Understanding Electrostatic Discharge (ESD)
Before diving into the prevention strategies, it is essential to understand the basics of ESD and how it can impact electronic components.
What is ESD?
Electrostatic discharge is the sudden flow of electricity between two objects with different electrical potentials. This occurs when an electrically charged object comes into contact with an uncharged object or an object with a different electrical potential. The resulting discharge can generate high voltages and currents that can easily damage sensitive electronic components.
ESD Sensitivity of Electronic Components
Different electronic components have varying levels of sensitivity to ESD. Some components, such as metal oxide semiconductor field-effect transistors (MOSFETs) and integrated circuits (ICs), are particularly susceptible to ESD damage due to their small size and delicate internal structures.
The following table provides an overview of the ESD sensitivity levels for common electronic components:
Component Type | ESD Sensitivity Threshold (V) |
---|---|
MOSFET | 100-200 |
CMOS IC | 250-3000 |
Schottky diode | 300-2500 |
Bipolar IC | 500-4000 |
Resistor | 500-25000 |
Capacitor | 500-25000 |
As evident from the table, some components can be damaged by ESD voltages as low as 100V, while others can withstand higher voltages. It is crucial to identify the ESD sensitivity of the components used in the SMT assembly process and implement appropriate prevention measures.
ESD Prevention Strategies in SMT Assembly
To minimize the risk of ESD damage in the SMT assembly process, manufacturers should implement a comprehensive ESD prevention program that includes the following strategies:
1. ESD-Safe Workstations
One of the most effective ways to prevent ESD damage is to establish ESD-safe workstations. These workstations should be equipped with the following:
- Grounded work surfaces: Use conductive or dissipative work surfaces that are connected to a common ground point to prevent the buildup of static charges.
- Grounded operators: Ensure that operators are properly grounded using wrist straps or heel grounders connected to the common ground point.
- Ionizers: Use ionizers to neutralize static charges in the air surrounding the workstation.
- ESD-safe tools: Use ESD-safe tools, such as grounded soldering irons and dissipative tweezers, to minimize the risk of ESD events.
2. ESD-Safe Packaging and Handling
Proper packaging and handling of electronic components are crucial for preventing ESD damage. Follow these guidelines:
- Use ESD-safe packaging materials, such as static shielding bags and conductive foam, to store and transport sensitive components.
- Label ESD-sensitive components and materials clearly to ensure proper handling.
- Minimize the handling of sensitive components and only handle them when necessary.
- Use grounded wrist straps or heel grounders when handling ESD-sensitive components.
3. ESD Training and Awareness
Educating and training employees about ESD prevention is essential for maintaining an effective ESD control program. Ensure that all personnel involved in the SMT assembly process receive regular ESD training, which should cover:
- The basics of ESD and its impact on electronic components
- Proper use of ESD-safe workstations, tools, and packaging materials
- Handling procedures for ESD-sensitive components
- Recognizing and reporting ESD events
4. ESD Monitoring and Testing
Regularly monitor and test the effectiveness of the ESD prevention measures to ensure ongoing compliance and identify areas for improvement. This can include:
- Conducting periodic audits of ESD-safe workstations and practices
- Testing the resistance of grounding systems and wrist straps
- Monitoring the voltage levels on ESD-sensitive components during handling and assembly
- Investigating and addressing any reported ESD events
5. Humidity Control
Maintaining appropriate humidity levels in the SMT assembly environment can help minimize the risk of ESD events. Higher humidity levels (typically 40-60% relative humidity) can help dissipate static charges more efficiently. Consider installing humidity control systems in the production area to maintain optimal humidity levels.
Frequently Asked Questions (FAQ)
-
What is the most common cause of ESD damage in SMT assembly?
The most common cause of ESD damage in SMT assembly is improper handling of ESD-sensitive components. This can occur when operators are not properly grounded or when components are not stored or transported in ESD-safe packaging materials. -
How often should ESD training be conducted?
ESD training should be conducted at least annually for all personnel involved in the SMT assembly process. New employees should receive ESD training as part of their onboarding process, and refresher training should be provided as needed. -
What is the recommended humidity level for ESD prevention in SMT assembly?
The recommended humidity level for ESD prevention in SMT assembly is typically between 40-60% relative humidity. This level helps dissipate static charges more efficiently, reducing the risk of ESD events. -
Can ESD damage be detected visually?
In many cases, ESD damage cannot be detected visually, as it often occurs within the internal structure of the electronic component. However, some ESD events may cause visible damage, such as scorch marks or melted components. -
How can I test the effectiveness of my ESD prevention measures?
To test the effectiveness of your ESD prevention measures, you can conduct periodic audits of ESD-safe workstations and practices, test the resistance of grounding systems and wrist straps, and monitor the voltage levels on ESD-sensitive components during handling and assembly. Additionally, investigating and addressing any reported ESD events can help identify areas for improvement.
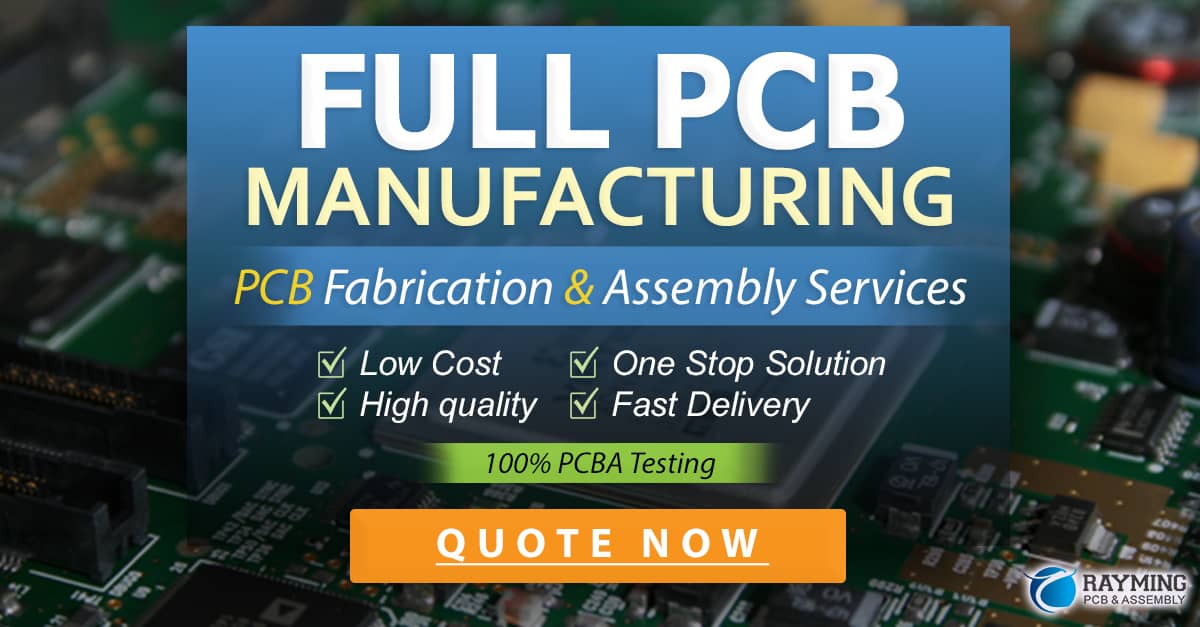
Conclusion
Preventing ESD damage in the SMT assembly process is crucial for ensuring the production of high-quality electronic products and minimizing production costs. By implementing a comprehensive ESD prevention program that includes ESD-safe workstations, proper packaging and handling procedures, employee training, and regular monitoring and testing, manufacturers can significantly reduce the risk of ESD-related issues.
Remember, ESD prevention is an ongoing process that requires continuous improvement and vigilance. By staying up-to-date with the latest ESD prevention strategies and technologies and fostering a culture of ESD awareness among employees, manufacturers can maintain a high level of ESD control and produce reliable electronic products that meet the demands of their customers.
0 Comments