Introduction to NPI Prototypes in Electronics Manufacturing Services (EMS)
New Product Introduction (NPI) is a critical process in the Electronics Manufacturing Services (EMS) industry. It involves the development and manufacturing of prototypes for new electronic products before they are released for mass production. The NPI process is essential for Original Equipment Manufacturers (OEMs) to ensure that their products meet the required quality standards and are free from defects.
Importance of NPI Prototypes in EMS
NPI prototypes play a crucial role in the success of new electronic products. They allow OEMs to test and validate their designs, identify potential issues, and make necessary adjustments before committing to full-scale production. By investing in a robust NPI prototyping process, OEMs can:
- Reduce time-to-market
- Minimize development costs
- Improve product quality and reliability
- Enhance customer satisfaction
The NPI Prototypes Checklist
To achieve zero defects in NPI prototypes, OEMs should follow a comprehensive checklist. This checklist covers all the essential aspects of the NPI process, from design and development to testing and validation.
1. Design and Development
1.1 Product Requirements and Specifications
- [ ] Define clear and detailed product requirements and specifications
- [ ] Ensure that all stakeholders (engineering, manufacturing, quality, etc.) are aligned on the requirements
1.2 Design for Manufacturability (DFM)
- [ ] Conduct a thorough DFM analysis to identify potential manufacturing challenges
- [ ] Optimize the design for ease of manufacturing and assembly
- [ ] Consider the capabilities and limitations of the EMS provider
1.3 Component Selection
- [ ] Select components that meet the product requirements and specifications
- [ ] Ensure that the selected components are readily available and have long-term supply stability
- [ ] Consider alternative components to mitigate the risk of obsolescence
1.4 Schematic and PCB Layout Design
- [ ] Develop a detailed schematic diagram that accurately represents the product’s electrical design
- [ ] Create a PCB layout that follows best practices for signal integrity, power integrity, and EMC
- [ ] Perform a design review with the EMS provider to identify any potential issues
2. Prototyping
2.1 Prototype Build
- [ ] Provide clear and complete build instructions to the EMS provider
- [ ] Ensure that all necessary components, materials, and equipment are available
- [ ] Monitor the prototype build process closely to identify any issues or deviations
2.2 Prototype Inspection and Testing
- [ ] Perform a visual inspection of the prototype to identify any obvious defects or issues
- [ ] Conduct functional testing to verify that the prototype meets the product requirements and specifications
- [ ] Perform environmental testing (thermal, vibration, humidity, etc.) to ensure product reliability
3. Validation and Verification
3.1 Design Validation
- [ ] Validate that the prototype meets all the product requirements and specifications
- [ ] Conduct a design review with all stakeholders to identify any necessary changes or improvements
3.2 Process Validation
- [ ] Validate that the manufacturing processes used to build the prototype are robust and repeatable
- [ ] Identify any process improvements that can be implemented for mass production
3.3 Compliance and Certification
- [ ] Ensure that the prototype meets all relevant industry standards and regulations
- [ ] Obtain necessary certifications (UL, CE, FCC, etc.) before releasing the product for mass production
4. Documentation and Communication
4.1 Documentation
- [ ] Create and maintain accurate and up-to-date documentation for the prototype, including:
- Bill of Materials (BOM)
- Assembly instructions
- Test procedures
- Quality control plans
4.2 Communication
- [ ] Establish clear and effective communication channels with the EMS provider
- [ ] Regularly review project status and address any issues or concerns promptly
- [ ] Involve all stakeholders in key decisions and milestones
Benefits of Following the NPI Prototypes Checklist
By following the NPI prototypes checklist, OEMs can realize several benefits, including:
- Reduced development time and costs
- Improved product quality and reliability
- Enhanced collaboration with EMS providers
- Faster time-to-market
- Increased customer satisfaction
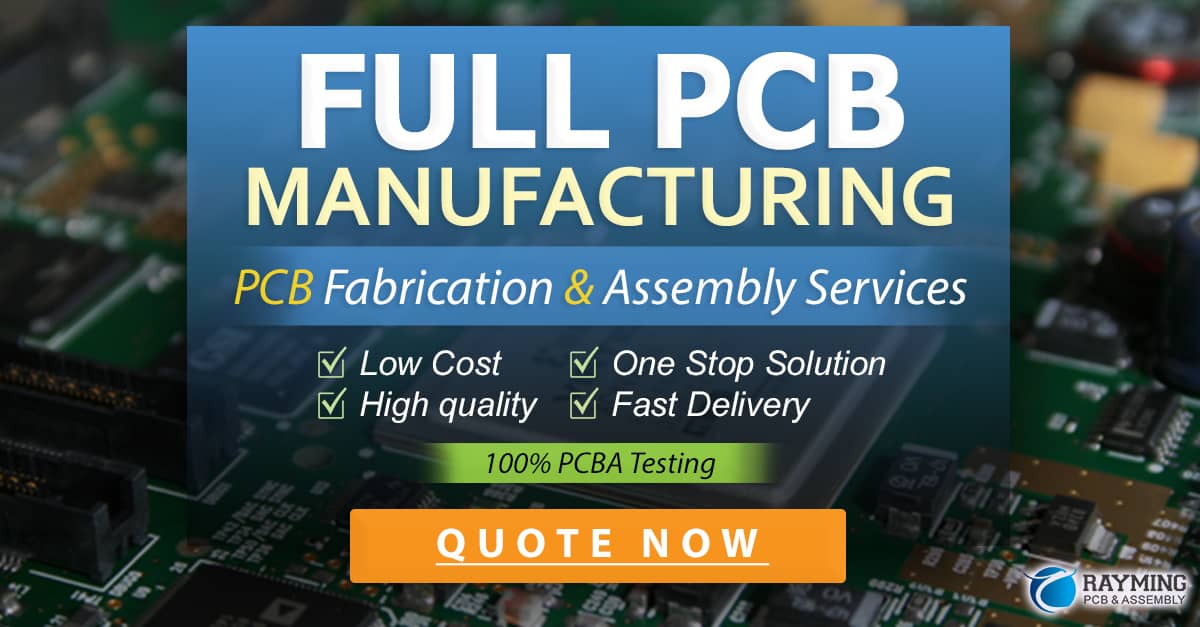
Common Pitfalls to Avoid in NPI Prototyping
To ensure a successful NPI prototyping process, OEMs should avoid the following common pitfalls:
- Incomplete or ambiguous product requirements and specifications
- Inadequate DFM analysis and design optimization
- Poor component selection and supply chain management
- Insufficient testing and validation
- Lack of communication and collaboration with EMS providers
Best Practices for Successful NPI Prototyping
To achieve the best results in NPI prototyping, OEMs should adopt the following best practices:
- Involve all stakeholders early in the process
- Prioritize Design for Manufacturability (DFM)
- Select reliable and experienced EMS partners
- Invest in comprehensive testing and validation
- Foster open and transparent communication with all stakeholders
FAQ
1. What is the difference between NPI prototyping and mass production?
NPI prototyping focuses on developing and validating a new product design before it is released for mass production. The main goal is to identify and address any issues or defects in the design, manufacturing processes, and supply chain. In contrast, mass production involves the large-scale manufacturing of a product that has already been validated and optimized through the NPI process.
2. How long does the NPI prototyping process typically take?
The duration of the NPI prototyping process can vary depending on the complexity of the product, the resources available, and the experience of the OEM and EMS provider. On average, the process can take anywhere from a few weeks to several months. However, by following the NPI prototypes checklist and adopting best practices, OEMs can streamline the process and reduce the overall development time.
3. What are the key factors to consider when selecting an EMS provider for NPI prototyping?
When selecting an EMS provider for NPI prototyping, OEMs should consider the following key factors:
- Experience and expertise in NPI prototyping
- Quality management systems and certifications
- Manufacturing capabilities and capacity
- Supply chain management and component sourcing
- Communication and collaboration processes
4. How can OEMs ensure effective communication with their EMS provider during the NPI prototyping process?
To ensure effective communication with their EMS provider, OEMs should:
- Establish clear and well-defined communication channels
- Schedule regular project status meetings and updates
- Use collaborative project management tools and platforms
- Encourage open and transparent communication at all levels
- Address any issues or concerns promptly and constructively
5. What are the most common causes of defects in NPI prototypes, and how can they be prevented?
The most common causes of defects in NPI prototypes include:
- Design errors and oversights
- Component quality and compatibility issues
- Manufacturing process errors and inconsistencies
- Inadequate testing and validation
To prevent these defects, OEMs should follow the NPI prototypes checklist, which includes:
- Thorough design reviews and DFM analysis
- Rigorous component selection and supply chain management
- Comprehensive testing and validation at all stages of the process
- Close collaboration and communication with EMS providers
By adhering to the checklist and best practices, OEMs can significantly reduce the risk of defects and ensure the success of their NPI prototyping efforts.
Conclusion
NPI prototyping is a critical process for the successful development and launch of new electronic products. By following a comprehensive NPI prototypes checklist, OEMs can achieve zero defects, reduce development time and costs, and improve product quality and reliability.
The key elements of the checklist include:
- Design and development
- Prototyping
- Validation and verification
- Documentation and communication
By adhering to best practices, avoiding common pitfalls, and fostering close collaboration with experienced EMS providers, OEMs can streamline their NPI prototyping process and bring innovative, high-quality products to market faster and more efficiently.
0 Comments