Introduction to Gold Plating
Gold plating is a process of depositing a thin layer of gold onto the surface of another metal, such as copper or nickel. This process is widely used in various industries, including electronics, aerospace, and automotive, due to gold’s unique properties. Gold is an excellent conductor of electricity, resistant to corrosion and oxidation, and provides a reliable and durable surface for electrical contacts.
In the electronics industry, gold plating is particularly important for edge connectors. Edge connectors are used to establish electrical connections between printed circuit boards (PCBs) and other components, such as cables or other PCBs. These connectors are critical for ensuring reliable and efficient data transfer and power delivery in electronic devices.
Benefits of Gold Plating for Edge Connectors
- Excellent electrical conductivity: Gold is one of the best conductors of electricity, ensuring minimal signal loss and resistance in edge connectors.
- Corrosion resistance: Gold is highly resistant to corrosion and oxidation, preventing the formation of insulating oxide layers that can degrade electrical performance over time.
- Durability: Gold-plated edge connectors can withstand numerous insertion and removal cycles without significant wear, ensuring long-term reliability.
- Low contact resistance: Gold-plated contacts provide low and stable contact resistance, which is essential for maintaining signal integrity and minimizing power loss.
- Compatibility: Gold is compatible with a wide range of other materials used in electronics, such as copper, nickel, and various alloys.
Types of Gold Plating for Edge Connectors
There are several methods used for gold plating edge connectors, each with its own advantages and limitations. The choice of the plating method depends on factors such as the base material, desired thickness, and specific application requirements.
Electroplating
Electroplating is the most common method for gold plating edge connectors. In this process, an electric current is used to deposit gold ions onto the surface of the connector from a gold-containing electrolyte solution. The thickness of the gold layer can be precisely controlled by adjusting the current density and plating time.
Advantages of electroplating:
– Uniform and consistent gold layer thickness
– High deposition rates, enabling faster production
– Suitable for high-volume manufacturing
– Relatively low cost compared to other methods
Limitations of electroplating:
– Requires a conductive base material
– May require additional pre-treatment steps, such as cleaning and activation
– Can be affected by surface defects or contamination on the base material
Electroless Plating
Electroless plating is a chemical process that does not require an external electric current to deposit the gold layer. Instead, it relies on an autocatalytic reaction between the gold ions in the solution and a reducing agent. The gold ions are selectively reduced and deposited onto the surface of the edge connector.
Advantages of electroless plating:
– Can be applied to non-conductive base materials
– Provides excellent coverage and uniformity, even on complex geometries
– Minimizes the risk of hydrogen embrittlement in sensitive materials
– Produces a dense and porosity-free gold layer
Limitations of electroless plating:
– Slower deposition rates compared to electroplating
– Higher cost due to the use of more expensive chemicals
– Requires strict control of the plating solution composition and operating conditions
Immersion Plating
Immersion plating is a simple and cost-effective method for depositing a thin layer of gold onto edge connectors. In this process, the connector is immersed in a gold-containing solution, and the gold ions replace the surface atoms of the base material through a displacement reaction. The resulting gold layer is typically thinner than those obtained by electroplating or electroless plating.
Advantages of immersion plating:
– Simple and easy to implement
– Does not require external power or complex equipment
– Suitable for small-scale production or prototyping
– Can be applied to a variety of base materials
Limitations of immersion plating:
– Limited gold layer thickness (usually less than 0.1 µm)
– May not provide adequate coverage on highly porous or rough surfaces
– The displacement reaction can be sensitive to surface contamination or oxides
Gold Plating Process for Edge Connectors
The gold plating process for edge connectors typically involves several steps to ensure a high-quality and reliable gold layer. These steps may vary depending on the specific plating method and the base material used.
- Cleaning: The edge connectors are thoroughly cleaned to remove any surface contaminants, such as oils, oxides, or dirt. This step is critical for ensuring good adhesion of the gold layer and preventing defects.
- Surface preparation: Depending on the base material, additional surface preparation steps may be required. For example, copper connectors may undergo a micro-etching process to roughen the surface and improve gold adhesion.
- Activation: In some cases, the surface of the connector is activated using a special solution to enhance the chemical bonding between the base material and the gold layer.
- Plating: The edge connectors are subjected to the chosen gold plating method (electroplating, electroless plating, or immersion plating) to deposit the desired thickness of the gold layer.
- Rinsing: After plating, the connectors are rinsed with deionized water to remove any residual plating solution and prevent contamination.
- Drying: The gold-plated edge connectors are dried using hot air or an oven to remove any remaining moisture and ensure a clean and stable surface.
- Inspection: The plated connectors are visually inspected for any defects, such as pinholes, blisters, or uneven coverage. Electrical and mechanical tests may also be performed to verify the performance and reliability of the gold-plated contacts.
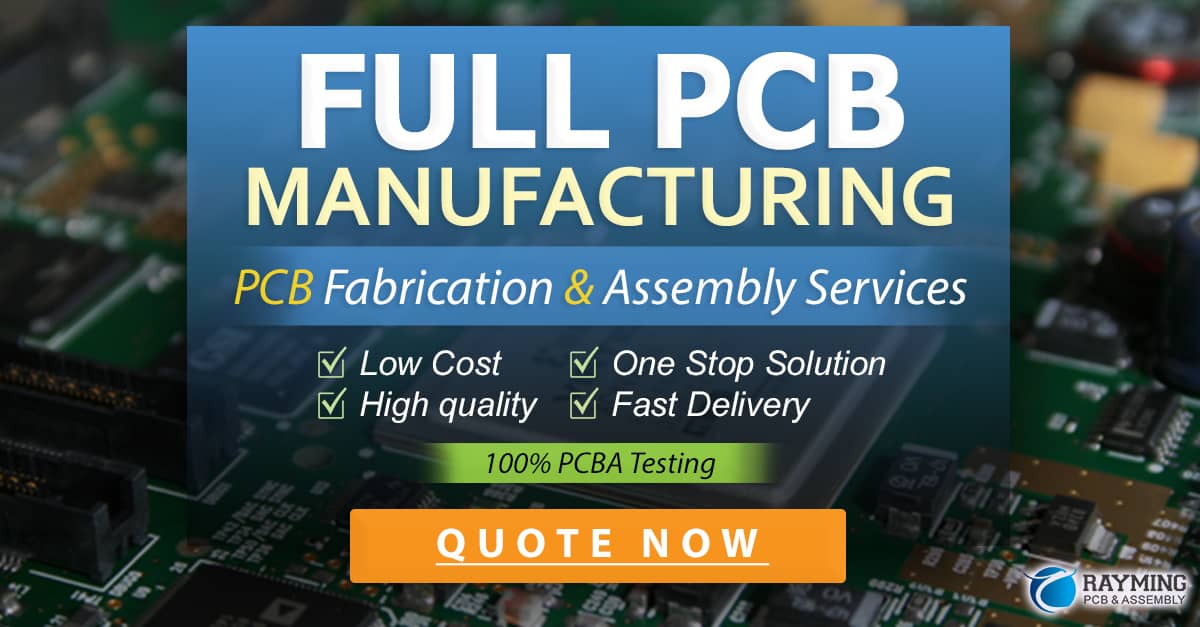
Gold Plating Specifications for Edge Connectors
To ensure the optimal performance and reliability of gold-plated edge connectors, various specifications and standards have been established by industry organizations and regulatory bodies. These specifications define the requirements for gold purity, thickness, and other key parameters.
Gold Purity
The purity of the gold used for plating edge connectors is typically expressed in karats (K) or as a percentage. The most common gold purities used in the electronics industry are:
- 24K (99.9% pure gold): Offers the best electrical conductivity and corrosion resistance but is relatively soft and prone to wear.
- 23K (95.8% pure gold): Provides a good balance between electrical performance and durability.
- 22K (91.7% pure gold): Offers increased hardness and wear resistance compared to higher purity options.
The choice of gold purity depends on the specific application requirements, such as the expected number of insertion/removal cycles and the operating environment.
Gold Thickness
The thickness of the gold layer on edge connectors is critical for ensuring reliable electrical performance and long-term durability. The gold thickness is typically measured in microinches (µin) or micrometers (µm).
Common gold thickness specifications for edge connectors include:
Thickness (µin) | Thickness (µm) | Application |
---|---|---|
15 – 30 | 0.38 – 0.76 | Low-cost, consumer-grade electronics |
30 – 50 | 0.76 – 1.27 | General-purpose, commercial electronics |
50 – 100 | 1.27 – 2.54 | High-reliability, industrial, and automotive applications |
100 – 200 | 2.54 – 5.08 | Extreme environments, aerospace, and military applications |
The optimal gold thickness for a specific application depends on factors such as the base material, contact force, and expected service life.
Industry Standards
Several industry standards provide guidelines and requirements for gold plating of edge connectors. Some of the most relevant standards include:
- IPC-4552: Specification for Electroless Nickel/Immersion Gold (ENIG) Plating for Printed Circuit Boards
- IPC-4556: Specification for Electroless Nickel/Electroless Palladium/Immersion Gold (ENEPIG) Plating for Printed Circuit Boards
- MIL-DTL-45204D: Military specification for gold plating (electrodeposited)
- ASTM B488: Standard specification for electrodeposited coatings of gold for engineering uses
These standards ensure consistency and reliability in the gold plating process and help manufacturers meet the performance requirements of various industries.
Challenges and Considerations in Gold Plating Edge Connectors
While gold plating offers numerous benefits for edge connectors, there are several challenges and considerations that manufacturers must address to ensure optimal performance and reliability.
Pore Corrosion
Pore corrosion, also known as Creep Corrosion, is a common issue in gold-plated edge connectors. It occurs when the underlying base metal (e.g., copper or nickel) migrates through pores or defects in the gold layer and forms corrosion products on the surface. This can lead to increased contact resistance, signal degradation, and even failure of the connector.
To minimize the risk of pore corrosion, manufacturers can:
– Ensure a sufficient gold thickness to provide a barrier against base metal migration
– Optimize the plating process to minimize porosity and defects in the gold layer
– Use a nickel underplate to act as a diffusion barrier between the base metal and the gold layer
Wear and Fretting
Gold-plated edge connectors are subject to wear and fretting due to repeated insertion and removal cycles. Fretting occurs when microscopic relative motion between the mating surfaces leads to the formation of oxide debris, which can increase contact resistance and cause intermittent connections.
To mitigate wear and fretting, manufacturers can:
– Use a harder gold alloy or a higher gold purity to improve wear resistance
– Apply a thicker gold layer to provide a larger wear reserve
– Optimize the contact design to minimize relative motion and debris accumulation
– Incorporate lubricants or anti-fretting coatings to reduce friction and wear
Intermetallic Compound Formation
Intermetallic compounds (IMCs) can form at the interface between the gold layer and the base metal, particularly at elevated temperatures. These IMCs, such as gold-tin or gold-nickel, are brittle and can lead to reduced mechanical strength and electrical conductivity of the connector.
To address IMC formation, manufacturers can:
– Use a nickel underplate to slow down the diffusion of gold into the base metal
– Limit the exposure of gold-plated connectors to high temperatures during assembly or operation
– Select compatible base materials and gold alloys to minimize IMC formation
Environmental Concerns
Gold plating processes can have environmental impacts due to the use of hazardous chemicals and the generation of wastewater containing metal ions. Manufacturers must comply with local and international regulations regarding the handling, storage, and disposal of plating chemicals and waste.
To minimize environmental impacts, manufacturers can:
– Implement closed-loop plating systems to recycle and reuse plating solutions
– Invest in wastewater treatment technologies to remove metal ions and other contaminants
– Explore alternative, more environmentally friendly plating processes, such as ionic liquid-based plating or self-assembled monolayer (SAM) coatings
Future Trends in Gold Plating for Edge Connectors
As the electronics industry continues to evolve, new trends and technologies are emerging in the field of gold plating for edge connectors. These developments aim to address the challenges of miniaturization, high-speed data transmission, and environmental sustainability.
Selective Plating
Selective plating is a process that allows for the precise deposition of gold only on the critical contact areas of the edge connector, rather than plating the entire surface. This approach reduces gold consumption, lowers costs, and minimizes the environmental impact of the plating process.
Selective plating techniques include:
– Laser-assisted plating: A laser beam is used to selectively activate the surface of the connector, promoting gold deposition only in the desired areas.
– Masking: A protective mask is applied to the connector, exposing only the contact areas to the plating solution.
– Inkjet printing: A gold-containing ink is precisely deposited onto the contact areas using an inkjet printer, followed by a sintering process to form a conductive gold layer.
Nanostructured Gold Coatings
Nanostructured gold coatings, such as nanoporous gold or gold nanoparticle-based coatings, offer unique properties that can enhance the performance and durability of edge connectors. These coatings can provide:
– Increased surface area for improved electrical contact
– Enhanced mechanical properties, such as hardness and wear resistance
– Reduced friction and improved anti-fretting behavior
– Potential for self-healing properties, where the nanostructures can migrate and fill in surface defects over time
Alternative Plating Materials
While gold remains the primary choice for plating edge connectors, researchers are exploring alternative materials that can offer similar or better performance at a lower cost and with reduced environmental impact. Some promising candidates include:
– Palladium: A noble metal with excellent electrical conductivity and corrosion resistance, palladium can be used as a standalone plating layer or in combination with gold.
– Ruthenium: Another noble metal with good electrical properties, ruthenium can form conductive oxide layers that provide additional protection against corrosion and wear.
– Conductive polymers: Polymer-based coatings, such as polyaniline or polypyrrole, can be doped with metal nanoparticles to create a conductive and protective layer on edge connectors.
As these alternative materials and technologies mature, they may offer new opportunities for enhancing the performance, reliability, and sustainability of gold-plated edge connectors in the future.
Frequently Asked Questions (FAQ)
-
Q: What is the difference between hard and soft gold plating for edge connectors?
A: Hard gold plating typically involves the use of gold alloys containing small amounts of other metals, such as cobalt or nickel, to increase the hardness and wear resistance of the gold layer. Soft gold plating, on the other hand, uses high-purity gold (≥99.9%) and offers excellent electrical conductivity but lower durability. The choice between hard and soft gold depends on the specific application requirements, such as the expected number of insertion/removal cycles and the contact force. -
Q: Can gold-plated edge connectors be soldered?
A: Yes, gold-plated edge connectors can be soldered, but care must be taken to avoid excessive heat exposure and gold dissolution into the solder. The gold layer should be kept thin (typically less than 30 µin or 0.76 µm) to minimize the formation of brittle gold-tin intermetallic compounds during soldering. It is also important to use compatible solder alloys and flux to ensure good wetting and a reliable solder joint. -
Q: How can I test the quality of gold plating on edge connectors?
A: Several methods can be used to test the quality of gold plating on edge connectors, including: - Visual inspection: Check for any visible defects, such as pinholes, blisters, or uneven coverage.
- Thickness measurement: Use X-ray fluorescence (XRF) or cross-sectional microscopy to measure the thickness of the gold layer and ensure it meets the specified requirements.
- Adhesion testing: Perform tape tests or scratch tests to assess the adhesion of the gold layer to the base material.
- Contact resistance measurement: Use a four-wire resistance measurement technique to evaluate the electrical performance of the gold-plated contacts.
-
Accelerated aging tests: Expose the gold-plated connectors to elevated temperatures, humidity, or corrosive environments to assess their long-term reliability.
-
Q: What is the shelf life of gold-plated edge connectors?
A: The shelf life of gold-plated edge connectors depends on various factors, such as the storage conditions, packaging materials, and the presence of any contaminants or corrosive agents. In general, properly stored gold-plated connectors can maintain their performance and reliability for several years. To extend the shelf life, it is recommended to store the connectors in a clean, dry, and temperature-controlled environment, preferably in sealed packaging with desiccants or anti-tarnish agents. -
Q: How can I prevent oxidation on the exposed base metal of gold-plated edge connectors?
A: To prevent oxidation on the exposed base metal of gold-plated edge connectors, several approaches can be used: - Apply a Conformal Coating: Use a protective polymer coating, such as parylene or silicone, to seal the exposed base metal and prevent oxidation.
- Use a nickel underplate: A nickel layer between the base metal and the gold plating can act as a barrier to prevent oxidation and improve the overall corrosion resistance of the connector.
- Ensure complete gold coverage: Optimize the plating process to achieve a uniform and defect-free gold layer that completely covers the base metal, minimizing the risk of exposure to oxidizing environments.
- Store connectors in a controlled environment: Keep gold-plated connectors in a clean, dry, and low-humidity environment to reduce the rate of oxidation on any exposed base metal surfaces.
0 Comments