What is Design Rule Check (DRC)?
Design Rule Check, commonly known as DRC, is a critical step in the integrated circuit (IC) design process. DRC is an automated verification process that checks the layout of an IC design against a set of predefined design rules. These rules are established by the semiconductor foundry or fabrication facility to ensure that the design can be reliably manufactured using their specific process technology.
DRC is essential because it identifies potential issues in the IC layout that could lead to manufacturing defects or reliability problems. By running DRC, designers can catch and correct these issues before the design is sent for fabrication, saving time and costs associated with producing faulty chips.
Key aspects of DRC:
- Checks the layout against design rules
- Automated verification process
- Ensures manufacturability and reliability
- Saves time and costs by catching issues early
Why is DRC Important?
DRC plays a crucial role in the IC design process for several reasons:
-
Manufacturability: DRC ensures that the IC layout adheres to the design rules specified by the foundry, making it compatible with their manufacturing processes. This increases the likelihood of successfully fabricating the chip without defects.
-
Reliability: By catching potential issues such as short circuits, open circuits, or insufficient spacing between components, DRC helps improve the reliability and performance of the manufactured chip.
-
Cost reduction: Identifying and correcting layout issues early in the design process through DRC saves costs associated with manufacturing faulty chips and redesigning.
-
Time-to-market: DRC enables faster design iterations and reduces the overall time-to-market by minimizing the need for post-fabrication debugging and redesign.
Benefits of DRC:
Benefit | Description |
---|---|
Manufacturability | Ensures compatibility with foundry processes |
Reliability | Improves chip reliability and performance |
Cost reduction | Saves costs by catching issues early |
Time-to-market | Enables faster design iterations and reduces overall time |
DRC Design Rules
Design rules are a set of guidelines and constraints that define the allowable geometries, spacings, and configurations in an IC layout. These rules are specific to each foundry and process technology node. Some common categories of design rules include:
1. Minimum feature size
This rule specifies the smallest allowable width for various features in the layout, such as metal lines, polysilicon gates, and diffusion regions.
2. Minimum spacing
Spacing rules define the minimum distance required between different features to prevent short circuits or unwanted interactions.
3. Minimum enclosure
Enclosure rules ensure that one layer adequately overlaps or covers another layer to maintain proper connectivity and prevent open circuits.
4. Antenna rules
Antenna rules limit the maximum allowable ratio between the metal area and the gate area connected to it to prevent damage during the manufacturing process.
5. Density rules
Density rules specify the minimum and maximum allowable densities for various layers to ensure uniform distribution and prevent manufacturing issues.
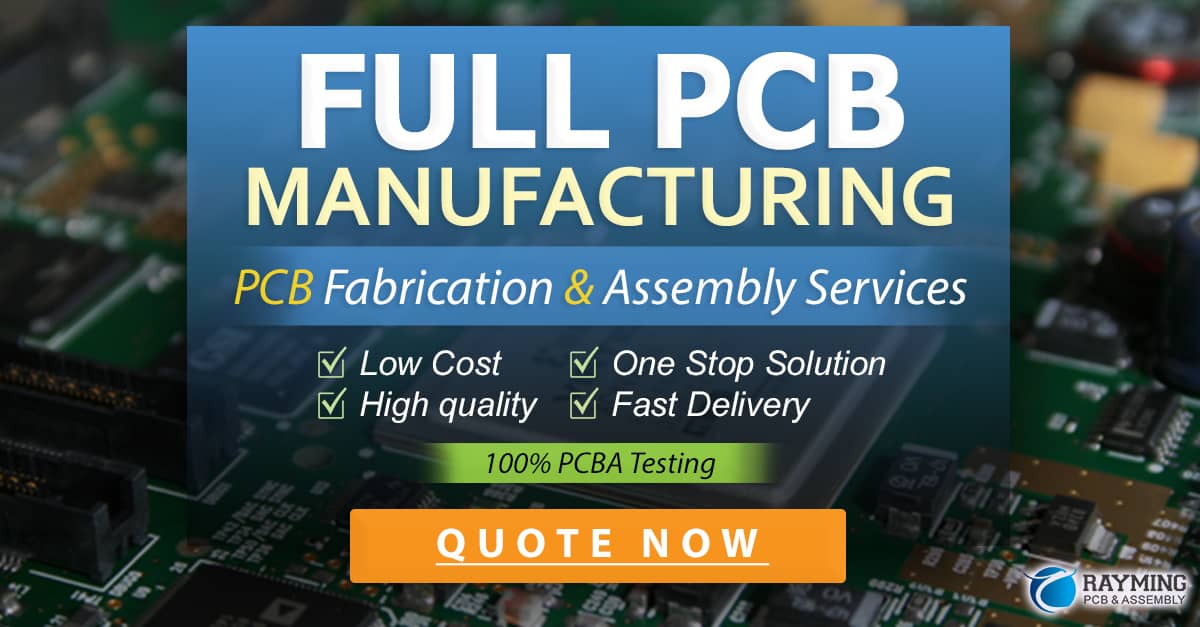
DRC Process Flow
The DRC process typically involves the following steps:
-
Design rule definition: The foundry provides a set of design rules specific to their process technology.
-
Layout creation: The IC design team creates the physical layout of the chip using electronic design automation (EDA) tools.
-
DRC setup: The design rules are imported into the DRC tool, and the tool is configured to run the required checks.
-
DRC execution: The DRC tool analyzes the IC layout and compares it against the defined design rules.
-
Error reporting: The DRC tool generates a report listing any violations of the design rules, along with their locations in the layout.
-
Error correction: The design team reviews the DRC report and makes necessary corrections to the layout to resolve the identified issues.
-
Re-verification: After making corrections, the DRC process is repeated to ensure that all violations have been resolved and no new issues have been introduced.
DRC Process Flow Table:
Step | Description |
---|---|
1 | Design rule definition |
2 | Layout creation |
3 | DRC setup |
4 | DRC execution |
5 | Error reporting |
6 | Error correction |
7 | Re-verification |
Common DRC Violations and Solutions
Some common DRC violations and their potential solutions include:
-
Minimum width violation: Increase the width of the affected feature to meet the minimum requirement.
-
Minimum spacing violation: Adjust the spacing between features to satisfy the minimum spacing rule.
-
Enclosure violation: Extend the enclosing layer to adequately cover the enclosed layer.
-
Antenna violation: Add antenna diodes or adjust the metal-to-gate ratio to mitigate antenna effects.
-
Density violation: Modify the layout to redistribute the features and meet the density requirements.
Common DRC Violations Table:
Violation | Solution |
---|---|
Minimum width | Increase feature width |
Minimum spacing | Adjust spacing between features |
Enclosure | Extend enclosing layer |
Antenna | Add antenna diodes or adjust ratio |
Density | Redistribute features |
Best Practices for DRC-Clean Designs
To minimize DRC violations and ensure a smooth design process, consider the following best practices:
-
Familiarize yourself with the design rules: Thoroughly understand the design rules provided by the foundry and how they apply to your specific design.
-
Use DRC-aware layout techniques: Employ layout techniques that inherently minimize DRC violations, such as using standard cell libraries and following recommended layout practices.
-
Run DRC early and often: Perform DRC checks regularly throughout the design process to catch and correct issues as early as possible.
-
Use automated layout tools: Leverage EDA tools with built-in DRC checks and automatic layout generation capabilities to minimize manual errors.
-
Collaborate with the foundry: Maintain open communication with the foundry to clarify any ambiguities in the design rules and seek guidance on best practices.
Best Practices Table:
Practice | Description |
---|---|
Familiarize with design rules | Understand and apply foundry-specific rules |
Use DRC-aware layout techniques | Employ techniques that minimize violations |
Run DRC early and often | Catch and correct issues early |
Use automated layout tools | Leverage EDA tools with built-in checks |
Collaborate with the foundry | Maintain open communication for guidance |
DRC in Advanced Process Nodes
As IC fabrication technology advances to smaller process nodes (e.g., 7nm, 5nm, 3nm), DRC becomes increasingly critical and challenging. Advanced process nodes introduce new design rules and complexities, such as:
-
More complex design rules: Advanced nodes have a larger number of design rules with tighter constraints, requiring more sophisticated DRC tools and methodologies.
-
Increased layout sensitivity: Smaller feature sizes and higher densities make layouts more sensitive to process variations, necessitating more stringent DRC checks.
-
3D design considerations: Advanced nodes often incorporate 3D structures like FinFETs or nanosheets, requiring DRC tools to handle 3D design rules and geometries.
-
Multi-patterning: Advanced nodes may use multi-patterning techniques, such as double or triple patterning, which introduce additional design rules and complexities for DRC.
Challenges in Advanced Nodes Table:
Challenge | Description |
---|---|
Complex design rules | Larger number of rules with tighter constraints |
Layout sensitivity | Increased sensitivity to process variations |
3D design considerations | Incorporation of 3D structures like FinFETs |
Multi-patterning | Additional rules and complexities |
To address these challenges, EDA vendors continuously develop more advanced DRC tools with improved algorithms, performance, and support for the latest process technologies. Close collaboration between IC design teams, EDA vendors, and foundries is essential to ensure successful DRC in advanced process nodes.
Frequently Asked Questions (FAQ)
1. What is the difference between DRC and LVS?
While DRC checks the layout against design rules, Layout Versus Schematic (LVS) is another verification process that compares the IC layout against the original schematic to ensure they match. LVS verifies the circuit connectivity and device properties, while DRC focuses on the physical layout’s adherence to manufacturing constraints.
2. Can DRC guarantee a perfect IC layout?
Although DRC is a critical step in ensuring a manufacturable and reliable IC layout, it cannot guarantee a perfect layout. DRC checks the layout against a set of predefined rules, but it may not catch all potential issues, especially those related to circuit functionality or performance. Other verification processes, such as LVS and parasitic extraction, are also necessary for a comprehensive verification flow.
3. How long does the DRC process take?
The duration of the DRC process depends on various factors, such as the size and complexity of the IC layout, the number of design rules, and the performance of the DRC tool. For small to medium-sized layouts, DRC may take a few minutes to a few hours. However, for larger and more complex designs, DRC can take several hours or even days to complete.
4. What happens if DRC violations are not corrected?
If DRC violations are not corrected before sending the IC layout for fabrication, it can lead to several problems. The fabricated chip may have manufacturing defects, such as short circuits or open circuits, which can affect its functionality and reliability. In some cases, the foundry may reject the design altogether, requiring the design team to make corrections and resubmit the layout, leading to delays and additional costs.
5. Are DRC rules the same for all foundries and process nodes?
No, DRC rules are specific to each foundry and process node. Different foundries may have different manufacturing capabilities and constraints, resulting in variations in their design rules. Moreover, as process nodes advance, design rules become more complex and stringent to accommodate the smaller feature sizes and higher densities. It is crucial for IC designers to obtain and follow the specific design rules provided by their target foundry and process node.
Conclusion
Design Rule Check is a critical step in the IC design process, ensuring that the physical layout of a chip adheres to the manufacturing constraints set by the foundry. By identifying and correcting potential issues early in the design phase, DRC helps improve the manufacturability, reliability, and overall success of an IC design.
As the semiconductor industry continues to push the boundaries of Moore’s Law and advance to smaller process nodes, DRC becomes increasingly important and challenging. IC designers must stay up-to-date with the latest design rules, best practices, and tools to effectively navigate the complexities of modern IC design and verification.
By understanding the principles of DRC, following best practices, and collaborating closely with foundries and EDA vendors, designers can create robust, manufacturable, and reliable IC layouts that meet the ever-growing demands of the digital age.
0 Comments