For hardware companies, getting products to market faster is critical to seize opportunities and edge out competitors. However, PCB assembly, with its long process cycles, complex logistics and stringent quality needs, is often a bottleneck. Utilizing fast PCB assembly services is key to overcoming this and accelerating time-to-market.
In this guide, we’ll cover:
- Importance of Fast PCB Assembly
- Comparison of PCB Assembly Approaches
- Keys to Enable Rapid Prototype Assembly
- Techniques for High-Speed Low-Volume Production
- Strategies for Streamlining Mass Production
- Role of Supply Chain and Contract Manufacturing
- Testing Considerations with Faster Assembly
- Cost Implications of Expedited Assembly
- FAQs on Fast PCB Assembly
Let’s examine how to slash PCB assembly lead times across prototyping, initial production, and volume manufacturing.
Importance of Fast PCB Assembly
Getting working PCB prototypes and production boards assembled quickly provides many benefits:
- Faster design validation – Verify design functionality sooner with quick-turn assembled prototypes.
- Rapid design iteration – With fast assembly, multiple design spins can be tested in parallel.
- Accelerated time-to-market – Products with the latest features can be launched ahead of competition.
- Quicker customer samples – Get sales samples out faster to secure orders and feedback.
- Faster manufacturing ramp-up – Front-load production to fulfill early demand spikes and avoid stock-outs.
- Lower costs – Faster product launch means earlier realization of revenue, reducing costs.
- Enhanced agility – Ability to respond quickly to changing requirements and new opportunities.
For today’s fast-paced electronics markets, long PCB assembly lead times is a massive competitive disadvantage. Investing in fast assembly capabilities is becoming imperative.
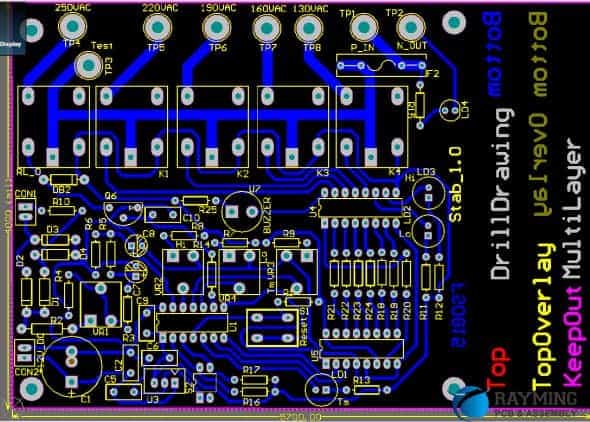
Comparison of PCB Assembly Approaches
There are three primary options for getting PCBs assembled, each with different costs, lead times and capabilities:<div class=”table-wrap”>
Approach | Description | Lead Times | Volumes Supported |
---|---|---|---|
In-house Assembly | Investing in SMT lines and skilled staff for assembly | 12-16 weeks (equipment) + training period | 10 – 5,000 boards/week |
Contract Manufacturing Partners | Outsourcing assembly to third-party assemblers | 4-8 weeks | 500 – 20,000 boards/week |
PCB Assembly Services | Utilizing specialized quick-turn assembly providers | 5-10 days | 5 – 1,000 boards/week |
</div>
For fast assembly during prototyping and pre-production, PCB assembly services are the optimal choice, avoiding lengthy in-house setup times or contract manufacturer schedules.
Keys to Enable Rapid Prototype PCB Assembly
To assemble PCB prototypes in just days rather than weeks, leveraging quick-turn assembly services is key. Here are ways to enable it:
- Design for Manufacturability (DFM) – Ensure design is assembly-friendly right from prototyping stage.
- Standardize Components – Reuse previously used parts as much as possible across versions.
- Concurrent Engineering – Start assembly planning even as design is being finished.
- Local Sourcing – Source components from trusted distributors with local warehouses.
- No BOM Changes – Avoid BOM churn during prototyping to prevent iterative sourcing.
- Single PCB Partner – Use one assembly provider throughout prototyping for continuity.
- Panelization – Manufacture in panels for faster processing.
- Fab & Assembly Together – Keep both under one roof for seamless coordination.
- On-Demand Capacity – Work with assemblers who can provide flexible capacity.
Following these best practices reduces overall assembly timeline for PCB prototypes by 50-80%, cuting lead times from weeks to days.
Techniques for High-Speed Low-Volume PCB Production
The transition from prototyping to initial production often sees large lead time increases. Here are techniques to prevent that:
- Advanced Purchasing – For long lead components, place orders in advance during prototyping.
- Build Inventory – Stock up on components, especially those at risk of shortage.
- Forecast Demand – Share initial sales estimates so assembler can plan capacity.
- Flexible Capacity – Use an assembler that can dynamically adjust lines & shifts.
- Board Reuse – Retain boards from prototype builds and rework for initial production.
- Staged Ramp-Up – Gradually increase volumes each month for controlled scaling.
- Expediting Fees – Pay premiums for prioritized scheduling and overtime.
- Temporary Contracts – Supplement with additional capacity from other assemblers.
- Nearby Assembly – Start production with local assemblers before offshoring.
With good planning, production lead times of just 2-3 weeks are achievable even at volumes of 500-1000 boards.
Strategies for Streamlining Mass Production PCB Assembly
At volume production stage, absolute minimum lead times are difficult to attain. But here are some strategies for optimization:
- Detailed Forecasting – Provide 12-18 month rolling forecast to give assembler visibility.
- Framework Contracts – Secure dedicated capacity at contract manufacturers.
- Component Standardization – Minimize BOM variations across products and over time.
- Build-to-Order – Wait for customer order before starting production to cut inventory.
- Ship-to-Stock – Air ship initial finished goods to open sales channels sooner.
- Risk Production – Build limited quantities in advance of forecast to prevent shortages.
- Dual Sourcing – Maintain backup production sources for surge capacity.
- Localization – Position assembly nearer to target markets to save logistics time.
While attaining quick-turn performance gets harder at scale, these techniques can still help compress lead times significantly.
Role of Supply Chain and Contract Manufacturing
To enable fast PCB assembly, choosing manufacturing partners strategically is vital:
Component Sourcing
- Local Distributors – Source from local warehouses for fastest delivery
- Custom Brokering – Leverage brokers to find parts with best lead time
- Strategic Stocking – Have assembler stock long-lead components
- Alternative Parts – Be open substituting approved alternates if faster
Contract Manufacturers
- Qualify Multiple – Maintain 2-3 assemblers for flexibility
- Check Capabilities – Evaluate technical breadth for future needs
- Review Capacity – Ensure adequate capacity for demand swings
- Validate Quality – Audit and approve key processes
- Demand Forecasts – Provide quarterly rolling estimates
- Monitor Flexibility – Track ability to compress lead times
Strong supply chain and manufacturing partnerships are instrumental for rapid PCB assembly across product life cycles.
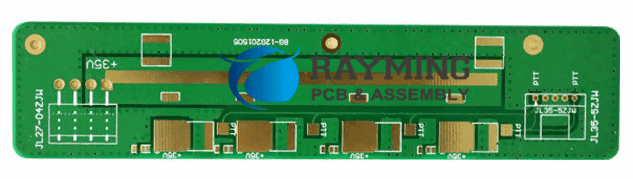
Testing Considerations with Faster Assembly
While fast assembly is needed for quick product launch, quality cannot be compromised. Some testing considerations include:
- Design Reviews – Invest more time upfront in rigorous DFM analysis.
- First Article Audits – Perform detailed inspection of initial boards.
- Test Development – Ensure test plans are defined during assembly, not after.
- Early Testing – Start testing key functionality before full assembly lot is complete.
- In-line Monitoring – Use test fixtures at critical process steps for early feedback.
- Traceability – Ensure assembler provides full component traceability.
- Failure Analysis – Study any defects deeply for root cause.
- Quality Feedback – Provide ongoing input to assembler on issues observed.
- Guardbanding – Keep slightly higher defect margins when accelerating assembly.
While compressing assembly schedules, maintaining strong quality practices prevents downstream disruptions.
Cost Implications of Expedited PCB Assembly
Faster assembly invariably comes at a premium cost. Some considerations:
- NRE Charges – One-time fees for prioritized scheduling, out of cycle setups etc.
- Expedite Fees – Recurring fees for accelerated delivery each time, typically 10-25% premium.
- Shift Overtime – Extra hourly charges for additional shifts to maximize capacity utilization.
- Air Shipping – Fast delivery of small batches may rely heavily on costly air freight.
- Inventory Buffer – Holding buffer stock has carrying cost implications.
- Alternate Sourcing – Custom expediting for components could require paying a markup.
- Quality Fallout – Faster pace increases chances of escapes impacting field failure rates.
The total cost impact could range from 25-60%+ over normal assembly. But faster time-to-market provides ROI in terms of revenues and competitiveness.
Fast PCB Assembly FAQs
Here are some common questions on rapid PCB assembly:
Q: What is the fastest assembly time possible?
A: Using overnight assembly, bare boards can be fully assembled and shipped in 24-48 hours in special cases. Normal best case is 3-5 days.
Q: Does faster assembly affect quality?
A: If underlying processes are robust, quality should not be impacted significantly. But reliability risks increase, so testing and inspections become more critical.
Q: How early should fast assembly planning start?
A: Engage assembly partners while still designing so they can start planning – especially for items like expedited sourcing of long lead components.
Q: What volumes can rapid assembly support?
A: Prototype builds can be done in hours. For production, fast-turn services support up to ~500 boards, beyond which standard leas times apply.
Q: Is fast assembly more expensive?
A: Yes, expedited delivery carries a premium of 25-100% typically over normal costs due to additional shifts, air freight etc.
Q: Does fast assembly require excess inventory?
A: Not necessarily – just more agile supply chain and assembly scheduling. But having buffer stock is recommended when launching new products.
Conclusion
Fast PCB assembly is becoming critical for hardware companies to deliver products rapidly and seize market opportunities. Quick-turn prototype builds along with streamlined low-volume and mass production are essential across the product life cycle. While traditional contract manufacturing alone cannot provide such accelerated timescales, the strategies above leverage specialized assembly services, agile supply chain and capacity planning to slash lead times. The result is dramatically faster time-to-market, outweighing the higher costs involved.
0 Comments