Understanding PCB Rework
PCB rework is the process of modifying or repairing a printed circuit board (PCB) after it has been manufactured. This process is often necessary when a defect is discovered during quality control inspections or when a design change is required. PCB rework can be a complex and delicate process, requiring specialized tools and expertise to ensure that the board is not damaged during the repair process.
Common Reasons for PCB Rework
There are several reasons why a PCB may require rework, including:
-
Manufacturing defects: Despite stringent quality control measures, manufacturing defects can occur during the PCB assembly process. These defects may include incorrect component placement, solder bridges, or damaged components.
-
Design changes: Sometimes, a design change may be necessary after the PCB has been manufactured. This could be due to a change in the product’s specifications or the discovery of a design flaw.
-
Component obsolescence: As technology advances, certain components may become obsolete or difficult to source. In these cases, a PCB may need to be reworked to accommodate a newer component.
-
Damage during handling: PCBs can be damaged during handling, storage, or transportation. This damage may require rework to restore the board’s functionality.
Tools and Equipment for PCB Rework
To perform PCB rework effectively, it is essential to have the right tools and equipment. Some of the most common tools used in PCB rework include:
-
Soldering iron: A soldering iron is a fundamental tool for PCB rework. It is used to melt solder and create electrical connections between components and the PCB.
-
Desoldering tools: Desoldering tools, such as desoldering pumps and desoldering wicks, are used to remove solder from components and pads on the PCB.
-
Tweezers and pliers: Tweezers and pliers are used to handle small components and wires during the rework process.
-
Magnifying glass or microscope: A magnifying glass or microscope is essential for inspecting the PCB and identifying defects or areas that require rework.
-
Cleaning supplies: Cleaning supplies, such as isopropyl alcohol and lint-free wipes, are used to clean the PCB before and after the rework process.
PCB Rework Techniques
There are several techniques used in PCB rework, depending on the type of repair required and the components involved. Some of the most common PCB rework techniques include:
Through-Hole Component Rework
Through-hole components are mounted on the PCB by inserting their leads through holes in the board and soldering them in place. To rework a through-hole component, follow these steps:
-
Desolder the component: Use a desoldering pump or desoldering wick to remove the solder from the component’s leads.
-
Remove the component: Once the solder has been removed, carefully lift the component from the board using tweezers or pliers.
-
Clean the pads: Use a soldering iron and desoldering wick to remove any remaining solder from the pads on the PCB.
-
Install the new component: Insert the new component’s leads through the holes in the board and solder them in place.
Surface-Mount Component Rework
Surface-mount components are mounted directly on the surface of the PCB without the need for through-holes. To rework a surface-mount component, follow these steps:
-
Desolder the component: Use a hot-air rework station or a soldering iron with a fine tip to melt the solder and remove the component from the board.
-
Clean the pads: Use a soldering iron and desoldering wick to remove any remaining solder from the pads on the PCB.
-
Apply solder paste: Apply a small amount of solder paste to the pads using a solder paste dispenser or a fine-tipped syringe.
-
Place the new component: Use tweezers to place the new component on the pads, ensuring that it is aligned correctly.
-
Reflow the solder: Use a hot-air rework station or a reflow oven to melt the solder paste and create a strong bond between the component and the PCB.
Trace Repair
Sometimes, the copper traces on a PCB can be damaged, causing an open circuit or a short circuit. To repair a damaged trace, follow these steps:
-
Locate the damaged area: Use a magnifying glass or microscope to locate the damaged area on the PCB.
-
Clean the area: Use isopropyl alcohol and a lint-free wipe to clean the area around the damaged trace.
-
Scrape away the solder mask: Use a sharp knife or a specialized scraping tool to remove the solder mask from the damaged area, exposing the copper trace.
-
Bridge the gap: Use a fine-gauge wire or conductive epoxy to bridge the gap in the damaged trace.
-
Solder the repair: Use a soldering iron to solder the wire or epoxy in place, ensuring a strong and reliable connection.
Best Practices for PCB Rework
To ensure successful PCB rework and minimize the risk of further damage to the board, follow these best practices:
-
Use the appropriate tools: Always use the appropriate tools for the specific rework task at hand. Using the wrong tools can lead to damage or poor-quality repairs.
-
Work in a clean environment: Perform PCB rework in a clean, well-lit, and well-ventilated workspace to minimize the risk of contamination and ensure accurate work.
-
Follow ESD precautions: Electrostatic discharge (ESD) can damage sensitive electronic components. Always follow proper ESD precautions, such as wearing an ESD wrist strap and using an ESD-safe workstation.
-
Inspect the work: After completing the rework, thoroughly inspect the PCB using a magnifying glass or microscope to ensure that the repair is sound and no new defects have been introduced.
-
Document the rework: Keep detailed records of all rework performed, including the specific components replaced, the techniques used, and any challenges encountered. This documentation can be invaluable for future reference and quality control purposes.
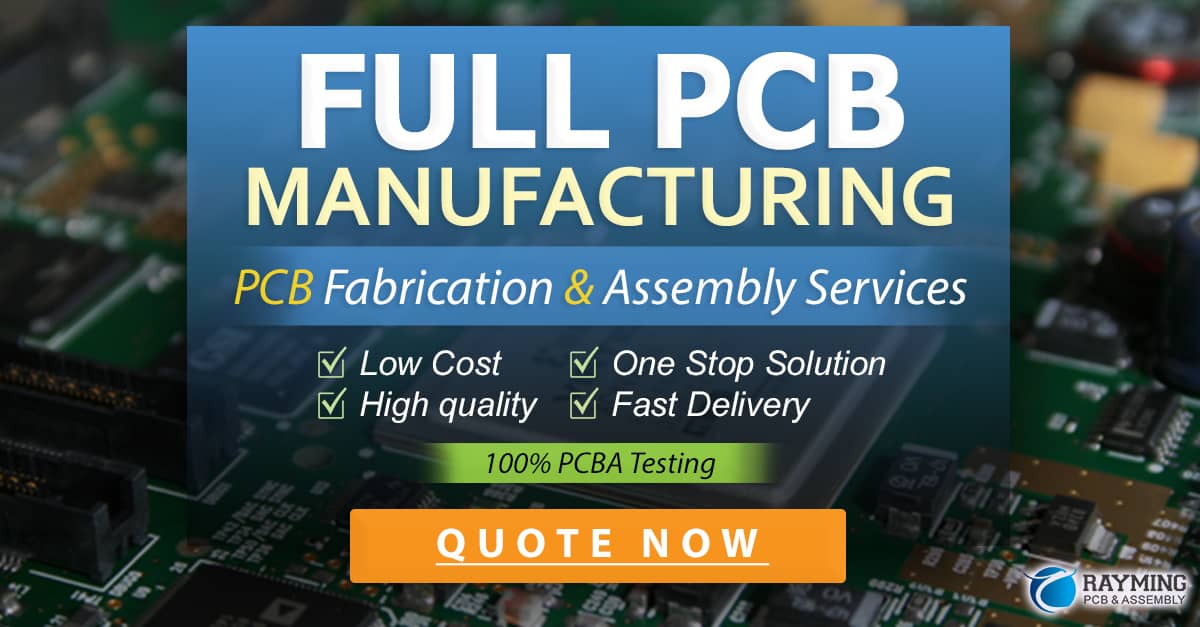
Common Challenges in PCB Rework
While PCB rework is a necessary process, it can present several challenges, including:
-
Component damage: Rework can be stressful for components, particularly sensitive components like ICs and connectors. Excessive heat or mechanical stress can damage these components, leading to further rework or scrap.
-
Pad lifting: During desoldering, the pads on the PCB can lift or delaminate from the board, making it difficult to create a reliable solder joint.
-
Solder bridges: When soldering components in close proximity, solder bridges can form between adjacent pads, causing short circuits.
-
Thermal damage: Excessive heat during rework can cause thermal damage to the PCB, such as delamination or charring of the substrate material.
To minimize these challenges, it is essential to use the appropriate tools and techniques, follow best practices, and work carefully and methodically.
PCB Rework and Quality Control
PCB rework is closely tied to quality control in the electronics manufacturing process. Effective rework can help to salvage boards that would otherwise be scrapped, reducing waste and increasing production yields. However, rework can also introduce new defects or quality issues if not performed properly.
To ensure that rework does not compromise the quality of the final product, it is important to have robust quality control measures in place. This may include:
-
Inspection: All reworked boards should be thoroughly inspected to ensure that the repair is sound and no new defects have been introduced.
-
Testing: Reworked boards should undergo the same functional testing as new boards to verify that they meet all performance and reliability requirements.
-
Documentation: Detailed records of all rework performed should be maintained for traceability and quality control purposes.
-
Continuous improvement: Quality control data from PCB rework should be analyzed to identify trends and opportunities for process improvement, helping to reduce the need for rework in the future.
By incorporating PCB rework into a comprehensive quality control strategy, electronics manufacturers can improve production yields, reduce waste, and ensure the highest levels of product quality and reliability.
FAQ
-
What is PCB rework?
PCB rework is the process of modifying or repairing a printed circuit board (PCB) after it has been manufactured. This process is often necessary when a defect is discovered during quality control inspections or when a design change is required. -
What tools are needed for PCB rework?
Some of the most common tools used in PCB rework include soldering irons, desoldering tools (such as desoldering pumps and desoldering wicks), tweezers, pliers, magnifying glasses or microscopes, and cleaning supplies like isopropyl alcohol and lint-free wipes. -
What are some common techniques used in PCB rework?
Common PCB rework techniques include through-hole component rework (desoldering the component, removing it, cleaning the pads, and installing a new component), surface-mount component rework (desoldering the component, cleaning the pads, applying solder paste, placing the new component, and reflowing the solder), and trace repair (locating the damaged area, cleaning it, scraping away the solder mask, bridging the gap, and soldering the repair). -
What are some best practices for PCB rework?
Best practices for PCB rework include using the appropriate tools, working in a clean environment, following ESD precautions, thoroughly inspecting the work, and documenting the rework process. -
How does PCB rework relate to quality control in electronics manufacturing?
PCB rework is closely tied to quality control in electronics manufacturing. Effective rework can help to salvage boards that would otherwise be scrapped, reducing waste and increasing production yields. However, rework must be performed properly to avoid introducing new defects or quality issues. Robust quality control measures, such as inspection, testing, documentation, and continuous improvement, are essential to ensure that rework does not compromise the quality of the final product.
PCB Rework Technique | Key Steps |
---|---|
Through-Hole Component Rework | 1. Desolder the component 2. Remove the component 3. Clean the pads 4. Install the new component |
Surface-Mount Component Rework | 1. Desolder the component 2. Clean the pads 3. Apply solder paste 4. Place the new component 5. Reflow the solder |
Trace Repair | 1. Locate the damaged area 2. Clean the area 3. Scrape away the solder mask 4. Bridge the gap 5. Solder the repair |
By understanding the various PCB rework techniques, best practices, and challenges, electronics manufacturers can effectively repair and modify PCBs while maintaining the highest levels of quality and reliability. Through the implementation of robust quality control measures and continuous improvement efforts, the need for PCB rework can be minimized, leading to increased production efficiency and customer satisfaction.
0 Comments