The Evolution of Miniaturization
Over the past few decades, the electronics industry has witnessed a remarkable shift towards miniaturization. The demand for smaller, lighter, and more portable devices has driven manufacturers to develop innovative solutions that optimize space and reduce component sizes. From smartphones and wearables to medical devices and aerospace systems, miniaturization has become a key factor in product design and development.
Moore’s Law and Its Impact
One of the fundamental drivers of miniaturization is Moore’s Law, which states that the number of transistors on an integrated circuit doubles approximately every two years. This observation, made by Intel co-founder Gordon Moore in 1965, has held true for several decades. As a result, electronic components have become smaller, faster, and more energy-efficient, enabling the development of compact and powerful devices.
Year | Transistor Count | Relative Size |
---|---|---|
1971 | 2,300 | 1 |
1980 | 29,000 | 0.08 |
1990 | 1,180,000 | 0.002 |
2000 | 42,000,000 | 0.000055 |
2010 | 1,170,000,000 | 0.000002 |
2020 | 50,000,000,000 | 0.000000046 |
Table 1: Transistor count and relative size over the years (Source: Our World in Data)
Advancements in Manufacturing Processes
Miniaturization has been made possible by continuous advancements in manufacturing processes. The introduction of surface-mount technology (SMT) revolutionized PCB Assembly by allowing components to be directly mounted onto the board’s surface, reducing the need for through-hole mounting. SMT enables higher component density, smaller footprints, and improved performance.
Furthermore, advancements in photolithography, etching, and plating techniques have enabled the creation of finer traces and smaller vias on PCBs. These developments have allowed for the fabrication of high-density interconnect (HDI) PCBs, which offer superior connectivity and signal integrity in a compact form factor.
The Role of PCBs in Miniaturization
PCBs serve as the backbone of electronic devices, providing mechanical support and electrical connectivity for components. As Miniaturization trends continue to shape the electronics industry, PCBs have evolved to meet the demanding requirements of smaller, more complex devices.
Space Optimization
One of the primary roles of PCBs in miniaturization is space optimization. Modern PCB designs employ various techniques to maximize component density and minimize board size. Some of these techniques include:
-
Multi-layer PCBs: By stacking multiple layers of conductive material, PCBs can accommodate a higher number of components and interconnections within a limited space.
-
High-density interconnect (HDI): HDI PCBs feature finer traces, smaller vias, and reduced spacing between components, allowing for greater routing density and improved signal integrity.
-
Embedded components: Embedding passive components, such as resistors and capacitors, within the PCB substrate further reduces the overall board size and improves performance.
Flex and Rigid-Flex PCBs
Flex and rigid-flex PCBs have gained popularity in miniaturized devices due to their ability to conform to complex shapes and save space. Flex PCBs are made from flexible materials, such as polyimide, and can be bent or folded to fit into tight spaces. Rigid-flex PCBs combine rigid and flexible sections, allowing for three-dimensional packaging and improved reliability.
These types of PCBs are particularly useful in wearable devices, medical implants, and aerospace applications, where space is limited and flexibility is required.
3D PCB Assembly
3D PCB assembly is another technique that has emerged to support miniaturization efforts. This approach involves stacking multiple PCBs vertically and interconnecting them using through-silicon vias (TSVs) or other methods. 3D PCB assembly enables the creation of highly compact and dense electronic packages, suitable for applications such as smartphones, cameras, and advanced sensor systems.
Applications of Miniaturized PCBs
The impact of miniaturization and the increased usage of PCBs can be seen across various industries. Some notable applications include:
-
Consumer Electronics: Smartphones, tablets, smartwatches, and other portable devices heavily rely on miniaturized PCBs to achieve their compact form factors and advanced functionalities.
-
Medical Devices: Miniaturized PCBs are essential in medical devices, such as implantable sensors, pacemakers, and surgical instruments, where size, reliability, and performance are critical factors.
-
Automotive Electronics: As vehicles become more technologically advanced, miniaturized PCBs play a vital role in enabling features such as advanced driver assistance systems (ADAS), infotainment systems, and electric vehicle powertrains.
-
Aerospace and Defense: Miniaturized PCBs are crucial in aerospace and defense applications, where space and weight are limited, and reliability is paramount. Examples include satellite systems, avionics, and military communication devices.
-
Internet of Things (IoT): The proliferation of IoT devices, such as smart sensors, wearables, and connected appliances, relies heavily on miniaturized PCBs to achieve compact sizes and low power consumption.
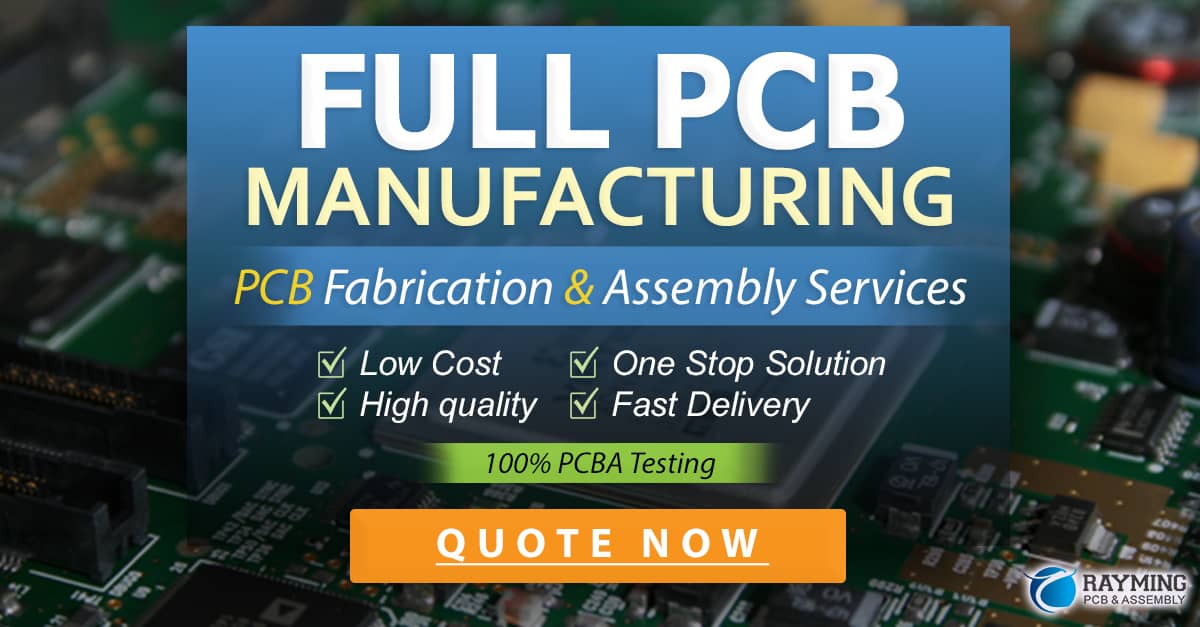
Challenges and Future Prospects
While miniaturization has brought numerous benefits, it also presents various challenges for PCB design and manufacturing. Some of these challenges include:
-
Signal Integrity: As PCBs become more densely populated and traces become finer, maintaining signal integrity becomes increasingly difficult. Designers must carefully consider factors such as impedance matching, crosstalk, and electromagnetic interference (EMI) to ensure reliable performance.
-
Thermal Management: With higher component density and increased power consumption, thermal management becomes a critical concern in miniaturized PCBs. Effective heat dissipation techniques, such as thermal vias, heat sinks, and advanced materials, must be employed to prevent overheating and ensure long-term reliability.
-
Manufacturing Complexity: Miniaturization demands precise manufacturing processes and tight tolerances. PCB manufacturers must invest in advanced equipment and skilled personnel to meet the challenges of fabricating high-density, multi-layer, and HDI boards.
Despite these challenges, the future of miniaturization and PCB usage looks promising. Advancements in materials science, such as the development of advanced substrates and conductive inks, are expected to further push the boundaries of PCB miniaturization. Additionally, the adoption of advanced packaging technologies, such as system-in-package (SiP) and wafer-level packaging (WLP), will enable even greater levels of integration and miniaturization.
Frequently Asked Questions (FAQ)
-
What is the main driver behind the miniaturization trend in electronics?
The main driver behind the miniaturization trend is the increasing demand for smaller, lighter, and more portable devices with enhanced functionality. Consumers and industries alike seek compact and powerful electronic solutions that optimize space and performance. -
How have PCBs evolved to support miniaturization?
PCBs have evolved to support miniaturization through various techniques, such as multi-layer designs, high-density interconnect (HDI), embedded components, flex and rigid-flex PCBs, and 3D PCB assembly. These advancements allow for greater component density, improved signal integrity, and more compact form factors. -
What are some of the key applications of miniaturized PCBs?
Miniaturized PCBs find applications in a wide range of industries, including consumer electronics (smartphones, wearables), medical devices (implantable sensors, surgical instruments), automotive electronics (ADAS, infotainment systems), aerospace and defense (satellites, avionics), and the Internet of Things (IoT) devices (smart sensors, connected appliances). -
What challenges does miniaturization pose for PCB design and manufacturing?
Miniaturization presents challenges such as maintaining signal integrity, ensuring effective thermal management, and dealing with increased manufacturing complexity. Designers must carefully consider factors like impedance matching, crosstalk, and EMI, while manufacturers must invest in advanced equipment and skilled personnel to fabricate high-density, multi-layer, and HDI boards. -
What advancements are expected to further push the boundaries of PCB miniaturization?
Advancements in materials science, such as the development of advanced substrates and conductive inks, are expected to further push the boundaries of PCB miniaturization. Additionally, the adoption of advanced packaging technologies, like system-in-package (SiP) and wafer-level packaging (WLP), will enable even greater levels of integration and miniaturization in the future.
Conclusion
The leap in miniaturization trends has undeniably magnified the usage of Printed Circuit Boards across various industries. As electronic devices continue to shrink in size while offering enhanced functionality, PCBs have evolved to meet the demanding requirements of smaller, more complex devices. Through space optimization techniques, flex and rigid-flex designs, and 3D PCB assembly, PCBs have become the backbone of miniaturized electronics.
While miniaturization presents challenges in terms of signal integrity, thermal management, and manufacturing complexity, the future prospects remain promising. Advancements in materials science and packaging technologies are expected to further push the boundaries of PCB miniaturization, enabling even more compact and powerful electronic solutions.
As the world continues to embrace miniaturization, the role of PCBs in enabling this transformation will only grow in importance. From consumer electronics and medical devices to automotive and aerospace applications, miniaturized PCBs will continue to shape the future of the electronics industry, driving innovation and empowering the development of groundbreaking technologies.
0 Comments