Introduction to PCB Grounding
Printed Circuit Boards (PCBs) are the backbone of modern electronic devices. They provide a platform for mounting and connecting electronic components, allowing for the efficient and reliable operation of the device. One crucial aspect of PCB-Design/”>PCB Design is grounding, which involves creating a low-impedance path for current to flow back to the source. Proper grounding is essential for ensuring the stability, performance, and safety of the electronic device.
In this article, we will explore the concept of PCB grounding in-depth, discussing its importance, various grounding techniques, and best practices for designing and implementing effective grounding schemes.
The Importance of PCB Grounding
Noise Reduction
One of the primary reasons for implementing proper grounding in PCBs is to reduce noise and interference. Electronic devices are susceptible to both internal and external sources of noise, such as power supply ripple, digital switching noise, and electromagnetic interference (EMI). By providing a low-impedance path for noise currents to flow back to the source, effective grounding helps to minimize the impact of noise on sensitive components and signals.
Signal Integrity
Grounding plays a vital role in maintaining signal integrity in PCBs. When signals travel through the traces on a PCB, they can be affected by factors such as crosstalk, reflections, and ground bounce. These issues can lead to signal distortion, timing errors, and other problems that can compromise the performance and reliability of the device. By implementing a well-designed grounding scheme, you can help to mitigate these issues and ensure that signals remain clean and stable throughout the PCB.
Safety
Proper grounding is also essential for ensuring the safety of both the electronic device and its users. In the event of a fault condition, such as a short circuit or overvoltage, a well-designed grounding system can provide a safe path for fault currents to flow, preventing damage to the device and potential harm to users. Additionally, effective grounding can help to protect sensitive components from electrostatic discharge (ESD) events, which can cause permanent damage to the device.
Grounding Techniques
There are several techniques that can be used to implement effective grounding in PCBs. The choice of grounding technique will depend on factors such as the complexity of the design, the frequency of operation, and the specific requirements of the application. Some common grounding techniques include:
Star Grounding
Star grounding is a technique where all ground connections are made to a single point, known as the star point. This approach helps to minimize ground loops and reduce the impact of ground noise on sensitive components. In a star grounding scheme, each component or subsystem has its own dedicated ground connection to the star point, which is typically located near the power supply or the center of the PCB.
Ground Planes
Ground planes are large areas of copper on the PCB that are used to provide a low-impedance path for ground currents. They are typically placed on one or more layers of the PCB and connected to the ground points of components and connectors. Ground planes help to reduce ground impedance, minimize ground noise, and improve signal integrity by providing a stable reference for signals.
Partitioning and Zoning
Partitioning and zoning are techniques used to separate different sections of the PCB based on their function or noise sensitivity. By dividing the PCB into distinct zones, each with its own local ground plane, you can help to isolate noisy circuits from sensitive ones and prevent noise from propagating throughout the board. This approach is particularly useful in mixed-signal designs, where analog and digital circuits coexist on the same PCB.
High-Frequency Grounding
At high frequencies, the behavior of ground currents and the effectiveness of grounding techniques can change significantly. High-frequency grounding techniques, such as the use of ground vias, stitching capacitors, and EMI filters, are designed to address the unique challenges associated with high-speed designs. These techniques help to minimize the impact of high-frequency noise, reduce EMI, and ensure signal integrity in high-speed applications.
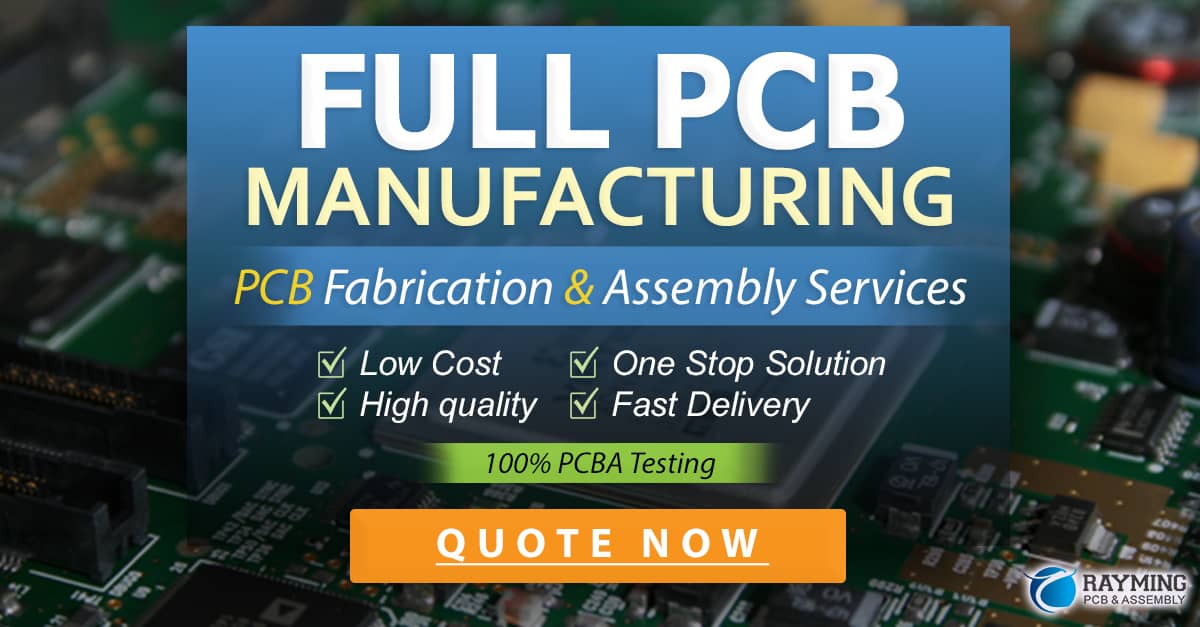
Best Practices for PCB Grounding
To ensure effective grounding in your PCB design, consider the following best practices:
-
Identify and Classify Ground Types: Determine the different types of grounds in your design (e.g., analog ground, digital ground, chassis ground) and establish a clear hierarchy and separation between them.
-
Use Appropriate Grounding Techniques: Select the most suitable grounding techniques for your design based on factors such as the frequency of operation, noise sensitivity, and the complexity of the circuit.
-
Minimize Ground Impedance: Use techniques such as ground planes, wide traces, and multiple vias to minimize ground impedance and ensure a low-resistance path for ground currents.
-
Avoid Ground Loops: Identify and eliminate ground loops, which can cause noise and interference issues in the circuit. Use star grounding or partitioning techniques to prevent ground loops from forming.
-
Separate Sensitive Circuits: Isolate sensitive analog and digital circuits from noisy ones using techniques such as partitioning, zoning, and the use of local ground planes.
-
Use Ground Stitching Capacitors: Place decoupling and stitching capacitors close to noise sources and sensitive components to provide a low-impedance path for high-frequency noise currents.
-
Route Signals Carefully: Follow best practices for signal routing, such as avoiding long, parallel traces, minimizing crosstalk, and using appropriate termination techniques to maintain signal integrity.
-
Test and Verify: Perform thorough testing and verification of the grounding scheme to ensure that it meets the desired performance and safety requirements. Use tools such as ground loop testers, oscilloscopes, and spectrum analyzers to identify and resolve any grounding issues.
Grounding in Multi-Layer PCBs
Multi-layer PCBs present additional challenges and opportunities for implementing effective grounding. By using dedicated ground planes and strategically placing ground vias, you can create a robust and low-impedance grounding structure that minimizes noise and ensures signal integrity.
When designing multi-layer PCBs, consider the following guidelines:
-
Dedicate Ground Layers: Assign one or more layers of the PCB as dedicated ground planes. This helps to minimize ground impedance and provides a low-resistance path for ground currents.
-
Use Ground Vias: Place ground vias strategically throughout the PCB to connect the ground planes and provide a low-impedance path for ground currents. Use multiple vias in parallel to further reduce ground impedance.
-
Stitch Ground Planes: If using multiple ground planes, stitch them together using vias to ensure continuity and minimize ground impedance.
-
Consider Split Planes: In some cases, it may be beneficial to use split planes, where different sections of the ground plane are isolated from each other. This can be useful for isolating noisy circuits or preventing ground loops.
-
Minimize Apertures: Avoid large apertures or gaps in the ground planes, as they can disrupt the flow of ground currents and create high-impedance paths.
Layer | Purpose |
---|---|
Top | Signal routing, component placement |
Ground 1 | Dedicated ground plane |
Power | Power distribution |
Ground 2 | Dedicated ground plane |
Bottom | Signal routing, component placement |
Example of a multi-layer PCB Stackup with dedicated ground planes.
Grounding and EMI/EMC Considerations
Effective grounding is essential for managing electromagnetic interference (EMI) and ensuring electromagnetic compatibility (EMC) in electronic devices. EMI refers to the unwanted generation, propagation, and reception of electromagnetic energy, which can cause interference and disrupt the operation of electronic devices. EMC, on the other hand, refers to the ability of an electronic device to function properly in its intended electromagnetic environment without causing or being susceptible to EMI.
To address EMI/EMC concerns in PCB design, consider the following grounding-related techniques:
-
Shielding: Use shielding techniques, such as metal enclosures or shielding gaskets, to contain EMI and prevent it from radiating to or from the PCB.
-
Grounding Shields: Properly ground any shielding elements to provide a low-impedance path for EMI currents to flow back to the source.
-
Cable Grounding: Ensure that cable shields are properly grounded at the point of entry to the PCB to prevent EMI from entering or exiting the system.
-
EMI Filters: Use EMI filters, such as ferrite beads or LC filters, to suppress high-frequency noise and prevent EMI from propagating through the grounding system.
-
Ground Plane Stitching: Use stitching capacitors to connect ground planes at high frequencies, helping to minimize ground impedance and reduce EMI.
By implementing these EMI/EMC considerations in conjunction with effective grounding techniques, you can help to ensure that your electronic device operates reliably and complies with relevant EMC standards and regulations.
Conclusion
Grounding is a critical aspect of PCB design that plays a vital role in ensuring the stability, performance, and safety of electronic devices. By understanding the importance of grounding, selecting appropriate grounding techniques, and following best practices for implementation, you can create a robust and reliable grounding scheme that minimizes noise, maintains signal integrity, and protects your device from potential hazards.
When designing your PCB, consider factors such as the frequency of operation, noise sensitivity, and the specific requirements of your application to determine the most suitable grounding approach. Use techniques such as star grounding, ground planes, partitioning, and high-frequency grounding as needed to create a low-impedance path for ground currents and minimize the impact of noise on sensitive components and signals.
Remember to also address EMI/EMC concerns by implementing shielding, grounding shields, cable grounding, EMI filters, and ground plane stitching as appropriate. By taking a comprehensive approach to grounding and EMI/EMC management, you can help to ensure that your electronic device operates reliably and complies with relevant standards and regulations.
Frequently Asked Questions
- What is the purpose of grounding in PCBs?
-
The purpose of grounding in PCBs is to provide a low-impedance path for current to flow back to the source, minimizing noise, ensuring signal integrity, and protecting the device and its users from potential hazards such as short circuits, overvoltage, and electrostatic discharge.
-
What are some common grounding techniques used in PCB design?
-
Some common grounding techniques used in PCB design include star grounding, ground planes, partitioning and zoning, and high-frequency grounding techniques such as ground vias, stitching capacitors, and EMI filters.
-
Why is it important to minimize ground impedance in PCBs?
-
Minimizing ground impedance is important because it helps to reduce noise, maintain signal integrity, and ensure that ground currents have a low-resistance path to flow back to the source. High ground impedance can lead to issues such as ground bounce, crosstalk, and EMI.
-
How can you address EMI/EMC concerns in PCB grounding?
-
EMI/EMC concerns can be addressed in PCB grounding by using techniques such as shielding, grounding shields, cable grounding, EMI filters, and ground plane stitching. These techniques help to contain, suppress, and prevent the propagation of electromagnetic interference.
-
What are some best practices for implementing effective grounding in PCBs?
- Some best practices for implementing effective grounding in PCBs include identifying and classifying ground types, selecting appropriate grounding techniques, minimizing ground impedance, avoiding ground loops, separating sensitive circuits, using ground stitching capacitors, routing signals carefully, and thoroughly testing and verifying the grounding scheme.
0 Comments