What is ENIG-Black Pad?
ENIG-Black Pad (BPD), also known as “Black Pad Syndrome”, is a defect that can occur in printed circuit boards (PCBs) with an Electroless Nickel Immersion Gold (ENIG) surface finish. It is characterized by the formation of a thin, brittle layer of black nickel oxide or phosphorous compounds between the nickel and gold layers, leading to poor solderability and weak solder joint strength.
BPD has become an increasingly common issue in the PCB industry due to the widespread adoption of ENIG surface finishes, which offer several advantages such as excellent oxidation resistance, good shelf life, and compatibility with fine-pitch components. However, the occurrence of BPD can result in a high scrap rate, rework costs, and reliability issues, making it a significant concern for PCB manufacturers and assemblers.
Causes of ENIG-Black Pad
Several factors can contribute to the formation of BPD in ENIG-finished PCBs:
Improper ENIG process control
One of the primary causes of BPD is the lack of proper control over the ENIG plating process parameters. Some of the critical factors include:
-
Nickel bath composition: An imbalance in the nickel bath composition, such as high phosphorus content or the presence of contaminants, can lead to the formation of a brittle, phosphorous-rich layer at the nickel-gold interface.
-
Plating time and temperature: Excessive plating time or high bath temperature can result in the over-deposition of nickel, increasing the risk of BPD formation.
-
Rinsing and drying: Inadequate rinsing or drying between the nickel and gold plating steps can lead to the entrapment of contaminants, promoting BPD formation.
Substrate quality and preparation
The quality and preparation of the PCB substrate can also influence the occurrence of BPD:
-
Surface roughness: A rough or porous copper surface can lead to uneven nickel deposition and increased susceptibility to BPD formation.
-
Cleanliness: Contamination or residues on the copper surface, such as oils, oxides, or etching residues, can hinder proper nickel adhesion and promote BPD.
Exposure to harsh environments
Exposure of ENIG-finished PCBs to harsh environmental conditions, such as high humidity, elevated temperatures, or corrosive atmospheres, can accelerate the formation of BPD by promoting nickel oxidation or degradation of the nickel-gold interface.
Prevention and Mitigation Strategies
To minimize the occurrence of BPD in ENIG-finished PCBs, several prevention and mitigation strategies can be implemented:
Process optimization and control
Strict control and optimization of the ENIG plating process parameters are crucial for preventing BPD formation:
-
Nickel bath composition: Maintain the nickel bath composition within the recommended ranges, especially the phosphorus content (typically 6-9 wt%), and regularly monitor for contaminants.
-
Plating time and temperature: Optimize the nickel plating time and temperature to achieve the desired thickness without over-deposition. Typical nickel thickness ranges from 3-6 µm.
-
Rinsing and drying: Ensure thorough rinsing and drying between the nickel and gold plating steps to remove any contaminants or residual plating solutions.
Substrate preparation and quality control
Proper preparation and quality control of the PCB substrate can help reduce the risk of BPD:
-
Surface roughening: Employ suitable surface roughening techniques, such as micro-etching or oxide treatment, to improve nickel adhesion while maintaining a smooth, uniform surface.
-
Cleanliness: Implement strict cleaning and inspection procedures to ensure the copper surface is free from contaminants and oxides before ENIG plating.
Alternative surface finishes
In some cases, alternative surface finishes may be considered to mitigate the risk of BPD:
-
Immersion tin (ISn): ISn offers good solderability and is less prone to black pad formation compared to ENIG. However, it has a shorter shelf life and may not be suitable for fine-pitch components.
-
Organic Solderability Preservative (OSP): OSP is a cost-effective and BPD-free alternative, but it has limited shelf life and may not provide adequate oxidation resistance for some applications.
-
Electroless Palladium Immersion Gold (EPIG): EPIG is a promising alternative to ENIG, offering better solder joint reliability and resistance to black pad formation. However, it is more expensive and may have limited availability.
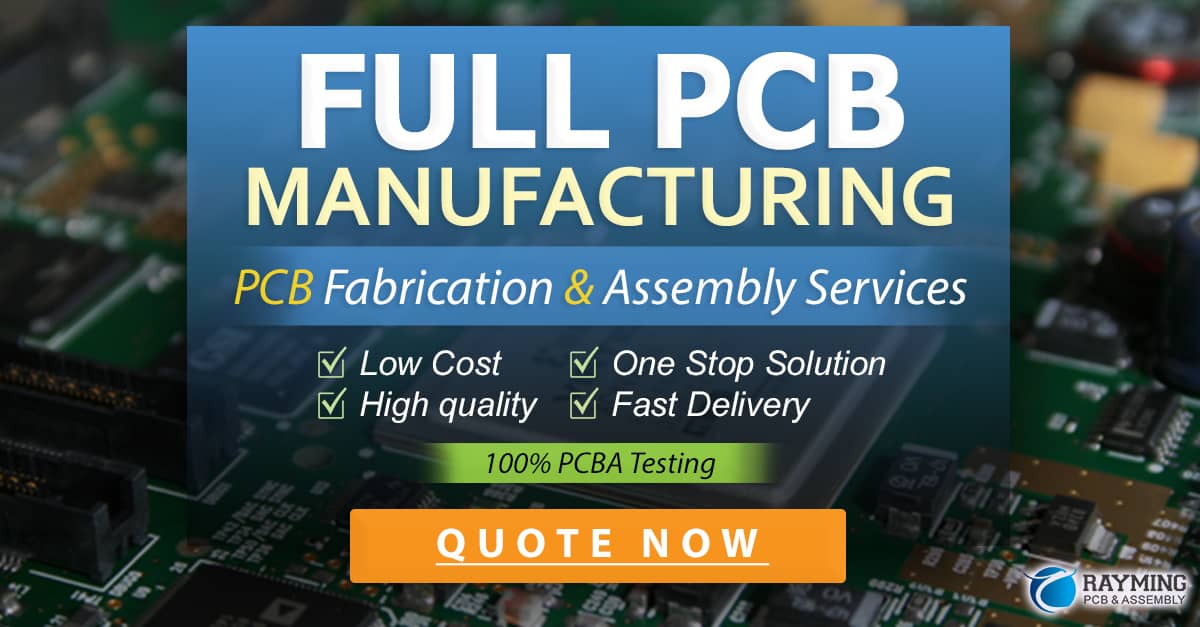
Inspection and Testing Methods
To detect and assess the severity of BPD in ENIG-finished PCBs, several inspection and testing methods can be employed:
Visual inspection
Visual examination of the ENIG surface under magnification can reveal the presence of black or discolored nickel, indicating potential BPD. However, this method is subjective and may not detect early-stage or localized BPD.
Cross-sectional analysis
Microsectioning and cross-sectional analysis of the ENIG-finished PCB can provide detailed information on the nickel-gold interface and the presence of any brittle or oxidized layers. This method is destructive and requires specialized sample preparation and microscopy techniques.
Solderability testing
Solderability testing, such as the wetting balance test or the dip-and-look method, can assess the solderability of the ENIG surface and indirectly indicate the presence of BPD. Poor solderability or non-wetting areas may suggest BPD formation.
Solder joint reliability testing
Mechanical testing of solder joints, such as shear or pull testing, can evaluate the strength and reliability of the solder connections on ENIG-finished PCBs. Weak or brittle solder joints may indicate the presence of BPD.
FAQ
1. What is the main cause of ENIG-Black Pad?
The main cause of ENIG-Black Pad is improper control of the ENIG plating process parameters, particularly the nickel bath composition, plating time, and temperature. Other contributing factors include substrate quality, surface preparation, and exposure to harsh environments.
2. How can I prevent ENIG-Black Pad in my PCBs?
To prevent ENIG-Black Pad, implement strict process control and optimization of the ENIG plating parameters, ensure proper substrate preparation and cleanliness, and consider alternative surface finishes if necessary.
3. What are the consequences of ENIG-Black Pad?
ENIG-Black Pad can lead to poor solderability, weak solder joint strength, and reduced reliability of the PCB assembly. This can result in a high scrap rate, rework costs, and potential field failures.
4. How can I detect ENIG-Black Pad in my PCBs?
ENIG-Black Pad can be detected through visual inspection, cross-sectional analysis, solderability testing, and solder joint reliability testing. A combination of these methods may be necessary to fully assess the presence and severity of BPD.
5. Are there any alternative surface finishes that can mitigate the risk of ENIG-Black Pad?
Yes, alternative surface finishes such as Immersion Tin (ISn), Organic Solderability Preservative (OSP), and Electroless Palladium Immersion Gold (EPIG) can be considered to mitigate the risk of ENIG-Black Pad. However, each alternative has its own advantages and limitations, and the choice depends on the specific application requirements and constraints.
0 Comments