Introduction to Flex PCB
Flexible printed circuit boards, also known as flex PCBs, have revolutionized the electronics industry by offering a versatile and durable solution for connecting electronic components. Unlike traditional rigid PCBs, flex PCBs are made from flexible materials that allow them to bend and conform to various shapes and sizes. This unique property makes them ideal for applications where space is limited, or where the device needs to withstand repeated flexing and bending.
What is a Flex PCB?
A flex PCB is a type of printed circuit board that is made from flexible materials, such as polyimide or polyester. These materials are laminated together with copper traces and other conductive materials to create a circuit that can be bent and flexed without breaking or losing its electrical properties. Flex PCBs can be single-sided, double-sided, or multi-layered, depending on the complexity of the circuit and the number of components that need to be connected.
Advantages of Using Flex PCBs
Flex PCBs offer several advantages over traditional rigid PCBs, including:
-
Flexibility: Flex PCBs can be bent and flexed to fit into tight spaces or to conform to the shape of the device. This makes them ideal for applications where space is limited, such as in wearable devices or in aerospace and military equipment.
-
Durability: Flex PCBs are more durable than rigid PCBs because they can withstand repeated flexing and bending without breaking or losing their electrical properties. This makes them ideal for applications where the device needs to be moved or handled frequently, such as in medical devices or in automotive electronics.
-
Weight Reduction: Flex PCBs are lighter than rigid PCBs because they use less material and have a thinner profile. This can help to reduce the overall weight of the device, which is important in applications where weight is a critical factor, such as in aerospace and military equipment.
-
Improved Signal Integrity: Flex PCBs can improve signal integrity by reducing the distance between components and minimizing the number of connectors and solder joints. This can help to reduce noise and interference, which is important in high-speed applications such as in telecommunications and data processing.
-
Cost Savings: Flex PCBs can help to reduce costs by eliminating the need for connectors and cables, and by simplifying the assembly process. This can help to reduce the overall cost of the device and improve its reliability.
How Flex PCBs Can Extend the Life of Electronic Devices
Flex PCBs can help to extend the life of electronic devices in several ways, including:
Reducing Mechanical Stress
One of the main advantages of flex PCBs is that they can reduce mechanical stress on the components and connections in the device. Traditional rigid PCBs are prone to cracking and breaking when subjected to repeated flexing and bending, which can cause the components to become disconnected or damaged. Flex PCBs, on the other hand, are designed to withstand repeated flexing and bending without breaking or losing their electrical properties. This can help to reduce the risk of damage to the components and extend the life of the device.
Improving Thermal Management
Flex PCBs can also help to improve thermal management in electronic devices by allowing for better heat dissipation. Traditional rigid PCBs can trap heat between the layers of the board, which can cause the components to overheat and fail prematurely. Flex PCBs, on the other hand, can be designed with thinner layers and more open areas, which allows for better airflow and heat dissipation. This can help to keep the components cooler and extend their lifespan.
Enabling More Compact Designs
Flex PCBs can also enable more compact designs in electronic devices, which can help to reduce the overall size and weight of the device. Traditional rigid PCBs require more space for connectors and cables, which can add bulk and weight to the device. Flex PCBs, on the other hand, can be designed to fit into tight spaces and conform to the shape of the device, which can help to reduce the overall size and weight. This can be particularly important in applications where size and weight are critical factors, such as in wearable devices or in aerospace and military equipment.
Reducing the Number of Connectors and Solder Joints
Flex PCBs can also help to reduce the number of connectors and solder joints in electronic devices, which can improve reliability and extend the life of the device. Traditional rigid PCBs require more connectors and solder joints to connect the components, which can be a source of failure and can reduce the reliability of the device. Flex PCBs, on the other hand, can be designed with fewer connectors and solder joints, which can help to reduce the risk of failure and extend the life of the device.
Applications of Flex PCBs
Flex PCBs are used in a wide range of applications, including:
Wearable Devices
Flex PCBs are particularly well-suited for use in wearable devices, such as smartwatches, fitness trackers, and medical devices. These devices need to be compact, lightweight, and durable, and flex PCBs can help to meet all of these requirements. Flex PCBs can be designed to fit into the small spaces available in these devices, and can withstand the repeated flexing and bending that occurs during use.
Automotive Electronics
Flex PCBs are also used in automotive electronics, such as in dashboard displays, infotainment systems, and safety systems. These applications require PCBs that can withstand the harsh environmental conditions found in vehicles, such as extreme temperatures, vibration, and moisture. Flex PCBs can be designed to meet these requirements, and can help to improve the reliability and durability of automotive electronics.
Aerospace and Military Equipment
Flex PCBs are also used in aerospace and military equipment, such as in avionics systems, communication devices, and weapons systems. These applications require PCBs that can withstand extreme environmental conditions, such as high altitudes, extreme temperatures, and high levels of vibration and shock. Flex PCBs can be designed to meet these requirements, and can help to improve the reliability and durability of aerospace and military equipment.
Medical Devices
Flex PCBs are also used in medical devices, such as in implantable devices, diagnostic equipment, and surgical tools. These applications require PCBs that are biocompatible, reliable, and durable, and flex PCBs can help to meet all of these requirements. Flex PCBs can be designed to fit into the small spaces available in these devices, and can withstand the repeated flexing and bending that occurs during use.
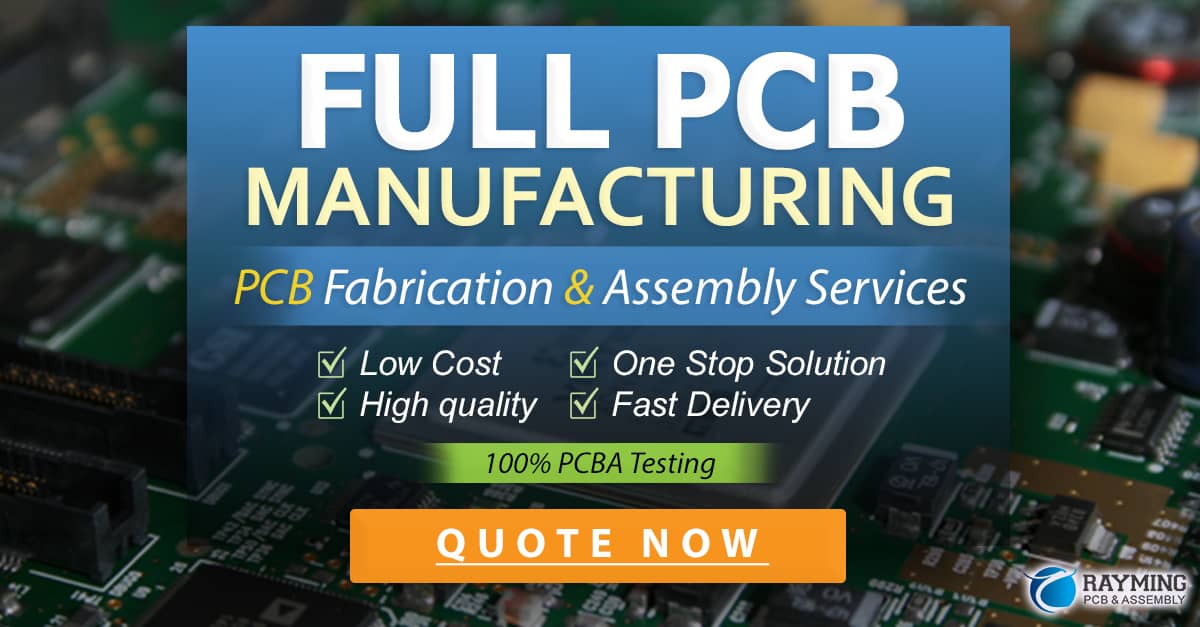
Designing Flex PCBs for Long Life
Designing flex PCBs for long life requires careful consideration of several factors, including:
Material Selection
The choice of materials used in the construction of a flex PCB can have a significant impact on its durability and lifespan. Polyimide is a common choice for flex PCBs because of its high temperature resistance, chemical stability, and mechanical strength. Other materials, such as polyester and PET, may be used in applications where cost is a primary concern, but these materials may not offer the same level of durability and reliability as polyimide.
Copper Thickness
The thickness of the copper traces used in a flex PCB can also impact its durability and lifespan. Thicker copper traces can help to improve the mechanical strength of the PCB and reduce the risk of damage from repeated flexing and bending. However, thicker copper traces can also increase the overall thickness and stiffness of the PCB, which may not be desirable in some applications.
Coverlay Material
The coverlay material used in a flex PCB can also impact its durability and lifespan. Coverlay is a protective layer that is applied over the copper traces to insulate and protect them from damage. The choice of coverlay material can impact the flexibility and durability of the PCB, as well as its resistance to chemicals and moisture.
Flexing Requirements
The flexing requirements of the application should also be carefully considered when designing a flex PCB for long life. The number of flex cycles, the degree of flexing, and the environmental conditions that the PCB will be subjected to can all impact its durability and lifespan. Designers should choose materials and design features that can withstand the expected flexing requirements of the application.
Manufacturing Flex PCBs for Long Life
Manufacturing flex PCBs for long life requires careful attention to several factors, including:
Lamination Process
The lamination process used to bond the layers of the flex PCB together can impact its durability and lifespan. The lamination process should be carefully controlled to ensure that the layers are properly bonded together and that there are no voids or delaminations that could weaken the PCB over time.
Etching Process
The etching process used to create the copper traces on the flex PCB can also impact its durability and lifespan. The etching process should be carefully controlled to ensure that the copper traces are properly formed and that there are no defects or irregularities that could weaken the PCB over time.
Inspection and Testing
Careful inspection and testing of the flex PCB during the manufacturing process can help to identify and correct any defects or issues that could impact its durability and lifespan. Visual inspection, electrical testing, and mechanical testing can all be used to ensure that the PCB meets the required specifications and is free from defects.
FAQs
- Q: How long do flex PCBs typically last compared to rigid PCBs?
A: Flex PCBs can last significantly longer than rigid PCBs, depending on the specific application and design. In general, flex PCBs are more durable and can withstand more flexing and bending than rigid PCBs, which can help to extend their lifespan.
- Q: What are the most common causes of failure in flex PCBs?
A: The most common causes of failure in flex PCBs include mechanical stress, thermal stress, and chemical exposure. Mechanical stress can cause the copper traces to crack or break, while thermal stress can cause the materials to degrade over time. Chemical exposure can also cause the materials to degrade or become brittle, which can lead to failure.
- Q: Can flex PCBs be repaired if they become damaged?
A: In some cases, flex PCBs can be repaired if they become damaged. However, the specific repair method will depend on the type and extent of the damage. In general, it is often more cost-effective to replace a damaged flex PCB than to attempt to repair it.
- Q: How can I tell if a flex PCB is nearing the end of its lifespan?
A: There are several signs that a flex PCB may be nearing the end of its lifespan, including visible cracks or damage to the copper traces, increased resistance or signal loss, and intermittent or complete failure of the device. Regular inspection and testing can help to identify these signs before they lead to complete failure.
- Q: Are there any special handling or storage requirements for flex PCBs to extend their lifespan?
A: Flex PCBs should be handled and stored carefully to avoid damage and extend their lifespan. They should be stored in a cool, dry place away from direct sunlight and extreme temperatures. They should also be handled carefully to avoid excessive bending or flexing, and should be protected from chemical exposure and moisture.
Conclusion
Flex PCBs offer a versatile and durable solution for connecting electronic components in a wide range of applications. By reducing mechanical stress, improving thermal management, enabling more compact designs, and reducing the number of connectors and solder joints, flex PCBs can help to extend the life of electronic devices and improve their reliability.
When designing and manufacturing flex PCBs for long life, careful consideration must be given to material selection, copper thickness, coverlay material, flexing requirements, lamination process, etching process, and inspection and testing. By following best practices in these areas, designers and manufacturers can create flex PCBs that are optimized for durability and reliability in even the most demanding applications.
As technology continues to advance and electronic devices become increasingly complex and sophisticated, the use of flex PCBs is likely to become even more widespread. By understanding the advantages and applications of flex PCBs, and by following best practices in their design and manufacture, engineers and manufacturers can create electronic devices that are more reliable, durable, and long-lasting than ever before.
0 Comments