Introduction to LED PCB
Light-emitting diode (LED) technology has revolutionized the lighting industry with its energy efficiency, durability, and versatility. The core of LED lighting lies in the printed circuit board (PCB) manufacturing process, which plays a crucial role in the performance and reliability of LED lighting systems. LED PCBs are specially designed to provide optimal thermal management, electrical conductivity, and mechanical support for LED components.
In recent years, the global application of LED lighting has experienced significant growth, driven by advancements in PCB manufacturing techniques and the increasing demand for energy-efficient lighting solutions. This article will explore the latest trends and innovations in LED PCB manufacturing and how they are shaping the future of LED lighting applications worldwide.
The Role of PCB Manufacturing in LED Lighting
Thermal Management
One of the most critical aspects of LED PCB design is thermal management. LEDs generate a significant amount of heat during operation, which can negatively impact their performance and lifespan if not properly dissipated. PCB manufacturers employ various techniques to ensure efficient heat dissipation, such as:
- Using high-thermal-conductivity materials like aluminum or copper for the PCB substrate
- Incorporating thermal vias to transfer heat from the LED components to the PCB’s backside
- Applying thermal interface materials (TIMs) between the LED and the PCB to enhance heat transfer
Electrical Conductivity
LED PCBs must provide a stable and reliable electrical connection to the LED components to ensure optimal performance. PCB manufacturers achieve this by:
- Using high-quality copper traces with appropriate thickness and width to minimize resistance
- Employing advanced surface finishes like immersion silver or electroless nickel/immersion gold (ENIG) to improve conductivity and solderability
- Implementing proper grounding and shielding techniques to minimize electromagnetic interference (EMI)
Mechanical Support
LED PCBs must also provide adequate mechanical support to the LED components, especially in applications subject to vibration or physical stress. PCB manufacturers address this by:
- Selecting appropriate PCB materials with sufficient rigidity and strength
- Designing the PCB layout to minimize mechanical stress on the LED components
- Utilizing reinforcement techniques like stiffeners or thicker PCB substrates in demanding applications
Advancements in LED PCB Manufacturing Techniques
High-Density Interconnect (HDI) PCBs
HDI PCBs feature finer trace widths, smaller via sizes, and higher layer counts compared to traditional PCBs. This technology enables the creation of more compact and efficient LED lighting systems, particularly in applications where space is limited, such as automotive lighting or miniature displays.
Flex and Rigid-Flex PCBs
Flexible and rigid-flex PCBs offer increased design freedom and mechanical durability for LED lighting applications. These PCBs can conform to complex shapes and withstand repeated flexing, making them ideal for wearable devices, flexible displays, and automotive interior lighting.
Metal Core PCBs (MCPCBs)
MCPCBs feature a metal substrate, typically aluminum, which provides excellent thermal conductivity for heat dissipation. This technology is particularly beneficial for high-power LED applications, such as street lighting or industrial illumination, where efficient thermal management is critical.
3D Printed Electronics
3D printing technology is emerging as a promising approach for LED PCB manufacturing. This technique allows for the creation of complex, three-dimensional PCB structures with integrated LED components, enabling novel lighting designs and improved thermal management.
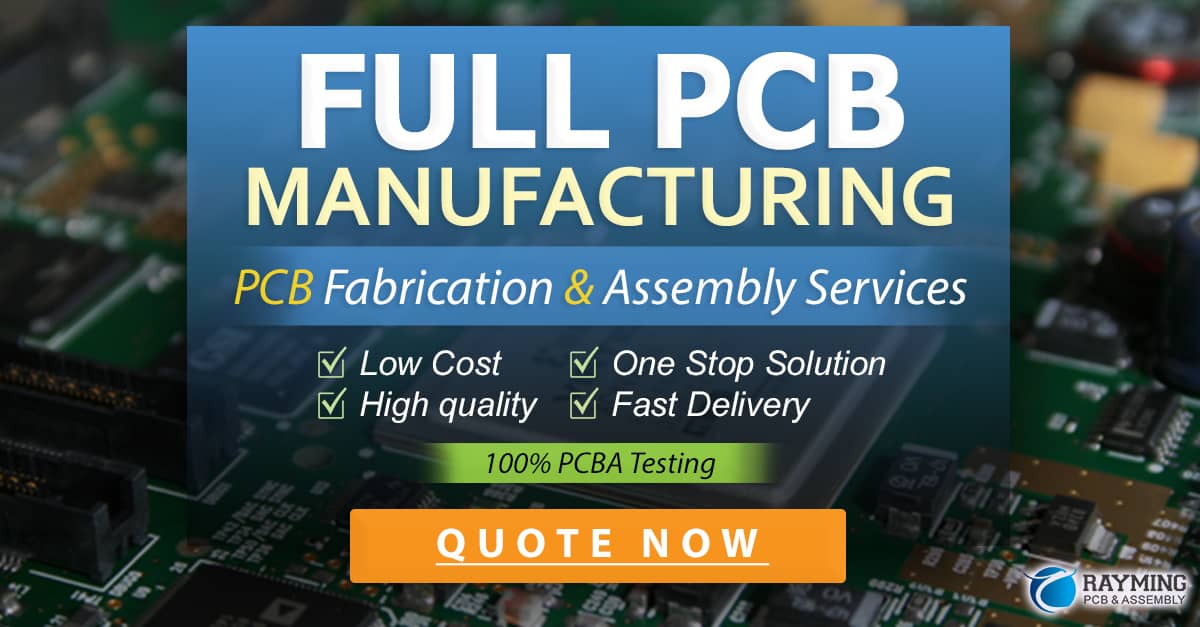
Global Trends in LED Lighting Applications
Smart Lighting Systems
The integration of LED lighting with smart home technologies and Internet of Things (IoT) devices is a growing trend worldwide. LED PCBs designed for smart lighting systems often incorporate additional features like wireless connectivity, sensors, and microcontrollers to enable remote control, energy monitoring, and adaptive lighting scenarios.
Horticultural Lighting
LED lighting has gained significant traction in the horticultural industry due to its ability to optimize plant growth and reduce energy consumption. LED PCBs designed for horticultural applications often feature specific wavelengths and spectral compositions tailored to the needs of different plant species.
Automotive Lighting
LED lighting has become increasingly prevalent in the automotive industry, both for interior and exterior applications. LED PCBs used in automotive lighting must meet stringent requirements for thermal management, vibration resistance, and long-term reliability. Advanced PCB manufacturing techniques, such as HDI and flexible PCBs, are essential for creating compact and durable automotive LED lighting systems.
Healthcare and Medical Devices
LED lighting is finding new applications in the healthcare sector, from surgical lighting to phototherapy devices. LED PCBs designed for medical applications must adhere to strict regulatory standards for safety, reliability, and biocompatibility. PCB manufacturers specializing in medical devices employ advanced quality control measures and use materials suitable for the medical environment.
Future Outlook for LED PCB Manufacturing
The future of LED PCB manufacturing is shaped by several key factors, including:
- Continued advancements in PCB materials and manufacturing processes to improve thermal management, electrical performance, and mechanical durability
- Growing demand for energy-efficient and smart lighting solutions driven by government regulations and consumer preferences
- Expansion of LED lighting applications into new sectors, such as agriculture, healthcare, and aerospace
- Integration of LED lighting with emerging technologies like AI, machine learning, and 5G networks to enable more intelligent and adaptive lighting systems
As the global market for LED lighting continues to grow, PCB manufacturers will play a crucial role in driving innovation and meeting the evolving needs of the industry.
FAQ
1. What are the key considerations when designing an LED PCB?
When designing an LED PCB, the main considerations include thermal management, electrical conductivity, and mechanical support. The PCB must effectively dissipate heat generated by the LEDs, provide stable and reliable electrical connections, and offer sufficient mechanical strength to withstand the application’s environmental conditions.
2. How do HDI PCBs benefit LED lighting applications?
HDI PCBs feature finer trace widths, smaller via sizes, and higher layer counts compared to traditional PCBs. This enables the creation of more compact and efficient LED lighting systems, which is particularly beneficial for applications where space is limited, such as automotive lighting or miniature displays.
3. What is the role of metal core PCBs (MCPCBs) in LED lighting?
Metal core PCBs (MCPCBs) feature a metal substrate, typically aluminum, which provides excellent thermal conductivity for heat dissipation. This technology is particularly beneficial for high-power LED applications, such as street lighting or industrial illumination, where efficient thermal management is critical to ensure optimal performance and longevity of the LEDs.
4. How are LED PCBs being used in smart lighting systems?
LED PCBs designed for smart lighting systems often incorporate additional features like wireless connectivity, sensors, and microcontrollers. This enables the integration of LED lighting with smart home technologies and Internet of Things (IoT) devices, allowing for remote control, energy monitoring, and adaptive lighting scenarios based on user preferences or environmental conditions.
5. What are the challenges faced by PCB manufacturers in the LED lighting industry?
PCB manufacturers in the LED lighting industry face several challenges, including:
- Keeping up with the rapid pace of technological advancements in LED components and manufacturing processes
- Meeting the diverse and stringent requirements of various LED lighting applications, such as thermal management, electrical performance, and mechanical durability
- Ensuring compliance with evolving industry standards and regulations for energy efficiency, safety, and environmental impact
- Managing supply chain complexities and cost pressures in a highly competitive global market
To overcome these challenges, PCB manufacturers must continually invest in research and development, collaborate closely with LED lighting designers and end-users, and adapt their processes and offerings to meet the changing needs of the industry.
Application | Key Requirements | Relevant PCB Technologies |
---|---|---|
Automotive Lighting | – Thermal management – Vibration resistance – Compact size |
– Metal Core PCBs (MCPCBs) – High-Density Interconnect (HDI) PCBs – Flexible PCBs |
Smart Lighting Systems | – Wireless connectivity – Sensor integration – Microcontroller compatibility |
– HDI PCBs – Flex and Rigid-Flex PCBs – Embedded components |
Horticultural Lighting | – Specific wavelengths – Spectral composition – Energy efficiency |
– Metal Core PCBs (MCPCBs) – High-quality LED components – Optimized PCB layouts |
Medical Devices | – Safety and reliability – Biocompatibility – Regulatory compliance |
– Medical-grade PCB materials – Stringent quality control – Specialized manufacturing processes |
In conclusion, the global application of LED lighting continues to expand and evolve, driven by advancements in PCB manufacturing techniques and the growing demand for energy-efficient, smart, and adaptable lighting solutions. As PCB manufacturers push the boundaries of thermal management, electrical performance, and mechanical durability, they enable the development of innovative LED lighting systems that cater to the unique requirements of various industries, from automotive and horticulture to healthcare and beyond.
By staying at the forefront of technological advancements, collaborating closely with LED lighting designers, and adapting to the ever-changing needs of the market, PCB manufacturers will continue to play a pivotal role in shaping the future of LED lighting worldwide. As the industry progresses, we can expect to see even more exciting developments in LED PCB manufacturing, paving the way for a brighter, smarter, and more sustainable future of lighting.
0 Comments