What is Thermal dissipation?
Thermal dissipation refers to the process of transferring heat away from a heat source to the surrounding environment. This is essential for maintaining the temperature of the heat source within its optimal operating range, preventing overheating and potential damage. Thermal dissipation is achieved through various heat transfer mechanisms, including conduction, convection, and radiation.
Conduction
Conduction is the transfer of heat through direct contact between two objects or materials. In the context of thermal dissipation, conduction occurs when heat is transferred from the heat source to a heat sink, which is a material or device designed to absorb and dissipate the heat. Heat sinks are typically made of materials with high thermal conductivity, such as copper or aluminum, to facilitate efficient heat transfer.
Convection
Convection is the transfer of heat through the movement of fluids or gases. In cooling systems, convection is often employed by using fans or other air-moving devices to circulate cool air around the heat source, absorbing the heat and carrying it away. Liquid cooling systems also rely on convection, using pumps to circulate coolant through heat exchangers to remove heat from the source.
Radiation
Radiation is the transfer of heat through electromagnetic waves, without the need for direct contact or a medium. While radiation plays a minor role in most cooling systems, it can be significant in high-temperature applications or in vacuum environments where conduction and convection are limited.
Passive Cooling Techniques
Passive cooling techniques rely on the natural heat transfer mechanisms without the use of active components such as fans or pumps. These techniques are often simple, reliable, and energy-efficient, making them suitable for a wide range of applications.
Heat Sinks
Heat sinks are the most common passive cooling devices, designed to increase the surface area available for heat dissipation. They are typically made of materials with high thermal conductivity, such as aluminum or copper, and feature fins or other protrusions to maximize the surface area in contact with the surrounding air. Heat sinks work by conducting heat away from the source and dissipating it through convection and radiation to the environment.
Material | Thermal Conductivity (W/mK) |
---|---|
Copper | 401 |
Aluminum | 237 |
Silver | 429 |
Gold | 318 |
Diamond | 2,300 |
Heat Pipes
Heat pipes are passive cooling devices that combine the principles of conduction and convection to efficiently transfer heat from a source to a remote heat sink. A heat pipe consists of a sealed tube containing a working fluid, such as water or alcohol, that undergoes a phase change (evaporation and condensation) to facilitate heat transfer.
As heat is applied to one end of the heat pipe (the evaporator), the working fluid vaporizes, absorbing the heat. The vapor then travels along the length of the tube to the other end (the condenser), where it cools and condenses, releasing the heat to the heat sink. The condensed fluid then returns to the evaporator through capillary action or gravity, completing the cycle.
Thermal Interface Materials
Thermal interface materials (TIMs) are substances applied between the heat source and the heat sink to enhance thermal conductivity and minimize air gaps, which can act as thermal insulators. TIMs come in various forms, such as thermal greases, pads, and adhesives, each with its own advantages and disadvantages.
TIM Type | Thermal Conductivity (W/mK) | Advantages | Disadvantages |
---|---|---|---|
Thermal Grease | 2-8 | High thermal conductivity, easy to apply | Messy, can dry out over time |
Thermal Pad | 1-5 | Easy to apply, no mess | Lower thermal conductivity than grease |
Thermal Adhesive | 1-2 | Permanent bond, no mess | Difficult to remove, lower conductivity |
Graphite Sheet | 10-100 | High thermal conductivity, thin, easy to apply | Fragile, can be expensive |
Active Cooling Techniques
Active cooling techniques employ powered components, such as fans or pumps, to enhance heat transfer and improve thermal dissipation. These techniques are often used in high-performance applications or when passive cooling alone is insufficient to maintain the desired operating temperature.
Forced Air Cooling
Forced air cooling is a common active cooling method that uses fans to generate airflow over the heat source and heat sink. The increased airflow enhances convective heat transfer, allowing for more efficient thermal dissipation. Forced air cooling is widely used in electronic devices, such as computers and gaming consoles, as well as in automotive and industrial applications.
Liquid Cooling
Liquid cooling systems use a coolant, such as water or a specialized liquid, to absorb heat from the source and transfer it to a remote heat exchanger. The coolant is circulated through a closed loop using a pump, and the heat is dissipated through the heat exchanger, which can be a radiator or a liquid-to-air heat exchanger.
Liquid cooling offers several advantages over air cooling, including:
– Higher thermal conductivity of liquids compared to air
– More efficient heat transfer due to the higher heat capacity of liquids
– Ability to transport heat over longer distances
– Quieter operation compared to fans
However, liquid cooling systems are more complex and expensive than air cooling, and they require regular maintenance to prevent leaks and ensure optimal performance.
Thermoelectric Cooling
Thermoelectric cooling, also known as Peltier cooling, is a solid-state cooling method that uses the Peltier effect to create a temperature difference between two sides of a thermoelectric module. When an electric current is applied to the module, heat is absorbed on one side (the cold side) and released on the other side (the hot side), effectively pumping heat from the cold side to the hot side.
Thermoelectric cooling is compact, silent, and has no moving parts, making it suitable for applications where reliability and low maintenance are essential. However, thermoelectric modules have lower efficiency compared to other cooling methods and are best suited for small-scale cooling applications.
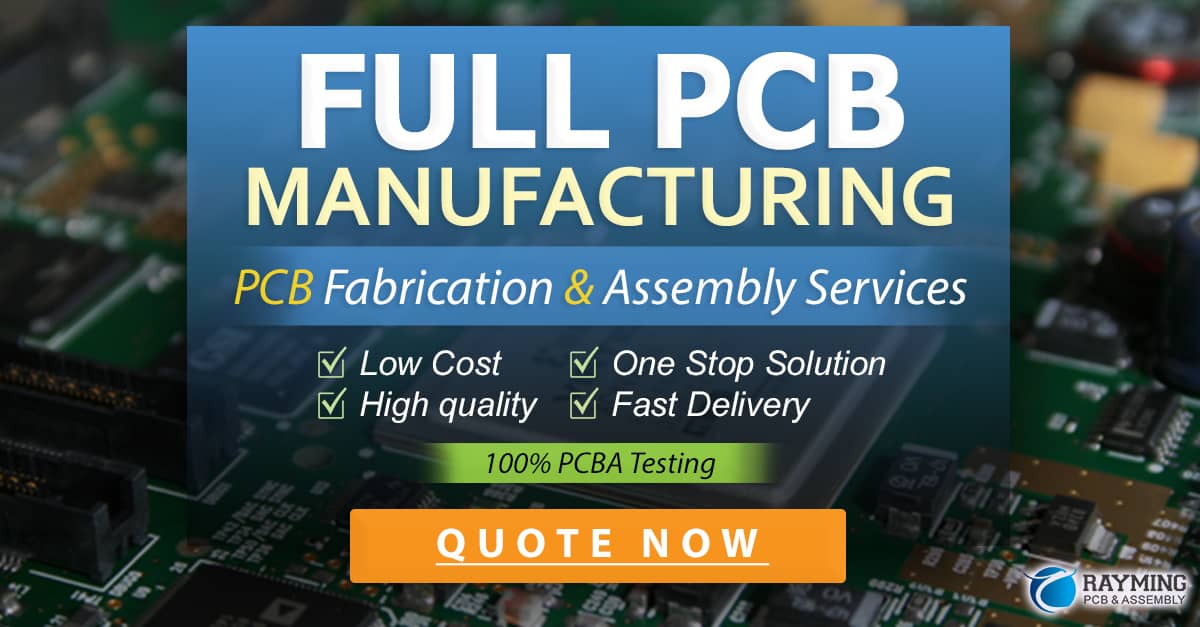
Advanced Cooling Techniques
In addition to the conventional cooling techniques discussed above, there are several advanced cooling methods that are being researched and developed for specific applications or to address the limitations of traditional cooling approaches.
Phase Change Materials
Phase change materials (PCMs) are substances that absorb or release large amounts of heat during a phase transition, such as melting or solidification. By incorporating PCMs into cooling systems, the heat absorbed by the PCM during the phase change can help stabilize the temperature of the heat source, providing a buffer against temperature fluctuations.
PCMs can be used in various forms, such as encapsulated beads or embedded in matrix materials, and they can be integrated into heat sinks, thermal interface materials, or even directly into the heat source itself.
Nanofluids
Nanofluids are colloidal suspensions of nanoscale particles (typically less than 100 nm in size) in a base fluid, such as water or oil. These nanoparticles, which can be made of metals, oxides, or carbon-based materials, have extremely high thermal conductivity compared to the base fluid, enhancing the overall heat transfer properties of the nanofluid.
Nanofluids can be used as coolants in liquid cooling systems or as additives in thermal interface materials to improve their performance. However, the long-term stability and potential health and environmental risks associated with nanoparticles are still under investigation.
Oscillating Heat Pipes
Oscillating heat pipes (OHPs) are a type of passive cooling device that combines the principles of heat pipes and thermosyphons. An OHP consists of a serpentine capillary tube partially filled with a working fluid. As heat is applied to the OHP, the fluid inside the tube undergoes oscillatory motion due to the alternating evaporation and condensation of the fluid in the different sections of the tube.
This oscillatory motion enhances heat transfer by promoting mixing and turbulence within the fluid, leading to improved thermal dissipation compared to traditional heat pipes. OHPs are compact, lightweight, and can be easily integrated into various systems, making them an attractive option for cooling applications in aerospace, electronics, and other industries.
Conclusion
Thermal dissipation is a critical aspect of cooling systems, and there are numerous techniques available to achieve efficient heat transfer and maintain optimal operating temperatures. From passive methods like heat sinks and heat pipes to active techniques such as forced air and liquid cooling, the choice of the most suitable cooling solution depends on the specific requirements of the application, including the heat load, space constraints, and performance targets.
As technology advances and the demand for more efficient and compact cooling solutions grows, researchers and engineers continue to develop and refine advanced cooling techniques, such as phase change materials, nanofluids, and oscillating heat pipes. These innovations hold promise for addressing the challenges of thermal management in various industries, from electronics and automotive to aerospace and beyond.
Frequently Asked Questions (FAQ)
- What is the difference between active and passive cooling techniques?
-
Active cooling techniques use powered components, such as fans or pumps, to enhance heat transfer, while passive cooling techniques rely on natural heat transfer mechanisms without the use of active components.
-
What are the advantages of liquid cooling over air cooling?
-
Liquid cooling offers higher thermal conductivity, more efficient heat transfer, the ability to transport heat over longer distances, and quieter operation compared to air cooling.
-
How do heat pipes work?
-
Heat pipes are passive cooling devices that use a working fluid to transfer heat from the evaporator (heat source) to the condenser (heat sink) through a cycle of evaporation and condensation.
-
What are thermal interface materials (TIMs), and why are they important?
-
Thermal interface materials are substances applied between the heat source and the heat sink to enhance thermal conductivity and minimize air gaps. They are important for ensuring efficient heat transfer between components.
-
What are the potential benefits of using nanofluids in cooling systems?
- Nanofluids contain nanoparticles with extremely high thermal conductivity, which can enhance the overall heat transfer properties of the fluid. This can lead to improved cooling performance and efficiency in various applications.
0 Comments