What is Low Volume PCB Assembly (LVPCBA)?
Low Volume PCB Assembly (LVPCBA) is a specialized service that focuses on the production of printed circuit boards (PCBs) in small quantities, typically ranging from a few pieces to several hundred. This service caters to clients who require high-quality PCBs for prototyping, testing, or small-scale production runs. LVPCBA is essential for industries such as aerospace, medical devices, telecommunications, and consumer electronics, where rapid prototyping and iterative design processes are crucial for product development.
Advantages of LVPCBA
- Cost-effective for small quantities
- Faster turnaround times compared to high-volume production
- Flexibility in design changes and modifications
- Ideal for prototyping and testing new designs
- Enables quick market entry for new products
The LVPCBA Process
The Low Volume PCB Assembly process involves several key steps to ensure the production of high-quality PCBs that meet the client’s specifications. These steps include:
1. PCB Design and Fabrication
The first step in the LVPCBA process is the design and fabrication of the PCB. Clients provide the PCB design files, which are typically created using electronic design automation (EDA) software such as Altium Designer, Eagle, or KiCad. The design files include the schematic diagram, bill of materials (BOM), and PCB layout.
Once the design files are received, they are reviewed by the LVPCBA service provider to ensure that they meet the necessary manufacturing requirements. Any issues or potential improvements are communicated to the client for approval before proceeding with the fabrication process.
2. Component Sourcing and Procurement
After the PCB design is finalized, the LVPCBA service provider sources and procures the required components based on the BOM provided by the client. This step is critical, as the availability and lead times of components can significantly impact the overall turnaround time of the LVPCBA process.
For low-volume production, LVPCBA service providers often maintain a stock of commonly used components to minimize lead times. In cases where specific components are not readily available, the service provider works with the client to find suitable alternatives or manage the extended lead times.
3. PCB Assembly
With the fabricated PCBs and sourced components in hand, the LVPCBA service provider begins the assembly process. Low-volume PCB assembly typically involves a combination of automated and manual processes, depending on the complexity of the design and the quantity required.
SMT Assembly
Surface Mount Technology (SMT) assembly is an automated process that places surface mount components onto the PCB. The process involves the following steps:
- Solder paste application: A thin layer of solder paste is applied to the PCB pads using a stencil or screen printing method.
- Component placement: Surface mount components are placed onto the solder paste using a pick-and-place machine, which accurately positions the components based on the PCB layout.
- Reflow soldering: The PCB with placed components is passed through a reflow oven, where the solder paste melts and forms a permanent electrical and mechanical connection between the components and the PCB.
THT Assembly
Through-Hole Technology (THT) assembly involves the manual placement and soldering of through-hole components. This process is typically used for components that are not suitable for SMT assembly, such as connectors, large capacitors, or transformers.
THT assembly involves the following steps:
- Component insertion: Through-hole components are manually inserted into the designated holes on the PCB.
- Soldering: The component leads are soldered to the PCB pads using a soldering iron or wave soldering machine.
4. Inspection and Quality Control
After the PCB assembly is complete, the LVPCBA service provider conducts a thorough inspection and quality control process to ensure that the assembled PCBs meet the client’s specifications and industry standards. This process may include:
- Visual inspection: Assembled PCBs are visually inspected for any defects, such as poor soldering, component misalignment, or damaged components.
- Automated Optical Inspection (AOI): AOI machines use high-resolution cameras and image processing software to detect any assembly defects that may not be visible to the naked eye.
- X-ray inspection: For complex PCBs with hidden or obscured solder joints, X-ray inspection may be used to verify the integrity of the connections.
- Electrical testing: Assembled PCBs undergo electrical testing to ensure that they function as intended. This may include in-circuit testing (ICT), flying probe testing, or functional testing.
Any PCBs that fail the inspection and quality control process are either reworked or rejected, depending on the nature and severity of the defect.
5. Packaging and Shipping
Once the assembled PCBs have passed the inspection and quality control process, they are packaged and shipped to the client. The packaging method depends on the quantity and size of the PCBs, as well as the client’s shipping requirements.
For low-volume orders, PCBs are typically packaged in anti-static bags and foam-lined boxes to protect them from static discharge and physical damage during shipping. The LVPCBA service provider may also offer additional packaging options, such as moisture barrier bags or vacuum sealing, for clients with specific packaging requirements.
Choosing an LVPCBA Service Provider
When selecting a Low Volume PCB Assembly service provider, there are several key factors to consider to ensure that your project is completed successfully and to your satisfaction. These factors include:
1. Experience and Expertise
Choose an LVPCBA service provider with a proven track record of successfully completing projects similar to yours. Look for providers with experience in your specific industry or application, as they will be better equipped to understand your requirements and provide valuable insights and recommendations.
2. Technology and Capabilities
Ensure that the LVPCBA service provider has the necessary technology and capabilities to handle your project. This includes the ability to work with the PCB materials, component types, and assembly processes required for your design.
Some key capabilities to consider include:
- SMT and THT assembly capabilities
- Automated Optical Inspection (AOI) and X-ray inspection
- In-circuit testing (ICT) and functional testing
- Rework and repair capabilities
- Conformal coating and potting services
3. Turnaround Time and Flexibility
For low-volume projects, turnaround time is often a critical factor. Choose an LVPCBA service provider that can meet your project’s timeline without compromising on quality. Additionally, look for providers that offer flexibility in terms of design changes and modifications, as this can be valuable during the prototyping and testing phases.
4. Quality Management System
A robust quality management system is essential for ensuring that your PCBs are manufactured to the highest standards. Look for LVPCBA service providers that are certified to industry standards such as ISO 9001, ISO 13485 (for medical devices), or AS9100 (for aerospace applications). These certifications demonstrate that the provider has implemented strict quality control processes and is committed to continuous improvement.
5. Communication and Customer Support
Effective communication and customer support are crucial for the success of your LVPCBA project. Choose a service provider that is responsive, proactive, and transparent in their communication. They should be willing to answer your questions, provide regular updates on your project’s progress, and work with you to resolve any issues that may arise.
6. Cost and Value
While cost is an important consideration, it should not be the sole deciding factor when choosing an LVPCBA service provider. Instead, focus on finding a provider that offers the best value for your project, balancing cost with factors such as quality, turnaround time, and customer support.
Be cautious of providers that offer significantly lower prices than their competitors, as this may indicate that they are cutting corners on quality or using substandard materials and processes.
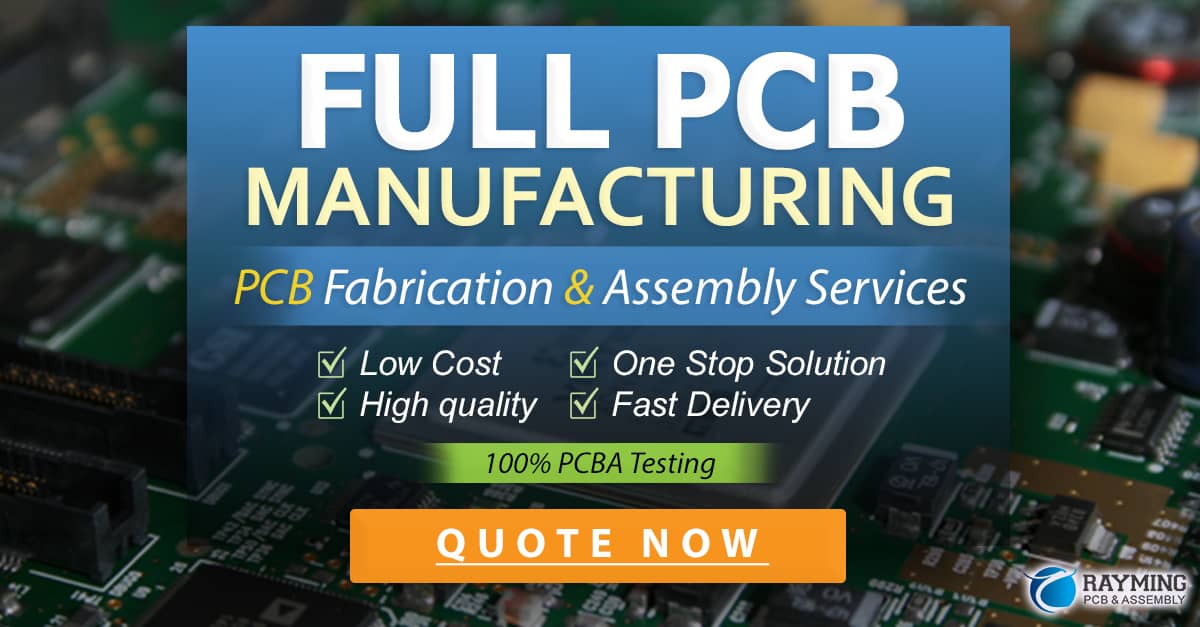
Common LVPCBA Challenges and Solutions
Low Volume PCB Assembly projects can present unique challenges that require careful planning and collaboration between the client and the LVPCBA service provider. Some common challenges and their solutions include:
1. Component Availability and Lead Times
Challenge: Low-volume projects often require specialized or hard-to-find components that may have long lead times or minimum order quantities (MOQs) that exceed the project’s requirements.
Solution: Work closely with your LVPCBA service provider to identify potential component availability issues early in the project. Consider alternative components or redesign the PCB to use more readily available components. In some cases, the service provider may be able to source smaller quantities of components or negotiate reduced MOQs with suppliers.
2. Design for Manufacturability (DFM)
Challenge: PCB designs that are not optimized for manufacturability can lead to assembly issues, delays, and increased costs.
Solution: Collaborate with your LVPCBA service provider to conduct a thorough Design for Manufacturability (DFM) review before finalizing your PCB design. This review will identify potential manufacturability issues and provide recommendations for improving the design to ensure a smooth and efficient assembly process.
3. Intellectual Property (IP) Protection
Challenge: Low-volume projects often involve proprietary or sensitive designs that require protection from unauthorized access or copying.
Solution: Choose an LVPCBA service provider that has strong intellectual property (IP) protection measures in place, such as non-disclosure agreements (NDAs), secure data storage and transfer protocols, and employee background checks. Additionally, consider splitting your project between multiple service providers to minimize the risk of IP theft or reverse engineering.
4. Rework and Repair
Challenge: Despite thorough inspection and quality control processes, some assembled PCBs may require rework or repair due to component failures, assembly defects, or design issues.
Solution: Select an LVPCBA service provider that has experienced rework and repair technicians and the necessary equipment to handle these issues efficiently. Establish clear communication channels and protocols for reporting and resolving rework and repair issues to minimize delays and ensure that the final product meets your quality standards.
LVPCBA Industry Applications
Low Volume PCB Assembly services are used across a wide range of industries and applications, each with its own unique requirements and challenges. Some common industry applications include:
1. Aerospace and Defense
LVPCBA is essential for the aerospace and defense industry, where high-reliability PCBs are required for applications such as avionics, satellite systems, and military communications equipment. Key requirements in this industry include:
- Compliance with standards such as MIL-PRF-31032, MIL-PRF-55110, and IPC-6012 Class 3
- Traceability and documentation for all components and processes
- Rigorous inspection and testing, including environmental stress screening (ESS) and burn-in testing
2. Medical Devices
The medical device industry relies on LVPCBA for the development and production of PCBs used in diagnostic equipment, monitoring systems, and implantable devices. Key requirements in this industry include:
- Compliance with standards such as ISO 13485 and FDA Quality System Regulations (QSR)
- Cleanroom assembly for sensitive devices
- Biocompatibility testing for implantable devices
- Traceability and documentation for all components and processes
3. Industrial Automation and Control
LVPCBA is used in the development and production of PCBs for industrial automation and control systems, such as programmable logic controllers (PLCs), human-machine interfaces (HMIs), and sensor networks. Key requirements in this industry include:
- Ruggedized designs for harsh industrial environments
- Compliance with standards such as IEC 61131 and IEC 61508
- Conformal coating or potting for protection against moisture, dust, and vibration
4. Telecommunications
The telecommunications industry uses LVPCBA for the development and production of PCBs used in networking equipment, wireless devices, and fiber-optic systems. Key requirements in this industry include:
- High-speed PCB designs for data transmission
- Compliance with standards such as IEEE 802.11, IEEE 802.3, and IEC 60950
- Electromagnetic Compatibility (EMC) testing
5. Consumer Electronics
LVPCBA is used in the development and prototyping of PCBs for consumer electronics devices, such as smartphones, tablets, and wearables. Key requirements in this industry include:
- Rapid prototyping and short lead times
- Cost-effective assembly for low-volume production runs
- Compliance with standards such as FCC Part 15 and RoHS
Frequently Asked Questions (FAQ)
-
What is the typical turnaround time for a low-volume PCB assembly project?
Turnaround times for low-volume PCB assembly projects can vary depending on the complexity of the design, component availability, and the LVPCBA service provider’s workload. Typical turnaround times range from 5 to 15 business days, but some service providers may offer expedited services for an additional fee. -
What is the minimum order quantity (MOQ) for low-volume PCB assembly?
Minimum order quantities for low-volume PCB assembly can vary between service providers. Some providers may offer assembly services for as few as one or two PCBs, while others may have a minimum order quantity of 10 or more. It’s best to discuss your specific requirements with potential service providers to find one that can accommodate your needs. -
Can I supply my own components for low-volume PCB assembly?
Yes, most LVPCBA service providers allow clients to supply their own components, which is known as consigned inventory. However, it’s important to ensure that the supplied components meet the service provider’s quality and packaging requirements. Some providers may also offer component procurement services for clients who prefer not to manage their own inventory. -
How much does low-volume PCB assembly cost?
The cost of low-volume PCB assembly depends on several factors, including the PCB size and complexity, component types and quantities, assembly processes required, and the service provider’s pricing structure. In general, low-volume assembly will have a higher per-unit cost compared to high-volume production due to the fixed setup costs and lower economies of scale. It’s best to request quotes from multiple service providers to compare pricing and value. -
What documentation should I provide to my LVPCBA service provider?
To ensure a smooth and successful low-volume PCB assembly project, provide your service provider with the following documentation: -
Bill of Materials (BOM): A complete list of all components used in the PCB design, including manufacturer part numbers, quantities, and any special handling or sourcing requirements.
- Gerber Files: A set of files that describe the PCB layout, including the copper layers, solder mask, silk screen, and drill holes.
- Assembly Drawings: Detailed drawings that show the placement and orientation of components on the PCB, as well as any special assembly instructions or requirements.
- Test Specifications: A description of the testing requirements for the assembled PCBs, including any functional, in-circuit, or environmental tests that must be performed.
Industry | Key Requirements |
---|---|
Aerospace and Defense | – Compliance with MIL-PRF-31032, MIL-PRF-55110, and IPC-6012 Class 3 – Traceability and documentation – Rigorous inspection and testing |
Medical Devices | – Compliance with ISO 13485 and FDA QSR – Cleanroom assembly – Biocompatibility testing – Traceability and documentation |
Industrial Automation and Control | – Ruggedized designs for harsh environments – Compliance with IEC 61131 and IEC 61508 – Conformal coating or potting |
Telecommunications | – High-speed PCB designs – Compliance with IEEE 802.11, IEEE 802.3, and IEC 60950 – EMC testing |
Consumer Electronics | – Rapid prototyping and short lead times – Cost-effective assembly – Compliance with FCC Part 15 and RoHS |
In conclusion, Low Volume PCB Assembly is a critical service for industries that require high-quality PCBs for prototyping, testing, and small-scale production runs. By understanding the LVPCBA process, key considerations for choosing a service provider, common challenges and solutions, and industry-specific requirements, clients can ensure the success of their low-volume PCB assembly projects.
Effective communication, collaboration, and attention to detail throughout the LVPCBA process are essential for achieving the desired results and bringing innovative products to market quickly and efficiently. As technology continues to advance and the demand for customized, low-volume electronics grows, LVPCBA services will remain a vital part of the product development landscape.
0 Comments