Introduction to IC Packaging
Integrated Circuit (IC) packaging is a crucial aspect of electronic device manufacturing. It involves encasing a semiconductor chip in a protective material, such as plastic or ceramic, to provide mechanical support, electrical connectivity, and protection from the environment. The package also serves as an interface between the chip and the printed circuit board (PCB) on which it is mounted.
IC packaging has evolved significantly over the years to keep pace with the increasing complexity and miniaturization of electronic devices. As devices become smaller and more powerful, IC packaging techniques have had to adapt to ensure reliable performance and longevity.
Types of IC Packaging
There are several types of IC packaging, each with its own advantages and disadvantages. The choice of packaging depends on factors such as the application, performance requirements, and cost. Some of the most common types of IC packaging include:
Through-Hole Packaging
Through-hole packaging is one of the oldest and most reliable packaging methods. It involves inserting the leads of the IC package through holes drilled in the PCB and soldering them to the other side. This method provides a strong mechanical connection and is well-suited for high-power applications. However, it is relatively large and not suitable for high-density applications.
Surface Mount Packaging
Surface mount packaging is a more modern approach that involves soldering the IC package directly onto the surface of the PCB. This method allows for smaller package sizes and higher component density compared to through-hole packaging. Surface mount packages come in various forms, including:
- Small Outline Package (SOP)
- Quad Flat Package (QFP)
- Ball Grid Array (BGA)
- Chip Scale Package (CSP)
Flip Chip Packaging
Flip chip packaging is a type of surface mount packaging where the IC is flipped upside down and connected directly to the PCB using solder bumps. This method eliminates the need for bond wires, reducing the package size and improving electrical performance. Flip chip packaging is commonly used in high-performance applications such as microprocessors and graphics chips.
Multi-Chip Packaging
Multi-chip packaging involves combining multiple ICs into a single package. This can be done using various techniques such as stacking, side-by-side placement, or embedding. Multi-chip packaging allows for higher functionality and performance in a smaller footprint, making it suitable for applications such as mobile devices and wearables.
Importance of IC Packaging
IC packaging plays a vital role in the performance, reliability, and cost of electronic devices. Some of the key reasons why IC packaging is important include:
Protection
The primary function of IC packaging is to protect the delicate semiconductor chip from the environment. The package provides mechanical support and protection from factors such as moisture, dust, and physical damage. This ensures that the chip can operate reliably over its intended lifetime.
Electrical Connectivity
IC packaging provides electrical connectivity between the chip and the PCB. The package includes conductive elements such as bond wires, solder bumps, or pins that connect the chip’s input/output (I/O) pads to the PCB. The choice of packaging and the design of the interconnects can significantly impact the electrical performance of the device, including signal integrity, power delivery, and electromagnetic interference (EMI).
Thermal Management
ICs generate heat during operation, which must be dissipated to prevent overheating and ensure reliable performance. The package plays a crucial role in thermal management by providing a path for heat to flow from the chip to the environment. This can be achieved through various means such as heat spreaders, heat sinks, or thermal vias in the package.
Cost Reduction
IC packaging can also contribute to cost reduction in electronic device manufacturing. By optimizing the package design and materials, manufacturers can reduce the overall size and weight of the device, leading to lower material and shipping costs. Additionally, advanced packaging techniques such as wafer-level packaging and 3D packaging can enable higher yields and lower cost per unit.
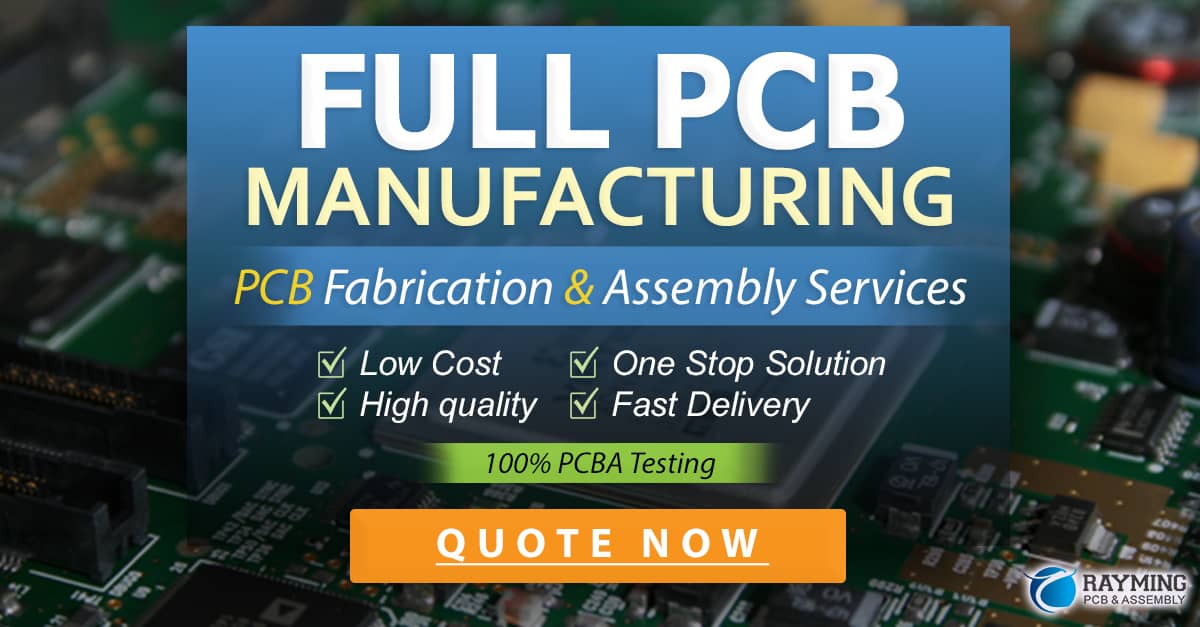
Challenges in IC Packaging
While IC packaging has come a long way, there are still several challenges that need to be addressed to keep pace with the demands of modern electronic devices. Some of the key challenges include:
Miniaturization
As devices become smaller and more compact, IC packages need to shrink accordingly. This requires advanced packaging techniques such as 3D packaging, fan-out wafer-level packaging, and system-in-package (SiP) that can provide high density and functionality in a small footprint. Miniaturization also poses challenges in terms of signal integrity, power delivery, and thermal management.
High-Speed Applications
The increasing demand for high-speed applications such as 5G, artificial intelligence, and autonomous vehicles requires IC packages that can support high bandwidth and low latency. This requires advanced packaging materials and techniques that can minimize signal loss, crosstalk, and EMI. Examples include high-density interconnects, shielded packages, and low-loss dielectrics.
Heterogeneous Integration
Many modern electronic devices require the integration of multiple functionalities such as computing, sensing, and communication into a single package. This requires heterogeneous integration techniques that can combine different types of ICs, such as digital, analog, and RF, into a single package. Challenges include managing different process technologies, materials, and thermal requirements.
Environmental Sustainability
As electronic waste continues to grow, there is increasing pressure on the industry to develop more environmentally sustainable packaging solutions. This includes the use of recyclable and biodegradable materials, as well as design for disassembly and reuse. Challenges include finding materials that can meet the performance and reliability requirements of IC packaging while also being environmentally friendly.
Future Trends in IC Packaging
IC packaging technology continues to evolve to meet the demands of future electronic devices. Some of the key trends in IC packaging include:
3D Packaging
3D packaging involves stacking multiple ICs vertically to achieve higher density and functionality in a smaller footprint. This can be done using various techniques such as through-silicon vias (TSVs), interposers, or package-on-package (PoP). 3D packaging enables the integration of heterogeneous ICs and can provide significant improvements in performance, power efficiency, and form factor.
Fan-Out Wafer-Level Packaging
Fan-out wafer-level packaging (FOWLP) is a type of packaging where the ICs are embedded in a molding compound and the interconnects are fanned out beyond the chip boundaries. This allows for higher I/O density and smaller package sizes compared to traditional wafer-level packaging. FOWLP is particularly well-suited for applications such as mobile devices and IoT sensors.
Advanced Materials
The development of advanced packaging materials is crucial for meeting the performance and reliability requirements of future electronic devices. This includes materials with lower dielectric constants, higher thermal conductivity, and better mechanical properties. Examples include low-k dielectrics, copper pillars, and advanced underfills.
Heterogeneous Integration
Heterogeneous integration will become increasingly important as electronic devices become more complex and multifunctional. This will require the development of new packaging architectures and techniques that can integrate diverse ICs and components into a single package. Examples include chiplets, system-in-package (SiP), and hybrid bonding.
Conclusion
IC packaging is a critical aspect of electronic device manufacturing that plays a vital role in the performance, reliability, and cost of modern devices. As devices continue to become smaller, faster, and more complex, IC packaging technology must evolve to meet these challenges. This will require the development of advanced packaging techniques, materials, and architectures that can provide high density, functionality, and performance in a small footprint.
By understanding the importance of IC packaging and staying up-to-date with the latest trends and challenges, electronics manufacturers can ensure that their devices are reliable, cost-effective, and competitive in the marketplace.
FAQs
1. What is the difference between IC packaging and PCB Assembly?
IC packaging refers to the process of encasing a semiconductor chip in a protective material and providing electrical connectivity to the PCB. PCB assembly, on the other hand, refers to the process of mounting and interconnecting various electronic components, including IC packages, onto a printed circuit board.
2. What are the most common materials used in IC packaging?
The most common materials used in IC packaging include:
– Plastic (e.g., epoxy resin)
– Ceramic
– Metal (e.g., copper, aluminum)
– Glass
The choice of material depends on factors such as the application, performance requirements, and cost.
3. What is the difference between wire bonding and flip chip bonding?
Wire bonding and flip chip bonding are two methods of connecting the IC to the package substrate. In wire bonding, thin metal wires are used to connect the chip’s I/O pads to the package leads. In flip chip bonding, the chip is flipped upside down and connected directly to the substrate using solder bumps. Flip chip bonding provides higher I/O density and better electrical performance compared to wire bonding.
4. What is the role of underfill in IC packaging?
Underfill is a material that is used to fill the gap between the IC and the package substrate. Its primary role is to provide mechanical support and protect the interconnects from stress and fatigue caused by thermal expansion mismatches. Underfill also helps to improve the thermal and electrical performance of the package by providing a path for heat dissipation and reducing signal reflections.
5. What are the key factors to consider when selecting an IC package?
When selecting an IC package, some of the key factors to consider include:
– Application requirements (e.g., performance, power, size)
– Chip size and I/O count
– Thermal and mechanical requirements
– Cost and availability
– Compatibility with the PCB and assembly process
By carefully considering these factors, designers can select the optimal IC package for their specific application and ensure reliable and cost-effective performance.
0 Comments