Introduction to PCB Testing
Printed Circuit Boards (PCBs) are the backbone of modern electronics. They provide the foundation for interconnecting electronic components and enabling the functionality of devices we use every day, from smartphones and computers to medical equipment and aerospace systems. To ensure the reliability and performance of these devices, thorough testing of PCBs is crucial. Among the various types of tests conducted, functional testing plays a vital role in validating the proper operation of PCBs before they are integrated into final products.
What is Functional Testing?
Functional testing, also known as functional verification, is a critical step in the PCB manufacturing process that evaluates the board’s ability to perform its intended functions. It involves subjecting the PCB to a series of tests that simulate real-world operating conditions to ensure that it meets the specified requirements and operates as expected. Functional testing goes beyond basic continuity and isolation tests, focusing on the PCB’s overall functionality and its interaction with other components in the system.
Importance of Functional Testing
Functional testing is essential for several reasons:
-
Quality Assurance: It helps identify defects, design flaws, and manufacturing issues early in the production cycle, enabling timely corrections and preventing costly rework or product recalls.
-
Reliability: Thorough functional testing ensures that the PCB can withstand the intended operating conditions and perform reliably over its expected lifetime.
-
Compliance: Functional testing helps verify that the PCB meets industry standards, regulatory requirements, and customer specifications.
-
Cost Reduction: By detecting and addressing issues early, functional testing minimizes the risk of product failures and associated costs, such as warranty claims and reputation damage.
Types of Functional Tests
Functional testing encompasses a wide range of tests that evaluate different aspects of a PCB’s performance. Some of the common types of functional tests include:
In-Circuit Testing (ICT)
In-Circuit Testing is a powerful technique that verifies the functionality of individual components on the PCB. It involves using specialized test probes to access test points on the board and measure the electrical characteristics of each component. ICT can detect issues such as:
- Incorrect component values
- Shorts and opens
- Reversed or missing components
- Defective semiconductor devices
ICT offers high fault coverage and can quickly identify manufacturing defects. However, it requires dedicated test fixtures and can be time-consuming to set up.
Boundary Scan Testing (BST)
Boundary Scan Testing, also known as JTAG (Joint Test Action Group) testing, is a method that uses built-in test circuitry to test the interconnections between integrated circuits (ICs) on a PCB. It involves shifting test patterns into the boundary scan cells of the ICs and capturing the output responses. BST is particularly useful for testing high-density boards with limited physical access to test points. Benefits of BST include:
- Testing of complex ICs and their interconnections
- Detection of opens, shorts, and stuck-at faults
- Programmability and flexibility
- Reduced need for physical test access
However, BST requires the ICs to support the boundary scan architecture, and it may not cover all aspects of the PCB’s functionality.
Functional Circuit Testing (FCT)
Functional Circuit Testing focuses on verifying the overall functionality of the PCB by exercising it under real-world operating conditions. It involves applying input signals and monitoring output responses to ensure that the PCB performs as intended. FCT can be performed at various levels, such as:
- Component-level testing
- Subsystem-level testing
- System-level testing
FCT helps validate the PCB’s functionality, performance, and compatibility with other components in the system. It can detect issues related to:
- Signal integrity
- Timing and synchronization
- Power management
- Communication protocols
FCT requires well-defined test scenarios and can be automated using specialized test equipment and software.
Flying Probe Testing
Flying Probe Testing is a non-contact testing method that uses movable test probes to access test points on the PCB. The probes are guided by a computer-controlled system and can quickly move from one test point to another. Flying Probe Testing offers several advantages:
- No need for dedicated test fixtures
- Flexibility to test a wide range of PCB designs
- Ability to test both sides of the PCB
- High test coverage and accuracy
However, Flying Probe Testing can be slower compared to other methods, especially for large and complex PCBs.
Test Coverage and Fault Detection
One of the key aspects of functional testing is ensuring adequate test coverage and fault detection. Test coverage refers to the percentage of the PCB’s functionality that is verified by the test procedures. The goal is to achieve high test coverage to minimize the risk of undetected defects.
Fault detection, on the other hand, focuses on the ability to identify and isolate specific faults or defects on the PCB. Different functional tests have varying levels of fault detection capabilities. For example, ICT can detect a wide range of manufacturing defects, while FCT is better suited for identifying functional issues.
To enhance test coverage and fault detection, several techniques can be employed:
-
Design for Testability (DFT): Incorporating testability features into the PCB design, such as test points, boundary scan architecture, and built-in self-test (BIST) circuits, can greatly facilitate functional testing.
-
Test Planning: Developing a comprehensive test plan that defines the test requirements, test scenarios, and acceptance criteria helps ensure thorough testing and reduces the chances of missing critical defects.
-
Test Automation: Automating functional tests using specialized software and test equipment can improve test efficiency, repeatability, and coverage. Automated tests can be run continuously and can quickly identify issues that may be difficult to detect manually.
-
Fault Simulation: Performing fault simulations during the design phase can help identify potential failure modes and optimize test strategies. Fault simulation tools can inject virtual faults into the PCB design and evaluate the effectiveness of the test procedures in detecting those faults.
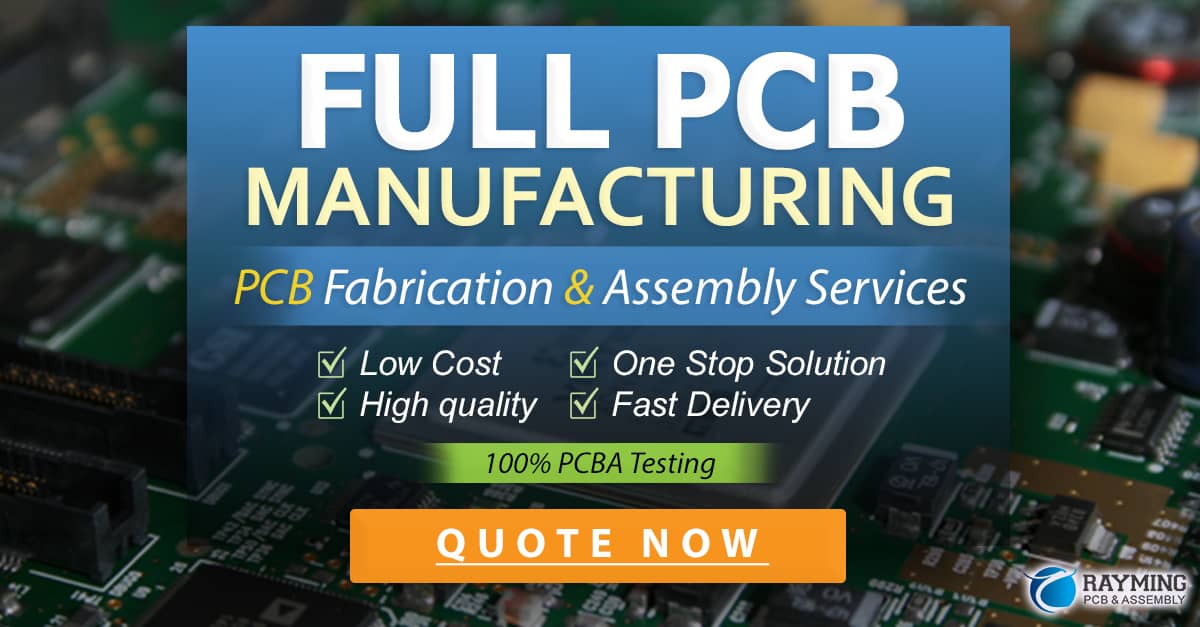
Test Equipment and Setup
Functional testing requires specialized test equipment and setup to accurately evaluate the PCB’s performance. The specific equipment and setup depend on the type of functional test being performed. Some common test equipment used in functional testing includes:
Automated Test Equipment (ATE)
ATEs are computer-controlled systems that automate the execution of functional tests. They typically consist of a test controller, test fixtures, and various instruments such as:
- Digital multimeters (DMMs)
- Oscilloscopes
- Waveform generators
- Power supplies
ATEs offer high test throughput, repeatability, and accuracy. They can be programmed to perform a wide range of tests and can quickly identify defects.
Boundary Scan Test Systems
Boundary Scan Test Systems are specialized equipment designed for performing boundary scan testing. They include a JTAG controller, test fixtures, and software tools for generating and analyzing test patterns. These systems can test complex ICs and interconnections and can diagnose faults at the pin level.
Flying Probe Testers
Flying Probe Testers are automated systems that use movable test probes to access test points on the PCB. They consist of a precise positioning system, test probes, and measurement instruments. Flying Probe Testers offer flexibility and can test a wide range of PCB designs without the need for dedicated fixtures.
Functional Test Fixtures
Functional test fixtures are custom-designed jigs that hold the PCB in place and provide electrical connections to the test equipment. They ensure proper alignment and contact between the PCB and the test probes. Test fixtures can be designed for specific PCB layouts and can include features such as:
- Bed of nails probes
- Vacuum fixtures
- Pneumatic actuators
Well-designed test fixtures are crucial for reliable and repeatable functional testing.
Test Procedures and Documentation
Functional testing requires well-defined test procedures and documentation to ensure consistent and accurate results. Test procedures outline the step-by-step instructions for setting up the test equipment, executing the tests, and interpreting the results. They should include:
- Test objectives and requirements
- Test setup and configuration
- Test sequences and parameters
- Pass/fail criteria
- Troubleshooting guidelines
Test documentation, such as test plans, test reports, and failure analysis reports, provides a record of the testing process and helps track the PCB’s performance over time. It also facilitates communication between the testing team, designers, and manufacturing personnel.
Proper test procedures and documentation are essential for:
- Ensuring test repeatability and reproducibility
- Identifying and resolving issues efficiently
- Meeting regulatory and quality standards
- Continuous improvement of the testing process
Challenges and Best Practices
Functional testing of PCBs can present several challenges, such as:
-
Complexity: As PCBs become more complex, with high-density layouts and advanced components, functional testing becomes more challenging. It requires sophisticated test equipment and techniques to adequately test all aspects of the PCB’s functionality.
-
Time and Cost: Functional testing can be time-consuming and costly, especially for large production volumes. Balancing test coverage, test time, and cost is a critical consideration.
-
Evolving Technologies: With the rapid advancement of electronic technologies, functional testing must keep pace with new components, interfaces, and protocols. Updating test equipment and procedures to accommodate new technologies can be challenging.
To overcome these challenges and ensure effective functional testing, several best practices can be followed:
-
Early Involvement: Engage the testing team early in the PCB design process to incorporate testability features and optimize the design for functional testing.
-
Standardization: Develop standardized test procedures and documentation to ensure consistency and reduce variability in the testing process.
-
Continuous Improvement: Regularly review and update test procedures based on feedback, failure analysis, and advances in testing technologies.
-
Collaboration: Foster collaboration between the design, manufacturing, and testing teams to identify and resolve issues quickly and efficiently.
-
Invest in Training: Provide adequate training to the testing personnel to ensure they have the necessary skills and knowledge to perform functional testing effectively.
Conclusion
Functional testing is a critical aspect of PCB manufacturing that ensures the reliability, performance, and compliance of the final product. It involves a range of tests, such as In-Circuit Testing, Boundary Scan Testing, Functional Circuit Testing, and Flying Probe Testing, each with its own strengths and limitations. Effective functional testing requires careful test planning, adequate test coverage, and fault detection techniques.
To overcome the challenges associated with functional testing, best practices such as early involvement, standardization, continuous improvement, collaboration, and investment in training should be followed. By implementing robust functional testing processes, PCB manufacturers can deliver high-quality products that meet customer expectations and regulatory requirements.
As electronic technologies continue to evolve, functional testing will remain a vital tool in ensuring the reliability and performance of PCBs. Staying up-to-date with the latest testing technologies, techniques, and best practices will be essential for PCB manufacturers to stay competitive in the market.
Frequently Asked Questions (FAQ)
-
What is the difference between functional testing and other types of PCB testing?
Functional testing focuses on evaluating the overall functionality and performance of the PCB under real-world operating conditions. It goes beyond basic continuity and isolation tests and verifies that the PCB meets its specified requirements and operates as intended. Other types of PCB testing, such as in-circuit testing or manufacturing defect analysis, focus on specific aspects of the PCB, such as component functionality or manufacturing quality. -
Is functional testing necessary for all PCBs?
Yes, functional testing is necessary for all PCBs to ensure their reliability, performance, and compliance with specifications. The complexity and extent of functional testing may vary depending on the PCB’s application, criticality, and regulatory requirements. However, some level of functional testing is always recommended to validate the PCB’s functionality before it is integrated into the final product. -
Can functional testing be automated?
Yes, functional testing can be automated using specialized test equipment and software. Automated functional testing offers several benefits, such as improved test efficiency, repeatability, and coverage. It allows for continuous testing and can quickly identify issues that may be difficult to detect manually. Automated test equipment (ATE) and flying probe testers are examples of automated functional testing solutions. -
What are the key considerations when selecting functional test equipment?
When selecting functional test equipment, several key considerations should be taken into account: - Test coverage and fault detection capabilities
- Compatibility with the PCB design and components
- Test speed and throughput
- Flexibility and adaptability to different PCB designs
- Ease of programming and user interface
- Cost and return on investment
-
Support and maintenance options
-
How can functional testing be optimized for cost and time efficiency?
To optimize functional testing for cost and time efficiency, several strategies can be employed: - Implement Design for Testability (DFT) principles in the PCB design phase
- Develop a comprehensive test plan and prioritize critical tests
- Automate functional tests wherever possible
- Use standardized test procedures and documentation
- Invest in training and skills development for testing personnel
- Regularly review and optimize test processes based on data and feedback
- Collaborate with suppliers and partners to streamline the testing process
By considering these factors and implementing best practices, PCB manufacturers can strike a balance between thorough functional testing and cost and time efficiency.
0 Comments