Factors Affecting In-circuit test cost
PCB Complexity
The complexity of the PCB is one of the primary factors that determine the cost of in-circuit testing. PCBs with a higher number of components, layers, and test points require more time and resources to test, resulting in increased costs. The following table illustrates the relationship between PCB complexity and the associated testing costs:
PCB Complexity | Number of Components | Number of Layers | Test Points | Relative Cost |
---|---|---|---|---|
Simple | < 100 | 1-2 | < 50 | Low |
Moderate | 100-500 | 2-4 | 50-200 | Medium |
Complex | 500-1000 | 4-8 | 200-500 | High |
Very Complex | > 1000 | > 8 | > 500 | Very High |
As evident from the table, the cost of in-circuit testing increases with the complexity of the PCB. Simple PCBs with fewer components and layers require less time and resources to test, resulting in lower costs. On the other hand, very complex PCBs with a large number of components, layers, and test points demand more extensive testing, leading to higher costs.
Test Coverage
The extent of test coverage required for a PCB also influences the cost of in-circuit testing. Test coverage refers to the percentage of components and connections that are tested during the ICT process. Higher test coverage provides a more thorough evaluation of the PCB’s functionality but also increases the testing time and cost. The following table shows the relationship between test coverage and the associated costs:
Test Coverage | Relative Cost |
---|---|
Basic (80%) | Low |
Standard (90%) | Medium |
High (95%) | High |
Full (100%) | Very High |
Basic test coverage, which typically tests around 80% of the PCB’s components and connections, is the most cost-effective option. However, it may not be sufficient for critical applications or high-reliability products. Standard test coverage, which tests approximately 90% of the PCB, is a more common choice and provides a good balance between cost and quality assurance. High and full test coverage options, testing 95% and 100% of the PCB respectively, offer the most comprehensive testing but come with a higher price tag.
Production Volume
The volume of PCBs being produced and tested also plays a significant role in determining the cost of in-circuit testing. Higher production volumes can lead to lower per-unit testing costs due to economies of scale. The following table illustrates the relationship between production volume and the associated testing costs:
Production Volume | Relative Cost per Unit |
---|---|
Low (< 1,000) | High |
Medium (1,000-10,000) | Medium |
High (10,000-100,000) | Low |
Very High (> 100,000) | Very Low |
For low-volume production runs, the fixed costs associated with setting up the test equipment and programming the test software are spread across fewer units, resulting in higher per-unit testing costs. As the production volume increases, these fixed costs are distributed over a larger number of units, leading to lower per-unit testing costs. Very high-volume production runs benefit from significant cost savings due to the efficient utilization of testing resources and optimized processes.
Test Equipment and Software
The cost of in-circuit testing is also influenced by the test equipment and software used. Specialized ICT equipment, such as bed-of-nails fixtures and flying probe testers, can be expensive to purchase or rent. Additionally, the test software used to program and execute the tests may require licensing fees or subscription costs. The following table provides an overview of the costs associated with test equipment and software:
Equipment/Software | Cost Range |
---|---|
Bed-of-Nails Fixture | $10,000-$50,000 |
Flying Probe Tester | $100,000-$500,000 |
Test Software License | $1,000-$10,000 per year |
The cost of test equipment and software can be a significant investment for manufacturers, especially for those with limited production volumes. However, these costs can be justified by the improved product quality, reduced defect rates, and faster time-to-market that in-circuit testing provides.
Labor Costs
Labor costs associated with setting up, programming, and operating the in-circuit test equipment also contribute to the overall cost of testing. Skilled technicians and engineers are required to develop test plans, create test programs, and analyze test results. The following table provides an estimate of the labor costs involved in in-circuit testing:
Role | Hourly Rate |
---|---|
Test Technician | $20-$40 |
Test Engineer | $40-$80 |
Test Manager | $60-$120 |
The labor costs can vary depending on the complexity of the PCB, the test coverage required, and the experience level of the personnel involved. Manufacturers often balance the labor costs with the benefits of in-circuit testing, such as improved product reliability and reduced warranty claims.
Cost Reduction Strategies
While in-circuit testing can be expensive, there are several strategies manufacturers can employ to reduce the overall cost of testing without compromising on quality:
Design for Testability
Designing PCBs with testability in mind can significantly reduce the cost of in-circuit testing. This involves incorporating test points, boundary scan architecture, and other features that facilitate easier testing. By considering testability during the design phase, manufacturers can reduce the time and resources required for testing, resulting in lower costs.
Standardization
Standardizing PCB designs and components can help reduce the cost of in-circuit testing. By using common components and design practices across multiple products, manufacturers can develop test programs and fixtures that can be reused, reducing the overall testing costs. Standardization also helps in reducing the inventory of spare parts and minimizing the need for custom test solutions.
Outsourcing
Outsourcing in-circuit testing to specialized service providers can be a cost-effective solution for manufacturers, particularly those with limited production volumes or lack of in-house testing capabilities. Outsourcing allows manufacturers to leverage the expertise and resources of the service provider, reducing the need for capital investment in test equipment and software. However, it is essential to carefully evaluate the quality and reliability of the service provider to ensure that the outsourced testing meets the required standards.
Automated Testing
Implementing automated testing solutions can help reduce the labor costs associated with in-circuit testing. Automated test equipment (ATE) can perform tests faster and more consistently than manual testing, reducing the time and resources required. Additionally, automated testing can help identify defects early in the production process, reducing the cost of rework and scrap.
Frequently Asked Questions (FAQ)
-
Q: What is the average cost of in-circuit testing for a simple PCB?
A: The average cost of in-circuit testing for a simple PCB with fewer than 100 components and 1-2 layers can range from $500 to $1,500, depending on the test coverage and production volume. -
Q: How does the production volume affect the cost of in-circuit testing?
A: Higher production volumes generally lead to lower per-unit testing costs due to economies of scale. As the fixed costs associated with setting up the test equipment and programming the test software are spread across a larger number of units, the per-unit testing cost decreases. -
Q: Can in-circuit testing be performed in-house, or is it necessary to outsource?
A: In-circuit testing can be performed in-house if the manufacturer has the necessary test equipment, software, and skilled personnel. However, for manufacturers with limited production volumes or lack of in-house testing capabilities, outsourcing to specialized service providers can be a cost-effective solution. -
Q: What are the benefits of investing in in-circuit testing despite the costs?
A: Investing in in-circuit testing, despite the costs, provides several benefits, such as improved product quality, reduced defect rates, faster time-to-market, and lower warranty claims. In-circuit testing helps identify defects early in the production process, reducing the cost of rework and scrap, and ultimately leading to higher customer satisfaction. -
Q: Are there any cost reduction strategies for in-circuit testing?
A: Yes, there are several cost reduction strategies for in-circuit testing, including designing for testability, standardizing PCB designs and components, outsourcing to specialized service providers, and implementing automated testing solutions. These strategies help in reducing the time, resources, and labor costs associated with in-circuit testing.
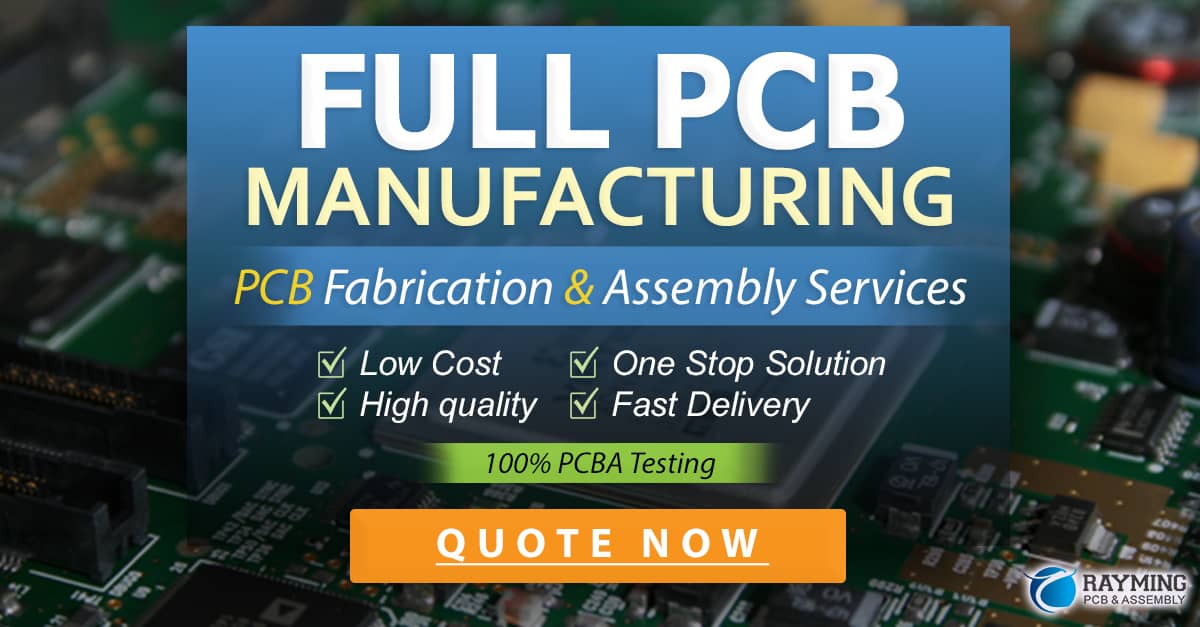
Conclusion
In-circuit testing is a critical step in ensuring the quality and reliability of electronic PCBs. The cost of in-circuit testing can vary significantly depending on factors such as PCB complexity, test coverage, production volume, test equipment and software, and labor costs. Manufacturers must carefully evaluate these factors and consider cost reduction strategies, such as design for testability, standardization, outsourcing, and automated testing, to balance the costs and benefits of in-circuit testing.
By understanding the various aspects that influence the cost of in-circuit testing and implementing appropriate cost reduction strategies, manufacturers can optimize their testing processes, reduce overall costs, and maintain high product quality standards. Ultimately, investing in in-circuit testing, despite the costs, can lead to improved product reliability, reduced warranty claims, and higher customer satisfaction, providing a strong return on investment for manufacturers in the long run.
0 Comments