Introduction to Laser PCB Manufacturing
Printed circuit board (PCB) manufacturing has come a long way since its inception in the early 20th century. Today, PCBs are an essential component in almost all electronic devices, from smartphones and laptops to medical equipment and aerospace systems. As the demand for smaller, faster, and more complex PCBs continues to grow, manufacturers are turning to advanced technologies like laser exposure machines to improve efficiency and accuracy.
What is a Laser Exposure Machine?
A laser exposure machine, also known as a laser direct imaging (LDI) system, is a high-precision tool used in the PCB manufacturing process. It uses a focused laser beam to directly expose the photoresist layer on the PCB substrate, creating the desired circuit pattern. This eliminates the need for traditional photomasks and allows for faster, more accurate, and more flexible PCB production.
Benefits of Laser PCB Manufacturing
Compared to traditional PCB manufacturing methods, laser exposure machines offer several key benefits:
-
Higher precision: Laser beams can be focused down to a few microns in diameter, enabling the creation of extremely fine circuit features. This is especially important for high-density PCBs used in advanced electronics.
-
Faster production: Laser exposure is a direct imaging process, meaning it doesn’t require the creation of physical photomasks. This can significantly reduce setup time and allow for faster overall production speeds.
-
Greater flexibility: Since laser exposure doesn’t rely on masks, it’s easy to make changes to the circuit design without incurring additional costs or delays. This makes it ideal for prototyping and low-volume production runs.
-
Improved yield: The high precision and direct imaging capabilities of laser exposure machines can help reduce defects and improve overall yield, leading to cost savings for manufacturers.
How Laser Exposure Machines Work
The PCB Manufacturing Process
To understand how laser exposure machines fit into the PCB manufacturing process, let’s first review the basic steps involved:
-
PCB design: The circuit layout is designed using specialized software, taking into account factors like component placement, routing, and signal integrity.
-
PCB fabrication: The bare PCB substrate is created by laminating copper foil onto an insulating material like FR-4. Holes are drilled for through-hole components, and the copper is etched away to create the desired circuit pattern.
-
Solder mask application: A layer of solder mask is applied over the copper traces to protect them from oxidation and prevent short circuits during soldering.
-
Silkscreen printing: Text and symbols are printed onto the PCB surface to aid in component placement and identification.
-
Surface finish: A final surface finish, such as HASL or ENIG, is applied to the exposed copper pads to improve solderability and protect against corrosion.
The Role of Laser Exposure Machines
Laser exposure machines come into play during the PCB fabrication step, specifically when creating the circuit pattern on the copper layer. Here’s how it works:
-
The bare PCB substrate is coated with a layer of photoresist, a light-sensitive polymer that hardens when exposed to ultraviolet (UV) light.
-
The PCB is loaded into the laser exposure machine, which uses a high-powered laser to selectively expose the photoresist in the desired circuit pattern. The laser beam is guided by a computer-controlled mirror system, allowing for precise and rapid exposure of complex designs.
-
After exposure, the PCB is developed in a chemical solution that removes the unexposed photoresist, leaving behind a protective mask over the copper traces that will form the final circuit.
-
The exposed copper is etched away using a chemical process, leaving only the desired circuit pattern behind.
-
Finally, the remaining photoresist is stripped away, revealing the completed copper circuit on the PCB surface.
Types of Laser Exposure Machines
There are two main types of laser exposure machines used in PCB manufacturing:
-
UV laser exposure machines: These systems use ultraviolet lasers with wavelengths typically in the range of 355-375 nm. UV lasers are compatible with a wide range of photoresists and offer good resolution and speed for most PCB applications.
-
IR laser exposure machines: Infrared lasers, with wavelengths around 1064 nm, are also used in some PCB exposure systems. IR lasers can achieve even higher resolutions than UV lasers, but require specialized photoresists and may have slower exposure speeds.
Both types of laser exposure machines offer significant advantages over traditional photomask-based exposure methods in terms of precision, flexibility, and efficiency.
Advancements in Laser PCB Technology
As the PCB industry continues to evolve, so too does the technology behind laser exposure machines. Here are some of the latest advancements and trends in laser PCB manufacturing:
Multi-Wavelength Laser Systems
Some newer laser exposure machines incorporate multiple laser wavelengths into a single system. This allows for greater flexibility in terms of compatible photoresists and enables optimization of the exposure process for different PCB materials and feature sizes.
High-Power Laser Sources
The power output of laser exposure machines has been steadily increasing over the years, with some systems now offering laser powers in excess of 10 watts. Higher power lasers can improve exposure speeds and enable the creation of even finer circuit features.
Improved Beam Control and Shaping
Advanced beam control and shaping technologies, such as adaptive optics and dynamic focusing, are being incorporated into laser exposure machines to further enhance precision and resolution. These technologies help to compensate for variations in PCB topography and ensure consistent exposure quality across the entire board surface.
Integration with Other Manufacturing Processes
Laser exposure machines are increasingly being integrated with other PCB manufacturing processes, such as direct imaging of solder mask and legend ink. This allows for a more streamlined and efficient production workflow, reducing the need for multiple specialized machines and minimizing handling of the PCBs.
Inline Inspection and Metrology
Some laser exposure machines now include inline inspection and metrology capabilities, allowing for real-time monitoring and control of the exposure process. This can help to identify and correct any defects or variations early in the manufacturing process, improving overall yield and quality.
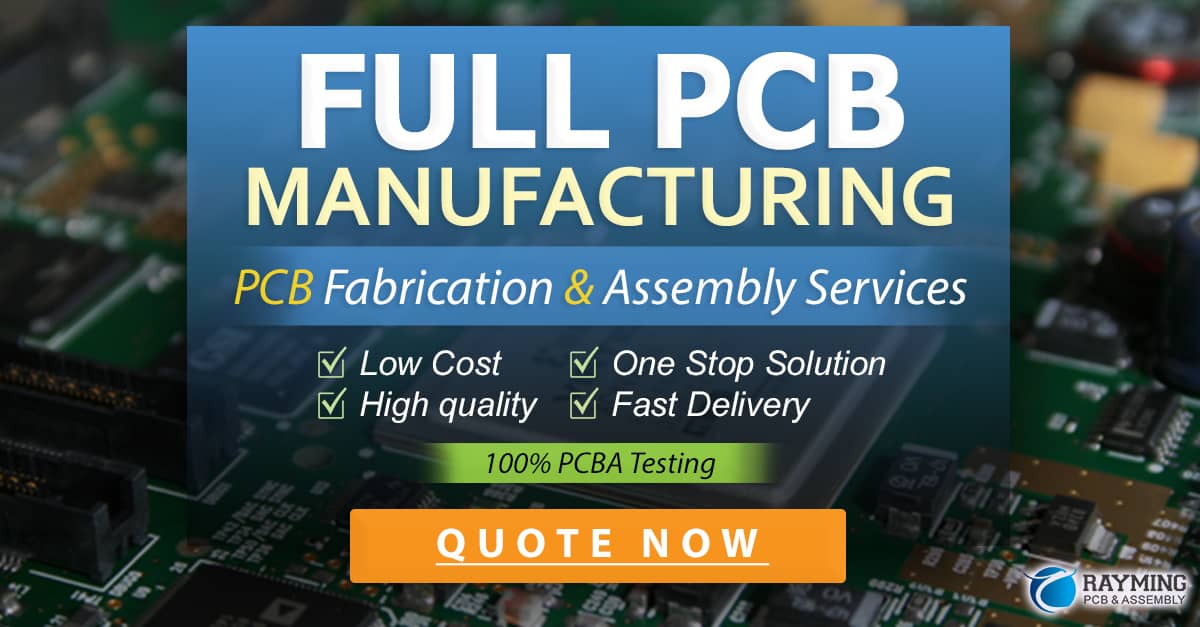
Applications of Laser PCB Technology
The benefits of laser exposure machines make them well-suited for a wide range of PCB applications, from consumer electronics to aerospace and defense. Here are some specific areas where laser PCB technology is having a significant impact:
High-Density Interconnect (HDI) PCBs
HDI PCBs are characterized by their fine pitch and high-density circuitry, with features sizes often measured in microns rather than millimeters. Laser exposure machines are essential for achieving the required precision and resolution in HDI PCB manufacturing, enabling the creation of dense, complex circuit patterns with minimal defects.
Flexible and Rigid-Flex PCBs
Flexible and rigid-flex PCBs are becoming increasingly popular in applications where space is limited or where the PCB needs to conform to a specific shape. Laser exposure machines are well-suited for these types of PCBs, as they can handle the unique challenges associated with exposing circuit patterns on flexible substrates.
RF and Microwave PCBs
PCBs designed for radio frequency (RF) and microwave applications often require specialized materials and very tight tolerances to ensure proper signal integrity and performance. Laser exposure machines can help to meet these demanding requirements, providing the precision and control needed to create high-quality RF and microwave PCBs.
Automotive and Aerospace PCBs
PCBs used in automotive and aerospace applications are subject to stringent reliability and performance standards, given the critical nature of these systems. Laser exposure machines can help to ensure the consistency and quality of these PCBs, reducing the risk of defects and failures in the field.
Case Studies
To illustrate the real-world impact of laser PCB technology, let’s look at a couple of case studies from industry leaders:
Company A: Doubling Production Capacity
Company A, a major PCB manufacturer, recently installed a new laser exposure machine in their facility. By replacing their older photomask-based exposure system with a state-of-the-art laser machine, they were able to double their production capacity for high-density PCBs while maintaining superior quality and yield.
Metric | Before Laser Exposure | After Laser Exposure |
---|---|---|
Monthly PCB Output | 10,000 | 20,000 |
Average Feature Size | 100 μm | 50 μm |
Defect Rate | 1.5% | 0.5% |
As the table shows, not only did Company A achieve a significant increase in production volume, but they were also able to improve the precision and quality of their PCBs by adopting laser exposure technology.
Company B: Rapid Prototyping Success
Company B, a leading electronics design firm, needed a way to quickly prototype and iterate on new PCB designs for a client’s product. By partnering with a PCB manufacturer that utilized laser exposure machines, they were able to go from initial design to fully assembled prototype in just 48 hours.
Stage | Time Required |
---|---|
PCB Design | 8 hours |
PCB Fabrication | 24 hours |
PCB Assembly | 16 hours |
Total Time | 48 hours |
The speed and flexibility afforded by laser PCB technology allowed Company B to meet their client’s tight deadlines and deliver a successful product on schedule.
FAQ
-
Q: How much does a laser exposure machine cost?
A: The cost of a laser exposure machine can vary widely depending on factors like laser power, exposure area, and additional features. Entry-level systems may start around $100,000, while high-end machines can exceed $1 million. -
Q: What is the minimum feature size achievable with laser exposure machines?
A: The minimum feature size depends on the specific machine and laser wavelength, but many modern systems can achieve resolutions down to 25 μm or less. Some specialized machines may even be capable of sub-10 μm features. -
Q: How do laser exposure machines compare to inkjet-based direct imaging systems?
A: While both technologies offer advantages over traditional photomask-based exposure, laser machines typically offer higher resolutions and faster exposure speeds than inkjet systems. However, inkjet systems may have lower upfront costs and can be more suitable for certain niche applications. -
Q: Can laser exposure machines be used for other PCB manufacturing processes beyond photoresist exposure?
A: Yes, some laser exposure machines are capable of directly imaging solder mask and legend ink, eliminating the need for separate screen printing processes. This can help to streamline the overall PCB manufacturing workflow. -
Q: Are there any limitations or drawbacks to using laser exposure machines for PCB manufacturing?
A: While laser exposure machines offer many benefits, they do have some limitations. The high upfront cost can be a barrier for smaller manufacturers, and the machines require specialized training and maintenance. Additionally, some materials and substrates may not be compatible with certain laser wavelengths, requiring careful selection and testing.
Conclusion
Laser exposure machines have revolutionized the PCB manufacturing industry, enabling the creation of high-density, high-precision circuit boards with unparalleled efficiency and flexibility. As electronics continue to become smaller, faster, and more complex, the role of laser PCB technology will only become more critical.
By understanding the capabilities and advancements in laser exposure machines, PCB manufacturers and designers can make informed decisions about how to leverage this technology for their specific applications. Whether it’s doubling production capacity, achieving rapid prototyping, or pushing the boundaries of circuit miniaturization, laser PCB manufacturing offers a powerful tool for driving innovation in the electronics industry.
As the technology continues to evolve, we can expect to see even greater improvements in resolution, speed, and integration with other manufacturing processes. The future of PCB manufacturing is bright, and laser exposure machines will undoubtedly play a central role in shaping that future.
0 Comments