as the PCB’s operating voltage, environmental conditions, and manufacturing capabilities. It is crucial to consult with the PCB manufacturer and adhere to their recommended clearance guidelines.
4.2 Creepage
Creepage is the shortest distance between two conductive features along the surface of the PCB. It is particularly important in high-voltage applications where the risk of electrical breakdown is higher. When designing a PCB, consider the following creepage guidelines:
- Minimum creepage distance between different voltage levels
- Creepage distance requirements based on the PCB’s operating environment (e.g., humidity, altitude)
- Use of conformal coating or insulating materials to increase creepage distances
Ensuring adequate creepage distances helps to prevent electrical discharge and maintains the long-term reliability of the PCB.
5. Documentation and Annotation
5.1 Documentation
Proper documentation is essential for effective communication and collaboration among the PCB design team and with external stakeholders. When creating PCB documentation, consider the following elements:
- Bill of Materials (BOM): A comprehensive list of all components used in the PCB design, including part numbers, quantities, and descriptions.
- Assembly Drawings: Detailed illustrations showing the placement and orientation of components on the PCB.
- Fabrication Drawings: Drawings that provide the necessary information for PCB manufacturing, including layer stackup, drill sizes, and copper weights.
- Schematic Diagrams: Visual representations of the electrical connections and components in the PCB design.
Maintaining clear and concise documentation helps to streamline the manufacturing process and facilitates future revisions and maintenance of the PCB.
5.2 Annotation
Annotation involves adding relevant information and labels to the PCB drawings to enhance clarity and understanding. When annotating PCB drawings, consider the following practices:
- Component Labeling: Assign unique reference designators to each component on the schematic and PCB layout.
- Pin Numbering: Label component pins consistently with the manufacturer’s datasheet.
- Net Naming: Assign descriptive names to nets (electrical connections) to improve readability and troubleshooting.
- Revision Tracking: Include revision numbers and dates on the PCB drawings to track changes and updates.
Proper annotation helps to minimize errors, improves communication among team members, and facilitates the debugging and maintenance of the PCB.
Frequently Asked Questions (FAQ)
- What are the benefits of following PCB drafting standards?
Following PCB drafting standards offers several benefits, including: - Improved accuracy and consistency in PCB designs
- Enhanced communication and collaboration among team members
- Reduced errors and manufacturing issues
- Faster design and manufacturing processes
-
Increased reliability and quality of the final product
-
How can I ensure that my PCB design meets the required clearance and creepage distances?
To ensure that your PCB design meets the required clearance and creepage distances, follow these steps: - Consult with the PCB manufacturer and obtain their recommended guidelines for clearance and creepage distances
- Use PCB design software that includes design rule checks (DRC) to automatically verify clearance and creepage distances
- Carefully review the PCB layout and manually check critical areas for adequate clearance and creepage
-
Consider the operating voltage, environment, and manufacturing capabilities when determining the appropriate distances
-
What should I include in the Bill of Materials (BOM) for a PCB design?
A comprehensive Bill of Materials (BOM) should include the following information: - Component reference designators
- Manufacturer part numbers
- Detailed component descriptions
- Quantities of each component
- Supplier information (if applicable)
-
Any special notes or instructions
-
How can I maintain consistency in schematic symbols and footprints across different PCB designs?
To maintain consistency in schematic symbols and footprints, consider the following practices: - Develop and maintain a centralized library of schematic symbols and footprints
- Use standardized naming conventions for symbols and footprints
- Regularly update and maintain the library to ensure accuracy and completeness
- Share the library among team members and enforce its usage across different projects
-
Utilize version control systems to track changes and revisions to the library
-
What are some common mistakes to avoid when creating PCB drawings?
Some common mistakes to avoid when creating PCB drawings include: - Inconsistent or unclear layer naming and stacking
- Inaccurate or incomplete schematic symbols and footprints
- Neglecting dimensional accuracy and tolerances
- Insufficient clearance and creepage distances
- Lack of proper documentation and annotation
- Not adhering to manufacturer guidelines and specifications
By being aware of these common pitfalls and following the drafting standards outlined in this article, you can create high-quality PCB drawings that lead to successful manufacturing and reliable electronic devices.
Conclusion
PCB drafting is a critical aspect of electronic product development, and adhering to established drafting standards is essential for creating accurate, reliable, and manufacturable PCB designs. By following the five key drafting standards discussed in this article – standardized layer naming and stacking, schematic symbol and footprint libraries, dimensional accuracy and tolerances, clearance and creepage distances, and documentation and annotation – PCB designers can streamline the design process, improve communication, and ensure the success of their projects.
As the complexity of electronic devices continues to increase, the importance of proper PCB drafting standards becomes even more evident. By investing time and effort into developing and maintaining a robust set of drafting guidelines, PCB designers can create high-quality designs that meet the demands of modern electronics.
Standard | Description | Benefits |
---|---|---|
Layer Naming and Stacking | Use consistent and descriptive layer names and follow a standardized layer stacking order | Improved clarity and communication, easier manufacturing |
Schematic Symbol and Footprint Libraries | Maintain accurate and standardized libraries for schematic symbols and component footprints | Faster design process, reduced errors, improved consistency |
Dimensional Accuracy and Tolerances | Adhere to precise measurements and incorporate manufacturing tolerances | Ensured proper fit and functionality, higher manufacturing yield |
Clearance and Creepage Distances | Maintain adequate distances between conductive features to prevent short circuits and electrical breakdown | Improved electrical integrity and long-term reliability |
Documentation and Annotation | Create comprehensive documentation and annotate PCB drawings with relevant information | Enhanced communication, easier troubleshooting and maintenance |
By following these PCB drafting standards, designers can create robust and reliable PCB designs that meet the ever-evolving needs of the electronics industry. Embrace these standards in your PCB design process, and you’ll be well on your way to creating high-quality, manufacturable PCBs that drive innovation and success in your projects.
0 Comments