The Importance of PCB Electrical Testing
Electrical testing is an essential step in the PCB manufacturing process for several reasons:
-
Quality Assurance: Electrical testing helps identify any defects or issues with the PCB, ensuring that only high-quality boards are delivered to the customer.
-
Functionality Verification: By testing the electrical properties of the PCB, manufacturers can confirm that the board functions as designed and meets the required specifications.
-
Reliability: Thorough electrical testing helps improve the reliability of the PCB, reducing the risk of failures or malfunctions in the final application.
-
Cost Savings: Identifying and addressing issues early in the manufacturing process through electrical testing can save significant costs associated with rework or product recalls.
Types of PCB Electrical Tests
There are several types of electrical tests performed during PCB manufacturing, each designed to assess different aspects of the board’s functionality. Some of the most common tests include:
Continuity Testing
Continuity testing is performed to ensure that all the intended connections on the PCB are intact and that there are no unintended short circuits. This test is typically done using a Continuity Tester or a Multimeter, which applies a small current to the circuit and measures the resistance between two points. If the resistance is within the expected range, the connection is considered good.
Isolation Testing
Isolation testing, also known as insulation resistance testing, is conducted to verify that there are no leakages or shorts between different circuits on the PCB. This test is crucial for ensuring the safety and reliability of the board, especially in high-voltage applications. An isolation tester applies a high voltage between different points on the PCB and measures the resistance. If the resistance is above a specified threshold, the isolation is considered adequate.
High-Voltage Testing
High-voltage testing is performed to assess the PCB’s ability to withstand high voltages without breaking down or experiencing any unintended leakage. This test is particularly important for boards used in power electronics or high-voltage applications. A high-voltage tester applies a specified voltage across different points on the PCB and monitors the current flow. If the current remains below a certain threshold, the board passes the test.
Impedance Testing
Impedance testing is used to measure the impedance of the PCB’s traces, which is crucial for high-speed and RF applications. The impedance of a trace affects the signal integrity and can lead to reflections and distortions if not properly controlled. An impedance tester measures the characteristic impedance of the traces and compares it to the specified value. If the impedance is within the acceptable range, the board passes the test.
Functional Testing
Functional testing is performed to verify that the PCB performs its intended functions as designed. This test involves applying input signals to the board and measuring the output signals to ensure they match the expected values. Functional testing can be done using a variety of equipment, such as oscilloscopes, logic analyzers, and specialized test fixtures.
PCB Electrical Testing Equipment
To perform the various electrical tests on PCBs, manufacturers use a range of specialized equipment. Some of the most common pieces of equipment include:
Flying probe tester
A flying probe tester is an automated testing machine that uses movable probes to make contact with specific points on the PCB. These testers are highly versatile and can perform a wide range of electrical tests, including continuity, isolation, and impedance testing. Flying probe testers are ideal for low-volume production or prototype testing, as they do not require custom test fixtures.
Advantage | Disadvantage |
---|---|
Versatility | Slower than fixture-based testing |
No custom fixtures required | Higher cost per test |
Ideal for low-volume or prototype testing | Limited test coverage compared to fixtu res |
In-Circuit Tester (ICT)
An in-circuit tester is a fixture-based testing system that uses a bed-of-nails fixture to make contact with specific points on the PCB. ICTs are designed to perform a comprehensive set of electrical tests, including continuity, isolation, and component value verification. These testers are highly automated and can test multiple boards simultaneously, making them ideal for high-volume production.
Advantage | Disadvantage |
---|---|
High test coverage | Requires custom test fixtures |
Fast testing speed | Higher initial setup costs |
Ideal for high-volume production | Limited flexibility for design changes |
Boundary Scan Tester
A boundary scan tester is a specialized testing system that uses the JTAG (Joint Test Action Group) interface to test the interconnections and functionality of digital components on the PCB. This tester relies on the boundary scan architecture built into the components, which allows access to their input and output pins. Boundary scan testing is particularly useful for testing complex boards with high component density, as it can test the interconnections between components without requiring physical access.
Advantage | Disadvantage |
---|---|
Tests complex boards with high component density | Requires components with boundary scan architecture |
No physical access to components required | Limited to digital components |
Ideal for testing interconnections between components | Requires specialized software and knowledge |
Automated Optical Inspection (AOI)
While not strictly an electrical testing method, automated optical inspection is often used in conjunction with electrical testing to identify any visible defects on the PCB. AOI systems use high-resolution cameras and advanced image processing algorithms to detect issues such as missing components, incorrect component placement, and solder defects. By combining AOI with electrical testing, manufacturers can achieve a more comprehensive quality control process.
Advantage | Disadvantage |
---|---|
Detects visible defects | Cannot detect electrical faults |
Fast inspection speed | Requires specialized lighting and camera setup |
Ideal for identifying component placement and solder issues | May require multiple inspection angles for complex boards |
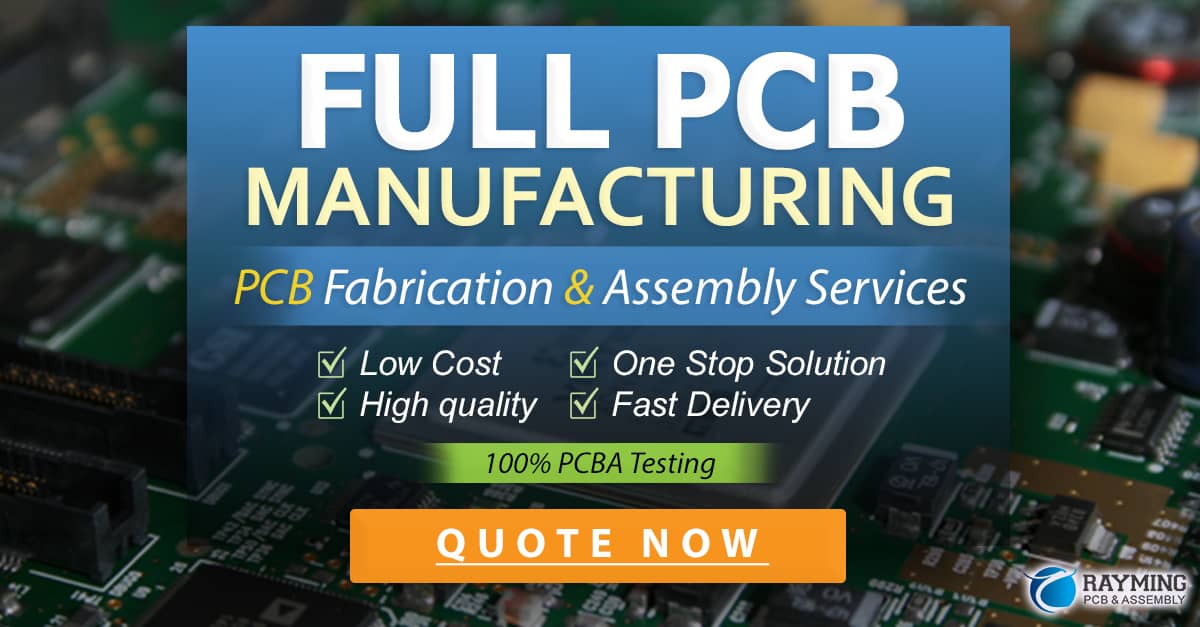
The PCB Electrical Testing Process
The electrical testing process typically follows a specific sequence to ensure that all aspects of the PCB’s functionality are thoroughly tested. The general steps in the process include:
-
Visual Inspection: Before electrical testing begins, the PCB undergoes a visual inspection to identify any obvious defects or issues.
-
Continuity Testing: Continuity testing is performed to verify that all intended connections are intact and that there are no unintended short circuits.
-
Isolation Testing: Isolation testing is conducted to ensure that there are no leakages or shorts between different circuits on the PCB.
-
Component Testing: Individual components on the PCB are tested to verify their functionality and ensure they meet the required specifications.
-
High-Voltage Testing (if applicable): For PCBs used in high-voltage applications, a high-voltage test is performed to assess the board’s ability to withstand the specified voltage levels.
-
Impedance Testing (if applicable): For high-speed and RF applications, impedance testing is conducted to ensure that the PCB’s traces meet the required impedance specifications.
-
Functional Testing: Functional testing is performed to verify that the PCB performs its intended functions as designed, with input signals applied and output signals measured.
-
Boundary Scan Testing (if applicable): For PCBs with components that support boundary scan architecture, boundary scan testing is performed to test the interconnections and functionality of the digital components.
-
Final Inspection: After all electrical tests are completed, a final visual inspection is performed to ensure that the PCB has not been damaged during the testing process.
Challenges in PCB Electrical Testing
While electrical testing is a critical step in ensuring the quality and functionality of PCBs, it also presents several challenges that manufacturers must address:
-
Test Coverage: Ensuring that all aspects of the PCB’s functionality are adequately tested can be challenging, especially for complex boards with high component density.
-
Test Fixture Design: For fixture-based testing systems like ICTs, designing and fabricating custom test fixtures can be time-consuming and expensive.
-
Test Program Development: Developing comprehensive test programs that cover all the necessary electrical tests requires specialized knowledge and can be a complex and time-consuming process.
-
Keeping Up with Technology: As PCB technology advances, with smaller components and higher frequencies, electrical testing equipment and methods must also evolve to keep pace.
-
Balancing Cost and Quality: Manufacturers must strike a balance between the cost of electrical testing and the desired level of quality and reliability for the PCB.
Conclusion
Electrical testing is a vital aspect of PCB manufacturing, ensuring that the final product meets the required specifications and performs as intended. By conducting a range of tests, including continuity, isolation, high-voltage, impedance, and functional testing, manufacturers can identify and address any issues early in the production process, ultimately leading to higher quality and more reliable PCBs.
As PCB technology continues to advance, electrical testing methods and equipment must also evolve to keep pace. Manufacturers must stay up-to-date with the latest testing technologies and best practices to ensure that their products meet the ever-increasing demands of the electronics industry.
By understanding the importance of electrical testing, the different types of tests performed, and the equipment used in the process, PCB designers and manufacturers can work together to create high-quality, reliable products that meet the needs of their customers.
Frequently Asked Questions (FAQ)
-
What is the purpose of electrical testing in PCB manufacturing?
Electrical testing in PCB manufacturing is performed to ensure that the board functions as intended, meets the required specifications, and is free from defects or issues that could affect its performance or reliability. -
What are the most common types of electrical tests performed on PCBs?
The most common types of electrical tests performed on PCBs include continuity testing, isolation testing, high-voltage testing, impedance testing, and functional testing. -
What is the difference between a flying probe tester and an in-circuit tester?
A flying probe tester uses movable probes to make contact with specific points on the PCB and is ideal for low-volume production or prototype testing. An in-circuit tester, on the other hand, uses a bed-of-nails fixture to make contact with the PCB and is better suited for high-volume production. -
What is boundary scan testing, and when is it used?
Boundary scan testing is a specialized testing method that uses the JTAG interface to test the interconnections and functionality of digital components on the PCB. It is particularly useful for testing complex boards with high component density, where physical access to components may be limited. -
How can manufacturers balance the cost of electrical testing with the desired level of quality and reliability?
Manufacturers can balance the cost of electrical testing with the desired level of quality and reliability by carefully selecting the appropriate testing methods and equipment for their specific needs, optimizing test programs to minimize unnecessary tests, and regularly reviewing and updating their testing processes to ensure efficiency and effectiveness.
0 Comments