Introduction to Flex PCB Technology
Flexible printed circuit boards (Flex PCBs) have revolutionized the electronics industry by providing a versatile and reliable solution for interconnecting electronic components in applications where traditional rigid PCBs fall short. Flex PCBs offer numerous advantages, including increased design flexibility, improved reliability, and reduced assembly costs. This article will delve into the world of Flex PCB technology and manufacturing, exploring its benefits, applications, and the processes involved in creating these innovative circuit boards.
What is a Flex PCB?
A Flex PCB, also known as a flexible circuit board, is a type of printed circuit board that consists of a thin, flexible substrate with conductive traces and components mounted on its surface. Unlike rigid PCBs, which are made from a solid, non-flexible material, Flex PCBs can bend and twist without damaging the electrical connections. This unique property makes them ideal for applications where the circuit board needs to conform to a specific shape or withstand repeated flexing.
Advantages of Flex PCBs
Flex PCBs offer several advantages over traditional rigid PCBs:
-
Design Flexibility: Flex PCBs can be designed to fit into tight spaces and conform to complex shapes, making them ideal for applications with limited space or unique packaging requirements.
-
Reduced Weight and Size: By eliminating the need for bulky connectors and wires, Flex PCBs can significantly reduce the overall weight and size of electronic devices.
-
Improved Reliability: Flex PCBs are more resistant to vibration and shock than rigid PCBs, as they can absorb mechanical stress without cracking or breaking. This improved reliability translates to longer product life and reduced maintenance costs.
-
Simplified Assembly: Flex PCBs can be designed with fewer interconnects and connectors, simplifying the assembly process and reducing the risk of errors.
-
Cost Savings: Although the initial cost of Flex PCBs may be higher than rigid PCBs, the reduced assembly time, improved reliability, and elimination of connectors can result in significant cost savings over the product’s lifecycle.
Applications of Flex PCBs
Flex PCBs find applications in a wide range of industries, including:
-
Consumer Electronics: Flex PCBs are commonly used in smartphones, tablets, wearables, and other portable devices where space is at a premium, and reliability is crucial.
-
Automotive: In the automotive industry, Flex PCBs are used in applications such as dashboard displays, sensors, and engine control units, where they must withstand harsh environmental conditions and vibrations.
-
Medical Devices: Flex PCBs are used in medical devices such as implantable sensors, wearable health monitors, and surgical instruments, where they must be biocompatible and able to withstand sterilization processes.
-
Aerospace and Defense: Flex PCBs are used in aerospace and defense applications, such as satellites, aircraft, and military equipment, where they must be lightweight, reliable, and able to withstand extreme temperatures and radiation.
-
Industrial Automation: Flex PCBs are used in industrial automation systems, such as robotics, motion control, and machine vision, where they must be able to withstand harsh environments and repeated flexing.
Flex PCB Manufacturing Process
The manufacturing process for Flex PCBs is similar to that of rigid PCBs, with a few key differences to accommodate the flexible substrate. The main steps involved in Flex PCB manufacturing are:
-
Substrate Selection: The first step in Flex PCB manufacturing is selecting the appropriate flexible substrate material. The most common materials used are polyimide (PI) and polyester (PET), which offer excellent electrical properties, thermal stability, and mechanical flexibility.
-
Circuit Design: The circuit design is created using computer-aided design (CAD) software, taking into account the specific requirements of the application, such as the desired flexibility, bend radius, and component placement.
-
Lamination: The flexible substrate is laminated with a thin layer of copper foil using heat and pressure. This process creates a strong bond between the substrate and the copper, ensuring the integrity of the electrical connections.
-
Patterning: The copper layer is then patterned using a photolithography process, which involves coating the copper with a light-sensitive material (photoresist), exposing it to UV light through a patterned mask, and then etching away the unwanted copper to create the desired circuit pattern.
-
Drilling: If required, holes are drilled through the Flex PCB to accommodate through-hole components or vias, which are used to connect different layers of the circuit.
-
Plating: The drilled holes and exposed copper traces are then plated with a thin layer of copper, followed by a layer of tin or gold, to improve the electrical conductivity and protect against oxidation.
-
Solder Mask Application: A solder mask is applied to the Flex PCB to protect the copper traces from short-circuits and environmental damage. The solder mask also helps to define the areas where components will be soldered.
-
Silkscreen Printing: A silkscreen layer is printed onto the Flex PCB to add text, logos, and other markings that aid in assembly and identification.
-
Surface Finishing: The exposed copper areas, such as contact pads and terminals, are plated with a surface finish, such as gold, silver, or ENIG (Electroless Nickel Immersion Gold), to improve solderability and protect against corrosion.
-
Cutting and Punching: The Flex PCB panel is then cut and punched into individual circuit boards using a die-cutting process or laser cutting, depending on the complexity of the design and the required tolerances.
-
Assembly: Finally, the components are assembled onto the Flex PCB using either surface mount technology (SMT) or through-hole technology (THT), depending on the specific requirements of the application.
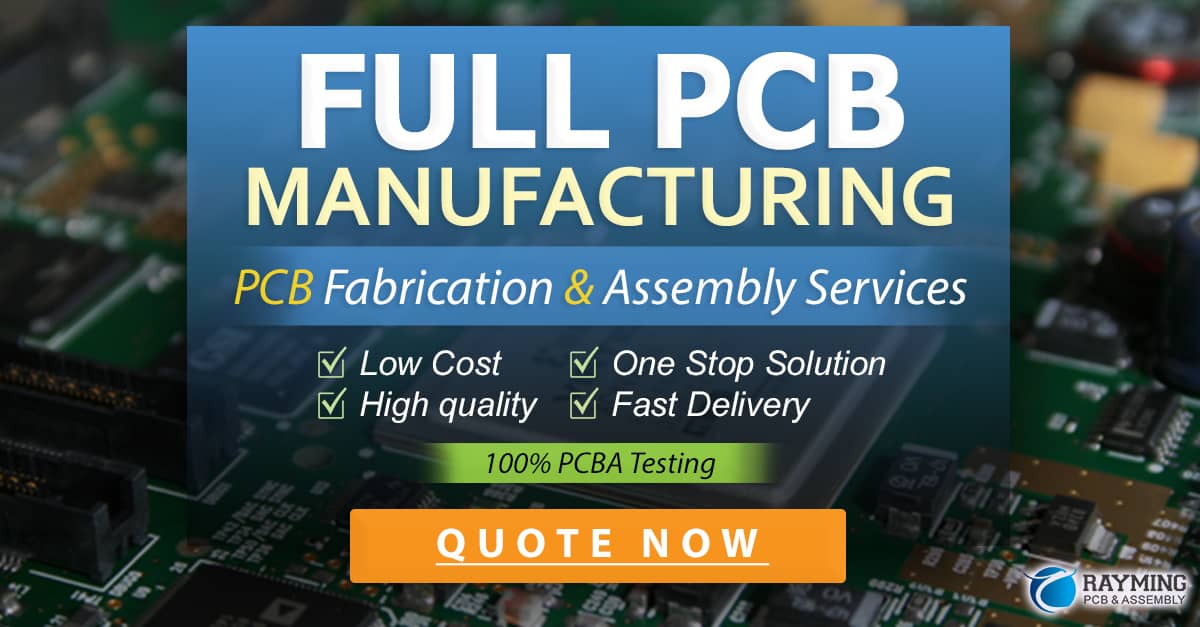
Rigid Flex PCB Technology
Rigid Flex PCBs are a hybrid of traditional rigid PCBs and Flex PCBs, combining the benefits of both technologies. A Rigid Flex PCB consists of one or more rigid PCB sections connected by flexible PCB sections, allowing for three-dimensional packaging and improved reliability in applications where the circuit board must conform to a specific shape or withstand repeated flexing.
Advantages of Rigid Flex PCBs
Rigid Flex PCBs offer several advantages over using separate rigid and Flex PCBs:
-
Reduced Assembly Time: By combining rigid and flexible sections into a single PCB, the number of interconnects and connectors is reduced, simplifying the assembly process and reducing the risk of errors.
-
Improved Reliability: Rigid Flex PCBs eliminate the need for connectors between rigid and flexible sections, which are often a point of failure in electronic devices. This improved reliability translates to longer product life and reduced maintenance costs.
-
Reduced Weight and Size: Rigid Flex PCBs allow for more compact packaging and can reduce the overall weight and size of electronic devices by eliminating the need for bulky connectors and wires.
-
Enhanced Design Flexibility: Rigid Flex PCBs enable three-dimensional packaging and can be designed to fit into complex shapes and tight spaces, making them ideal for applications with unique packaging requirements.
Rigid Flex PCB Manufacturing Process
The manufacturing process for Rigid Flex PCBs is similar to that of Flex PCBs, with the addition of rigid PCB sections and the use of specialized materials and techniques to ensure a strong and reliable connection between the rigid and flexible sections.
-
Material Selection: In addition to the flexible substrate materials used in Flex PCBs, Rigid Flex PCBs also incorporate rigid substrate materials, such as FR-4, for the rigid sections of the board.
-
Lamination: The rigid and flexible substrate materials are laminated together using a combination of heat, pressure, and specialized adhesives, creating a strong bond between the sections.
-
Circuit Patterning: The copper layers on both the rigid and flexible sections are patterned using photolithography, similar to the process used for Flex PCBs.
-
Drilling and Plating: Holes are drilled through the rigid and flexible sections, and the holes and exposed copper traces are plated with copper and a protective finish.
-
Solder Mask and Silkscreen: A solder mask is applied to the rigid and flexible sections, and a silkscreen layer is printed for identification and assembly purposes.
-
Cutting and Punching: The Rigid Flex PCB panel is cut and punched into individual circuit boards, with special attention given to the transition areas between the rigid and flexible sections to ensure a smooth and reliable connection.
-
Assembly: Components are assembled onto the rigid and flexible sections using SMT or THT, depending on the specific requirements of the application.
Flex PCB Design Considerations
When designing a Flex PCB, there are several key considerations to keep in mind to ensure optimal performance, reliability, and manufacturability:
-
Bend Radius: The bend radius is the minimum radius to which a Flex PCB can be bent without damaging the copper traces or causing delamination. The bend radius depends on the thickness of the substrate and the copper, as well as the number of layers in the Flex PCB. It is essential to design the Flex PCB with the appropriate bend radius to avoid failures during use.
-
Copper Thickness: The thickness of the copper traces on a Flex PCB can affect its flexibility and current-carrying capacity. Thinner copper traces are more flexible but have a lower current-carrying capacity, while thicker traces are less flexible but can carry more current. It is important to select the appropriate copper thickness based on the electrical requirements of the application and the desired flexibility.
-
Coverlay and Stiffeners: Coverlay is a protective layer applied to the Flex PCB to insulate and protect the copper traces. Stiffeners are used to reinforce specific areas of the Flex PCB, such as connector areas or component mounting locations, to improve durability and reliability. The placement and thickness of coverlay and stiffeners should be carefully considered to ensure the desired flexibility and mechanical stability of the Flex PCB.
-
Trace Width and Spacing: The width and spacing of the copper traces on a Flex PCB can affect its electrical performance and manufacturability. Wider traces can carry more current but may reduce the flexibility of the board, while narrower traces are more flexible but have a lower current-carrying capacity. The spacing between traces should be sufficient to prevent short-circuits and ensure reliable operation.
-
Component Placement: When placing components on a Flex PCB, it is important to consider the flexibility requirements of the application. Components should be placed in areas of the Flex PCB that will experience minimal bending or flexing to reduce the risk of component damage or solder joint failure. In some cases, it may be necessary to use specialized components, such as flexible connectors or surface mount devices with a low profile, to ensure reliable operation in a flexible environment.
Flex PCB Testing and Quality Control
To ensure the reliability and performance of Flex PCBs, rigorous testing and quality control measures are implemented throughout the manufacturing process. Some of the key testing and quality control steps include:
-
Visual Inspection: Flex PCBs are visually inspected for defects such as scratches, dents, or delamination, which could affect their performance or reliability.
-
Continuity Testing: Electrical continuity testing is performed to ensure that all the copper traces on the Flex PCB are properly connected and that there are no short-circuits or open connections.
-
Insulation Resistance Testing: Insulation resistance testing is conducted to verify that the insulation between the copper traces and the substrate is sufficient to prevent electrical leakage and ensure reliable operation.
-
Flexibility Testing: Flex PCBs are subjected to flexibility testing to ensure that they can withstand the expected number of bending cycles without damage or degradation in performance. This testing typically involves repeatedly bending the Flex PCB to its minimum bend radius and inspecting for any signs of damage or failure.
-
Environmental Testing: Depending on the application, Flex PCBs may be subjected to environmental testing to ensure that they can withstand the expected operating conditions, such as temperature, humidity, and vibration. This testing helps to identify potential failure modes and ensure the long-term reliability of the Flex PCB.
-
Functional Testing: Functional testing is performed on the assembled Flex PCB to verify that it meets the specified electrical and mechanical requirements of the application. This testing may involve measuring electrical parameters, such as voltage, current, and resistance, as well as verifying the mechanical performance of the Flex PCB under simulated use conditions.
Future Trends in Flex PCB Technology
As the demand for smaller, lighter, and more flexible electronic devices continues to grow, Flex PCB technology is expected to evolve to meet these challenges. Some of the key trends shaping the future of Flex PCB technology include:
-
Increased Miniaturization: Advances in materials and manufacturing processes are enabling the production of ever-thinner and more flexible Flex PCBs, allowing for even greater miniaturization of electronic devices.
-
High-Speed Applications: As data rates continue to increase, Flex PCBs are being designed to support high-speed applications, such as 5G wireless communication and high-bandwidth data transfer.
-
Advanced Materials: New substrate materials, such as liquid crystal polymers (LCPs) and thermoplastic polyurethanes (TPUs), are being developed to provide enhanced flexibility, thermal stability, and electrical performance for demanding applications.
-
Embedded Components: The integration of passive components, such as resistors and capacitors, directly into the Flex PCB substrate is becoming more common, enabling further miniaturization and improved reliability.
-
Sustainable Manufacturing: There is a growing emphasis on sustainable manufacturing practices in the Flex PCB industry, including the use of recyclable materials and the adoption of environmentally friendly processes, such as lead-free soldering and halogen-free substrates.
Frequently Asked Questions (FAQ)
-
What is the difference between a Flex PCB and a rigid PCB?
A Flex PCB is made from a thin, flexible substrate material that allows the circuit board to bend and twist without damaging the electrical connections. In contrast, a rigid PCB is made from a solid, non-flexible material and cannot be bent or flexed. -
What are the main advantages of using Flex PCBs?
Flex PCBs offer several advantages, including increased design flexibility, reduced weight and size, improved reliability, simplified assembly, and potential cost savings over the product’s lifecycle. -
What industries commonly use Flex PCBs?
Flex PCBs are used in a wide range of industries, including consumer electronics, automotive, medical devices, aerospace and defense, and industrial automation. -
What is a Rigid Flex PCB, and what are its benefits?
A Rigid Flex PCB is a hybrid of rigid and flexible PCBs, combining the benefits of both technologies. Rigid Flex PCBs offer reduced assembly time, improved reliability, reduced weight and size, and enhanced design flexibility compared to using separate rigid and Flex PCBs. -
What are some key design considerations when creating a Flex PCB?
When designing a Flex PCB, key considerations include the bend radius, copper thickness, coverlay and stiffeners, trace width and spacing, and component placement. These factors must be carefully balanced to ensure optimal performance, reliability, and manufacturability of the Flex PCB.
Conclusion
Flex PCB technology has revolutionized the electronics industry, enabling the development of smaller, lighter, and more reliable devices across a wide range of applications. By understanding the advantages, manufacturing processes, design considerations, and testing requirements associated with Flex PCBs, engineers and designers can create innovative solutions that push the boundaries of what is possible in electronic packaging.
As the demand for more advanced and flexible electronic devices continues to grow, the future of Flex PCB technology looks bright. With ongoing advances in materials, manufacturing processes, and design tools, Flex PCBs are poised to play an increasingly important role in shaping the future of the electronics industry.
Flex PCB Characteristic | Description |
---|---|
Substrate Material | Polyimide (PI), Polyester (PET) |
Copper Thickness | Typically 18-35 µm |
Minimum Bend Radius | Depends on substrate and copper thickness |
Trace Width and Spacing | Depends on electrical and flexibility requirements |
Surface Finishes | ENIG, OSP, Immersion Silver, Immersion Tin |
Common Applications | Consumer electronics, automotive, medical devices, aerospace, industrial automation |
0 Comments