What is PCB Soldering?
PCB soldering is the process of joining electronic components to a printed circuit board using a molten metal alloy called solder. The solder forms a strong electrical and mechanical bond between the component leads and the PCB pads, allowing current to flow through the circuit.
Types of Soldering
There are two main types of soldering used in PCB Assembly:
-
Through-hole soldering: This method involves inserting component leads through holes in the PCB and soldering them to pads on the opposite side of the board.
-
Surface-mount soldering: This method involves soldering components directly onto pads on the surface of the PCB, without using holes.
Tools and Materials for PCB Soldering
To get started with PCB soldering, you’ll need the following tools and materials:
Soldering Iron
A soldering iron is the most essential tool for PCB soldering. It heats up the solder and allows you to melt it onto the component leads and PCB pads. When choosing a soldering iron, consider the following factors:
- Wattage: A higher wattage iron heats up faster and maintains its temperature better, but can also damage components if not used carefully.
- Temperature control: Some soldering irons have adjustable temperature controls, which can be useful for working with different types of solder and components.
- Tip size and shape: Choose a tip that matches the size of the components and pads you’ll be soldering.
Solder
Solder is a metal alloy that melts at a relatively low temperature and forms a strong bond between components and PCB pads. The most common types of solder used in PCB assembly are:
- Lead-based solder: This type of solder contains lead and tin, and has a lower melting point than lead-free solder. However, it is being phased out due to environmental and health concerns.
- Lead-free solder: This type of solder contains tin, silver, and copper, and has a higher melting point than lead-based solder. It is becoming more widely used as regulations restrict the use of lead in electronics.
When choosing solder, also consider the diameter of the wire. A thinner wire is easier to work with for small components, while a thicker wire can be used for larger components and connections.
Soldering Flux
Flux is a chemical compound that helps the solder flow and bond to the components and PCB pads. It also helps to remove oxides and other contaminants from the surfaces being soldered. There are two main types of flux:
- Rosin flux: This type of flux is made from pine resin and is available in liquid, paste, or pen form. It is the most common type of flux used in PCB soldering.
- Water-soluble flux: This type of flux is designed to be easily cleaned off the PCB after soldering, using water or a mild solvent. It is often used in industrial PCB assembly.
Other Tools and Materials
In addition to a soldering iron, solder, and flux, you may also need the following tools and materials for PCB soldering:
- Solder wick or Desoldering Braid: This is a braided copper wire used to remove excess solder from joints.
- Solder sucker or desoldering pump: This is a spring-loaded tool used to suck up molten solder from a joint.
- Tweezers: Used for picking up and positioning small components on the PCB.
- Wire cutters: Used for trimming component leads after soldering.
- Isopropyl alcohol and cotton swabs: Used for cleaning the PCB before and after soldering.
- Safety glasses and ventilation: Always wear safety glasses to protect your eyes from solder splashes, and work in a well-ventilated area to avoid inhaling fumes.
PCB Soldering Techniques
Now that you have your tools and materials, let’s look at some basic PCB soldering techniques.
Through-Hole Soldering
- Insert the component leads through the holes in the PCB, making sure they are straight and seated properly.
- Bend the leads slightly outward to hold the component in place.
- Apply a small amount of solder to the tip of the iron and touch it to the pad and lead simultaneously. The solder should flow evenly around the joint.
- Remove the iron and let the joint cool for a few seconds.
- Trim the excess lead with wire cutters.
Surface-Mount Soldering
- Apply a small amount of solder paste to the pads on the PCB using a syringe or stencil.
- Place the component onto the pads, making sure it is aligned properly.
- Heat the joint with the soldering iron until the solder melts and flows around the component leads.
- Remove the iron and let the joint cool for a few seconds.
Desoldering
If you make a mistake or need to remove a component, you can use desoldering tools to remove the solder from the joint. Here’s how:
- Apply some flux to the joint to help the solder melt more easily.
- Heat the joint with the soldering iron until the solder melts.
- Use a solder sucker or desoldering braid to remove the molten solder from the joint.
- Repeat until all the solder is removed and the component can be lifted off the PCB.
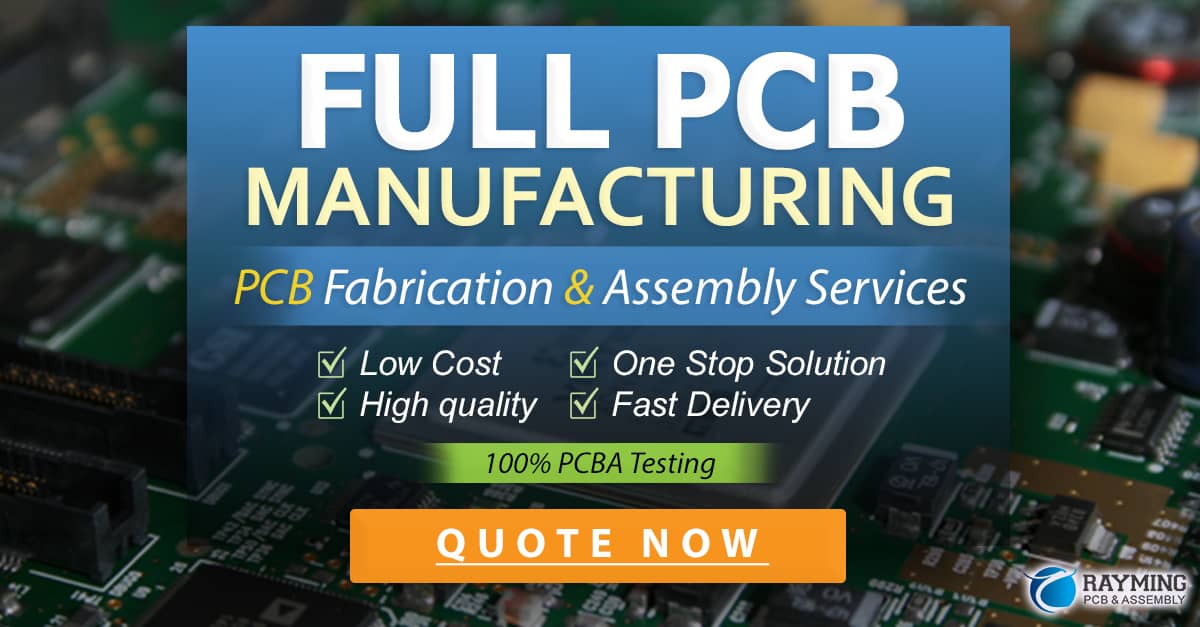
Common PCB Soldering Problems and Solutions
Even with the right tools and techniques, PCB soldering can sometimes go wrong. Here are some common problems and solutions:
Cold Joints
A cold joint occurs when the solder doesn’t melt completely or doesn’t bond properly to the component lead or PCB pad. This can happen if the iron is too cold, the joint is dirty or oxidized, or the solder is old or contaminated. To fix a cold joint:
- Apply some flux to the joint and reheat it with the iron until the solder melts completely.
- If the joint still looks dull or lumpy, add a little fresh solder and reheat until it flows smoothly.
Bridging
Bridging occurs when solder accidentally connects two adjacent pads or leads, creating a short circuit. To fix bridging:
- Use a solder sucker or desoldering braid to remove the excess solder from the bridge.
- If the bridge is small, you may be able to break it with a sharp tool like a scalpel or tweezers.
Overheating
Overheating can damage components or lift pads off the PCB. To prevent overheating:
- Use the lowest temperature setting on your iron that still allows the solder to melt quickly.
- Apply heat to the joint for the shortest time possible, and let it cool before applying heat again.
- Use a heat sink or thermal insulation to protect sensitive components from excess heat.
Insufficient Wetting
Insufficient wetting occurs when the solder doesn’t flow properly onto the component lead or PCB pad, leaving gaps or voids in the joint. This can happen if the surfaces are dirty, oxidized, or not heated enough. To improve wetting:
- Clean the surfaces thoroughly with isopropyl alcohol before soldering.
- Apply a small amount of flux to the joint to help the solder flow.
- Make sure the iron is hot enough to melt the solder quickly and completely.
PCB Soldering Safety
PCB soldering involves high temperatures and potentially hazardous chemicals, so it’s important to follow some basic safety guidelines:
- Always wear safety glasses to protect your eyes from solder splashes and fumes.
- Work in a well-ventilated area or use a fume extractor to avoid inhaling solder fumes.
- Avoid touching the hot tip of the soldering iron or the molten solder.
- Keep flammable materials away from the soldering area, and never leave a hot iron unattended.
- Wash your hands thoroughly after soldering, especially if you’re using lead-based solder.
PCB Soldering Tips and Tricks
Here are some additional tips and tricks to help you achieve better results with PCB soldering:
- Use a soldering iron stand to hold the iron safely when not in use.
- Tin the tip of the iron with a small amount of solder before use to improve heat transfer and prevent oxidation.
- Apply heat to the pad and lead simultaneously, not just the solder.
- Use a magnifying glass or microscope to inspect joints for defects or voids.
- Practice on scrap boards or kits before soldering your final project.
FAQ
What type of solder should I use for PCB soldering?
For most PCB soldering applications, a lead-free solder with a diameter of 0.5-0.8mm is recommended. Look for solder with a composition of Sn96.5/Ag3.0/Cu0.5, which has a melting point of around 217°C.
How hot should my soldering iron be for PCB soldering?
The ideal temperature for PCB soldering depends on the type of solder and components you’re using, but a general range of 300-400°C is suitable for most applications. Start with a lower temperature and increase it gradually if needed.
Can I use a regular household iron for PCB soldering?
No, a regular household iron is not suitable for PCB soldering. Soldering irons are specifically designed to reach and maintain high temperatures, and have a pointed tip for precise application of heat.
How do I clean my PCB after soldering?
To clean your PCB after soldering, use a soft brush or cotton swab dipped in isopropyl alcohol to remove any flux residue or debris. Avoid using water or harsh solvents, which can damage the board or components.
What should I do if I accidentally damage a component or pad while soldering?
If you damage a component or pad while soldering, first assess the extent of the damage. If the component is burned or cracked, it will need to be replaced. If a pad is lifted or damaged, you may be able to repair it with some copper tape or conductive epoxy. In either case, it’s best to consult with an experienced technician or engineer before attempting any repairs.
Conclusion
PCB soldering is a valuable skill for anyone working with electronics, from hobbyists to professionals. By understanding the tools, techniques, and safety considerations involved, you can create reliable and long-lasting circuits for your projects. Remember to practice regularly, start with simple boards and components, and don’t be afraid to ask for help or guidance when needed. With patience and persistence, anyone can master the art of PCB soldering.
Soldering Iron Temperature | Solder Type | Solder Diameter |
---|---|---|
300-400°C | Lead-free (Sn96.5/Ag3.0/Cu0.5) | 0.5-0.8mm |
By following the tips and techniques outlined in this guide, you’ll be well on your way to creating professional-quality PCBs for all your electronic projects. Happy soldering!
0 Comments