What are EV Charger PCBAs?
EV Charger PCBAs are printed circuit board assemblies specifically designed for use in electric vehicle charging systems. These PCBAs contain various electronic components, such as microcontrollers, power converters, and communication interfaces, which work together to enable the safe and efficient transfer of electricity from the power grid to the EV’s battery.
The Importance of EV Charger PCBAs
EV Charger PCBAs are essential components in the EV charging ecosystem. They perform several critical functions, including:
-
Power Conversion: EV Charger PCBAs convert the alternating current (AC) from the power grid into direct current (DC) that can be used to charge the EV’s battery.
-
Communication: PCBAs facilitate communication between the EV and the charging station, ensuring that the charging process is properly initiated, monitored, and terminated.
-
Safety: EV Charger PCBAs incorporate various safety features, such as overcurrent protection, overvoltage protection, and ground fault detection, to prevent electrical hazards and protect both the EV and the charging infrastructure.
-
Efficiency: Advanced EV Charger PCBAs employ techniques like power factor correction (PFC) and resonant switching to maximize the efficiency of the charging process, reducing energy losses and minimizing the impact on the power grid.
Key Components of EV Charger PCBAs
EV Charger PCBAs consist of several key components that work together to ensure the safe and efficient charging of electric vehicles:
-
Microcontrollers: These programmable integrated circuits control the overall operation of the EV Charger PCBA, managing communication, monitoring system status, and implementing safety protocols.
-
Power Converters: Power converters, such as rectifiers and DC-DC converters, are responsible for converting the AC input from the power grid into the appropriate DC voltage and current levels required for charging the EV’s battery.
-
Communication Interfaces: EV Charger PCBAs include communication interfaces, such as CAN (Controller Area Network) or Ethernet, which enable the exchange of data between the EV and the charging station, facilitating the initiation, monitoring, and termination of the charging process.
-
Safety Components: Various safety components, such as fuses, surge protectors, and ground fault circuit interrupters (GFCIs), are incorporated into EV Charger PCBAs to protect against electrical hazards and ensure the safe operation of the charging system.
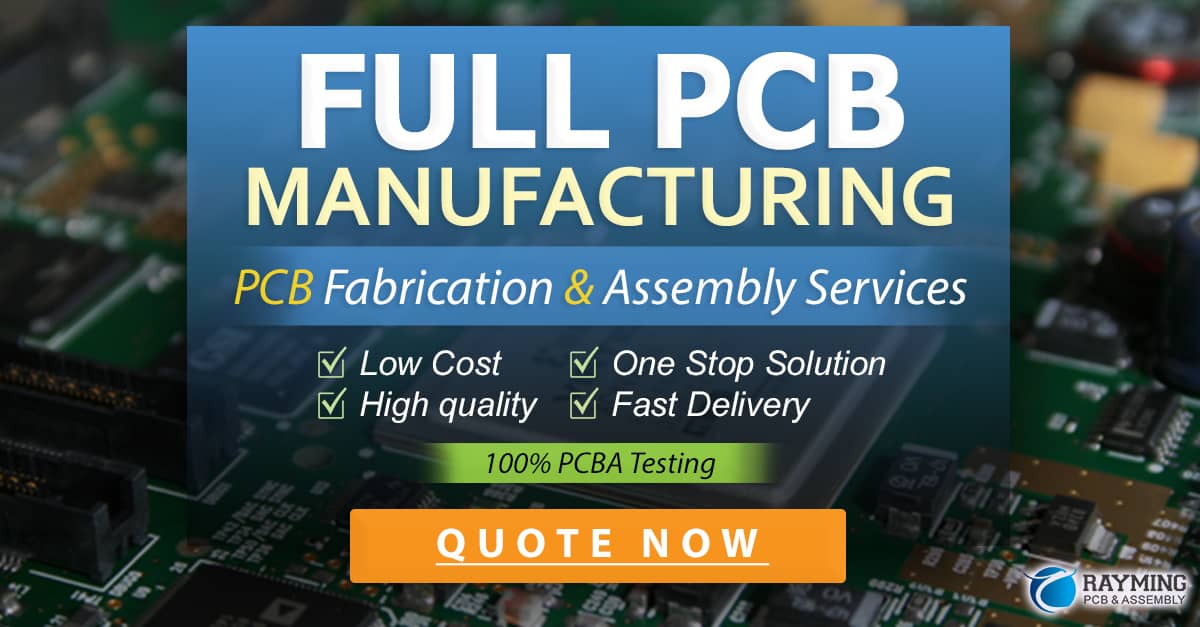
Advancements in EV Charger PCBA Technology
As the EV industry continues to evolve, so do the technologies used in EV Charger PCBAs. Some of the latest advancements include:
-
Bidirectional Charging: Bidirectional EV Charger PCBAs allow for the flow of electricity both from the power grid to the EV and from the EV back to the grid. This technology, also known as vehicle-to-grid (V2G), enables EVs to serve as energy storage devices, helping to balance the load on the power grid during peak demand periods.
-
Wireless Charging: Wireless EV Charger PCBAs utilize electromagnetic induction to transfer power from the charging station to the EV without the need for a physical connection. This technology offers increased convenience and eliminates the need for cumbersome charging cables.
-
Smart Charging: Smart EV Charger PCBAs incorporate advanced algorithms and communication protocols that enable the optimization of the charging process based on factors such as the EV’s battery state, the available power from the grid, and the user’s charging preferences. This technology helps to minimize the impact of EV charging on the power grid and reduces the overall cost of charging for EV owners.
The Role of EV Charger PCBAs in the Future of Transportation
As the world transitions towards a more sustainable future, electric vehicles are expected to play an increasingly important role in the transportation sector. EV Charger PCBAs will be critical in supporting the widespread adoption of EVs by ensuring the availability of safe, efficient, and reliable charging infrastructure.
Some of the ways in which EV Charger PCBAs will contribute to the future of transportation include:
-
Enabling Fast Charging: Advanced EV Charger PCBAs will support higher power levels, enabling faster charging times for EVs. This will help to overcome one of the main barriers to EV adoption, as users will be able to charge their vehicles quickly and conveniently, similar to refueling a traditional gasoline-powered vehicle.
-
Supporting the Development of Charging Networks: As the demand for EVs grows, so will the need for extensive charging networks. EV Charger PCBAs will be essential in building out these networks, ensuring that charging stations are reliable, efficient, and compatible with a wide range of EVs.
-
Facilitating the Integration of Renewable Energy: EV Charger PCBAs that support bidirectional charging and smart charging technologies will play a crucial role in facilitating the integration of renewable energy sources, such as solar and wind power, into the power grid. By allowing EVs to store excess renewable energy and feed it back into the grid when needed, EV Charger PCBAs will help to balance the intermittent nature of renewable energy generation and reduce the overall carbon footprint of the transportation sector.
Challenges and Opportunities
While EV Charger PCBAs offer numerous benefits, there are also some challenges and opportunities associated with their development and deployment:
-
Standardization: Ensuring compatibility between different EV models and charging stations requires the development and adoption of standardized communication protocols and connector types. Industry collaboration and government regulations will be essential in driving the standardization of EV Charger PCBA technologies.
-
Cost Reduction: As the demand for EV Charger PCBAs grows, there will be opportunities to reduce their manufacturing costs through economies of scale and technological advancements. Lower costs will help to accelerate the adoption of EVs by making charging infrastructure more affordable and accessible.
-
Reliability and Durability: EV Charger PCBAs must be designed to withstand the harsh environmental conditions and frequent use associated with EV charging. Manufacturers must focus on developing PCBAs with high reliability and durability to ensure the long-term performance and safety of charging infrastructure.
-
Cybersecurity: As EV Charger PCBAs become increasingly connected and smart, ensuring the cybersecurity of charging infrastructure will be critical. Manufacturers must implement robust security measures to protect against potential cyber threats and ensure the integrity of the charging process.
FAQs
-
Q: What is the difference between Level 1, Level 2, and Level 3 EV charging?
A: Level 1 charging uses a standard 120V household outlet and is the slowest charging method. Level 2 charging uses a 240V outlet, similar to those used for large appliances, and offers faster charging times. Level 3, also known as DC fast charging, uses high-voltage direct current to charge an EV’s battery rapidly, typically providing an 80% charge in 30-60 minutes. -
Q: Can EV Charger PCBAs be used with all types of electric vehicles?
A: EV Charger PCBAs are designed to be compatible with a wide range of electric vehicles. However, it is essential to ensure that the PCBA’s communication protocols and connector types are compatible with the specific EV model being charged. -
Q: How do EV Charger PCBAs ensure the safety of the charging process?
A: EV Charger PCBAs incorporate various safety features, such as overcurrent protection, overvoltage protection, and ground fault detection, to prevent electrical hazards. These features protect both the EV and the charging infrastructure from potential damage or malfunction. -
Q: What role do EV Charger PCBAs play in the adoption of renewable energy?
A: EV Charger PCBAs that support bidirectional charging and smart charging technologies can help to facilitate the integration of renewable energy sources into the power grid. By allowing EVs to store excess renewable energy and feed it back into the grid when needed, EV Charger PCBAs can help to balance the intermittent nature of renewable energy generation. -
Q: How can the cost of EV Charger PCBAs be reduced?
A: As the demand for EV Charger PCBAs grows, manufacturers can reduce costs through economies of scale and technological advancements. Standardization of communication protocols and connector types can also help to lower costs by increasing compatibility and reducing the need for custom solutions.
Conclusion
EV Charger PCB Assemblies are critical components in the growing ecosystem of electric vehicle charging infrastructure. By enabling the safe, efficient, and reliable transfer of electricity from the power grid to EVs, these PCBAs play a vital role in supporting the widespread adoption of electric vehicles and the transition towards a more sustainable future.
As the demand for EVs continues to grow, so will the need for advanced EV Charger PCBA technologies. Manufacturers and industry stakeholders must collaborate to address challenges related to standardization, cost reduction, reliability, and cybersecurity while capitalizing on opportunities to integrate renewable energy and develop extensive charging networks.
By investing in the development and deployment of cutting-edge EV Charger PCBAs, we can accelerate the shift towards clean, efficient, and sustainable transportation, ultimately contributing to a greener and more environmentally friendly future.
Component | Function |
---|---|
Microcontrollers | Control the overall operation of the EV Charger PCBA, managing communication, monitoring system status, and implementing safety protocols. |
Power Converters | Convert the AC input from the power grid into the appropriate DC voltage and current levels required for charging the EV’s battery. |
Communication Interfaces | Enable the exchange of data between the EV and the charging station, facilitating the initiation, monitoring, and termination of the charging process. |
Safety Components | Protect against electrical hazards and ensure the safe operation of the charging system, including fuses, surge protectors, and ground fault circuit interrupters. |
0 Comments