Factors to Consider When Selecting a PCB Surface Finish
When choosing a surface finish for your PCB, several key factors must be taken into account to ensure the best possible outcome. These factors include:
1. Application Requirements
The intended application of the PCB is the primary factor that guides the selection of the surface finish. Different applications have varying requirements in terms of environmental conditions, operating temperature, and expected lifespan. For instance, a PCB designed for aerospace or military applications may require a more robust and durable surface finish compared to a consumer electronics product.
2. Solderability
Solderability refers to the ease with which components can be soldered onto the PCB. The surface finish plays a crucial role in determining the solderability of the board. Some surface finishes, such as Immersion Silver (IAg) and Electroless Nickel Immersion Gold (ENIG), offer excellent solderability, while others, like Organic Solderability Preservative (OSP), may have limitations in terms of shelf life and multiple reflow cycles.
3. Cost
The cost of the surface finish is another important consideration, especially for high-volume production runs. Some surface finishes, such as ENIG and Electroless Nickel Electroless Palladium Immersion Gold (ENEPIG), are more expensive than others, like OSP and Hot Air Solder Leveling (HASL). The cost of the surface finish should be balanced against the performance requirements and the overall project budget.
4. Shelf Life
The shelf life of the PCB is the period during which the board maintains its solderability and functionality without deterioration. Different surface finishes have varying shelf lives, ranging from a few months to several years. For example, OSP has a relatively short shelf life of around 6 to 12 months, while ENIG can maintain its solderability for up to 12 months or more.
5. Compatibility with Other Processes
The compatibility of the surface finish with other processes, such as wire bonding, press-fit connectors, and conformal coating, should also be considered. Some surface finishes may not be suitable for certain processes, which can limit the design options or require additional steps in the manufacturing process.
Common PCB Surface Finish Options
There are several commonly used surface finish options in the PCB industry, each with its own set of advantages and disadvantages. The most popular surface finishes include:
1. Hot Air Solder Leveling (HASL)
HASL is one of the most widely used surface finishes in the PCB industry. In this process, the PCB is dipped into a molten solder bath, and then hot air is used to blow off the excess solder, leaving a thin, uniform layer on the exposed copper. HASL offers good solderability, low cost, and compatibility with most assembly processes. However, it may not be suitable for fine-pitch components due to the risk of solder bridges, and the surface may not be entirely flat, which can cause issues with some components.
2. Organic Solderability Preservative (OSP)
OSP is a thin, organic coating applied to the exposed copper on the PCB. It acts as a barrier against oxidation and maintains the solderability of the copper surface. OSP is a low-cost option and provides a flat surface, making it suitable for fine-pitch components. However, it has a limited shelf life and may not withstand multiple reflow cycles, which can lead to reduced solderability over time.
3. Immersion Silver (IAg)
Immersion Silver is a chemical process that deposits a thin layer of silver onto the exposed copper surface. It offers excellent solderability, good electrical conductivity, and compatibility with most assembly processes. IAg also provides a flat surface, making it suitable for fine-pitch components. However, it is more expensive than OSP and HASL and may be prone to tarnishing over time, which can affect its solderability.
4. Electroless Nickel Immersion Gold (ENIG)
ENIG is a two-step process that involves depositing a layer of nickel onto the copper surface, followed by a thin layer of gold. The nickel layer provides a barrier against copper diffusion, while the gold layer protects the nickel from oxidation and ensures good solderability. ENIG offers excellent shelf life, good electrical conductivity, and compatibility with most assembly processes. However, it is more expensive than other options and may be susceptible to “black pad” syndrome, which can cause solderability issues.
5. Electroless Nickel Electroless Palladium Immersion Gold (ENEPIG)
ENEPIG is an extension of the ENIG process, with an additional layer of palladium between the nickel and gold layers. The palladium layer enhances the wire bonding capability of the surface finish, making it suitable for applications that require both soldering and wire bonding. ENEPIG offers excellent solderability, long shelf life, and good electrical conductivity. However, it is one of the most expensive surface finish options and may have a longer lead time due to the additional processing steps.
Surface Finish Selection Matrix
To help visualize the characteristics and suitability of different surface finishes, a selection matrix can be used. The matrix below compares the key properties of the most common surface finishes:
Surface Finish | Solderability | Shelf Life | Cost | Flatness | Wire Bonding | Multiple Reflow |
---|---|---|---|---|---|---|
HASL | Good | Long | Low | Poor | Not Suitable | Suitable |
OSP | Good | Short | Low | Good | Not Suitable | Limited |
IAg | Excellent | Moderate | Moderate | Good | Not Suitable | Suitable |
ENIG | Excellent | Long | High | Good | Suitable | Suitable |
ENEPIG | Excellent | Long | Very High | Good | Excellent | Suitable |
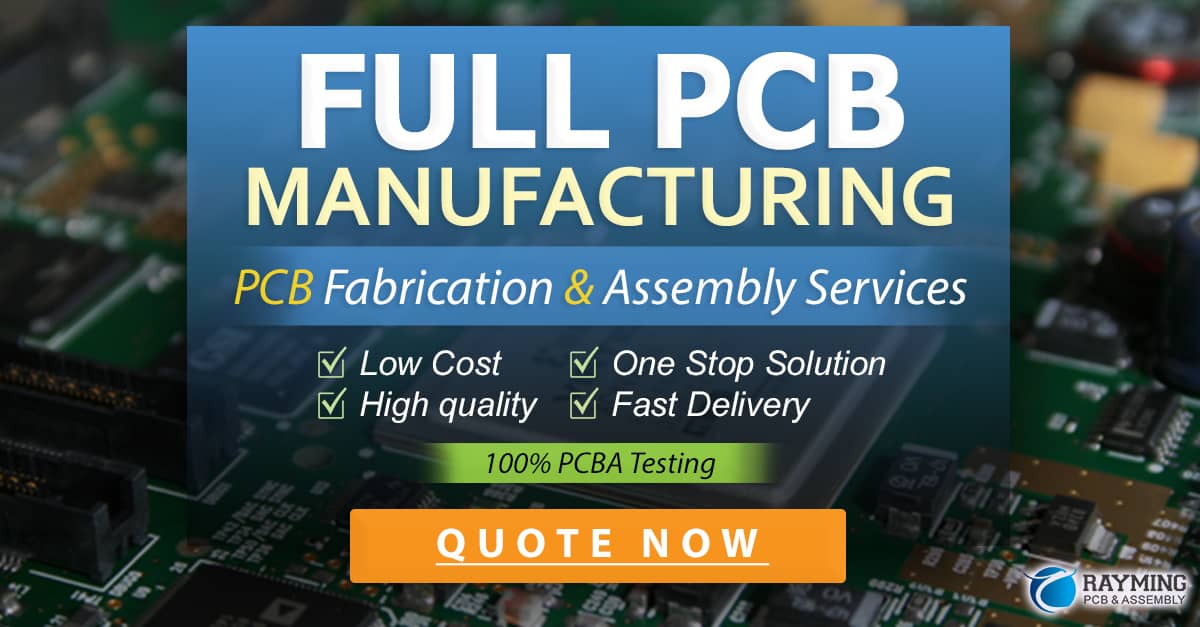
FAQ
1. What is the most cost-effective surface finish for high-volume production?
For high-volume production, HASL and OSP are the most cost-effective surface finish options. They offer good solderability and are compatible with most assembly processes. However, their limitations, such as poor flatness for HASL and short shelf life for OSP, should be considered when making the final decision.
2. Which surface finish is best suited for applications that require wire bonding?
ENEPIG is the best surface finish for applications that require wire bonding. The additional palladium layer in ENEPIG provides excellent wire bonding capability while maintaining good solderability and long shelf life. ENIG can also be used for wire bonding, but it may not offer the same level of reliability as ENEPIG.
3. Is there a surface finish that offers both excellent solderability and long shelf life?
Both IAg and ENIG offer excellent solderability and relatively long shelf life. IAg provides a flat surface and good electrical conductivity, while ENIG offers a longer shelf life and better protection against copper diffusion. The choice between the two depends on the specific requirements of the application and the project budget.
4. Can OSP be used for applications that require multiple reflow cycles?
OSP has limitations when it comes to multiple reflow cycles. The organic coating may degrade after exposure to high temperatures, leading to reduced solderability. If multiple reflow cycles are required, surface finishes like ENIG, IAg, or HASL may be more suitable.
5. What should be considered when selecting a surface finish for aerospace or military applications?
For aerospace or military applications, the surface finish must be able to withstand harsh environmental conditions and have a long lifespan. ENIG and ENEPIG are often preferred for these applications due to their excellent corrosion resistance, long shelf life, and compatibility with various assembly processes. The higher cost of these surface finishes is often justified by the increased reliability and durability required for these critical applications.
Conclusion
Selecting the most suitable surface finish for your PCB is a critical decision that impacts the reliability, functionality, and cost of the final product. By considering factors such as application requirements, solderability, cost, shelf life, and compatibility with other processes, you can narrow down the options and choose the surface finish that best meets your needs.
While no single surface finish is perfect for every application, understanding the characteristics and trade-offs of each option can help you make an informed decision. Whether you prioritize cost, solderability, or long-term reliability, there is a surface finish that can meet your requirements and ensure the success of your PCB project.
0 Comments