What is LPI Solder Mask?
Liquid photoimageable (LPI) solder mask is a photosensitive polymer coating applied to printed circuit boards (PCBs) to protect the copper traces, prevent solder bridges, and provide electrical insulation. LPI solder mask selectively covers the areas of the PCB where components will not be soldered, while leaving the pads and other features exposed for soldering.
The key advantages of LPI solder mask compared to other types include:
Advantage | Description |
---|---|
High resolution | Allows for finer pitch components and traces |
Even coating | Provides consistent thickness across the board |
Excellent adhesion | Bonds well to the copper and laminate surface |
Thermal resistance | Withstands high temperatures during soldering |
Durability | Resists scratching and damage during handling |
The LPI Solder Mask Application Process
Applying LPI solder mask to a PCB involves several steps to ensure proper coverage and patterning of the coating. The general process flow is as follows:
1. Surface Preparation
Before the solder mask can be applied, the bare PCB must be cleaned and conditioned to promote good adhesion. This typically involves:
- Scrubbing the copper surfaces to remove oxide
- Micro-etching to roughen the surface
- Cleaning to remove any contaminants
- Pre-baking to drive off moisture
2. Solder Mask Coating
The liquid solder mask is applied to the prepared PCB surface using one of several methods:
Method | Description | Thickness |
---|---|---|
Screen printing | Mask pushed through a fine mesh screen | 0.5-2 mils |
Curtain coating | PCB passed through a curtain of falling mask | 1-4 mils |
Spray coating | Liquid mask sprayed onto the PCB | 0.5-2 mils |
The mask must be applied in an even layer of the appropriate thickness, typically 1-2 mils (25-50 microns). Too thin of a coating may not provide adequate coverage, while too thick makes it difficult to properly expose and develop the mask.
3. Pre-baking
After coating, the panels are pre-baked in an oven to partially cure the mask and drive off any remaining solvents. Typical conditions are 80-90°C for 20-30 minutes. The pre-bake solidifies the mask so it can withstand handling during the subsequent steps.
4. Exposure
The coated panels are exposed to UV light through a phototool or photomask. The transparent areas of the phototool allow the UV light to crosslink and harden the solder mask in the desired pattern. The exposure energy, typically 300-500 mJ/cm2, must be carefully controlled to fully cross-link the exposed areas without overcuring.
5. Development
After exposure, the unexposed areas of the mask are selectively removed in an alkaline solution known as the developer. The developer chemically breaks down the non-crosslinked polymer, leaving behind the hardened mask pattern. Spray or immersion developing systems are used, with 1-3% sodium or potassium carbonate solutions at 30-40°C.
Following developing, the panels are rinsed to remove any residual developer and then oven dried.
6. Final Cure
To fully harden the solder mask pattern, the panels undergo a final thermal cure. This can be done in a batch oven or a conveyorized system at temperatures of 130-150°C for 60-90 minutes. The final cure further crosslinks the mask and improves its chemical, heat, and moisture resistance properties.
7. Final Finishing
After cure, the panels may receive additional surface finishing to enhance solderability or prepare them for the next fabrication steps. Options include:
- HAL (hot air solder leveling) to coat exposed pads with solder
- ENIG (electroless nickel immersion gold) plating of pads
- Routing or scoring to remove excess material and singulate boards
- Electrical test to verify continuity and isolation
- Visual inspection for coating defects or misregistration
Controlling the LPI Solder Mask Process
Achieving a high-quality and reliable LPI solder mask coating requires careful control of multiple process parameters. Some of the key factors include:
Material Selection
LPI solder masks are formulated from epoxy or acrylic monomers, photoimageable compounds, fillers, and pigments. The exact composition determines properties like:
- Viscosity and flow behavior
- UV sensitivity and resolution
- Adhesion to copper and laminate
- Thermal, chemical and moisture resistance
- Appearance and color
Selecting the appropriate mask formulation requires balancing the performance requirements with the processing parameters to achieve the desired results.
Equipment Set-up
The coating, exposure, and developing equipment must be properly set up and calibrated to ensure consistent results. This includes:
- Controlling the coating viscosity, thickness, and uniformity
- Setting the exposure energy and time based on the phototool
- Maintaining the developer concentration, temperature, and spray pressure
- Verifying the oven profiles for pre-bake and final cure
Regular preventative maintenance, including cleaning and replacement of consumable items, is also critical for consistent performance.
Process Control
Multiple process variables must be monitored and controlled to achieve the desired solder mask properties. Some of the key parameters include:
Parameter | Typical Range | Effect of Variation |
---|---|---|
Coating thickness | 1-2 mils | Resolution, coverage, adhesion |
Pre-bake conditions | 80-90°C, 20-30 min | Solvent removal, handling strength |
Exposure energy | 300-500 mJ/cm2 | Resolution, surface tackiness |
Developer concentration | 1-3% | Developing speed, residue |
Developer temperature | 30-40°C | Developing speed, surface roughness |
Final cure temperature | 130-150°C | Chemical & heat resistance, adhesion |
Final cure time | 60-90 min | Degree of crosslinking, brittleness |
Establishing the appropriate operating ranges and monitoring the process variables with SPC (statistical process control) methods allows for early detection and correction of issues.
Troubleshooting Common Defects
Even with a well-controlled process, various defects may occur that impact the quality and reliability of the solder mask. Some common issues and their potential causes include:
Defect | Potential Causes |
---|---|
Poor adhesion | Inadequate surface prep, underexposure, undercure |
Incomplete developing | Low exposure, weak or cold developer, insufficient developing time |
Rough or pitted surface | High exposure energy, strong or hot developer |
Poor resolution | Thick coating, low exposure, phototool issues |
Discoloration or yellowing | Overcure, UV degradation, chemical attack |
Identifying the root cause of defects often requires a systematic approach of isolating the variables, performing experiments, and analyzing the results. Corrective actions may involve adjusting the process settings, modifying the materials, or improving the maintenance procedures.
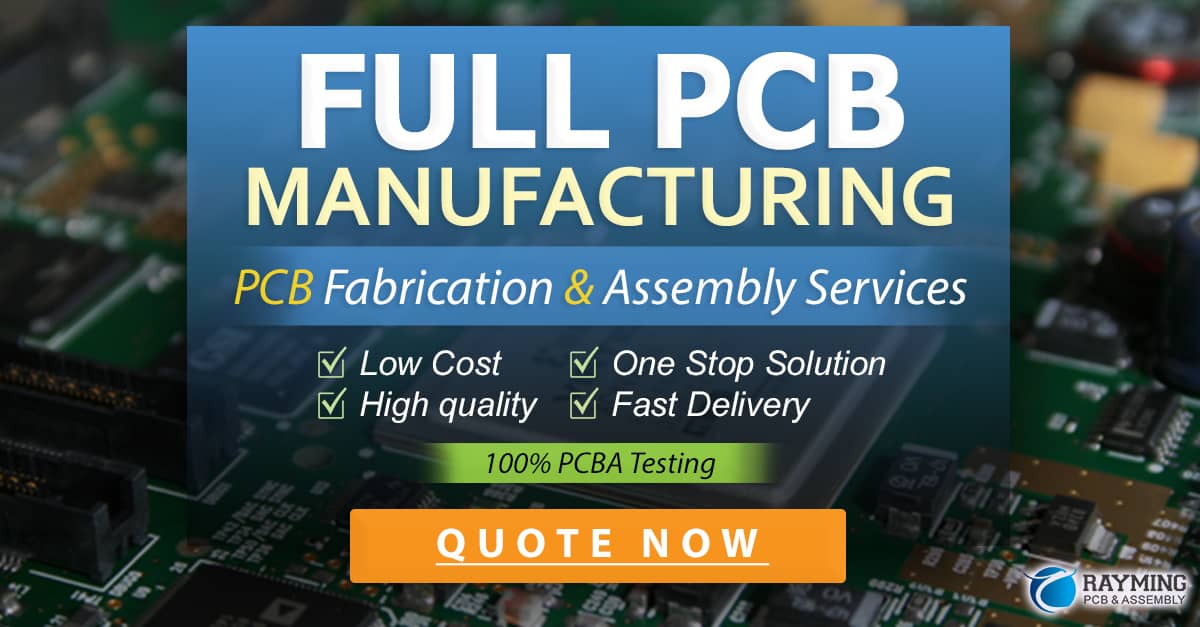
Evaluating LPI Solder Mask Performance
The quality and reliability of an LPI solder mask coating are ultimately determined by its ability to meet the performance requirements in the end-use environment. Some of the key properties and test methods used to evaluate LPI masks include:
Adhesion
Solder mask adhesion to the copper and laminate is critical for long-term reliability, particularly under thermal cycling and mechanical stress. Adhesion is typically evaluated by cross-hatch tape testing per IPC-TM-650 2.4.1 or peel testing per IPC-TM-650 2.4.8.
Insulation Resistance
The solder mask must provide adequate electrical insulation between conductors, even under high humidity conditions. Insulation resistance is measured per IPC-TM-650 2.6.3, with a minimum value of 500 MΩ required after exposure to 90% RH at 35°C for 7 days.
Solderability
The exposed pads and holes must be solderable without dewetting or non-wetting. Solderability is evaluated per IPC J-STD-003, with a minimum of 95% coverage required after aging for 8 hours at 155°C.
Hardness
The cured solder mask must be hard enough to resist scratching and abrasion during handling and assembly. Hardness is typically measured using the pencil hardness test per IPC-TM-650 2.4.27, with a minimum value of 6H required.
Flammability
For applications requiring UL listing, the solder mask must meet the flammability requirements of UL 94V-0. This involves self-extinguishing within 10 seconds after removal of the flame, with no flaming drips allowed.
Compatibility
The solder mask must be compatible with the other materials and processes used in PCB fabrication and assembly. This includes resistance to molten solder, fluxes, cleaning agents, and conformal coatings. Compatibility testing is often performed using production processes and environments to verify performance.
By carefully controlling the application process and verifying the performance through testing, LPI solder mask can provide reliable protection and insulation for a wide range of PCB applications.
FAQ
What is the difference between LPI and dry film solder mask?
LPI solder mask is applied as a liquid and then patterned using photolithography, while dry film is a solid sheet that is laminated to the PCB and then patterned. LPI offers higher resolution and finer pitch capability compared to dry film.
Can LPI solder mask be applied over HASL or OSP coatings?
No, LPI solder mask must be applied directly to the bare copper surfaces of the PCB. HASL or OSP coatings are applied after the solder mask to protect the exposed pads from oxidation.
What is the typical curing temperature and time for LPI solder mask?
LPI solder mask is typically cured at 130-150°C for 60-90 minutes, depending on the specific formulation and performance requirements. The curing step crosslinks the polymer and enhances its final properties.
How does the solder mask color affect the processing parameters?
Different pigments and dyes used to create colored solder masks can affect the UV sensitivity and exposure time. In general, darker colors like blue, black, and green require longer exposure times compared to lighter colors like white, yellow, and clear.
What is the shelf life of LPI solder mask?
Most LPI solder mask formulations have a shelf life of 6-12 months when stored at room temperature in sealed containers. The mask may start to gel or increase in viscosity over time, which can affect its processing and final properties. It is important to use the mask before its expiration date and to follow the manufacturer’s storage and handling guidelines.
0 Comments