Introduction to Flex PCBs
Flexible circuit boards, also known as flex PCBs or flexible printed circuit boards, are a revolutionary technology that has transformed the electronics industry. Unlike traditional rigid PCBs, flex PCBs are designed to be flexible, allowing them to conform to various shapes and fit into tight spaces. This unique characteristic has made them indispensable in a wide range of applications, from consumer electronics to medical devices and aerospace systems.
What are Flex PCBs?
Flex PCBs are printed circuit boards made from flexible materials, typically polyimide or polyester. These materials provide the flexibility needed for the circuit board to bend and twist without breaking or losing its electrical properties. The conductive traces on a flex PCB are usually made of copper, which is bonded to the flexible substrate using adhesive or lamination techniques.
Advantages of Flex PCBs
Flex PCBs offer several advantages over traditional rigid PCBs:
-
Flexibility: The most obvious advantage of flex PCBs is their ability to bend and flex, allowing them to conform to various shapes and fit into tight spaces.
-
Lightweight: Flex PCBs are typically thinner and lighter than rigid PCBs, making them ideal for applications where weight is a critical factor, such as in aerospace and portable electronics.
-
Durability: Despite their flexibility, flex PCBs are highly durable and can withstand repeated bending and flexing without breaking or losing their electrical properties.
-
Improved signal integrity: Flex PCBs can be designed with shorter signal paths, reducing the risk of signal interference and improving overall signal integrity.
-
Space savings: By eliminating the need for connectors and wires between rigid PCBs, flex PCBs can significantly reduce the overall size and weight of electronic assemblies.
Types of Flex PCBs
There are several types of flex PCBs, each designed for specific applications and requirements.
Single-sided Flex PCBs
Single-sided flex PCBs have conductive traces on only one side of the flexible substrate. They are the simplest and most cost-effective type of flex PCB, suitable for applications with low component density and simple circuit designs.
Double-sided Flex PCBs
Double-sided flex PCBs have conductive traces on both sides of the flexible substrate, allowing for higher component density and more complex circuit designs. They often include plated through-holes (PTHs) to connect the traces on both sides.
Multi-layer Flex PCBs
Multi-layer flex PCBs consist of multiple layers of flexible substrate with conductive traces, separated by insulating layers. They offer the highest component density and the most complex circuit designs, making them suitable for advanced applications in aerospace, military, and medical devices.
Rigid-Flex PCBs
Rigid-flex PCBs combine the benefits of both rigid and flexible PCBs by incorporating rigid sections and flexible sections in a single circuit board. This allows for the integration of complex electronic assemblies into a single, compact package, reducing the need for connectors and wires.
Manufacturing Process of Flex PCBs
The manufacturing process of flex PCBs is similar to that of rigid PCBs but with some unique considerations due to the flexible nature of the substrate.
Material Selection
The choice of flexible substrate material depends on the specific application and requirements, such as temperature range, chemical resistance, and mechanical properties. Polyimide and polyester are the most common materials used for flex PCBs.
Circuit Design and Layout
The circuit design and layout for flex PCBs must consider the flexibility of the substrate and the mechanical stresses that the board will experience during use. The design should also minimize the number of layers and the use of through-holes to maintain flexibility.
Lamination and Etching
The flexible substrate is laminated with a thin layer of copper, which is then etched to create the desired circuit pattern. The etching process is similar to that used for rigid PCBs but may require special considerations to ensure proper adhesion and prevent delamination.
Coverlay Application
A coverlay, typically made of polyimide or a similar material, is applied over the etched circuit pattern to protect the traces and provide electrical insulation. The coverlay is laminated to the flex PCB using heat and pressure.
Cutting and Finishing
The final step in the manufacturing process is cutting the flex PCB to the desired shape and size. This can be done using a variety of methods, such as die-cutting, laser cutting, or routing. Additional finishing steps, such as the application of solder mask or surface finishes, may also be performed.
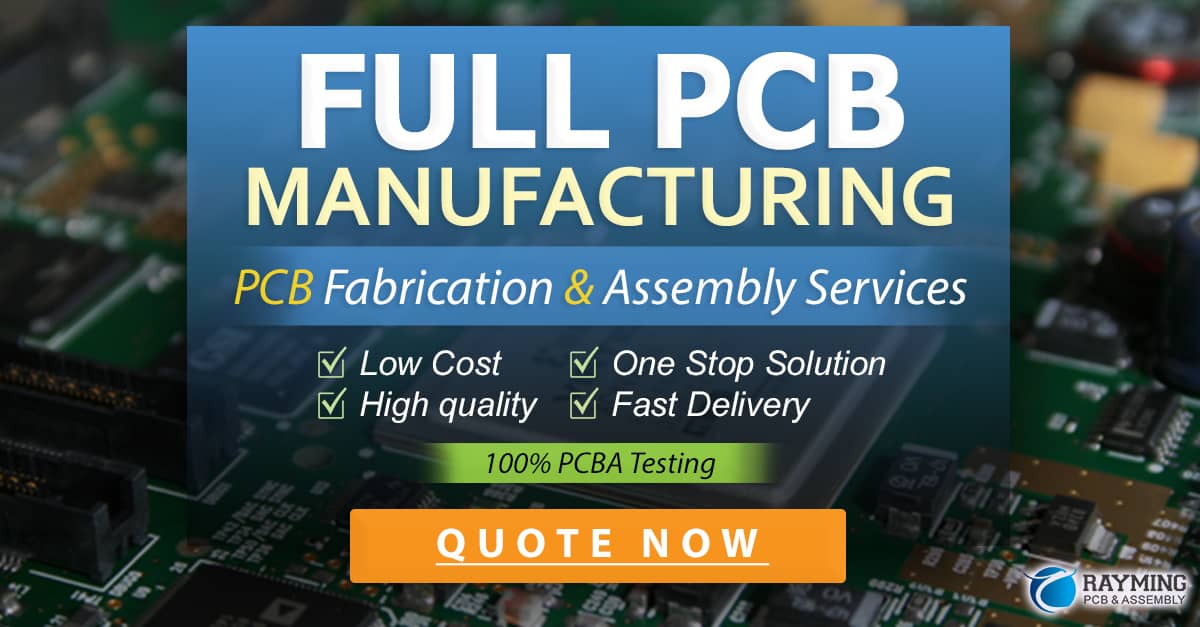
Applications of Flex PCBs
Flex PCBs have found widespread use in various industries due to their unique properties and advantages.
Consumer Electronics
Flex PCBs are extensively used in consumer electronics, such as smartphones, tablets, and wearable devices. They enable the design of compact, lightweight, and flexible devices that can withstand the rigors of daily use.
Medical Devices
Flex PCBs are essential in medical devices, particularly in implantable and wearable devices. They allow for the creation of miniaturized, biocompatible electronics that can conform to the shape of the human body and withstand the harsh environment inside the body.
Aerospace and Military
In aerospace and military applications, flex PCBs are used to create lightweight, compact, and reliable electronic systems that can withstand extreme temperatures, vibrations, and other harsh environmental conditions.
Automotive Electronics
Flex PCBs are increasingly used in automotive electronics, such as dashboard displays, sensors, and control modules. They offer the flexibility and durability needed to withstand the vibrations and temperature fluctuations experienced in a vehicle.
Industrial Automation
Flex PCBs are used in industrial automation systems, such as robots and machine vision systems, where they enable the creation of compact, flexible, and reliable electronic assemblies that can operate in harsh industrial environments.
Designing Flex PCBs
Designing flex PCBs requires careful consideration of several factors to ensure optimal performance and reliability.
Material Selection
The choice of flexible substrate material is critical to the performance and reliability of the flex PCB. Factors to consider include the operating temperature range, chemical resistance, and mechanical properties of the material.
Bend Radius and Flexibility
The bend radius and flexibility of the flex PCB must be carefully designed to ensure that the board can withstand the expected mechanical stresses without breaking or losing its electrical properties. The minimum bend radius should be at least six times the thickness of the board.
Trace Routing and Spacing
Trace routing and spacing on a flex PCB must be carefully designed to minimize stress on the traces during bending and to ensure proper signal integrity. The traces should be routed perpendicular to the bend axis whenever possible, and the spacing between traces should be increased in areas of high stress.
Strain Relief
Strain relief features, such as stiffeners and anchors, should be incorporated into the design of the flex PCB to prevent damage to the traces and components during bending and flexing.
Component Selection and Placement
The selection and placement of components on a flex PCB must consider the mechanical stresses that the board will experience during use. Surface-mount components are typically preferred over through-hole components to minimize stress on the board.
Testing and Quality Control
Ensuring the quality and reliability of flex PCBs requires rigorous testing and quality control procedures.
Visual Inspection
Visual inspection is the first step in the quality control process, involving a thorough examination of the flex PCB for any visible defects, such as scratches, dents, or delamination.
Continuity and Resistance Testing
Continuity and resistance testing are performed to ensure that all electrical connections on the flex PCB are intact and that there are no short circuits or open circuits.
Flexibility Testing
Flexibility testing is conducted to ensure that the flex PCB can withstand the expected mechanical stresses without breaking or losing its electrical properties. This typically involves subjecting the board to repeated bending cycles and measuring its electrical performance.
Environmental Testing
Environmental testing is performed to ensure that the flex PCB can operate reliably in the expected environmental conditions, such as temperature, humidity, and vibration. This may involve subjecting the board to thermal cycling, humidity cycling, and vibration testing.
Accelerated Life Testing
Accelerated life testing is conducted to predict the long-term reliability of the flex PCB by subjecting it to elevated stress levels and measuring its performance over time. This helps identify potential failure modes and ensures that the board will meet its intended lifespan.
Future Trends in Flex PCBs
As technology continues to advance, flex PCBs are expected to play an increasingly important role in the electronics industry.
Increased Adoption in Wearable Devices
The growth of the wearable device market is expected to drive increased adoption of flex PCBs, as they enable the creation of compact, lightweight, and flexible devices that can conform to the shape of the human body.
Advancements in Materials and Manufacturing
New materials and manufacturing techniques are being developed to improve the performance and reliability of flex PCBs. These include the use of high-performance polymers, such as liquid crystal polymers (LCPs), and advanced manufacturing techniques, such as 3D printing and laser direct structuring (LDS).
Integration with Emerging Technologies
Flex PCBs are expected to play a key role in the integration of emerging technologies, such as 5G wireless networks, the Internet of Things (IoT), and artificial intelligence (AI). They will enable the creation of compact, flexible, and reliable electronic systems that can support these technologies.
Increased Focus on Sustainability
As environmental concerns continue to grow, there is an increasing focus on sustainability in the electronics industry. Flex PCBs can contribute to sustainability efforts by reducing the use of materials, enabling the creation of more compact and lightweight devices, and facilitating the development of renewable energy systems.
Frequently Asked Questions (FAQ)
-
What is the difference between flex PCBs and rigid PCBs?
Flex PCBs are made from flexible materials, such as polyimide or polyester, which allow them to bend and conform to various shapes. Rigid PCBs, on the other hand, are made from rigid materials, such as FR-4, and cannot bend or flex. -
What are the advantages of using flex PCBs?
Flex PCBs offer several advantages, including flexibility, lightweight construction, durability, improved signal integrity, and space savings. They enable the creation of compact, flexible, and reliable electronic assemblies that can withstand harsh environmental conditions. -
What industries commonly use flex PCBs?
Flex PCBs are used in a wide range of industries, including consumer electronics, medical devices, aerospace, military, automotive electronics, and industrial automation. -
How are flex PCBs manufactured?
The manufacturing process for flex PCBs involves material selection, circuit design and layout, lamination and etching, coverlay application, and cutting and finishing. The process is similar to that used for rigid PCBs but with special considerations for the flexible nature of the substrate. -
What factors should be considered when designing flex PCBs?
When designing flex PCBs, several factors must be considered, including material selection, bend radius and flexibility, trace routing and spacing, strain relief, and component selection and placement. Careful consideration of these factors is essential to ensure optimal performance and reliability of the flex PCB.
Conclusion
Flex PCBs have revolutionized the electronics industry, enabling the creation of compact, lightweight, and flexible electronic assemblies that can withstand harsh environmental conditions. With their unique properties and advantages, flex PCBs have found widespread use in various industries, from consumer electronics to medical devices and aerospace systems.
As technology continues to advance, flex PCBs are expected to play an increasingly important role in the development of new and innovative electronic products. By understanding the fundamentals of flex PCBs, including their types, manufacturing process, design considerations, and testing and quality control procedures, engineers and designers can leverage this technology to create the next generation of electronic devices.
Characteristic | Flex PCBs | Rigid PCBs |
---|---|---|
Flexibility | High | Low |
Weight | Low | High |
Durability | High | Moderate |
Signal Integrity | Improved | Standard |
Space Savings | High | Low |
Table 1: Comparison of key characteristics between flex PCBs and rigid PCBs.
As the demand for smaller, lighter, and more flexible electronic devices continues to grow, flex PCBs will undoubtedly play a crucial role in shaping the future of the electronics industry. By embracing this technology and its potential, companies can stay ahead of the curve and deliver innovative products that meet the evolving needs of their customers.
0 Comments