What are LED-PCBs?
LED-PCBs, or Light Emitting Diode Printed Circuit Boards, are specialized circuit boards designed to power and control LED lights. These boards are essential components in a wide range of applications, from simple indicator lights to complex LED displays and lighting systems.
LED-PCBs are composed of a non-conductive substrate, typically made of fiberglass or other composite materials, with conductive copper traces printed on the surface. These traces connect various electronic components, such as resistors, capacitors, and microcontrollers, which work together to regulate the power and control the behavior of the LEDs.
Advantages of LED-PCBs
LED-PCBs offer several advantages over traditional lighting solutions:
-
Energy Efficiency: LEDs consume significantly less power compared to incandescent or fluorescent lights, resulting in lower energy costs and a smaller environmental footprint.
-
Longevity: LEDs have a much longer lifespan than traditional light sources, often lasting up to 50,000 hours or more. This reduces maintenance and replacement costs.
-
Versatility: LED-PCBs can be designed in a wide range of sizes, shapes, and configurations to suit various applications and design requirements.
-
Controllability: With the help of microcontrollers and other electronic components, LED-PCBs can offer advanced control features, such as dimming, color changing, and programmable lighting effects.
Types of LED-PCBs
There are several types of LED-PCBs, each with its own unique characteristics and applications:
Single-Layer LED-PCBs
Single-layer LED-PCBs have conductive traces on only one side of the substrate. These boards are the simplest and most cost-effective type of LED-PCB, making them ideal for basic applications and low-power LED lights.
Double-Layer LED-PCBs
Double-layer LED-PCBs have conductive traces on both sides of the substrate, allowing for more complex circuit designs and higher component density. These boards are commonly used in applications that require more advanced control features or higher power output.
Multilayer LED-PCBs
Multilayer LED-PCBs have three or more layers of conductive traces, separated by insulating layers. These boards offer the highest level of complexity and component density, making them suitable for advanced applications, such as high-resolution LED displays and intelligent lighting systems.
Flexible LED-PCBs
Flexible LED-PCBs use a flexible substrate material, such as polyimide or polyester, allowing the board to bend and conform to various shapes. These boards are ideal for applications that require non-planar lighting solutions, such as wearable electronics and automotive lighting.
Metal Core LED-PCBs
Metal Core LED-PCBs (MCPCBs) feature a metal substrate, typically aluminum, which provides excellent thermal conductivity. This helps dissipate heat generated by the LEDs, improving their performance and longevity. MCPCBs are commonly used in high-power LED applications, such as automotive headlights and industrial lighting.
Designing LED-PCBs
Designing LED-PCBs requires careful consideration of several factors to ensure optimal performance, reliability, and cost-effectiveness.
Schematic Design
The first step in designing an LED-PCB is creating a schematic diagram that represents the electrical connections between components. This includes selecting appropriate resistors to limit current, capacitors to smooth power supply, and microcontrollers or other control components.
Component Selection
Choosing the right components is crucial for the success of an LED-PCB design. Factors to consider include:
- LED type and power rating
- Resistor values and power rating
- Capacitor values and voltage rating
- Microcontroller or other control components
- Connectors and other mechanical components
PCB Layout
Once the schematic is complete, the next step is to create a PCB layout that translates the electrical connections into a physical board design. Key considerations for PCB layout include:
- Trace width and spacing
- Component placement and orientation
- Thermal management
- Electromagnetic interference (EMI) mitigation
- Manufacturing constraints, such as minimum hole size and trace spacing
Simulation and Verification
Before sending the design for manufacturing, it is essential to simulate and verify the circuit’s performance using electronic design automation (EDA) tools. This helps identify potential issues, such as voltage drops, current overloads, and signal integrity problems, allowing for design optimization and refinement.
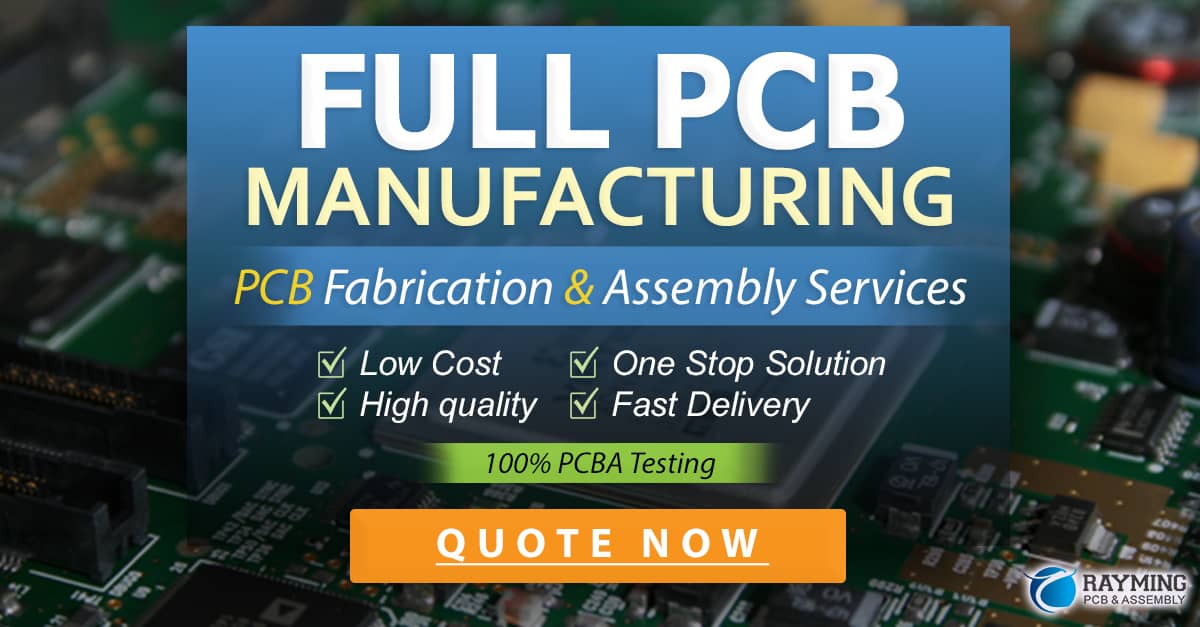
Manufacturing LED-PCBs
After the design is finalized and verified, the next step is to manufacture the LED-PCBs. The manufacturing process typically involves the following stages:
-
PCB Fabrication: The PCB layout is used to create a photomask, which is then used to transfer the circuit pattern onto a copper-clad substrate through a photolithography process. The unwanted copper is etched away, leaving the desired traces.
-
Component Placement: Surface mount devices (SMDs) and through-hole components are placed on the PCB using automated pick-and-place machines or manual assembly methods.
-
Soldering: The components are soldered to the PCB using reflow soldering for SMDs or wave soldering for through-hole components.
-
Inspection and Testing: The assembled PCBs undergo visual inspection and electrical testing to ensure proper functionality and adherence to specifications.
Quality Control
Maintaining strict quality control throughout the manufacturing process is crucial to ensure the reliability and performance of LED-PCBs. Key aspects of quality control include:
- Incoming material inspection
- Process control and monitoring
- Automated optical inspection (AOI) for component placement and soldering
- In-circuit testing (ICT) for electrical functionality
- Burn-in testing to identify early failures
Applications of LED-PCBs
LED-PCBs find applications in a wide range of industries and products, including:
-
Automotive Lighting: LED-PCBs are used in headlights, taillights, interior lighting, and instrument panel illumination.
-
General Lighting: LED-PCBs are used in residential, commercial, and industrial lighting fixtures, offering energy-efficient and long-lasting alternatives to traditional light sources.
-
Displays: LED-PCBs form the backbone of digital signage, video walls, and other large-format displays used in advertising, entertainment, and information dissemination.
-
Backlighting: LED-PCBs provide backlighting for LCDs in consumer electronics, such as smartphones, tablets, and televisions.
-
Wearable Electronics: Flexible LED-PCBs are used in wearable devices, such as smart clothing, fitness trackers, and medical monitoring devices.
-
Internet of Things (IoT): LED-PCBs play a role in IoT devices, providing visual feedback, status indication, and ambient lighting in smart home devices, industrial sensors, and other connected devices.
FAQ
-
What is the difference between an LED and an LED-PCB?
An LED is a single light-emitting diode, while an LED-PCB is a printed circuit board designed to power and control multiple LEDs in a specific configuration. -
Can LED-PCBs be customized for specific applications?
Yes, LED-PCBs can be designed and manufactured to meet specific application requirements, such as size, shape, power output, and control features. -
How do I choose the right type of LED-PCB for my project?
The choice of LED-PCB depends on factors such as the complexity of the circuit, power requirements, environmental conditions, and cost constraints. It is best to consult with an experienced PCB designer or manufacturer to determine the most suitable type of LED-PCB for your project. -
What is the typical lifespan of an LED-PCB?
The lifespan of an LED-PCB depends on factors such as the quality of components, design, and operating conditions. However, well-designed LED-PCBs can last up to 50,000 hours or more. -
Are LED-PCBs environmentally friendly?
Yes, LED-PCBs are considered environmentally friendly due to their energy efficiency, long lifespan, and the absence of toxic materials such as mercury, which is commonly found in traditional lighting sources.
Type of LED-PCB | Layers | Flexibility | Thermal Management |
---|---|---|---|
Single-Layer | 1 | Rigid | Limited |
Double-Layer | 2 | Rigid | Moderate |
Multilayer | 3+ | Rigid | Good |
Flexible | 1-2 | Flexible | Limited |
Metal Core (MCPCB) | 1-2 | Rigid | Excellent |
In conclusion, LED-PCBs are essential components in modern lighting and display applications, offering energy efficiency, longevity, versatility, and controllability. Understanding the types, design considerations, manufacturing processes, and applications of LED-PCBs is crucial for engineers, designers, and managers involved in the development of LED-based products. As the demand for efficient and innovative lighting solutions continues to grow, the importance of LED-PCBs in shaping the future of illumination cannot be overstated.
0 Comments