Introduction to PCB Fabrication and Laminates
Printed Circuit Boards (PCBs) are the backbone of modern electronics, providing the essential interconnections and support for various components in devices ranging from smartphones to aerospace systems. The fabrication of PCBs involves a complex process that requires precision, reliability, and adherence to strict industry standards. One of the critical elements in PCB fabrication is the use of laminates, which serve as the foundation for the circuit board and play a vital role in determining its performance and durability.
What are Laminates in PCB Fabrication?
Laminates in PCB fabrication are the base material used to create the substrate of the circuit board. They are typically composed of a combination of materials, such as fiberglass, resin, and copper foil. The laminate provides the necessary insulation, mechanical strength, and thermal stability required for the proper functioning of the PCB.
The most common type of laminate used in PCB fabrication is FR-4 (Flame Retardant 4), which is made of woven fiberglass cloth impregnated with epoxy resin. FR-4 laminates offer excellent electrical insulation, mechanical strength, and thermal stability, making them suitable for a wide range of applications.
Importance of Laminates in PCB Fabrication
Laminates play a crucial role in PCB fabrication, as they directly impact the performance, reliability, and longevity of the final product. Some of the key reasons why laminates are essential in PCB fabrication include:
-
Electrical Insulation: Laminates provide the necessary electrical insulation between the conductive layers of the PCB, preventing short circuits and ensuring proper signal transmission.
-
Mechanical Strength: The laminate serves as the structural backbone of the PCB, providing the necessary mechanical strength to withstand the stresses of manufacturing, assembly, and use.
-
Thermal Stability: Laminates help dissipate heat generated by the components on the PCB, ensuring that the board operates within its temperature limits and preventing thermal damage.
-
Signal Integrity: The choice of laminate material can significantly impact the signal integrity of the PCB, particularly in high-frequency applications where dielectric constant and loss tangent are critical factors.
Advancements in Laminate Technology
As the electronics industry continues to evolve, so do the requirements for PCB laminates. To meet the ever-increasing demands for higher performance, smaller form factors, and improved reliability, laminate manufacturers have been developing new materials and technologies.
High-Frequency Laminates
With the growing demand for high-speed digital and RF applications, the need for laminates that can support higher frequencies has become increasingly important. High-frequency laminates are designed to have lower dielectric constants and loss tangents, which help minimize signal loss and maintain signal integrity at higher frequencies.
Some examples of high-frequency laminates include:
-
Rogers RO4000 Series: These laminates are designed for high-frequency applications, offering low dielectric constant and loss tangent, as well as excellent thermal and mechanical properties.
-
Isola IS400 Series: These laminates are engineered for high-speed digital and RF applications, providing low dielectric constant and loss tangent, as well as improved thermal performance.
Halogen-Free Laminates
Traditional FR-4 laminates contain halogenated flame retardants, which can pose environmental and health concerns when disposed of or incinerated. To address these concerns, laminate manufacturers have developed halogen-free alternatives that offer similar performance characteristics to FR-4 while being more environmentally friendly.
Examples of halogen-free laminates include:
-
Isola TerraGreen: This laminate is a halogen-free alternative to FR-4, offering comparable performance and reliability while meeting strict environmental and safety standards.
-
Panasonic MEGTRON HF Series: These laminates are halogen-free and designed for high-frequency applications, providing low dielectric constant and loss tangent, as well as excellent thermal and mechanical properties.
Thermally Conductive Laminates
As electronic devices become more compact and powerful, the need for effective thermal management has become increasingly important. Thermally conductive laminates are designed to help dissipate heat more efficiently, reducing the risk of thermal damage to components and improving overall system reliability.
Examples of thermally conductive laminates include:
-
Ventec ThermalCladR: This laminate features a metal core that provides excellent thermal conductivity, helping to dissipate heat more effectively than traditional FR-4 laminates.
-
Arlon TC600: This laminate is designed for high-power applications, offering a combination of high thermal conductivity and excellent electrical insulation properties.
Impact of Laminate Selection on PCB Performance
The choice of laminate material can have a significant impact on the performance and reliability of the final PCB. Some of the key factors to consider when selecting a laminate include:
Dielectric Constant and Loss Tangent
The dielectric constant (Dk) and loss tangent (Df) of a laminate are critical factors in determining its suitability for high-frequency applications. A lower Dk helps reduce signal propagation delay, while a lower Df minimizes signal loss and maintains signal integrity.
Thermal Performance
The thermal performance of a laminate is essential for ensuring the long-term reliability of the PCB. Laminates with higher thermal conductivity can help dissipate heat more effectively, reducing the risk of thermal damage to components and improving overall system reliability.
Mechanical Strength
The mechanical strength of a laminate is important for ensuring the structural integrity of the PCB during manufacturing, assembly, and use. Laminates with higher mechanical strength can better withstand the stresses of these processes, reducing the risk of defects and failures.
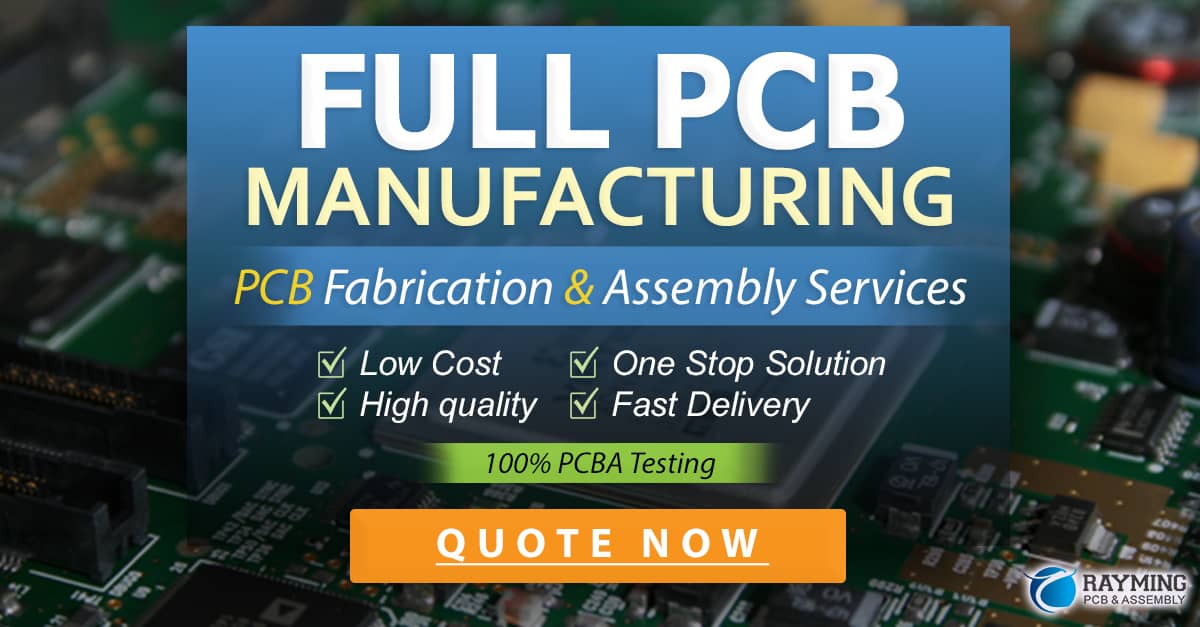
Future Trends in Laminate Technology
As the electronics industry continues to evolve, laminate manufacturers are constantly developing new materials and technologies to meet the ever-increasing demands for performance, reliability, and sustainability. Some of the future trends in laminate technology include:
5G and Beyond
With the rollout of 5G networks and the development of even higher-frequency applications, the demand for laminates that can support these frequencies will continue to grow. Laminate manufacturers are working on developing new materials with even lower dielectric constants and loss tangents to meet these challenges.
Flexible and Stretchable Laminates
The growth of wearable electronics and the Internet of Things (IoT) has created a demand for flexible and stretchable laminates that can conform to various shapes and withstand repeated bending and stretching. Research is ongoing to develop new materials and manufacturing processes to enable the production of reliable and high-performance flexible PCBs.
Sustainable and Eco-Friendly Materials
As environmental concerns continue to grow, there is an increasing demand for sustainable and eco-friendly laminate materials. Laminate manufacturers are exploring the use of bio-based materials, recycled content, and other environmentally friendly options to reduce the environmental impact of PCB fabrication.
FAQ
1. What is the most common laminate material used in PCB fabrication?
The most common laminate material used in PCB fabrication is FR-4 (Flame Retardant 4), which is made of woven fiberglass cloth impregnated with epoxy resin.
2. Why are laminates important in PCB fabrication?
Laminates are important in PCB fabrication because they provide the necessary electrical insulation, mechanical strength, and thermal stability required for the proper functioning of the PCB. They also directly impact the performance, reliability, and longevity of the final product.
3. What are high-frequency laminates, and why are they important?
High-frequency laminates are designed to have lower dielectric constants and loss tangents, which help minimize signal loss and maintain signal integrity at higher frequencies. They are important for supporting the growing demand for high-speed digital and RF applications.
4. What are the benefits of using halogen-free laminates?
Halogen-free laminates offer similar performance characteristics to traditional FR-4 laminates while being more environmentally friendly. They do not contain halogenated flame retardants, which can pose environmental and health concerns when disposed of or incinerated.
5. How can thermally conductive laminates improve PCB performance?
Thermally conductive laminates can help dissipate heat more efficiently, reducing the risk of thermal damage to components and improving overall system reliability. This is particularly important as electronic devices become more compact and powerful, generating more heat during operation.
Conclusion
Laminates play a critical role in PCB fabrication, serving as the foundation for the circuit board and directly impacting its performance, reliability, and longevity. As the electronics industry continues to evolve, laminate manufacturers are developing new materials and technologies to meet the ever-increasing demands for higher performance, smaller form factors, and improved sustainability.
From high-frequency laminates that support the growing demand for 5G and beyond to halogen-free and thermally conductive laminates that address environmental and thermal management concerns, the advancements in laminate technology are enabling the production of more advanced and reliable PCBs.
As the industry moves forward, it is essential for PCB designers and manufacturers to stay informed about the latest developments in laminate technology and to carefully consider the impact of laminate selection on the performance and reliability of their products.
Laminate Material | Key Features | Typical Applications |
---|---|---|
FR-4 | – Good electrical insulation – Mechanical strength – Thermal stability |
– General-purpose PCBs – Consumer electronics – Industrial applications |
High-Frequency Laminates (e.g., Rogers RO4000, Isola IS400) | – Low dielectric constant – Low loss tangent – Excellent thermal and mechanical properties |
– High-speed digital applications – RF applications – 5G networks |
Halogen-Free Laminates (e.g., Isola TerraGreen, Panasonic MEGTRON HF) | – Environmentally friendly – Comparable performance to FR-4 – Low dielectric constant and loss tangent (for high-frequency variants) |
– Eco-conscious products – Consumer electronics – High-frequency applications |
Thermally Conductive Laminates (e.g., Ventec ThermalCladR, Arlon TC600) | – High thermal conductivity – Excellent electrical insulation – Improved heat dissipation |
– High-power applications – Compact electronic devices – Aerospace and defense systems |
By understanding the magnitude of developments and the importance of laminates in PCB fabrication, designers and manufacturers can make informed decisions that lead to the creation of high-performance, reliable, and sustainable electronic products.
0 Comments