Introduction to High Frequency PCB (HF-PCB)
High Frequency Printed Circuit Boards (HF-PCBs) are specialized circuit boards designed to operate at high frequencies, typically above 100 MHz. These PCBs are crucial components in various electronic devices and systems, such as telecommunications equipment, radar systems, and high-speed digital circuits. The unique properties of HF-PCBs enable them to handle high-speed signals while minimizing signal loss, distortion, and interference.
Key Characteristics of HF-PCBs
- Low Dielectric Constant (Dk) Materials
- Controlled Impedance
- Tight Tolerances
- High-Quality Copper
- Advanced Manufacturing Techniques
Materials Used in HF-PCB Manufacturing
Low Dielectric Constant (Dk) Materials
HF-PCBs require substrate materials with low dielectric constants to minimize signal loss and distortion at high frequencies. Some common low Dk materials include:
Material | Dielectric Constant (Dk) |
---|---|
Rogers RO4003C | 3.38 |
Rogers RO4350B | 3.48 |
Isola I-Tera MT40 | 3.45 |
Taconic RF-35 | 3.50 |
These materials help maintain signal integrity and reduce the effects of parasitic capacitance and inductance.
Copper Foils
HF-PCBs use high-quality copper foils to minimize skin effect losses and ensure optimal signal transmission. The most common copper foil thicknesses used in HF-PCBs are:
- 0.5 oz (17 µm)
- 1 oz (35 µm)
- 2 oz (70 µm)
Thinner copper foils are preferred for higher frequencies to minimize skin effect losses.
HF-PCB Design Considerations
Controlled Impedance
Maintaining controlled impedance is crucial in HF-PCB design to ensure proper signal transmission and minimize reflections. The characteristic impedance of a transmission line is determined by factors such as:
- Substrate material properties (Dk and dissipation factor)
- Trace width and thickness
- Dielectric thickness
- Ground plane spacing
Common characteristic impedance values for HF-PCBs include:
- 50 Ω for RF circuits
- 75 Ω for video applications
- 90 Ω for high-speed digital circuits
Signal Integrity
To maintain signal integrity in HF-PCBs, designers must consider several factors:
- Trace routing: Minimize trace lengths, avoid sharp bends, and use smooth curves to reduce reflections and signal distortion.
- Via placement: Strategically place vias to minimize inductance and capacitance effects.
- Ground planes: Use solid ground planes to provide a low-impedance return path for high-frequency signals.
- Decoupling capacitors: Place decoupling capacitors close to active components to reduce power supply noise and maintain signal integrity.
Electromagnetic Compatibility (EMC)
HF-PCBs must be designed with EMC in mind to minimize electromagnetic interference (EMI) and ensure compliance with relevant standards. Some EMC design techniques include:
- Shielding: Use shielding enclosures, gaskets, and conductive coatings to reduce EMI.
- Grounding: Implement proper grounding techniques, such as ground planes and grounding vias, to minimize EMI.
- Filtering: Use EMI filters, such as ferrite beads and capacitors, to suppress high-frequency noise.
- Layer stacking: Arrange layers in the PCB stack-up to minimize crosstalk and EMI.
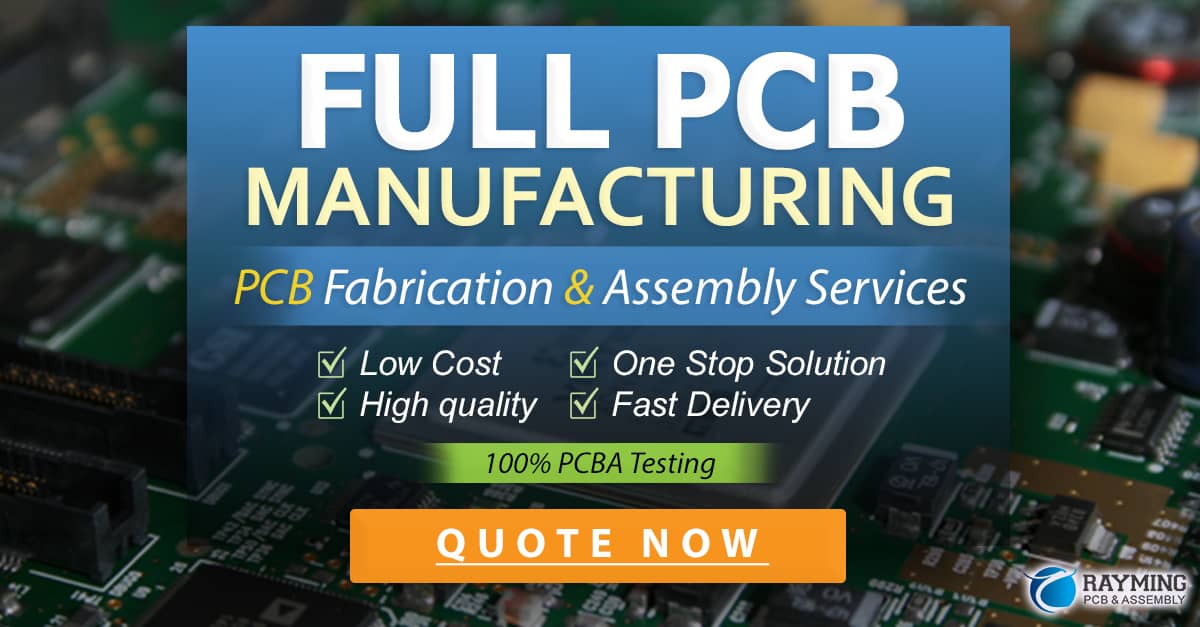
HF-PCB Manufacturing Process
PCB Stack-up
The PCB stack-up refers to the arrangement of layers in the HF-PCB. A typical 4-layer HF-PCB stack-up may include:
- Top layer: Signal traces and components
- Ground plane
- Power plane
- Bottom layer: Signal traces and components
The stack-up is designed to provide controlled impedance, minimize crosstalk, and ensure proper signal integrity.
Lamination
During the lamination process, the substrate materials, copper foils, and prepregs are bonded together under heat and pressure. The lamination process is critical for HF-PCBs, as it ensures a consistent dielectric thickness and minimizes air gaps or voids that can affect signal integrity.
Drilling and Plating
After lamination, the HF-PCB undergoes drilling and plating processes. High-speed drilling machines create holes for vias and through-hole components. The holes are then plated with copper to establish electrical connections between layers.
Etching and Solder Mask Application
The copper foils are etched to create the desired trace patterns using photolithography and chemical etching. A solder mask is then applied to the PCB surface to protect the traces and prevent short circuits during soldering.
Surface Finishing
Various surface finishes can be applied to HF-PCBs to improve solderability, protect the copper traces, and enhance electrical performance. Common surface finishes include:
- Immersion silver (IAg)
- Electroless nickel immersion gold (ENIG)
- Organic solderability preservative (OSP)
Testing and Quality Control
Automated Optical Inspection (AOI)
AOI systems use high-resolution cameras and advanced image processing algorithms to inspect HF-PCBs for manufacturing defects, such as:
- Shorts and opens
- Incorrect component placement
- Solder bridging
- Trace width violations
AOI helps identify defects early in the manufacturing process, reducing rework and improving overall quality.
Electrical Testing
Electrical testing is performed to verify the functionality and performance of HF-PCBs. Common electrical tests include:
- Continuity test: Verifies that all connections are intact and there are no open circuits.
- Isolation test: Checks for short circuits between traces and layers.
- Impedance test: Measures the characteristic impedance of transmission lines to ensure they meet the specified values.
- High-frequency tests: Evaluates the HF-PCB’s performance at its intended operating frequencies, such as S-parameter measurements and eye diagram analysis.
Microsectioning
Microsectioning is a destructive testing method used to evaluate the internal structure and quality of HF-PCBs. A small section of the PCB is cut, polished, and examined under a microscope to assess:
- Lamination quality
- Copper plating thickness and uniformity
- Via and hole quality
- Dielectric thickness and consistency
Microsectioning helps identify internal defects and ensures that the HF-PCB meets the specified manufacturing standards.
Applications of HF-PCBs
HF-PCBs find extensive use in various industries and applications, such as:
- Telecommunications: 5G networks, cellular base stations, and satellite communication systems.
- Aerospace and defense: Radar systems, avionics, and military communication equipment.
- Automotive: Advanced driver assistance systems (ADAS), vehicle-to-vehicle (V2V) communication, and autonomous vehicles.
- Medical devices: High-frequency imaging systems, such as MRI and ultrasound machines.
- Industrial automation: High-speed data acquisition and processing systems, industrial IoT devices.
As technology continues to advance and the demand for high-speed, high-frequency electronics grows, the importance of HF-PCBs will only increase.
Future Trends in HF-PCB Technology
Advanced Materials
Researchers are continuously developing new substrate materials with lower dielectric constants and improved thermal and mechanical properties. Some promising materials include:
- Ultra-low loss ceramics
- Liquid crystal polymers (LCPs)
- Polytetrafluoroethylene (PTFE) based composites
These materials will enable the design of HF-PCBs with even higher operating frequencies and better signal integrity.
3D Printing
Additive manufacturing techniques, such as 3D printing, are being explored for the fabrication of HF-PCBs. 3D printing allows for the creation of complex geometries, embedded components, and unique dielectric structures that can enhance the performance of HF-PCBs.
Artificial Intelligence (AI) in Design and Manufacturing
AI and machine learning algorithms are being employed to optimize HF-PCB design and manufacturing processes. These technologies can help:
- Automate design rule checks and layout optimization
- Predict and prevent manufacturing defects
- Optimize material selection and stack-up design
- Improve testing and quality control processes
The integration of AI in HF-PCB design and manufacturing will lead to more efficient, reliable, and high-performance products.
Frequently Asked Questions (FAQ)
-
What is the difference between HF-PCBs and regular PCBs?
HF-PCBs are designed to operate at high frequencies (above 100 MHz) and require specialized materials, design techniques, and manufacturing processes to maintain signal integrity and minimize losses. Regular PCBs are suitable for lower frequency applications and do not require the same level of specialization. -
What are the main challenges in designing HF-PCBs?
The main challenges in designing HF-PCBs include maintaining controlled impedance, minimizing signal loss and distortion, ensuring electromagnetic compatibility, and managing the effects of parasitic capacitance and inductance. -
What is the role of low dielectric constant materials in HF-PCBs?
Low dielectric constant materials help minimize signal loss and distortion at high frequencies by reducing the amount of energy absorbed by the substrate. This enables better signal propagation and maintains signal integrity in HF-PCBs. -
How does the skin effect impact HF-PCB design?
The skin effect causes high-frequency currents to flow primarily on the surface of conductors, increasing the effective resistance and leading to signal loss. To mitigate the skin effect, HF-PCBs use thinner copper foils and may employ techniques such as trace smoothing and edge plating. -
What are some common surface finishes used in HF-PCBs?
Common surface finishes for HF-PCBs include immersion silver (IAg), electroless nickel immersion gold (ENIG), and organic solderability preservative (OSP). These finishes improve solderability, protect the copper traces, and enhance electrical performance.
Conclusion
High Frequency PCBs are essential components in the rapidly advancing world of high-speed electronics. By leveraging specialized materials, advanced design techniques, and precise manufacturing processes, HF-PCBs enable the reliable transmission of high-frequency signals in a wide range of applications, from telecommunications and automotive to aerospace and medical devices.
As technology continues to push the boundaries of speed and performance, the demand for HF-PCBs will only grow. Ongoing research into advanced materials, 3D printing, and AI-driven design and manufacturing processes promises to unlock new possibilities in HF-PCB technology, enabling even higher operating frequencies, improved signal integrity, and more compact and efficient electronic devices.
By staying at the forefront of HF-PCB technology and continuously innovating, manufacturers and designers can meet the ever-increasing demands of the high-frequency electronics industry and drive the development of cutting-edge products that shape our connected world.
0 Comments