Introduction to PCB Assembly
PCB (Printed Circuit Board) assembly is the process of soldering or mounting electronic components onto a printed circuit board. This process is crucial in the manufacturing of electronic devices, as it enables the creation of complex circuits on a single board. PCB assembly companies specialize in this process, offering a range of services to help businesses bring their electronic products to market.
The PCB Assembly Process
The PCB assembly process typically involves several steps, including:
-
Solder Paste Printing: Solder paste, a mixture of tiny solder particles and flux, is applied to the PCB using a stencil printer. The paste is applied to the pads where the components will be placed.
-
Component Placement: The electronic components are placed onto the PCB using a pick-and-place machine. These machines use vacuum nozzles to pick up the components and place them precisely on the solder paste.
-
Reflow Soldering: The PCB is then passed through a reflow oven, which melts the solder paste and permanently attaches the components to the board. The temperature profile of the oven is carefully controlled to ensure proper soldering without damaging the components.
-
Inspection and Testing: After soldering, the PCB undergoes a visual inspection to check for any defects or misaligned components. Automated optical inspection (AOI) systems are often used for this purpose. The board may also undergo electrical testing to ensure proper functionality.
-
Final Assembly: If required, additional steps such as conformal coating, potting, or enclosure assembly may be performed to complete the final product.
Types of PCB Assembly
There are two main types of PCB assembly: through-hole and surface mount.
Through-Hole Assembly (THA)
Through-hole assembly involves inserting component leads through drilled holes in the PCB and soldering them to pads on the opposite side. This method is well-suited for larger components and provides strong mechanical connections. However, it is less space-efficient and slower than surface mount assembly.
Surface Mount Assembly (SMA)
Surface mount assembly involves placing components directly onto pads on the surface of the PCB and soldering them in place. This method allows for smaller components and higher component density, making it ideal for compact electronic devices. Surface mount assembly is faster and more automated than through-hole assembly.
Advantages of Outsourcing PCB Assembly
Outsourcing PCB assembly to a specialized company offers several advantages, including:
-
Cost Savings: Outsourcing eliminates the need to invest in expensive assembly equipment and hire skilled technicians, reducing overall production costs.
-
Expertise: PCB assembly companies have the knowledge and experience to handle complex projects and ensure high-quality results.
-
Scalability: Outsourcing allows businesses to easily scale production up or down based on demand, without the need to adjust in-house capacity.
-
Time Savings: By outsourcing PCB assembly, businesses can focus on their core competencies and leave the manufacturing process to the experts, resulting in faster time-to-market.
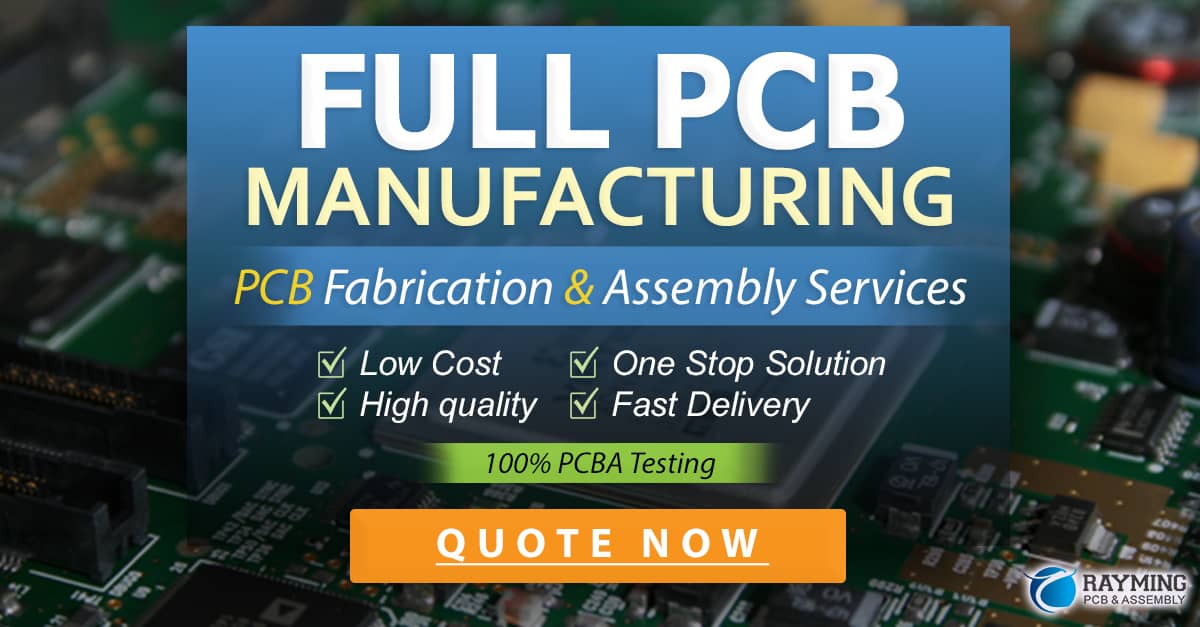
Choosing a PCB Assembly Company
When selecting a PCB assembly company, consider the following factors:
-
Experience: Look for a company with a proven track record of successfully completing projects similar to yours.
-
Capabilities: Ensure that the company has the necessary equipment and expertise to handle your specific requirements, such as component types, board sizes, and production volumes.
-
Quality Control: Choose a company that adheres to strict quality control standards and uses advanced inspection and testing methods to ensure the reliability of the final product.
-
Turnaround Time: Consider the company’s lead times and its ability to meet your deadlines consistently.
-
Customer Support: Select a company that provides excellent customer support and is responsive to your needs throughout the project.
The Importance of DFM in PCB Assembly
DFM (Design for Manufacturability) is a crucial aspect of PCB design that ensures the board can be efficiently and reliably manufactured. By incorporating DFM principles into the design process, potential manufacturing issues can be identified and addressed early on, reducing the risk of delays and additional costs during assembly.
Some key DFM considerations for PCB assembly include:
-
Component Selection: Choose components that are readily available and compatible with the chosen assembly process (through-hole or surface mount).
-
Pad and Trace Sizes: Ensure that pad and trace sizes are appropriate for the selected components and meet the manufacturer’s specifications.
-
Component Placement: Position components in a way that facilitates efficient assembly and minimizes the risk of defects, such as avoiding placing components too close to the board edge or under other components.
-
Solder Mask and Silkscreen: Use solder mask and silkscreen to protect the PCB and provide clear labeling for components and connectors.
By working closely with your PCB assembly company and incorporating their feedback during the design phase, you can optimize your board for manufacturability and ensure a smooth assembly process.
PCB Assembly Testing and Quality Control
To ensure the reliability and performance of the assembled PCBs, various testing and quality control methods are employed throughout the assembly process. Some common techniques include:
-
Automated Optical Inspection (AOI): AOI systems use high-resolution cameras and advanced image processing algorithms to inspect the PCB for defects such as missing components, incorrect component placement, and solder bridges.
-
X-Ray Inspection: X-ray inspection is used to detect defects that are not visible on the surface, such as voids in solder joints or hidden component defects.
-
In-Circuit Testing (ICT): ICT involves using a specialized fixture to make electrical contact with specific points on the PCB and testing the functionality of individual components and circuits.
-
Functional Testing: Functional testing verifies the overall performance of the assembled PCB by simulating real-world operating conditions and ensuring that the board meets the required specifications.
By implementing a rigorous quality control process, PCB assembly companies can identify and address issues early on, reducing the risk of defective products reaching the end-user.
PCB Assembly Industry Trends
The PCB assembly industry is constantly evolving, driven by advances in technology and changing market demands. Some current trends in the industry include:
-
Miniaturization: As electronic devices become smaller and more compact, there is a growing demand for miniaturized PCBs with high component density.
-
Flexible and Rigid-Flex PCBs: Flexible and rigid-flex PCBs are gaining popularity due to their ability to conform to unique shapes and withstand mechanical stress in applications such as wearables and automotive electronics.
-
High-Speed PCBs: With the increasing demand for faster data transmission and processing, PCB assembly companies are focusing on techniques to manufacture high-speed PCBs with controlled impedance and minimized signal distortion.
-
Sustainability: There is a growing emphasis on environmentally-friendly PCB assembly processes, such as the use of lead-free solder and the adoption of green manufacturing practices.
By staying up-to-date with these trends, PCB assembly companies can remain competitive and meet the evolving needs of their customers.
Frequently Asked Questions (FAQ)
-
What is the typical turnaround time for PCB assembly?
The turnaround time for PCB assembly varies depending on the complexity of the project, the quantity of boards required, and the workload of the assembly company. Typical turnaround times range from a few days to several weeks. It is essential to discuss your specific requirements with the assembly company to get an accurate estimate. -
How much does PCB assembly cost?
The cost of PCB assembly depends on several factors, including the complexity of the board, the number of components, the quantity of boards ordered, and the chosen assembly method (through-hole or surface mount). Generally, larger quantities and simpler designs result in lower per-unit costs. It is best to request a quote from the assembly company based on your specific project requirements. -
What file formats are required for PCB assembly?
PCB assembly companies typically require a set of files that include the Gerber files (which contain the PCB layout and layer information), drill files (which specify the location and size of holes), and a bill of materials (BOM) that lists all the required components. Some companies may also request additional files such as pick-and-place files or assembly drawings. It is important to discuss the required file formats with the assembly company before starting your project. -
Can I supply my own components for PCB assembly?
Yes, most PCB assembly companies allow customers to supply their own components, known as consigned parts. However, it is essential to ensure that the components are properly packaged, labeled, and meet the required specifications. The assembly company may also require additional documentation or testing to verify the quality of the consigned parts. -
What certifications should I look for when choosing a PCB assembly company?
When selecting a PCB assembly company, look for certifications that demonstrate their commitment to quality and adherence to industry standards. Some common certifications include ISO 9001 (quality management), ISO 14001 (environmental management), and IPC-A-610 (acceptability of electronic assemblies). Additionally, if your project has specific requirements, such as medical or military applications, ensure that the company has the necessary certifications and experience to meet those standards.
Conclusion
PCB assembly is a critical process in the production of electronic devices, and choosing the right PCB assembly company is essential for ensuring the success of your project. By understanding the different types of PCB assembly, the advantages of outsourcing, and the importance of DFM and quality control, you can make an informed decision when selecting a partner for your PCB assembly needs.
As the electronics industry continues to evolve, PCB assembly companies must adapt to new technologies and market demands. By staying up-to-date with the latest trends and continuously improving their processes, these companies can provide the high-quality, reliable PCB assembly services that businesses need to bring their innovative products to market.
PCB Assembly Method | Advantages | Disadvantages |
---|---|---|
Through-Hole Assembly (THA) | – Strong mechanical connections – Well-suited for larger components |
– Less space-efficient – Slower assembly process |
Surface Mount Assembly (SMA) | – Higher component density – Faster and more automated assembly – Ideal for compact electronic devices |
– Not suitable for all component types – Requires precise placement and soldering |
By carefully considering your project requirements and partnering with a reputable PCB assembly company, you can ensure that your electronic products are manufactured to the highest standards of quality and reliability.
0 Comments