What is Immersion Silver?
Immersion silver, also known as immersion tin, is a lead-free Surface Finish that involves depositing a thin layer of silver onto the exposed copper surfaces of a PCB. The process is an immersion reaction, where the silver ions in the solution replace the copper atoms on the surface, resulting in a uniform and smooth silver finish. Typically, the thickness of the immersion silver layer ranges from 0.05 to 0.15 microns (2 to 6 microinches).
Advantages of Immersion Silver
Immersion silver offers several advantages that make it an attractive choice for PCB surface finishes:
-
Excellent Solderability: Immersion silver provides excellent solderability, enabling easy and reliable solder joint formation during the assembly process. The silver surface promotes good wetting and spreading of solder, resulting in strong and consistent solder connections.
-
Flatness and Coplanarity: The thin and uniform nature of the immersion silver layer maintains the flatness and coplanarity of the PCB surface. This is particularly important for fine-pitch components and high-density designs, where a flat and even surface is critical for proper component placement and solder joint integrity.
-
Shelf Life: Immersion silver has a relatively long shelf life compared to other surface finishes. It can maintain its solderability and appearance for up to 12 months when stored in proper conditions. This extended shelf life allows for greater flexibility in PCB manufacturing and inventory management.
-
Compatibility with Various Assembly Processes: Immersion silver is compatible with a wide range of assembly processes, including Reflow Soldering, Wave Soldering, and pin-through-hole assembly. It can be used with both leaded and lead-free solder alloys, making it versatile for different manufacturing requirements.
-
Cost-Effectiveness: Compared to other lead-free surface finishes, such as ENIG (Electroless Nickel Immersion Gold) or ENEPIG (Electroless Nickel Electroless Palladium Immersion Gold), immersion silver is a cost-effective option. It requires fewer process steps and materials, resulting in lower production costs.
Considerations for Using Immersion Silver
While immersion silver offers numerous benefits, there are a few considerations to keep in mind when choosing this surface finish:
-
Silver Migration: One potential issue with immersion silver is the phenomenon of silver migration. Under certain environmental conditions, such as high humidity and the presence of an electrical potential, silver ions can migrate from one point to another on the PCB surface. This migration can lead to short circuits and affect the reliability of the PCB. To mitigate silver migration, proper design guidelines, such as maintaining adequate spacing between conductors and using conformal coatings, should be followed.
-
Tarnishing: Immersion silver can tarnish over time when exposed to air and moisture. The tarnishing process, also known as sulfidation, occurs when silver reacts with sulfur compounds in the atmosphere, forming silver sulfide. While tarnishing does not directly impact the solderability or functionality of the PCB, it can affect the visual appearance. If aesthetics are a critical concern, other surface finishes like ENIG or OSP (Organic Solderability Preservative) may be preferred.
-
Thickness Control: Controlling the thickness of the immersion silver layer is important to ensure optimal performance. If the silver layer is too thin, it may not provide adequate protection against oxidation and can lead to solderability issues. On the other hand, if the layer is too thick, it can cause problems with fine-pitch component placement and solder joint formation. Proper process control and monitoring are necessary to maintain the desired thickness range.
Other Lead-Free PCB Surfaces
While immersion silver is a popular lead-free surface finish, there are other options available that offer different properties and advantages. Let’s explore a few of these alternatives:
ENIG (Electroless Nickel Immersion Gold)
ENIG is a widely used lead-free surface finish that consists of a layer of electroless nickel followed by a thin layer of immersion gold. The nickel layer provides a barrier against copper diffusion and enhances the durability of the surface, while the gold layer offers excellent solderability and protection against oxidation.
Advantages of ENIG include:
- Excellent solderability and wettability
- Good shelf life and resistance to oxidation
- Compatibility with a wide range of assembly processes
- Suitable for fine-pitch and high-density designs
However, ENIG also has some drawbacks:
- Higher cost compared to other surface finishes
- Potential for black pad formation due to improper process control
- Possibility of Gold Embrittlement in solder joints
ENEPIG (Electroless Nickel Electroless Palladium Immersion Gold)
ENEPIG is an advanced lead-free surface finish that combines the benefits of ENIG with an additional layer of electroless palladium. The palladium layer serves as a barrier between the nickel and gold layers, preventing the formation of intermetallic compounds that can lead to brittle solder joints.
Advantages of ENEPIG include:
- Excellent solderability and wettability
- Improved mechanical strength and reliability of solder joints
- Suitable for high-frequency and high-speed applications
- Compatibility with multiple reflow cycles
However, ENEPIG also has some limitations:
- Higher cost due to the additional palladium layer
- Increased process complexity and control requirements
- Potential for palladium corrosion in certain environments
OSP (Organic Solderability Preservative)
OSP is a lead-free surface finish that involves applying a thin, organic coating onto the exposed copper surfaces of a PCB. The organic coating acts as a barrier against oxidation and preserves the solderability of the copper.
Advantages of OSP include:
- Cost-effectiveness compared to other surface finishes
- Good solderability and wettability
- Flat and coplanar surface for component placement
- Environmentally friendly and RoHS-compliant
However, OSP also has some drawbacks:
- Limited shelf life compared to other surface finishes
- Potential for poor wetting and solderability if not properly applied
- Sensitivity to handling and environmental conditions
Selecting the Right Lead-Free PCB Surface
Choosing the right lead-free PCB surface depends on various factors, including the specific application requirements, assembly processes, cost considerations, and reliability expectations. Here are a few guidelines to help in the selection process:
-
Solderability and Assembly Process: Consider the solderability requirements and compatibility with the intended assembly processes. Immersion silver, ENIG, and ENEPIG offer excellent solderability and are suitable for most assembly processes. OSP may be a good choice for simpler designs and shorter shelf life requirements.
-
Fine-Pitch and High-Density Designs: For fine-pitch components and high-density designs, surface finishes with good flatness and coplanarity are crucial. Immersion silver and ENEPIG are well-suited for these applications due to their thin and uniform layers.
-
Reliability and Durability: If the PCB will be subjected to harsh environments or requires high reliability, surface finishes like ENIG and ENEPIG offer better protection against oxidation and provide a more durable surface.
-
Cost and Production Volume: Consider the cost implications of each surface finish and the production volume. Immersion silver and OSP are generally more cost-effective options, while ENIG and ENEPIG involve higher costs due to additional process steps and materials.
-
Shelf Life and Storage: If the PCBs need to be stored for an extended period before assembly, surface finishes with longer shelf life, such as immersion silver and ENIG, are preferable. OSP has a shorter shelf life and may require more stringent storage conditions.
-
Environmental Considerations: All the lead-free surface finishes discussed in this article are RoHS-compliant and environmentally friendly. However, if environmental impact is a top priority, OSP may be the most eco-friendly option due to its organic nature and minimal use of chemicals.
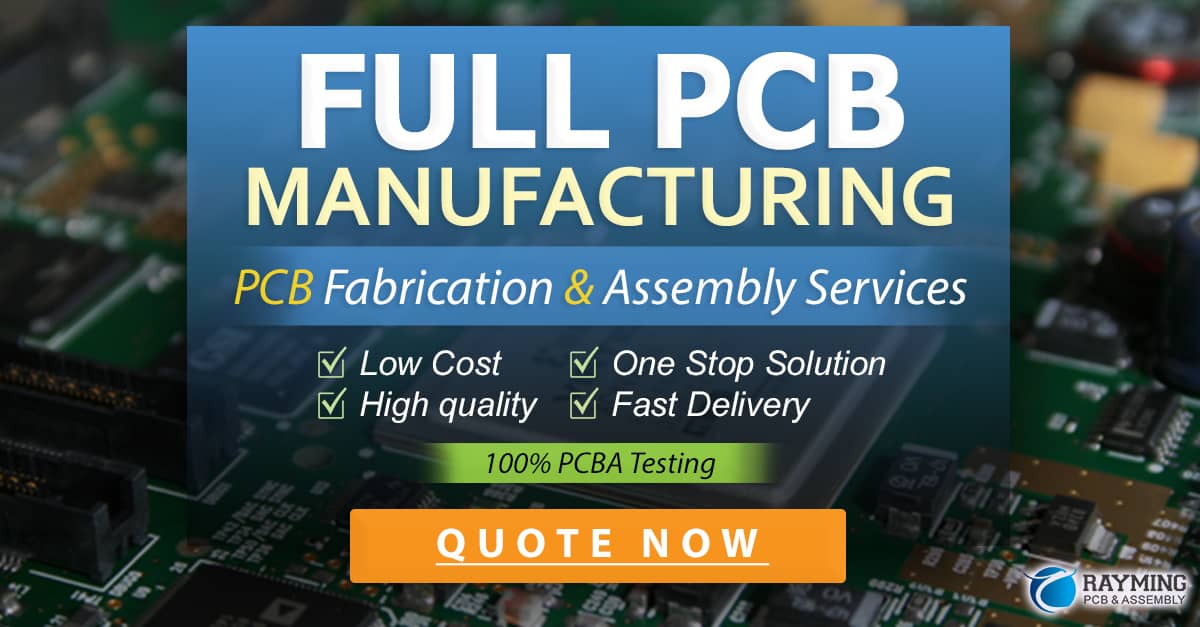
Frequently Asked Questions (FAQ)
-
What is the main advantage of using immersion silver as a PCB surface finish?
Immersion silver offers excellent solderability, good flatness and coplanarity, and a relatively long shelf life. It is also cost-effective compared to other lead-free surface finishes. -
Can immersion silver be used for fine-pitch and high-density PCB designs?
Yes, immersion silver is well-suited for fine-pitch and high-density designs due to its thin and uniform layer, which maintains the flatness and coplanarity of the PCB surface. -
What is silver migration, and how can it be mitigated in immersion silver PCBs?
Silver migration is a phenomenon where silver ions move from one point to another on the PCB surface under certain environmental conditions, potentially causing short circuits. It can be mitigated by following proper design guidelines, such as maintaining adequate spacing between conductors and using conformal coatings. -
How does ENEPIG differ from ENIG, and what are its main advantages?
ENEPIG includes an additional layer of electroless palladium between the nickel and gold layers, which prevents the formation of intermetallic compounds and improves the mechanical strength and reliability of solder joints. ENEPIG is particularly suitable for high-frequency and high-speed applications. -
What factors should be considered when selecting a lead-free PCB surface finish?
When selecting a lead-free PCB surface finish, consider factors such as solderability and assembly process compatibility, fine-pitch and high-density design requirements, reliability and durability expectations, cost and production volume, shelf life and storage needs, and environmental considerations.
Conclusion
Immersion silver has emerged as a popular lead-free PCB surface finish due to its excellent solderability, flatness, and cost-effectiveness. However, it is important to consider the potential challenges, such as silver migration and tarnishing, and follow appropriate design guidelines to mitigate these issues.
Other lead-free surface finishes, including ENIG, ENEPIG, and OSP, offer unique advantages and considerations. ENIG provides good solderability and durability, while ENEPIG adds enhanced mechanical strength and reliability. OSP is a cost-effective and environmentally friendly option but has limitations in terms of shelf life and handling.
Ultimately, the choice of lead-free PCB surface finish depends on the specific requirements of the application, assembly processes, reliability expectations, and cost constraints. By understanding the properties, advantages, and considerations of each surface finish, manufacturers can make informed decisions to ensure the optimal performance and reliability of their PCBs.
As the electronics industry continues to evolve and push for environmentally friendly solutions, lead-free PCB surfaces will remain a critical aspect of PCB manufacturing. Immersion silver, along with other lead-free options, will play a significant role in meeting the demands for RoHS compliance, high-quality PCBs, and sustainable practices in the years to come.
Lead-Free PCB Surface | Advantages | Considerations |
---|---|---|
Immersion Silver | – Excellent solderability – Good flatness and coplanarity – Relatively long shelf life – Cost-effective |
– Potential for silver migration – Tarnishing over time |
ENIG | – Excellent solderability and wettability – Good shelf life and oxidation resistance – Compatibility with various assembly processes |
– Higher cost compared to other finishes – Potential for black pad formation – Possibility of gold embrittlement |
ENEPIG | – Excellent solderability and wettability – Improved mechanical strength and reliability – Suitable for high-frequency and high-speed applications |
– Higher cost due to additional palladium layer – Increased process complexity – Potential for palladium corrosion |
OSP | – Cost-effectiveness – Good solderability and wettability – Flat and coplanar surface – Environmentally friendly |
– Limited shelf life – Potential for poor wetting if not properly applied – Sensitivity to handling and environmental conditions |
0 Comments