Introduction to PCB Manufacturing
Printed Circuit Boards (PCBs) are the backbone of modern electronics. They provide a platform for electronic components to be mounted and interconnected, enabling the creation of complex circuits and devices. In this comprehensive tutorial, we will guide you through the process of PCB manufacturing, from design to fabrication, making it easy for beginners to understand and follow.
What is a PCB?
A PCB is a flat, thin board made of insulating material, such as fiberglass or epoxy resin, with conductive copper traces printed on one or both sides. These traces connect various electronic components, such as resistors, capacitors, and integrated circuits (ICs), allowing them to work together as a complete electronic system.
Advantages of Using PCBs
PCBs offer several advantages over traditional point-to-point wiring:
- Compact size: PCBs allow for a more compact and organized layout of electronic components.
- Reliability: The use of PCBs reduces the risk of wiring errors and improves the overall reliability of the electronic device.
- Mass production: PCBs enable the mass production of electronic devices, reducing manufacturing costs and time.
- Improved performance: PCBs provide better signal integrity and reduce electromagnetic interference (EMI) compared to point-to-point wiring.
PCB Design Process
Before diving into the manufacturing process, it is essential to understand the PCB design process. This section will cover the key steps involved in designing a PCB.
Schematic Design
The first step in PCB design is creating a schematic diagram. A schematic is a graphical representation of the electronic circuit, showing the interconnections between components using standardized symbols. It serves as a blueprint for the PCB layout.
To create a schematic, you can use electronic design automation (EDA) software, such as:
- KiCad
- Eagle
- Altium Designer
- OrCAD
These software tools provide a user-friendly interface for designing schematics and often include extensive libraries of component symbols.
PCB Layout Design
Once the schematic is complete, the next step is to create the PCB layout. The layout design involves arranging the components on the board and routing the copper traces to connect them according to the schematic.
When designing the PCB layout, consider the following factors:
- Component placement: Arrange components in a logical and efficient manner, taking into account factors such as signal integrity, heat dissipation, and mechanical constraints.
- Trace routing: Route the copper traces to connect the components while minimizing the trace length and avoiding sharp angles. Ensure that the traces are of appropriate width to handle the required current.
- Ground planes: Include ground planes to provide a low-impedance return path for signals and to reduce EMI.
- Vias: Use vias to connect traces on different layers of the PCB.
- Design rules: Adhere to the design rules specified by the PCB manufacturer, such as minimum trace width, clearance between traces, and hole sizes.
EDA software tools, like those mentioned earlier, also provide PCB layout design capabilities. They often include features such as auto-routing, design rule checking (DRC), and 3D visualization to assist in creating an optimal PCB layout.
Gerber File Generation
After completing the PCB layout design, the next step is to generate Gerber files. Gerber files are industry-standard file formats used to describe the PCB layout for manufacturing. They contain information about the copper layers, solder mask, silkscreen, and drill holes.
Most EDA software tools can generate Gerber files automatically. It is essential to review the generated files to ensure that they accurately represent the intended PCB design.
PCB Manufacturing Process
With the PCB design complete and Gerber files generated, we can now move on to the manufacturing process. This section will provide an overview of the key steps involved in PCB manufacturing.
PCB Fabrication
PCB fabrication involves the following steps:
- Material preparation: The PCB substrate, typically FR-4 (a type of fiberglass), is cut to the required size.
- Copper lamination: Copper foil is laminated onto one or both sides of the substrate using heat and pressure.
- Drilling: Holes are drilled through the PCB to accommodate through-hole components and vias.
- Copper patterning: The desired copper pattern is transferred onto the PCB using a photolithography process. This involves applying a photoresist layer, exposing it to UV light through a photomask, and then developing and etching the exposed copper.
- Solder mask application: A solder mask, typically green in color, is applied to the PCB to protect the copper traces from oxidation and to prevent solder bridges during the assembly process.
- Silkscreen printing: A silkscreen layer, usually white, is printed on the PCB to provide component labels, logos, and other identifying information.
- Surface finish: A surface finish, such as HASL (Hot Air Solder Leveling) or ENIG (Electroless Nickel Immersion Gold), is applied to the exposed copper pads to improve solderability and protect against oxidation.
PCB Assembly
Once the PCB fabrication is complete, the next step is to assemble the electronic components onto the board. PCB assembly can be done manually for low-volume production or prototyping, but for higher volumes, automated assembly methods are used.
The two main types of PCB assembly are:
- Through-hole assembly: Components with long leads are inserted through the holes in the PCB and soldered onto the opposite side.
- Surface mount assembly: Components with small, flat leads (SMDs) are placed directly onto the solder pads on the PCB surface and soldered using a reflow oven.
Automated PCB assembly involves the following steps:
- Solder paste application: Solder paste, a mixture of tiny solder particles and flux, is applied to the solder pads using a stencil or syringe.
- Component placement: A pick-and-place machine automatically picks up the SMD components from reels or trays and places them onto the solder pads with high precision.
- Reflow soldering: The PCB is passed through a reflow oven, which heats the board to a specific temperature profile, melting the solder paste and creating a permanent connection between the components and the PCB.
- Inspection and testing: The assembled PCB undergoes visual inspection and electrical testing to ensure proper functionality and quality.
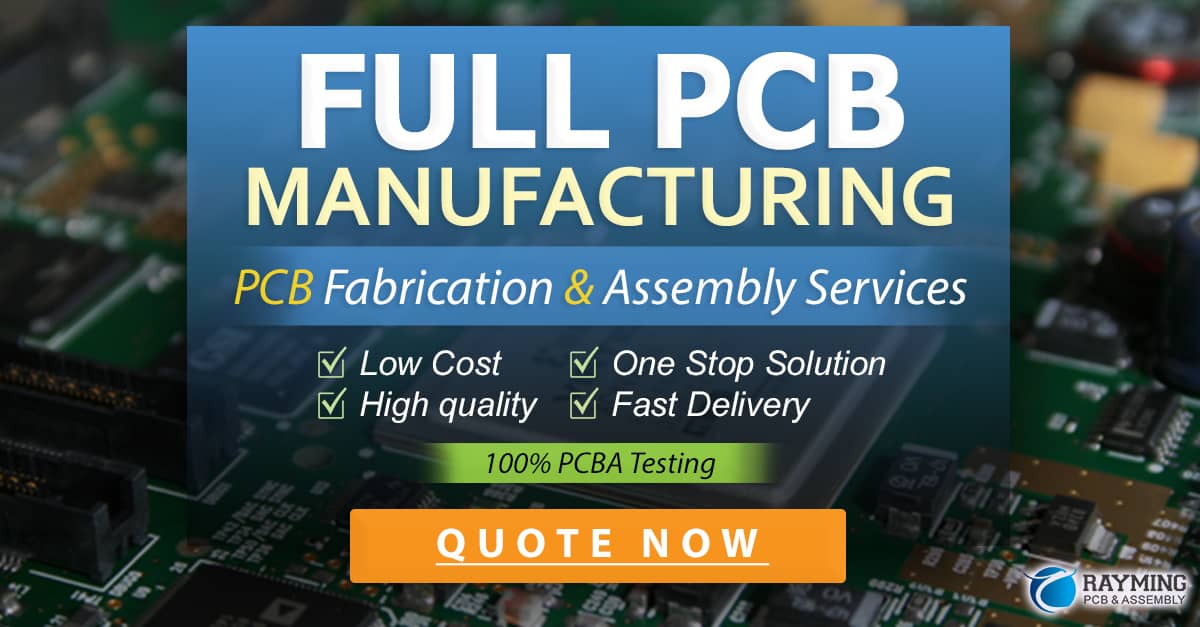
PCB Manufacturing Considerations
When planning for PCB manufacturing, there are several factors to consider to ensure a successful outcome.
Material Selection
The choice of PCB substrate material depends on the specific requirements of the application, such as:
- Temperature range
- Dielectric constant
- Mechanical strength
- Cost
FR-4 is the most commonly used PCB substrate material due to its good balance of properties and cost-effectiveness. However, for high-frequency or high-temperature applications, other materials like Rogers, Teflon, or ceramic may be more suitable.
Layer Stack-up
The number of layers in a PCB and their arrangement, known as the layer stack-up, is determined by the complexity of the circuit and the signal integrity requirements. A typical layer stack-up for a four-layer PCB might consist of:
- Top layer: Signal traces and components
- Inner layer 1: Ground plane
- Inner layer 2: Power plane
- Bottom layer: Signal traces and components
Proper layer stack-up design is crucial for maintaining signal integrity, controlling impedance, and minimizing crosstalk between traces.
Design for Manufacturing (DFM)
To ensure that your PCB design is manufacturable and to minimize the risk of defects, it is essential to follow Design for Manufacturing (DFM) guidelines. Some key DFM considerations include:
- Minimum trace width and spacing: Adhere to the manufacturer’s specifications for minimum trace width and spacing to ensure proper copper etching and to avoid short circuits.
- Drill hole sizes: Use standard drill sizes and ensure that the hole diameters are compatible with the component lead sizes.
- Solder mask and silkscreen clearances: Provide adequate clearance between solder mask openings, silkscreen text, and copper features to avoid manufacturing issues.
- Panelization: If your design will be part of a panel with multiple PCBs, consider the panelization layout and include necessary fiducial marks and tooling holes.
By following DFM guidelines, you can reduce the likelihood of manufacturing defects and delays, ultimately saving time and cost.
PCB Testing and Inspection
To ensure the quality and reliability of the manufactured PCBs, various testing and inspection methods are employed, including:
- Visual inspection: A visual check of the PCB for any obvious defects, such as incorrect component placement, solder bridges, or damaged traces.
- Automated Optical Inspection (AOI): An automated system that uses cameras and image processing algorithms to detect manufacturing defects.
- X-ray inspection: Used to inspect solder joints and other hidden features beneath surface-mounted components.
- Electrical testing: Includes continuity testing, insulation resistance testing, and functional testing to verify the electrical performance of the PCB.
- Burn-in testing: The PCB is subjected to elevated temperatures and voltages to identify any potential early failures.
Thorough testing and inspection help to identify and rectify any issues before the PCBs are put into use, ensuring a higher level of quality and reliability.
Frequently Asked Questions (FAQ)
-
What is the typical turnaround time for PCB manufacturing?
The turnaround time for PCB manufacturing depends on various factors, such as the complexity of the design, the chosen materials, and the manufacturer’s workload. Generally, for standard PCBs, the turnaround time can range from a few days to a couple of weeks. Rush services may be available at an additional cost for faster turnaround times. -
How much does PCB manufacturing cost?
The cost of PCB manufacturing depends on several factors, including the PCB size, layer count, material, surface finish, and quantity. For small-volume production or prototyping, the cost per PCB can range from a few dollars to several tens of dollars. As the quantity increases, the cost per PCB typically decreases due to economies of scale. It is advisable to request quotes from multiple manufacturers to compare prices and find the best value for your project. -
What are the most common PCB surface finishes?
Some of the most common PCB surface finishes include: - HASL (Hot Air Solder Leveling): A tin-lead alloy is applied to the exposed copper pads, providing good solderability and low cost.
- ENIG (Electroless Nickel Immersion Gold): A thin layer of nickel is deposited onto the copper pads, followed by a thin layer of gold. ENIG offers excellent solderability, flatness, and shelf life.
- OSP (Organic Solderability Preservative): A thin, organic coating is applied to the copper pads to protect against oxidation. OSP is a cost-effective option but has a limited shelf life.
-
Immersion Silver: A thin layer of silver is deposited onto the copper pads, providing good solderability and moderate cost.
-
Can I manufacture PCBs at home?
While it is possible to manufacture simple PCBs at home using methods like toner transfer and etching, the process can be time-consuming, and the results may not be as professional or reliable as those obtained from a commercial PCB manufacturer. Home-based PCB manufacturing is better suited for hobbyists and educational purposes rather than for production-grade PCBs. -
What are the environmental considerations in PCB manufacturing?
PCB manufacturing involves the use of chemicals and materials that can have an environmental impact if not handled properly. Responsible PCB manufacturers follow strict environmental regulations and implement best practices to minimize their ecological footprint. These practices include proper waste management, using lead-free materials, and adhering to RoHS (Restriction of Hazardous Substances) and REACH (Registration, Evaluation, Authorization, and Restriction of Chemicals) directives. As a designer or customer, you can opt for environmentally friendly materials and work with manufacturers that demonstrate a commitment to sustainability.
Conclusion
PCB manufacturing is a complex process that involves multiple steps, from design to fabrication and assembly. By understanding the basics of PCB design, manufacturing processes, and key considerations, you can ensure that your PCBs are manufactured to the highest quality standards and meet the specific requirements of your application.
When designing and manufacturing PCBs, it is essential to work closely with your chosen PCB manufacturer and to provide them with accurate and complete design files and specifications. By maintaining open communication and following best practices, you can minimize the risk of manufacturing issues and delays, ultimately resulting in a successful PCB manufacturing experience.
As the electronics industry continues to evolve, advancements in PCB manufacturing technologies and materials will enable the creation of even more complex and high-performance electronic devices. By staying informed about these developments and adapting your PCB design and manufacturing strategies accordingly, you can remain at the forefront of this exciting and ever-changing field.
0 Comments