Introduction to High Frequency PCB Layout
Designing printed circuit boards (PCBs) for high frequency applications requires careful consideration of many factors to ensure signal integrity, minimize noise and crosstalk, and achieve optimal performance. As digital systems operate at increasingly higher speeds, reaching into the gigahertz range, the PCB layout becomes critical to success. Poor layout practices can lead to significant issues like reflections, ringing, electromagnetic interference (EMI), and even complete circuit failure.
In this comprehensive guide, we will delve into the best practices and techniques for creating robust high frequency PCB layouts. From understanding the fundamentals of high-speed signaling to implementing advanced layout strategies, this article will provide valuable insights for PCB designers at all levels.
Understanding High-Speed Signaling
The Basics of High Frequency Signals
High frequency signals behave differently than low frequency ones due to the effects of parasitic reactances, transmission line behavior, and other factors that become significant at high speeds. As frequencies increase, PCB traces start to act like transmission lines rather than simple connections. This means that impedance matching, propagation delay, and termination techniques become crucial for maintaining signal integrity.
Some key characteristics of high frequency signals include:
– Shorter wavelengths
– Increased sensitivity to PCB material properties
– Higher susceptibility to noise and interference
– Greater impact of parasitic capacitance and inductance
To effectively design for high frequencies, PCB designers must have a solid understanding of these signal properties and how they interact with the PCB layout.
Signal Integrity Challenges
Signal integrity refers to the ability of a signal to maintain its original shape and timing as it propagates through a system. At high frequencies, several factors can degrade signal integrity:
-
Reflections: When a signal encounters an impedance mismatch, such as an unterminated trace or a poorly matched connector, a portion of the signal energy is reflected back toward the source. These reflections can cause ringing, overshoot, and undershoot, distorting the signal waveform.
-
Crosstalk: Crosstalk occurs when a signal on one trace induces unwanted energy onto adjacent traces through capacitive or inductive coupling. As frequencies increase, the coupling between traces becomes more pronounced, leading to greater crosstalk.
-
Attenuation: High frequency signals experience higher attenuation due to dielectric losses, skin effect, and other frequency-dependent phenomena. This can result in reduced signal amplitude and degraded rise/fall times.
-
EMI: High-speed signals can generate significant electromagnetic radiation, which can interfere with nearby circuits or violate regulatory emissions limits. Proper layout techniques are essential for minimizing EMI.
By understanding and addressing these signal integrity challenges, designers can create PCB layouts that maintain clean, reliable high-speed signaling.
PCB Material Considerations
Dielectric Properties
The choice of PCB substrate material is critical for high frequency designs. The dielectric constant (Dk) and dissipation factor (Df) of the material directly impact the signal propagation velocity, impedance, and losses.
Material | Dielectric Constant (Dk) | Dissipation Factor (Df) |
---|---|---|
FR-4 | 4.2 – 4.5 | 0.02 |
Rogers 4350B | 3.48 | 0.0037 |
Isola I-Tera MT | 3.45 | 0.0031 |
For high frequency applications, materials with lower Dk and Df values are preferred. Lower Dk allows for thinner dielectric layers and wider traces, which can help minimize losses and improve impedance control. Low Df reduces the amount of signal energy lost as heat, resulting in lower attenuation.
Copper Surface Finish
The choice of copper surface finish can also impact high-speed performance. Some common surface finishes include:
- Hot Air Solder Leveling (HASL)
- Electroless Nickel Immersion Gold (ENIG)
- Immersion Silver (IAg)
- Immersion Tin (ISn)
- Organic Solderability Preservative (OSP)
ENIG and IAg are often preferred for high frequency designs due to their flat, smooth surface, which promotes better impedance control and reduces signal reflections. HASL, while cost-effective, can introduce surface irregularities that affect impedance and increase losses.
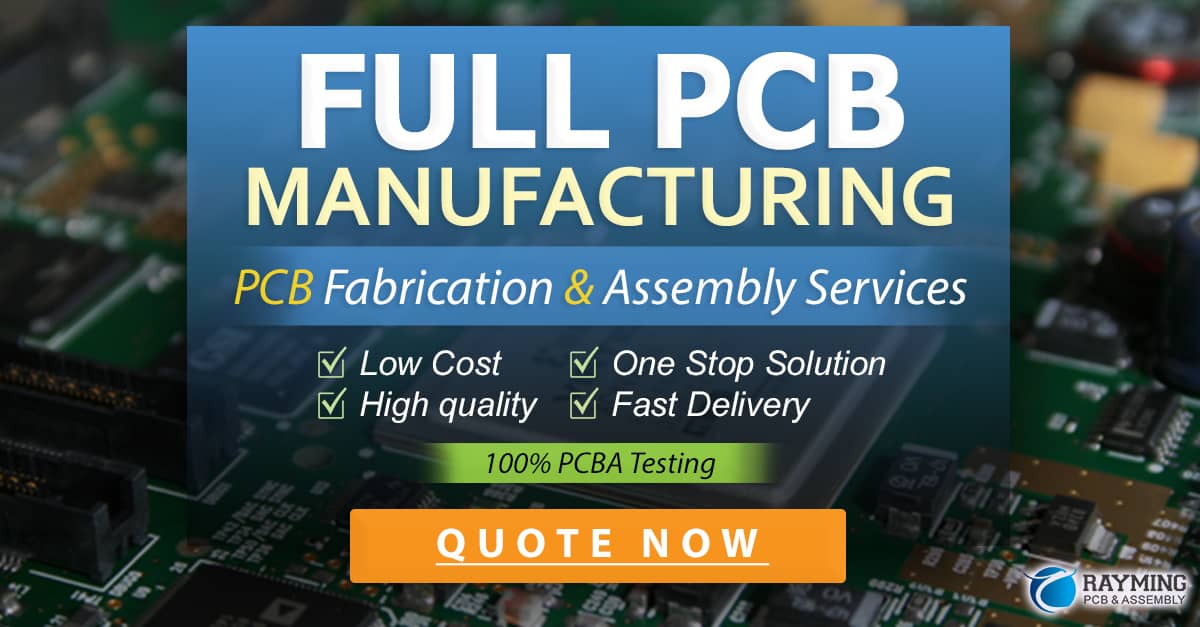
High Frequency PCB Layout Techniques
Controlled Impedance Routing
Maintaining consistent impedance throughout a high-speed signal path is essential for preventing reflections and ensuring good signal integrity. Controlled impedance routing involves carefully designing trace widths, spacing, and dielectric layer thicknesses to achieve a target characteristic impedance (typically 50Ω or 100Ω).
The characteristic impedance of a microstrip trace (on the outer layer) can be approximated by the following equation:
Z₀ = 87 / √(ℇᵣ + 1.41) × ln(5.98 × h / (0.8 × w + t))
Where:
– Z₀ is the characteristic impedance in ohms
– ℇᵣ is the dielectric constant of the substrate material
– h is the thickness of the dielectric layer in mils
– w is the width of the trace in mils
– t is the thickness of the trace in mils
For stripline traces (on inner layers), the characteristic impedance equation is slightly different:
Z₀ = 60 / √ℇᵣ × ln(4 × h / (0.67 × π × (0.8 × w + t)))
By using these equations and PCB design software tools, designers can calculate the appropriate trace geometries to achieve the desired impedance. It’s important to work closely with the PCB fabricator to ensure that the design can be manufactured within their process tolerances.
Trace Routing and Spacing
Proper trace routing and spacing are critical for minimizing crosstalk and signal integrity issues in high frequency designs. Some best practices include:
- Route critical high-speed traces on inner layers between power and ground planes to provide shielding and minimize crosstalk.
- Avoid routing high-speed traces parallel to each other for long distances. If parallel routing is unavoidable, maintain adequate spacing between traces based on the edge-coupled crosstalk length limit.
- Use serpentine routing or add meanders to match trace lengths and minimize skew between differential pairs or bus signals.
- Avoid sharp corners or abrupt changes in trace direction, as these can cause reflections. Use gradual curves or chamfered corners instead.
- Maintain symmetry and consistency in differential pair routing to ensure good common-mode rejection and minimize differential skew.
By following these guidelines, designers can create PCB layouts that minimize crosstalk and maintain good signal integrity.
Power Distribution Network (PDN) Design
A robust power distribution network is essential for providing clean, stable power to high-speed devices. The PDN design should minimize impedance, reduce voltage ripple, and suppress EMI. Some key considerations for PDN design include:
- Use dedicated power and ground planes to provide low-impedance power delivery and minimize voltage drops.
- Employ proper decoupling capacitor placement and selection to reduce high-frequency impedance and suppress noise.
- Optimize via placement and sizing to minimize inductance and ensure good current flow between layers.
- Implement split power planes or isolated power islands for noise-sensitive circuits, such as analog or RF sections.
- Use power plane cutouts sparingly and strategically to minimize disruption to the PDN.
By designing a robust PDN, designers can ensure that high-speed devices receive clean, stable power, minimizing noise and improving overall system performance.
Grounding and Shielding
Proper grounding and shielding techniques are crucial for controlling EMI and maintaining signal integrity in high frequency designs. Some best practices include:
- Implement a solid, low-impedance ground plane to provide a stable reference for high-speed signals and minimize ground bounce.
- Use ground vias liberally to stitch together ground planes on different layers, creating a continuous, low-impedance ground structure.
- Employ ground pour on signal layers to provide additional shielding and reduce crosstalk between traces.
- Use guard traces or co-planar waveguides to shield sensitive high-speed traces from adjacent signals.
- Implement shielding cans or Faraday cages around noise-sensitive components or circuits to minimize EMI coupling.
By incorporating effective grounding and shielding strategies, designers can reduce EMI, improve signal integrity, and ensure reliable high-speed performance.
Advanced High Frequency PCB Layout Techniques
High-Density Interconnect (HDI) Designs
HDI PCBs use microvias and fine-pitch traces to achieve higher component density and improved signal integrity. Some benefits of HDI for high frequency designs include:
- Shorter signal paths, which reduce propagation delay and minimize losses
- Improved impedance control due to smaller via sizes and thinner dielectric layers
- Enhanced routing flexibility, allowing for more efficient use of PCB real estate
- Better power integrity through the use of buried and blind vias for power delivery
When designing HDI PCBs for high frequencies, it’s essential to work closely with the fabricator to ensure that the design is manufacturable and reliable.
3D Electromagnetic Simulation
As frequencies increase and designs become more complex, traditional 2D layout tools may not provide sufficient accuracy for predicting high-speed performance. 3D electromagnetic (EM) simulation tools, such as Ansys HFSS or Keysight ADS, can help designers analyze and optimize their layouts for better signal integrity and EMI performance.
3D EM simulation allows designers to:
– Accurately model complex structures, such as vias, connectors, and packaging
– Analyze impedance discontinuities, reflections, and crosstalk
– Predict far-field radiation patterns and EMI performance
– Optimize trace geometries, spacing, and terminations for better signal integrity
By leveraging 3D EM simulation, designers can identify and address high-speed layout issues early in the design process, reducing the risk of costly redesigns and improving overall system performance.
FAQ
- What is the most important factor to consider when designing a high frequency PCB layout?
-
Signal integrity is the most critical factor in high frequency PCB design. Maintaining clean, undistorted signals is essential for ensuring reliable high-speed performance.
-
How can I minimize crosstalk in my high frequency PCB layout?
-
To minimize crosstalk, route high-speed traces on inner layers between power and ground planes, avoid long parallel runs, maintain adequate spacing between traces, and use guard traces or shielding where necessary.
-
What are the benefits of using low-loss PCB materials for high frequency designs?
-
Low-loss materials, such as Rogers 4350B or Isola I-Tera MT, have lower dielectric constants and dissipation factors, which help reduce signal attenuation, improve impedance control, and minimize power loss at high frequencies.
-
How important is the power distribution network (PDN) in high frequency PCB layouts?
-
A robust PDN is critical for providing clean, stable power to high-speed devices. Proper PDN design minimizes impedance, reduces voltage ripple, and suppresses EMI, ensuring reliable high-speed performance.
-
When should I consider using 3D electromagnetic simulation for my high frequency PCB layout?
- 3D EM simulation is valuable when designing complex, high-speed layouts that push the limits of traditional 2D tools. It provides accurate modeling of complex structures, predicts EMI performance, and helps optimize signal integrity, making it an essential tool for advanced high frequency designs.
Conclusion
Designing high frequency PCB layouts requires a deep understanding of signal integrity, material properties, and advanced layout techniques. By following best practices for controlled impedance routing, trace spacing, power distribution, grounding, and shielding, designers can create robust, reliable high-speed designs.
As frequencies continue to increase and designs become more complex, staying current with the latest tools, technologies, and strategies is essential for success in the high-speed PCB design landscape. By leveraging techniques like HDI and 3D EM simulation, designers can push the boundaries of high frequency performance and create cutting-edge PCB layouts that meet the demands of today’s advanced electronic systems.
0 Comments