Introduction to Multilayer PCBs
A Multilayer PCB, short for Multilayer Printed Circuit Board, is a type of printed circuit board that consists of three or more conductive copper layers. These layers are laminated together with insulating materials, allowing for more complex circuit designs and higher component density compared to single or double-layer PCBs. Multilayer PCBs have become increasingly popular in modern electronics due to their ability to accommodate advanced circuitry in a compact form factor.
Advantages of Multilayer PCBs
-
Increased Circuit Density: Multilayer PCBs allow for a higher density of components and interconnections, enabling more complex circuits to be designed in a smaller space.
-
Improved Signal Integrity: By using dedicated layers for power and ground planes, multilayer PCBs can reduce electromagnetic interference (EMI) and improve signal integrity.
-
Enhanced Reliability: The compact and organized structure of multilayer PCBs reduces the risk of manufacturing defects and improves overall reliability.
-
Reduced Size and Weight: With the ability to stack multiple layers, multilayer PCBs can significantly reduce the size and weight of electronic devices.
Multilayer PCB Structure
A typical multilayer PCB consists of alternating layers of conductive copper and insulating materials. The most common insulating material used in multilayer PCBs is FR-4, a glass-reinforced epoxy laminate. The number of layers in a multilayer PCB can vary depending on the complexity of the circuit design, with some boards having up to 50 layers or more.
Layer Stack-up
The layer stack-up of a multilayer PCB refers to the arrangement of copper and insulating layers. A basic 4-layer PCB stack-up might look like this:
Layer | Material |
---|---|
Top Layer | Copper |
Prepreg | Insulating Material |
Inner Layer 1 | Copper |
Core | Insulating Material |
Inner Layer 2 | Copper |
Prepreg | Insulating Material |
Bottom Layer | Copper |
Signal Layers
Signal layers are the layers in a multilayer PCB that carry the electrical signals between components. These layers are typically located on the outer layers of the board, as well as on some inner layers, depending on the design requirements.
Power and Ground Planes
Power and ground planes are dedicated layers in a multilayer PCB that provide a low-impedance path for power distribution and grounding. These planes help to reduce EMI and improve signal integrity by minimizing the loop area between power and ground connections.
Multilayer PCB Design Considerations
When designing a multilayer PCB, several factors must be considered to ensure optimal performance and manufacturability.
Signal Integrity
Signal integrity is a critical aspect of multilayer PCB design. To maintain signal integrity, designers must consider factors such as:
- Trace width and spacing
- Impedance matching
- Crosstalk reduction
- Termination strategies
Power Distribution
Proper power distribution is essential for the reliable operation of a multilayer PCB. Designers should consider the following:
- Adequate power and ground plane sizing
- Decoupling capacitor placement
- Current-carrying capacity of traces
Thermal Management
As multilayer PCBs can have a high component density, thermal management becomes an important consideration. Designers should:
- Use thermal vias to dissipate heat from high-power components
- Consider the thermal conductivity of the PCB materials
- Incorporate heat sinks or other cooling solutions when necessary
Manufacturing Constraints
Multilayer PCB design must also take into account the limitations and capabilities of the manufacturing process. Some key considerations include:
- Minimum trace width and spacing
- Minimum via size and drill diameter
- Copper thickness and plating requirements
- Solder mask and silkscreen specifications
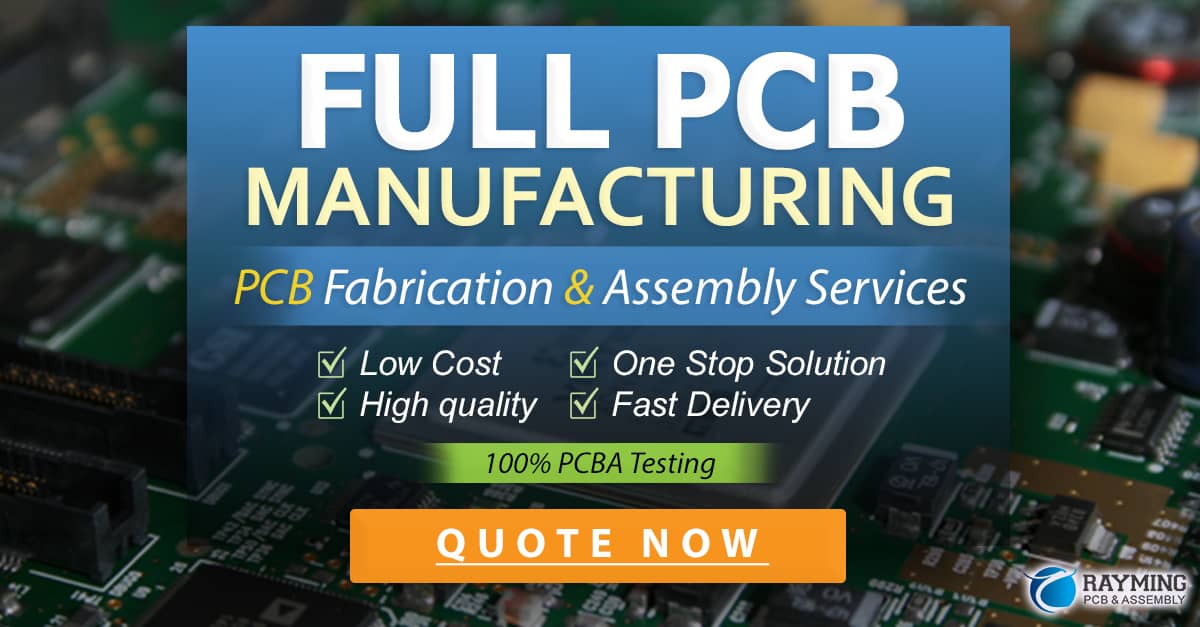
Multilayer PCB Manufacturing Process
The manufacturing process for multilayer PCBs is more complex than that of single or double-layer boards, due to the need to laminate multiple layers together.
Inner Layer Processing
-
Copper Clad Laminate Preparation: The process begins with the preparation of the copper clad laminate (CCL), which consists of a thin layer of copper foil bonded to an insulating substrate.
-
Dry Film Lamination: A photosensitive dry film is laminated onto the CCL using heat and pressure.
-
Exposure and Development: The dry film is exposed to UV light through a photomask, which hardens the exposed areas. The unexposed areas are then removed using a chemical developer, leaving behind the desired copper pattern.
-
Etching: The exposed copper is etched away using a chemical solution, leaving only the desired copper traces on the substrate.
Lamination and Drilling
-
Layer Alignment: The inner layers are aligned and stacked together with prepreg (pre-impregnated fiberglass) sheets between each layer.
-
Lamination: The stacked layers are laminated together under high pressure and temperature, bonding the layers into a solid board.
-
Drilling: Holes are drilled through the laminated board to create vias that connect the different layers.
Outer Layer Processing
-
Copper Deposition: A thin layer of copper is deposited onto the drilled board using electroless copper plating, followed by electroplating to achieve the desired copper thickness.
-
Patterning: The outer layers are patterned using a similar process to the inner layers, involving dry film lamination, exposure, development, and etching.
Finishing and Inspection
-
Solder Mask Application: A solder mask is applied to the board to protect the copper traces and prevent solder bridging.
-
Surface Finish: A surface finish, such as HASL (Hot Air Solder Leveling), ENIG (Electroless Nickel Immersion Gold), or OSP (Organic Solderability Preservative), is applied to the exposed copper to improve solderability and protect against oxidation.
-
Silkscreen: A silkscreen layer is applied to the board to add component identifiers, logos, and other markings.
-
Electrical Testing: The completed multilayer PCB undergoes electrical testing to ensure that all connections are correct and the board functions as intended.
Applications of Multilayer PCBs
Multilayer PCBs find applications in a wide range of industries and products, including:
- Consumer electronics (smartphones, laptops, gaming consoles)
- Automotive electronics (engine control units, infotainment systems)
- Medical devices (imaging equipment, patient monitors)
- Aerospace and defense systems (avionics, radar, and communication equipment)
- Industrial automation and control systems
Examples of Multilayer PCB Applications
Industry | Application | Benefits of Multilayer PCBs |
---|---|---|
Consumer Electronics | Smartphone Motherboard | High component density, compact size, improved signal integrity |
Automotive | Engine Control Unit (ECU) | Reliability, thermal management, signal integrity |
Medical | MRI Scanner Control Board | High-speed signaling, noise reduction, modularity |
Aerospace | Avionics Display Module | Weight reduction, reliability, complex functionality |
Future Trends in Multilayer PCB Technology
As electronic devices continue to advance and become more complex, multilayer PCB technology must also evolve to keep pace. Some of the key trends shaping the future of multilayer PCBs include:
High-Density Interconnect (HDI)
HDI PCBs feature finer trace widths, smaller vias, and higher layer counts than traditional multilayer PCBs. This allows for even greater component density and miniaturization, enabling the development of more advanced and compact electronic devices.
Embedded Components
Embedded component technology involves placing passive components, such as resistors and capacitors, inside the layers of a multilayer PCB. This can further reduce the size and weight of the board while improving electrical performance.
Advanced Materials
New materials, such as low-loss dielectrics and high-performance laminates, are being developed to improve the electrical and thermal performance of multilayer PCBs. These materials will enable faster signal speeds, lower power consumption, and better thermal management.
3D Printing
Additive manufacturing techniques, such as 3D printing, are being explored as a potential method for fabricating multilayer PCBs. This could enable faster prototyping, greater design flexibility, and the creation of complex, three-dimensional circuit structures.
Frequently Asked Questions (FAQ)
-
What is the difference between a multilayer PCB and a single or double-layer PCB?
A multilayer PCB consists of three or more conductive layers, while single and double-layer PCBs have one or two conductive layers, respectively. Multilayer PCBs offer higher component density, improved signal integrity, and better reliability compared to single or double-layer PCBs. -
How many layers can a multilayer PCB have?
The number of layers in a multilayer PCB can vary depending on the complexity of the circuit design. Most multilayer PCBs have between 4 and 12 layers, but some high-end designs can have up to 50 layers or more. -
What are the benefits of using power and ground planes in a multilayer PCB?
Power and ground planes provide a low-impedance path for power distribution and grounding, which helps to reduce electromagnetic interference (EMI) and improve signal integrity. By minimizing the loop area between power and ground connections, these planes contribute to the overall performance and reliability of the multilayer PCB. -
What is the most common insulating material used in multilayer PCBs?
The most common insulating material used in multilayer PCBs is FR-4, which is a glass-reinforced epoxy laminate. FR-4 offers good mechanical strength, thermal stability, and electrical insulation properties, making it well-suited for use in multilayer PCB construction. -
How does the manufacturing process for multilayer PCBs differ from that of single or double-layer PCBs?
The manufacturing process for multilayer PCBs is more complex than that of single or double-layer PCBs, as it involves the lamination of multiple layers together. The process includes inner layer processing, lamination, drilling, outer layer processing, and various finishing steps such as solder mask application and surface finishing. This complexity requires more advanced manufacturing equipment and techniques compared to the production of single or double-layer PCBs.
Conclusion
Multilayer PCBs have revolutionized the electronics industry by enabling the design and manufacture of more complex, compact, and reliable electronic devices. By offering increased circuit density, improved signal integrity, and enhanced thermal management, multilayer PCBs have become an essential component in a wide range of applications, from consumer electronics to aerospace and defense systems.
As technology continues to advance, the future of multilayer PCBs looks bright, with developments in high-density interconnects, embedded components, advanced materials, and 3D printing set to drive further innovation and growth in the field. By staying at the forefront of these trends, PCB designers and manufacturers can ensure that they are well-positioned to meet the ever-increasing demands of the modern electronics landscape.
0 Comments