What is Flying Probe Test (FPT)?
Flying Probe Test (FPT) is an advanced method for testing printed circuit boards (PCBs) without the need for a custom test fixture. Unlike traditional bed-of-nails testing, which requires a unique test fixture for each PCB design, FPT utilizes movable probes that can be programmed to test any point on the board. This flexibility makes FPT an ideal solution for low-volume production, prototyping, and high-mix manufacturing environments.
How Flying Probe Test Works
In a typical FPT setup, the PCB is placed on a test platform, and a set of precision-guided probes moves across the board to make contact with the desired test points. The probes can be programmed to perform various electrical tests, such as:
- Continuity testing
- Resistance measurement
- Capacitance measurement
- Diode and transistor testing
- Inductance measurement
The test program is created using CAD data from the PCB design files, ensuring accurate and repeatable testing. The system can quickly adapt to design changes or new board designs, making it a versatile solution for PCB testing.
Advantages of Flying Probe Test
-
Flexibility: FPT can test a wide variety of PCB designs without the need for custom test fixtures, making it ideal for low-volume production and prototyping.
-
Cost-effective: By eliminating the need for custom test fixtures, FPT reduces the overall cost of PCB testing, especially for low-volume production.
-
Fast setup: Programming an FPT system is much faster than designing and building a custom test fixture, allowing for quicker turnaround times.
-
Adaptability: FPT can easily accommodate design changes or new board designs, minimizing the impact on production schedules.
-
High test coverage: FPT can access test points that may be difficult or impossible to reach with a bed-of-nails fixture, resulting in higher test coverage.
Applications of Flying Probe Test
FPT is used in various industries and applications where PCB testing is critical, such as:
- Aerospace and defense
- Automotive electronics
- Medical devices
- Consumer electronics
- Industrial control systems
In these industries, FPT is particularly useful for:
- Prototype validation
- Low-volume production runs
- High-mix, low-volume manufacturing
- Quick turnaround testing
- Rework and repair validation
Types of Flying Probe Testers
There are several types of flying probe testers available, each with its own unique features and capabilities. Some common types include:
Single-sided Flying Probe Testers
Single-sided FPT systems have probes that can access test points on one side of the PCB. These systems are typically more affordable and suitable for simpler PCB designs.
Double-sided Flying Probe Testers
Double-sided FPT systems have probes that can access test points on both sides of the PCB simultaneously. This capability allows for faster testing and is suitable for more complex PCB designs.
Multi-probe Flying Probe Testers
Multi-probe FPT systems feature multiple pairs of probes that can test different points on the PCB simultaneously. This parallel testing approach significantly reduces test time and improves throughput.
High-voltage Flying Probe Testers
High-voltage FPT systems are designed to test PCBs that operate at high voltages, such as those found in power electronics applications. These systems typically have a higher voltage range and specialized probes to ensure safe and accurate testing.
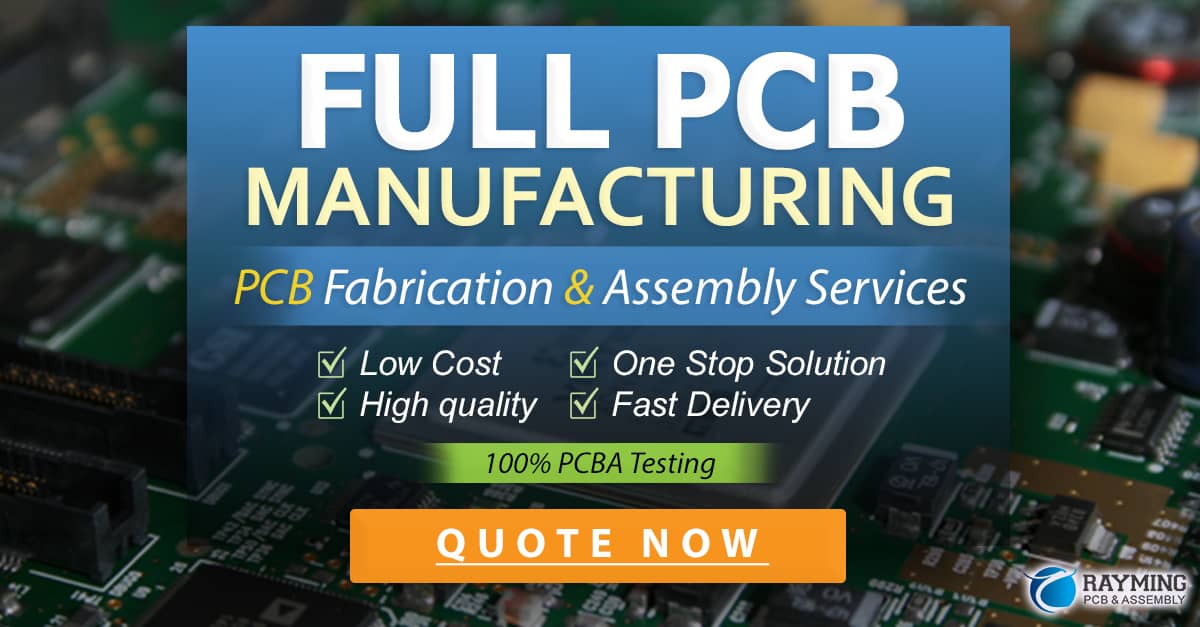
Preparing PCBs for Flying Probe Test
To ensure successful and accurate testing with FPT, it is essential to properly prepare the PCBs. Some key considerations include:
-
Test point design: Ensure that the PCB design includes adequate test points that are accessible by the flying probes. Test points should be of appropriate size and shape, and they should be placed in locations that minimize probe travel time.
-
Fiducial marks: Include fiducial marks on the PCB to help the FPT system align the probes accurately. Fiducial marks are typically placed in the corners or edges of the board.
-
Cleanness: Ensure that the PCB is clean and free from contaminants that could interfere with probe contact, such as flux residue, dust, or oils.
-
Flatness: The PCB should be flat and free from warpage to ensure consistent probe contact across the entire board.
Programming Flying Probe Testers
Programming an FPT system involves creating a test program based on the PCB design files. The test program defines the test points, the sequence of tests to be performed, and the pass/fail criteria for each test. Some key steps in programming an FPT system include:
-
Importing CAD data: Import the PCB design files, such as Gerber or ODB++ files, into the FPT software.
-
Defining test points: Specify the locations of the test points on the PCB, including their coordinates and net names.
-
Selecting test types: Choose the appropriate test types for each test point, such as continuity, resistance, or capacitance.
-
Setting test parameters: Define the test limits, such as the maximum and minimum resistance values, for each test.
-
Optimizing probe path: Optimize the probe path to minimize travel time and improve test efficiency.
-
Verifying the test program: Run a simulated test to verify the test program and ensure that all test points are accessible and that the tests are performed correctly.
Best Practices for Flying Probe Test
To maximize the effectiveness of FPT and ensure reliable results, consider the following best practices:
-
Collaborate with PCB designers: Work closely with PCB designers to ensure that the board layout is optimized for FPT, including the placement of test points and fiducial marks.
-
Maintain probe tips: Regularly inspect and maintain the probe tips to ensure consistent contact and accurate measurements.
-
Monitor system performance: Regularly monitor the performance of the FPT system, including probe positioning accuracy, test repeatability, and throughput, to identify and address any issues promptly.
-
Use appropriate test parameters: Set appropriate test parameters, such as test limits and probe contact force, based on the PCB design and the components being tested.
-
Document test results: Maintain detailed records of test results, including pass/fail data, for traceability and quality control purposes.
Future Trends in Flying Probe Test
As PCB designs continue to become more complex and miniaturized, FPT technology is evolving to keep pace. Some future trends in FPT include:
-
Increased speed and accuracy: Advances in probe positioning systems and motion control algorithms are enabling faster and more accurate testing.
-
Improved probe design: New probe designs, such as multi-point probes and high-frequency probes, are being developed to test smaller and more complex components.
-
Integration with other test methods: FPT is being combined with other test methods, such as automated optical inspection (AOI) and x-ray inspection, to provide more comprehensive PCB testing solutions.
-
Automation and data analytics: The integration of automation and data analytics into FPT systems is enabling more efficient test processes and better insights into PCB quality and manufacturing trends.
FAQ
1. How does Flying Probe Test differ from traditional bed-of-nails testing?
Flying Probe Test uses movable probes that can be programmed to test any point on the PCB, while bed-of-nails testing requires a custom test fixture for each PCB design. FPT offers greater flexibility and adaptability, while bed-of-nails testing is better suited for high-volume production of a single PCB design.
2. Can Flying Probe Test be used for high-volume production?
While FPT is typically used for low-volume production, prototyping, and high-mix manufacturing, it can be used for high-volume production in certain situations. For example, if the PCB design is complex or frequently changing, FPT may be more cost-effective than creating custom test fixtures for each design iteration.
3. How long does it take to program a Flying Probe Tester?
The time required to program an FPT system depends on the complexity of the PCB design and the number of test points. However, programming an FPT system is generally much faster than designing and building a custom test fixture for bed-of-nails testing.
4. What are the limitations of Flying Probe Test?
Some limitations of FPT include slower test speeds compared to bed-of-nails testing for high-volume production, limited access to test points in highly congested areas of the PCB, and potential probe wear over time due to repeated contact with the board.
5. How much does a Flying Probe Tester cost?
The cost of a Flying Probe Tester varies depending on factors such as the number of probes, the level of automation, and the software features included. Entry-level systems can cost around $100,000, while high-end systems with advanced capabilities can cost over $500,000. However, the cost of an FPT system should be weighed against the potential savings in test fixture costs and improved flexibility in PCB testing.
Conclusion
Flying Probe Test is a versatile and efficient method for testing printed circuit boards, offering numerous advantages over traditional bed-of-nails testing. By utilizing movable probes that can be programmed to test any point on the board, FPT provides greater flexibility, adaptability, and cost-effectiveness for low-volume production, prototyping, and high-mix manufacturing environments.
As PCB designs continue to become more complex and miniaturized, FPT technology is evolving to keep pace, with advances in probe design, speed, accuracy, and integration with other test methods. By understanding the capabilities and best practices of FPT, manufacturers can optimize their PCB testing processes and ensure the highest levels of quality and reliability in their products.
0 Comments