Introduction
Printed Circuit Board (PCB) design is a complex process that requires careful planning, attention to detail, and adherence to best practices. However, even experienced designers can make mistakes that can lead to costly rework, delays, and even product failures. In this article, we will discuss the top 5 mistakes to avoid in PCB design and how to prevent them.
Mistake #1: Inadequate Planning
One of the most common mistakes in PCB design is inadequate planning. Before starting the design process, it is essential to have a clear understanding of the project requirements, including the size, shape, and functionality of the PCB. Failing to plan properly can lead to delays, cost overruns, and even design failures.
How to Avoid Inadequate Planning
- Conduct a thorough requirements analysis before starting the design process
- Create a detailed project plan that includes timelines, milestones, and deliverables
- Involve all stakeholders in the planning process, including engineers, manufacturers, and end-users
- Use project management tools to track progress and identify potential issues early on
Mistake #2: Ignoring Design Rules
PCB design rules are a set of guidelines that ensure the manufacturability and reliability of the board. Ignoring these rules can lead to manufacturing defects, signal integrity issues, and even product failures.
How to Avoid Ignoring Design Rules
- Familiarize yourself with the design rules for your specific PCB manufacturer and assembly process
- Use PCB design software that includes design rule checks (DRC) to identify and correct violations
- Review the design with a manufacturer early in the process to ensure compliance with their specific requirements
- Conduct a final design review before releasing the design for manufacturing
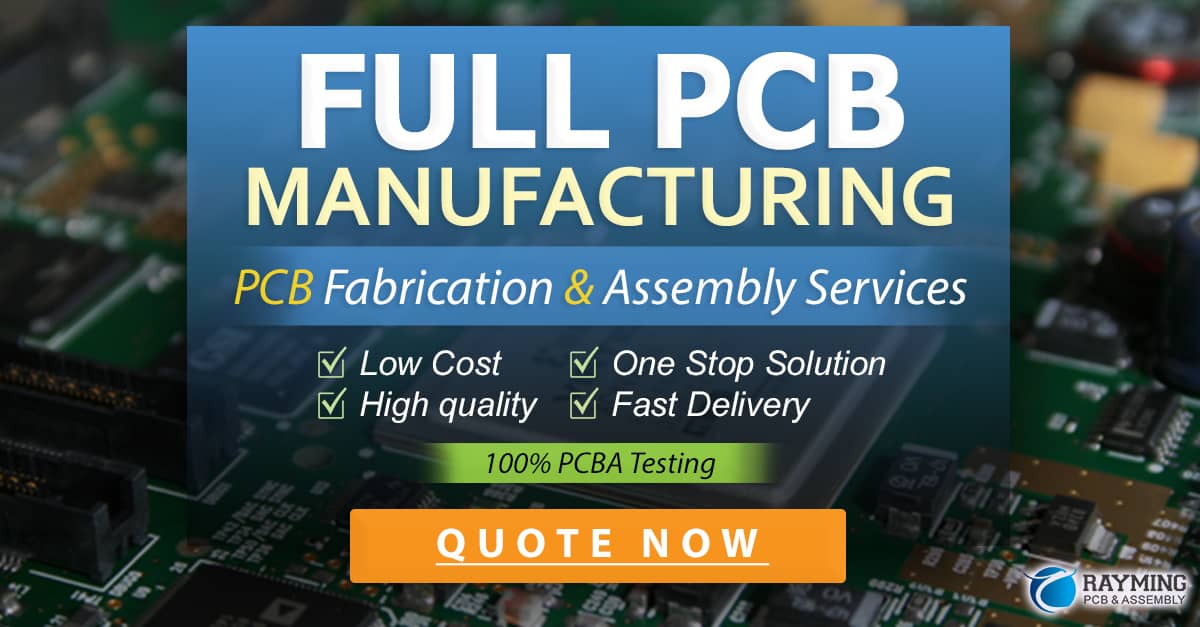
Mistake #3: Incorrect Component Placement
Incorrect component placement can lead to signal integrity issues, thermal problems, and even mechanical interference. It is essential to consider the placement of components carefully to ensure optimal performance and reliability.
How to Avoid Incorrect Component Placement
- Use a component placement strategy that considers signal integrity, thermal management, and mechanical constraints
- Place critical components close to their associated circuits to minimize signal delays and noise
- Use thermal simulation tools to identify potential heat sources and ensure adequate cooling
- Review the placement with a mechanical engineer to ensure clearance and accessibility for assembly and maintenance
Mistake #4: Inadequate Power and Ground Planes
Power and ground planes are critical for providing a low-impedance path for current flow and minimizing noise in the circuit. Inadequate power and ground planes can lead to signal integrity issues, EMI problems, and even product failures.
How to Avoid Inadequate Power and Ground Planes
- Use a multi-layer PCB design that includes dedicated power and ground planes
- Size the planes appropriately based on the current requirements of the circuit
- Use a star topology for power distribution to minimize voltage drops and noise
- Place decoupling capacitors close to the power pins of ICs to minimize high-frequency noise
Mistake #5: Inadequate Testing and Verification
Inadequate testing and verification can lead to product failures, recalls, and even legal liabilities. It is essential to conduct thorough testing and verification at every stage of the design process to ensure the reliability and performance of the PCB.
How to Avoid Inadequate Testing and Verification
- Develop a comprehensive test plan that covers all aspects of the PCB, including functionality, signal integrity, and reliability
- Use simulation tools to verify the design before physical prototyping
- Conduct thorough testing at the prototype stage, including environmental and stress testing
- Perform a final inspection and test before releasing the product for manufacturing
Mistake | Consequences | Prevention |
---|---|---|
Inadequate Planning | Delays, cost overruns, design failures | Thorough requirements analysis, detailed project plan, stakeholder involvement |
Ignoring Design Rules | Manufacturing defects, signal integrity issues, product failures | Familiarize with design rules, use DRC software, review with manufacturer |
Incorrect Component Placement | Signal integrity issues, thermal problems, mechanical interference | Use placement strategy, thermal simulation, mechanical review |
Inadequate Power and Ground Planes | Signal integrity issues, EMI problems, product failures | Multi-layer PCB, appropriate sizing, star topology, decoupling capacitors |
Inadequate Testing and Verification | Product failures, recalls, legal liabilities | Comprehensive test plan, simulation, prototype testing, final inspection |
Frequently Asked Questions (FAQ)
1. What is the most common mistake in PCB design?
The most common mistake in PCB design is inadequate planning. Failing to plan properly can lead to delays, cost overruns, and even design failures.
2. How can I ensure that my PCB design complies with manufacturing requirements?
To ensure compliance with manufacturing requirements, familiarize yourself with the design rules for your specific PCB manufacturer and assembly process. Use PCB design software that includes design rule checks (DRC) to identify and correct violations, and review the design with a manufacturer early in the process.
3. What are the consequences of incorrect component placement in PCB design?
Incorrect component placement can lead to signal integrity issues, thermal problems, and even mechanical interference. It is essential to consider the placement of components carefully to ensure optimal performance and reliability.
4. How can I minimize noise in my PCB design?
To minimize noise in your PCB design, use a multi-layer PCB that includes dedicated power and ground planes. Size the planes appropriately based on the current requirements of the circuit, and use a star topology for power distribution. Place decoupling capacitors close to the power pins of ICs to minimize high-frequency noise.
5. Why is testing and verification important in PCB design?
Testing and verification are critical in PCB design to ensure the reliability and performance of the final product. Inadequate testing and verification can lead to product failures, recalls, and even legal liabilities. It is essential to conduct thorough testing and verification at every stage of the design process, including simulation, prototype testing, and final inspection.
Conclusion
PCB design is a complex process that requires careful planning, attention to detail, and adherence to best practices. By avoiding the top 5 mistakes discussed in this article, designers can ensure the reliability, performance, and manufacturability of their PCBs. Remember to plan adequately, follow design rules, place components carefully, use appropriate power and ground planes, and conduct thorough testing and verification. By doing so, you can minimize the risk of costly rework, delays, and product failures, and deliver high-quality PCBs that meet the needs of your customers.
0 Comments