Introduction to PCB AOI
Automated Optical Inspection (AOI) is a crucial technology in the manufacturing process of Printed Circuit Boards (PCBs). PCB AOI systems use advanced imaging techniques and sophisticated algorithms to detect and identify defects, ensuring the quality and reliability of the final product. In this comprehensive article, we will explore the role of AOI in PCB manufacturing, its benefits, types of AOI systems, and the future trends in this field.
What is PCB AOI?
PCB AOI is an automated process that uses high-resolution cameras and advanced image processing software to inspect PCBs for defects. The system captures images of the PCB at various stages of the manufacturing process and compares them to a reference image of a defect-free PCB. Any deviations from the reference image are identified as potential defects, which are then classified and reported for further analysis and repair.
Benefits of PCB AOI
The implementation of AOI in PCB manufacturing offers several benefits, including:
- Early defect detection: AOI systems can identify defects early in the manufacturing process, reducing the risk of producing faulty PCBs and minimizing rework costs.
- Improved quality: By detecting and eliminating defects, AOI ensures that the final PCB products meet the required quality standards, enhancing customer satisfaction and reducing warranty claims.
- Increased productivity: AOI systems can inspect PCBs much faster than manual inspection methods, allowing for higher production throughput and shorter lead times.
- Cost savings: Early defect detection and improved quality result in reduced scrap, rework, and warranty costs, leading to overall cost savings in PCB manufacturing.
Types of PCB AOI Systems
There are three primary types of PCB AOI systems, each with its own advantages and limitations:
2D AOI Systems
2D AOI systems use conventional imaging techniques to capture two-dimensional images of the PCB surface. These systems are cost-effective and suitable for detecting surface-level defects such as:
- Solder bridges
- Solder opens
- Component placement errors
- Incorrect component polarity
However, 2D AOI systems may struggle to detect defects in complex PCB designs or those with tall components that can obstruct the camera’s view.
3D AOI Systems
3D AOI systems employ advanced imaging technologies, such as laser triangulation or structured light, to capture three-dimensional data of the PCB surface. This enables the detection of defects that may be difficult to identify using 2D imaging, such as:
- Insufficient solder volume
- Lifted leads
- Coplanarity issues
- Warpage and twist
3D AOI systems offer improved defect detection capabilities but are generally more expensive than 2D systems.
Combination AOI Systems
Combination AOI systems integrate both 2D and 3D imaging technologies to provide a comprehensive inspection solution. These systems leverage the strengths of both techniques to detect a wide range of defects accurately. Combination AOI systems are particularly useful for inspecting complex PCB designs with a mix of surface-level and three-dimensional defects.
AOI in the PCB Manufacturing Process
AOI is typically implemented at multiple stages of the PCB manufacturing process to ensure the highest quality and reliability of the final product. The most common inspection points include:
Solder Paste Inspection (SPI)
SPI is performed after the solder paste is applied to the PCB but before component placement. AOI systems inspect the solder paste deposits for defects such as:
- Insufficient or excessive solder volume
- Solder bridging
- Solder paste alignment issues
Detecting and correcting these defects early in the process helps prevent component placement errors and improves the overall quality of the soldered joints.
Pre-Reflow Inspection
Pre-reflow inspection occurs after component placement but before the PCB enters the reflow oven. AOI systems check for defects such as:
- Missing or misaligned components
- Incorrect component polarity
- Solder bridging or insufficiency
Identifying these defects before the reflow process allows for timely repairs, reducing the risk of producing faulty PCBs.
Post-Reflow Inspection
Post-reflow inspection is conducted after the PCB has gone through the reflow oven and the solder joints have been formed. AOI systems inspect the soldered joints for defects such as:
- Solder bridges
- Solder opens
- Insufficient or excessive solder
- Lifted leads or tombstoning
This final inspection ensures that the PCB meets the required quality standards before it is sent for further assembly or packaging.
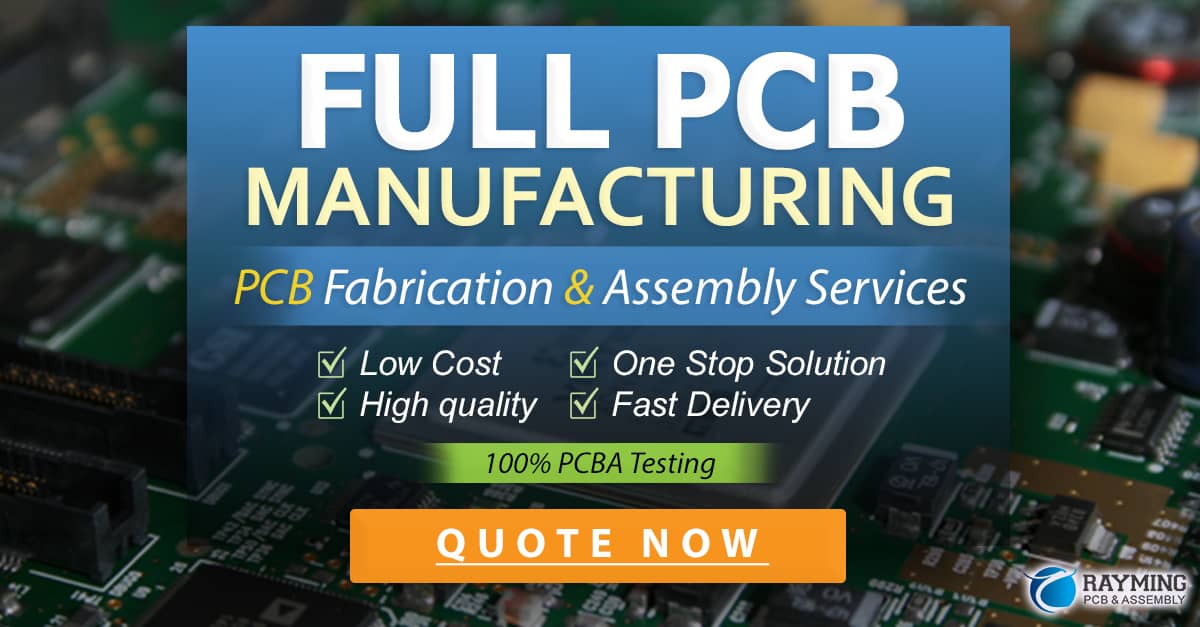
Challenges and Limitations of PCB AOI
While PCB AOI offers numerous benefits, there are some challenges and limitations to consider:
False Calls and Escapes
AOI systems may occasionally generate false calls (identifying a defect-free area as a defect) or allow escapes (failing to detect an actual defect). These errors can lead to unnecessary repairs or the release of faulty PCBs. To minimize false calls and escapes, it is essential to properly set up and calibrate the AOI system, as well as regularly review and update the defect library.
Component Compatibility
Some components, such as oddly shaped or transparent parts, may be challenging for AOI systems to inspect accurately. In these cases, alternative inspection methods, such as X-ray inspection or manual visual inspection, may be necessary to ensure the quality of the soldered joints.
Cost and Return on Investment
Implementing a PCB AOI system can be a significant investment, particularly for smaller manufacturing operations. It is crucial to carefully evaluate the costs and benefits of AOI and determine the return on investment based on factors such as production volume, PCB complexity, and quality requirements.
Future Trends in PCB AOI
As PCB designs become more complex and manufacturing processes continue to evolve, AOI technology must adapt to meet the changing needs of the industry. Some of the future trends in PCB AOI include:
Artificial Intelligence and Machine Learning
Integrating artificial intelligence (AI) and machine learning (ML) technologies into AOI systems can improve defect detection accuracy and reduce false calls and escapes. AI and ML algorithms can learn from historical data and adapt to new defect patterns, enabling more efficient and effective inspection processes.
Inline vs. Offline AOI
Inline AOI systems are integrated directly into the production line, inspecting PCBs in real-time as they move through the manufacturing process. Offline AOI systems, on the other hand, are standalone units that inspect PCBs in batches. As production speeds increase and the demand for real-time quality control grows, inline AOI systems are expected to become more prevalent in PCB manufacturing.
Integration with Other Inspection Technologies
Combining AOI with other inspection technologies, such as X-ray inspection or electrical testing, can provide a more comprehensive quality control solution. This integration allows for the detection of a wider range of defects and ensures that PCBs meet both visual and functional requirements.
Frequently Asked Questions (FAQ)
-
What is the difference between AOI and visual inspection?
AOI is an automated process that uses high-resolution cameras and advanced image processing software to inspect PCBs for defects, while visual inspection is a manual process performed by human operators. AOI is faster, more consistent, and can detect defects that may be difficult for human eyes to spot. -
Can AOI replace X-ray inspection?
While AOI is an effective inspection method for surface-level defects, it cannot detect internal defects or defects hidden under components. X-ray inspection is still necessary for identifying defects such as voids, cracks, or internal misalignments in soldered joints. -
How does AOI handle inspecting different PCB designs?
AOI systems use a reference image or CAD data of the PCB design to create inspection programs. These programs can be adapted to different PCB designs by updating the reference data and adjusting the inspection parameters. Some AOI systems also use adaptive algorithms that can automatically adjust to minor variations in PCB designs. -
What is the typical defect detection rate of AOI systems?
The defect detection rate of AOI systems can vary depending on factors such as the complexity of the PCB design, the type of components, and the quality of the inspection program. However, modern AOI systems can typically achieve defect detection rates of 90% or higher. -
How often should AOI systems be calibrated and maintained?
AOI systems should be regularly calibrated and maintained to ensure optimal performance and accuracy. The frequency of calibration and maintenance depends on factors such as the production volume, the operating environment, and the manufacturer’s recommendations. As a general rule, AOI systems should be calibrated at least once per shift and undergo thorough maintenance on a monthly or quarterly basis.
Conclusion
Automated Optical Inspection plays a vital role in ensuring the quality and reliability of PCBs in the manufacturing process. By detecting and identifying defects early, AOI systems help reduce rework costs, improve productivity, and ultimately lead to higher customer satisfaction. As PCB designs continue to evolve and become more complex, the importance of AOI will only grow, driving the development of more advanced inspection technologies and techniques.
By understanding the benefits, types, and applications of PCB AOI, manufacturers can make informed decisions about implementing this technology in their production processes. With the right AOI solution in place, PCB manufacturers can remain competitive in an increasingly demanding market and deliver high-quality products that meet the evolving needs of their customers.
0 Comments