Introduction to MicroVia PCB Technology
Microvia PCB technology has revolutionized the world of printed circuit boards (PCBs) by offering a solution for high-density interconnects and miniaturization. As electronic devices continue to shrink in size while increasing in functionality, microvia PCBs have become an essential component in modern electronics manufacturing. This article will delve into the design considerations and cost implications of microvia PCBs, providing a comprehensive overview for engineers, designers, and decision-makers.
What is a Microvia PCB?
A microvia is a small hole drilled in a PCB, typically with a diameter of less than 150 microns (0.15mm). These tiny vias enable the creation of high-density interconnects between layers in a PCB, allowing for more compact and complex designs. Microvia PCBs utilize these small vias to create multilayer boards with enhanced electrical performance and reduced size.
Advantages of Microvia PCBs
- Miniaturization: Microvias enable the creation of smaller, more compact PCBs, which is crucial for modern electronic devices with limited space.
- Improved Signal Integrity: The shorter interconnects provided by microvias result in reduced signal loss, crosstalk, and electromagnetic interference (EMI).
- Increased Reliability: Microvia PCBs offer better thermal management and reduced mechanical stress, leading to improved reliability and longer product life.
- Higher Density: The use of microvias allows for a higher density of interconnects, enabling more complex designs and functionality in a smaller footprint.
Microvia PCB Design Considerations
Microvia Types and Structures
There are several types of microvias used in PCB design, each with its own characteristics and applications:
Microvia Type | Description | Typical Diameter | Applications |
---|---|---|---|
Blind Via | Connects an outer layer to an inner layer, but does not pass through the entire board | 50-150 microns | High-density interconnects, BGA packaging |
Buried Via | Connects two or more inner layers, but does not reach the outer layers | 50-150 microns | Complex multilayer designs, signal integrity |
Stacked Via | A series of microvias stacked on top of each other, connecting multiple layers | 50-150 microns | High-density interconnects, 3D packaging |
Skip Via | A microvia that skips one or more layers, connecting non-adjacent layers | 50-150 microns | Optimizing signal routing, reducing layer count |
Design Rules and Guidelines
When designing a microvia PCB, several key factors must be considered to ensure optimal performance and manufacturability:
- Via Size and Spacing: Adhere to the manufacturer’s guidelines for minimum via size and spacing to ensure reliable connections and avoid manufacturing issues.
- Aspect Ratio: Maintain an appropriate aspect ratio (depth to diameter) for microvias to ensure proper plating and prevent via failures.
- Pad Size and Clearance: Follow the recommended pad size and clearance rules to accommodate the microvias and prevent short circuits or manufacturing defects.
- Stacked Via Limitations: Be aware of the limitations on the number of Stacked Microvias allowed, as excessive stacking can lead to reliability issues.
- Signal Integrity: Consider the impact of microvias on signal integrity, including impedance matching, crosstalk, and EMI, and design accordingly.
Software Tools for Microvia PCB Design
Several software tools are available to assist in the design of microvia PCBs, offering features such as automated rule checking, 3D modeling, and signal integrity analysis:
- Cadence Allegro: A comprehensive PCB design solution with advanced features for high-density designs and microvia support.
- Altium Designer: An integrated PCB design platform with built-in rule checking and 3D modeling capabilities for microvia designs.
- Mentor Graphics PADS: A PCB design suite with intuitive tools for microvia design, simulation, and manufacturing preparation.
- Zuken CR-8000: A high-end PCB design solution with advanced features for microvia design, signal integrity analysis, and 3D modeling.
Cost Considerations for Microvia PCBs
Factors Affecting Microvia PCB Cost
Several factors contribute to the cost of microvia PCBs, including:
- Board Size and Complexity: Larger and more complex boards with higher layer counts and denser interconnects will generally be more expensive.
- Microvia Density: A higher density of microvias will increase the cost due to the additional processing steps required.
- Material Selection: The choice of PCB materials, such as high-frequency laminates or low-loss dielectrics, can impact the overall cost.
- Manufacturing Process: The specific manufacturing processes used, such as laser drilling or plasma etching, can affect the cost of microvia PCBs.
- Quantity and Lead Time: Larger order quantities and longer lead times can often result in lower per-unit costs.
Cost Comparison: Microvia vs. Traditional PCBs
While microvia PCBs offer numerous benefits, they come at a higher cost compared to traditional PCBs. The additional processing steps, specialized equipment, and materials required for microvia fabrication contribute to the increased cost. However, the cost differential can be justified by the improved performance, reliability, and miniaturization enabled by microvia technology.
PCB Type | Relative Cost | Benefits | Applications |
---|---|---|---|
Traditional PCB | Low | Simple designs, low-density interconnects | Consumer electronics, low-cost products |
Microvia PCB | High | High-density interconnects, improved signal integrity, miniaturization | Advanced electronics, mobile devices, aerospace, and defense |
Strategies for Cost Optimization
To minimize the cost of microvia PCBs while still leveraging their benefits, consider the following strategies:
- Design Optimization: Streamline the PCB design to reduce complexity, layer count, and microvia density where possible.
- Panelization: Utilize panel sharing or multi-panel designs to maximize the number of PCBs per manufacturing panel, reducing per-unit costs.
- Material Selection: Choose cost-effective materials that still meet the performance requirements of the application.
- Supplier Selection: Partner with reputable PCB Manufacturers who offer competitive pricing and have experience with microvia fabrication.
- Order Consolidation: Consolidate orders to take advantage of volume discounts and reduce setup costs.
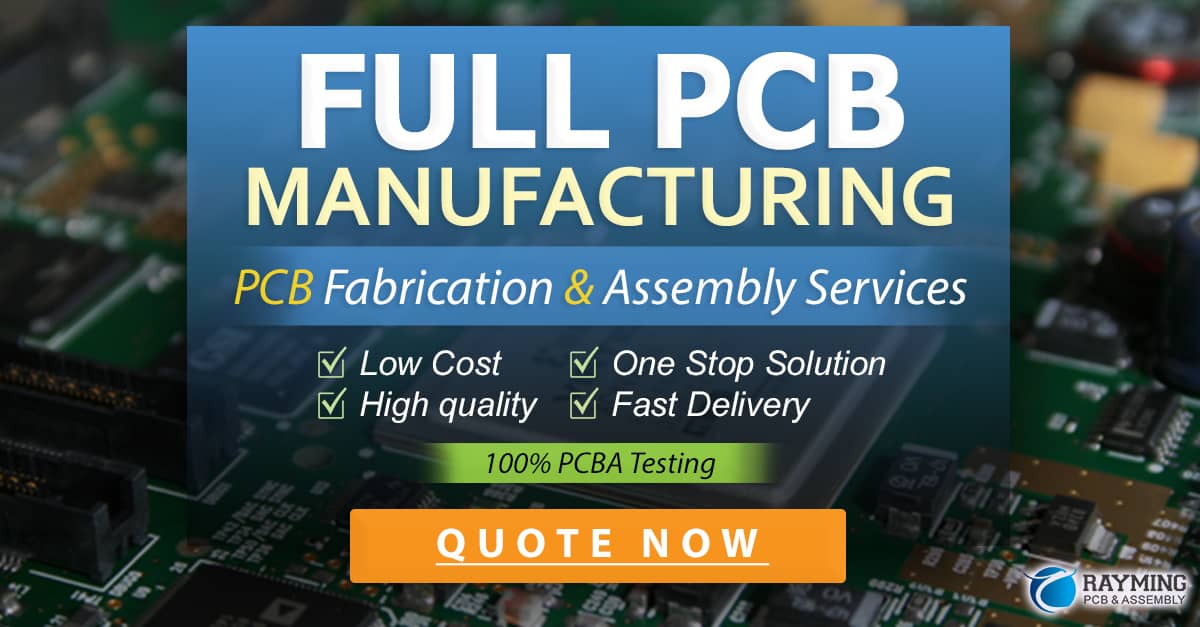
Frequently Asked Questions (FAQ)
-
Q: What is the minimum diameter of a microvia?
A: The minimum diameter of a microvia is typically around 50 microns (0.05mm), but this can vary depending on the manufacturer and the specific fabrication process used. -
Q: Can microvias be used in high-power applications?
A: Yes, microvias can be used in high-power applications, but special considerations must be made for thermal management and current-carrying capacity. Designers should work closely with the PCB manufacturer to ensure the microvia design is suitable for the specific application. -
Q: How do microvias affect signal integrity?
A: Microvias can improve signal integrity by reducing the length of interconnects, which minimizes signal loss, crosstalk, and EMI. However, designers must still consider factors such as impedance matching and via placement to optimize signal integrity. -
Q: Are microvia PCBs more reliable than traditional PCBs?
A: Microvia PCBs can offer improved reliability compared to traditional PCBs due to better thermal management and reduced mechanical stress. However, the reliability also depends on factors such as design, materials, and manufacturing quality. -
Q: How much more expensive are microvia PCBs compared to traditional PCBs?
A: The cost of microvia PCBs can be several times higher than traditional PCBs, depending on the complexity, density, and materials used. However, the exact cost difference will vary based on the specific design and manufacturing requirements.
Conclusion
Microvia PCB technology has become an essential tool for creating high-density, high-performance electronic devices in today’s rapidly evolving market. By understanding the design considerations, cost implications, and optimization strategies associated with microvia PCBs, engineers and decision-makers can effectively leverage this technology to create innovative, reliable, and cost-effective products.
As the demand for smaller, faster, and more sophisticated electronics continues to grow, microvia PCBs will undoubtedly play an increasingly important role in shaping the future of the industry. By staying informed about the latest advancements and best practices in microvia PCB design and manufacturing, companies can position themselves at the forefront of this exciting and dynamic field.
0 Comments