What is a Metal Core PCB (MCPCB)?
A Metal Core Printed Circuit Board (MCPCB) is a specialized type of PCB that incorporates a metal substrate, typically aluminum, as the base layer instead of the traditional FR-4 material. The metal substrate provides superior thermal conductivity compared to standard PCBs, making MCPCBs ideal for applications that generate significant heat, such as high-power LED lighting, power electronics, and automotive systems.
Key Features of MCPCBs
- Excellent thermal conductivity
- Improved heat dissipation
- Enhanced electrical performance
- Increased reliability and longevity
- Compatibility with a wide range of components
The Structure of a Metal Core PCB
An MCPCB consists of several layers:
-
Dielectric Layer: This layer is a thin, electrically insulating material that sits on top of the metal substrate. It is typically made of a thermally conductive but electrically insulating material, such as aluminum oxide or boron nitride.
-
Copper Layer: The copper layer is laminated onto the dielectric layer and is used for the electrical connections and traces. The thickness of the copper layer can vary depending on the application and current requirements.
-
Metal Substrate: The metal substrate, usually aluminum, forms the base of the MCPCB. It provides mechanical support and acts as a heat sink, efficiently dissipating heat away from the components.
-
Solder Mask: A solder mask is applied on top of the copper layer to protect the traces and prevent short circuits. It also provides a surface for component labeling and improves the aesthetics of the board.
MCPCB Layer Structure Table
Layer | Material | Thickness (µm) |
---|---|---|
Solder Mask | Epoxy-based ink | 20-30 |
Copper | Copper foil | 18-400 |
Dielectric | Aluminum oxide, Boron nitride, or other | 50-100 |
Metal Substrate | Aluminum | 1000-3000 |
Advantages of Using Metal Core PCBs
1. Superior Heat Dissipation
The primary advantage of using MCPCBs is their excellent thermal conductivity. The metal substrate, typically aluminum, has a thermal conductivity of around 200 W/mK, which is significantly higher than the 0.3 W/mK of standard FR-4 PCBs. This allows MCPCBs to efficiently transfer heat away from the components, preventing overheating and ensuring optimal performance.
2. Improved Electrical Performance
MCPCBs offer improved electrical performance compared to traditional PCBs. The metal substrate acts as a large ground plane, reducing electromagnetic interference (EMI) and improving signal integrity. This is particularly important in high-frequency applications, where signal quality is critical.
3. Enhanced Reliability and Longevity
By effectively managing heat, MCPCBs can significantly extend the lifespan of electronic components. High temperatures are a leading cause of component failure, and by keeping components cool, MCPCBs improve the overall reliability and longevity of the system.
4. Compatibility with a Wide Range of Components
MCPCBs are compatible with a wide range of electronic components, including surface mount devices (SMDs), through-hole components, and high-power LEDs. This versatility makes them suitable for a variety of applications across different industries.
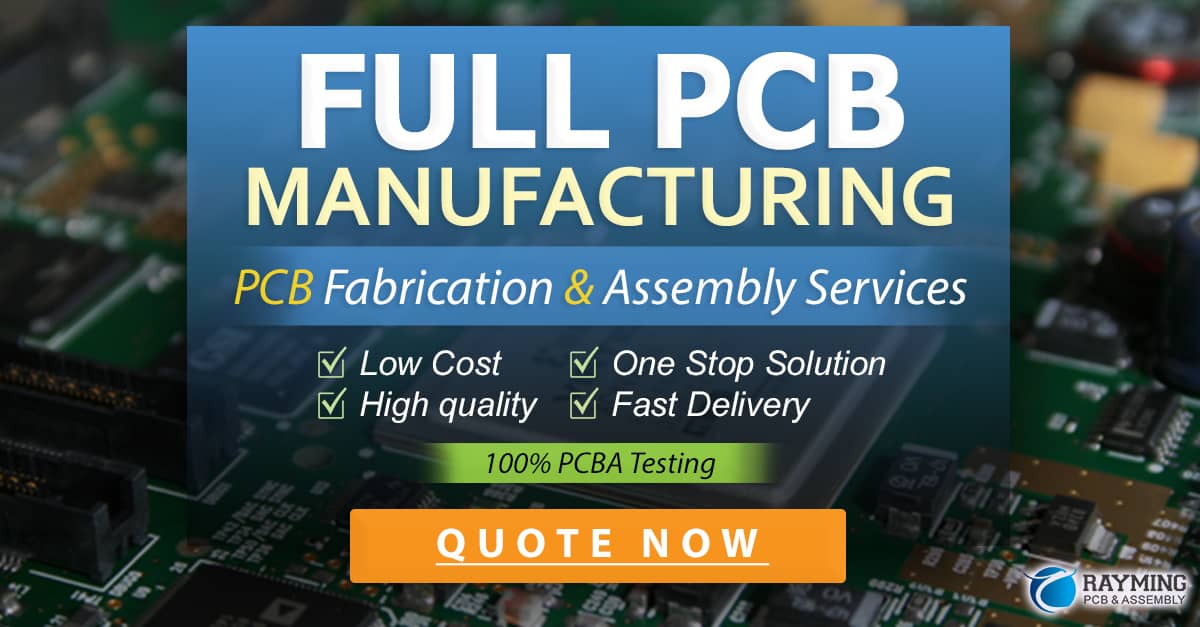
Applications of Metal Core PCBs
1. LED Lighting
MCPCBs are widely used in LED lighting applications, particularly in high-power LED systems. LEDs generate a significant amount of heat, and if not properly managed, this heat can reduce the lifespan and efficiency of the LEDs. By using MCPCBs, the heat generated by the LEDs can be effectively dissipated, ensuring optimal performance and longevity.
2. Power Electronics
Power electronic devices, such as motor drives, power supplies, and inverters, can benefit from the use of MCPCBs. These devices often handle high currents and generate substantial heat. MCPCBs can help dissipate this heat, preventing component damage and ensuring reliable operation.
3. Automotive Electronics
The automotive industry has increasingly adopted MCPCBs for various electronic systems, such as headlights, taillights, and engine control units (ECUs). The harsh operating environment in vehicles, which includes high temperatures and vibrations, requires robust and reliable electronic components. MCPCBs can withstand these conditions and provide excellent thermal management, making them ideal for automotive applications.
4. Telecommunications
In the telecommunications industry, MCPCBs are used in high-frequency applications, such as 5G networks and satellite communication systems. The improved electrical performance and EMI reduction provided by MCPCBs make them suitable for these applications, where signal integrity is paramount.
Designing with Metal Core PCBs
When designing with MCPCBs, there are several factors to consider to ensure optimal performance and reliability.
1. Thermal Management
Proper thermal management is crucial when designing with MCPCBs. The layout of the components and the placement of thermal vias can significantly impact the board’s ability to dissipate heat. Thermal simulations and analysis should be performed to optimize the design for heat dissipation.
2. Dielectric Material Selection
The choice of dielectric material is essential for the performance of an MCPCB. The dielectric layer must provide good electrical insulation while allowing efficient heat transfer. Common dielectric materials include aluminum oxide, boron nitride, and thermally conductive polymers. The selection of the dielectric material depends on the specific application requirements, such as the operating temperature range and the required thermal conductivity.
3. Copper Thickness
The thickness of the copper layer in an MCPCB can affect both its electrical and thermal performance. Thicker copper layers can handle higher currents and provide better heat spreading, but they may also increase the overall cost of the board. The copper thickness should be selected based on the specific requirements of the application, considering factors such as current density and thermal management needs.
4. Solder Mask and Finish
The solder mask and finish applied to an MCPCB can impact its performance and reliability. A solder mask helps protect the copper traces from oxidation and prevents short circuits, while the finish, such as HASL (Hot Air Solder Leveling) or ENIG (Electroless Nickel Immersion Gold), provides a surface for component soldering. The choice of solder mask and finish should consider the application environment and the compatibility with the selected components.
Manufacturing Process of Metal Core PCBs
The manufacturing process of MCPCBs differs from that of traditional PCBs due to the presence of the metal substrate. The key steps in the manufacturing process are:
-
Substrate Preparation: The aluminum substrate is cleaned and prepared for the application of the dielectric layer.
-
Dielectric Layer Application: The dielectric material is applied to the aluminum substrate using techniques such as screen printing, lamination, or powder coating.
-
Copper Foil Lamination: A copper foil is laminated onto the dielectric layer using heat and pressure.
-
Circuit Patterning: The desired circuit pattern is transferred onto the copper layer using photolithography and etching processes.
-
Drill and Plating: Holes are drilled in the board, and the holes are plated with copper to create electrical connections between layers.
-
Solder Mask and Finish Application: A solder mask is applied to the board, and the desired finish (e.g., HASL or ENIG) is applied to the exposed copper areas.
-
Singulation: The individual boards are cut from the panel using routing or punching techniques.
Challenges and Considerations in MCPCB Manufacturing
Manufacturing MCPCBs presents some unique challenges compared to traditional PCB manufacturing:
-
Material Compatibility: The choice of dielectric material must be compatible with the aluminum substrate and the copper layer to ensure proper adhesion and avoid delamination.
-
Thermal Expansion Mismatch: The different thermal expansion coefficients of the metal substrate, dielectric layer, and copper layer can lead to stress and warpage during manufacturing and operation. Proper material selection and process control are essential to minimize these issues.
-
Cost: MCPCBs are generally more expensive than traditional PCBs due to the specialized materials and manufacturing processes involved. However, the improved performance and reliability offered by MCPCBs can justify the higher cost in many applications.
-
Design Constraints: The presence of the metal substrate can impose some design constraints, such as limitations on the minimum trace width and spacing, as well as the placement of vias. Designers must take these constraints into account when creating MCPCB layouts.
Frequently Asked Questions (FAQ)
1. What is the typical thermal conductivity of an MCPCB?
The thermal conductivity of an MCPCB depends on the specific materials used, but it is generally in the range of 1-10 W/mK, which is significantly higher than the 0.3 W/mK of standard FR-4 PCBs.
2. Can MCPCBs be used for high-frequency applications?
Yes, MCPCBs are well-suited for high-frequency applications due to their improved electrical performance and reduced EMI. The metal substrate acts as a large ground plane, helping to maintain signal integrity.
3. Are MCPCBs compatible with surface mount devices (SMDs)?
Yes, MCPCBs are compatible with a wide range of electronic components, including SMDs. The design and manufacturing processes for MCPCBs can accommodate the specific requirements of SMD assembly.
4. How does the cost of MCPCBs compare to traditional PCBs?
MCPCBs are generally more expensive than traditional PCBs due to the specialized materials and manufacturing processes involved. However, the improved performance and reliability offered by MCPCBs can offset the higher cost in applications where thermal management and long-term reliability are critical.
5. What are the key factors to consider when designing with MCPCBs?
When designing with MCPCBs, key factors to consider include thermal management, dielectric material selection, copper thickness, and compatibility with the chosen solder mask and finish. Proper attention to these factors can help ensure optimal performance and reliability in the final application.
Conclusion
Metal Core PCBs offer a high-performance solution for applications that require efficient thermal management and improved electrical performance. By incorporating a metal substrate, typically aluminum, MCPCBs can effectively dissipate heat away from electronic components, ensuring optimal performance and extended lifespan.
The unique structure and manufacturing process of MCPCBs present both advantages and challenges compared to traditional PCBs. When designing with MCPCBs, careful consideration must be given to thermal management, material selection, and compatibility with the chosen components and manufacturing processes.
As the demand for high-power, high-reliability electronic systems continues to grow across various industries, the adoption of MCPCB technology is expected to increase. From LED lighting and power electronics to automotive and telecommunications applications, MCPCBs offer a robust and efficient solution for managing the thermal and electrical challenges of modern electronic devices.
0 Comments