What is a Layer Stack-Up in PCB Design?
A layer stack-up in PCB (Printed Circuit Board) design refers to the arrangement and configuration of the various layers that make up a PCB. It is a critical aspect of PCB design as it determines the electrical, mechanical, and thermal properties of the board. The layer stack-up defines the number of layers, their order, thickness, and the materials used for each layer.
Importance of Layer Stack-Up in PCB Design
The layer stack-up is essential in PCB design for several reasons:
-
Signal Integrity: The layer stack-up plays a crucial role in maintaining signal integrity. It affects the impedance, crosstalk, and electromagnetic interference (EMI) of the signals propagating through the PCB. Proper layer stack-up design ensures that the signals maintain their quality and minimize interference.
-
Power Distribution: The layer stack-up also influences power distribution on the PCB. Dedicated power and ground planes in the stack-up provide low-impedance paths for power distribution, minimizing voltage drops and ensuring stable power delivery to components.
-
Thermal Management: The choice of materials and the arrangement of layers in the stack-up affect the thermal management of the PCB. Proper layer stack-up design helps dissipate heat generated by components, preventing overheating and ensuring reliable operation.
-
Manufacturing Feasibility: The layer stack-up must be designed considering the manufacturing capabilities and constraints. It should adhere to the fabrication tolerances, material availability, and cost considerations to ensure that the PCB can be manufactured efficiently and reliably.
Common Layer Types in PCB Stack-Up
A typical PCB stack-up consists of several layers, each serving a specific purpose. Here are the common layer types found in a PCB stack-up:
-
Signal Layers: These layers are used for routing the electrical signals between components on the PCB. They are typically made of copper and can be present on the outer layers (top and bottom) or inner layers of the PCB.
-
Power and Ground Planes: Power and ground planes are dedicated layers that provide a low-impedance path for power distribution and grounding. They help maintain a stable voltage supply and minimize noise and interference. These planes are usually made of copper and are placed in the inner layers of the PCB.
-
Dielectric Layers: Dielectric layers, also known as insulation layers, are non-conductive layers that separate the conductive layers in the PCB stack-up. They provide electrical insulation and determine the impedance of the signal traces. Common dielectric materials include FR-4, Rogers, and Isola.
-
Solder Mask Layers: Solder mask layers are applied on the outer layers of the PCB to protect the copper traces from oxidation and prevent solder bridging during the assembly process. They also provide insulation and improve the aesthetics of the PCB.
-
Silkscreen Layers: Silkscreen layers are used for printing text, logos, and component identifiers on the outer layers of the PCB. They aid in the assembly process and provide useful information for testing and debugging.
Factors to Consider in Layer Stack-Up Design
When designing the layer stack-up for a PCB, several factors need to be considered to ensure optimal performance and manufacturability. These factors include:
-
Number of Layers: The number of layers in the PCB stack-up depends on the complexity of the design, the signal density, and the routing requirements. A higher number of layers allows for more routing space but also increases the manufacturing cost and complexity.
-
Material Selection: The choice of materials for the conductive and dielectric layers affects the electrical, mechanical, and thermal properties of the PCB. Factors such as dielectric constant, loss tangent, glass transition temperature, and copper weight should be considered based on the application requirements.
-
Impedance Control: Impedance control is crucial for maintaining signal integrity in high-speed designs. The layer stack-up should be designed to achieve the desired impedance of the signal traces. This involves selecting appropriate dielectric materials, controlling the thickness of the dielectric layers, and adjusting the width and spacing of the signal traces.
-
Via Configuration: Vias are used to connect traces between different layers in the PCB stack-up. The placement and configuration of vias affect signal integrity, manufacturability, and reliability. Factors such as via size, via type (through-hole, blind, or buried), and via stubs should be considered in the layer stack-up design.
-
Manufacturing Constraints: The layer stack-up design must adhere to the manufacturing capabilities and constraints of the PCB fabricator. This includes minimum and maximum layer thicknesses, copper weights, dielectric thicknesses, and tolerances. Collaborating with the fabricator early in the design process can help ensure that the stack-up is manufacturable and cost-effective.
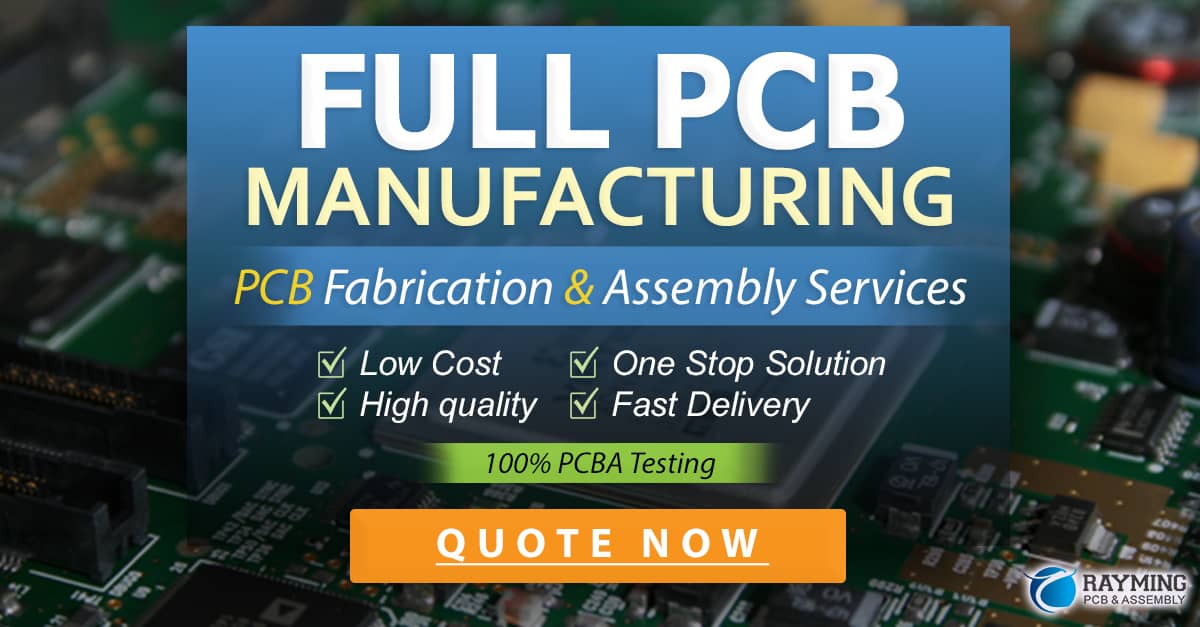
Common Layer Stack-Up Configurations
There are several common layer stack-up configurations used in PCB design, each suitable for different applications and requirements. Here are a few examples:
- 4-Layer Stack-Up:
- Top Layer: Signal
- Inner Layer 1: Ground
- Inner Layer 2: Power
- Bottom Layer: Signal
A 4-layer stack-up is a common configuration for simple to moderate complexity designs. It provides a good balance between routing space, power distribution, and cost.
- 6-Layer Stack-Up:
- Top Layer: Signal
- Inner Layer 1: Ground
- Inner Layer 2: Signal
- Inner Layer 3: Power
- Inner Layer 4: Signal
- Bottom Layer: Signal
A 6-layer stack-up offers more routing space and is suitable for designs with higher component density and signal requirements.
- 8-Layer Stack-Up:
- Top Layer: Signal
- Inner Layer 1: Ground
- Inner Layer 2: Signal
- Inner Layer 3: Power
- Inner Layer 4: Signal
- Inner Layer 5: Ground
- Inner Layer 6: Signal
- Bottom Layer: Signal
An 8-layer stack-up provides even more routing space and is used for complex designs with high-speed signals and dense component placement.
These are just a few examples, and the actual layer stack-up configuration can vary based on the specific design requirements, signal integrity considerations, and manufacturing constraints.
Best Practices for Layer Stack-Up Design
To ensure a robust and reliable PCB design, follow these best practices when defining the layer stack-up:
-
Plan the Stack-Up Early: Consider the layer stack-up early in the design process. Collaborate with the PCB fabricator to ensure that the stack-up is manufacturable and meets the design requirements.
-
Use Dedicated Power and Ground Planes: Incorporate dedicated power and ground planes in the stack-up to provide low-impedance paths for power distribution and grounding. This helps minimize noise, reduce voltage drops, and improve signal integrity.
-
Control Impedance: Design the stack-up to achieve the desired impedance for critical signals. Use appropriate dielectric materials, adjust the thickness of the dielectric layers, and control the width and spacing of the signal traces to maintain consistent impedance throughout the PCB.
-
Minimize Signal Layer Transitions: Minimize the number of layer transitions for signals, especially for high-speed signals. Each layer transition introduces discontinuities and can degrade signal quality. Use careful via placement and optimize signal routing to minimize layer transitions.
-
Consider Differential Pairs: When routing differential pairs, ensure that the traces are closely spaced and have equal lengths to maintain signal integrity. Use appropriate dielectric materials and control the impedance of the differential pairs in the stack-up.
-
Provide Adequate Clearance: Ensure sufficient clearance between different signal layers, power planes, and ground planes to prevent unintended coupling and crosstalk. Follow the PCB fabricator’s guidelines for minimum clearance requirements.
-
Use Symmetrical Stack-Up: Whenever possible, design a symmetrical stack-up to minimize warpage and improve the mechanical stability of the PCB. This involves balancing the copper distribution and using similar materials on opposite sides of the stack-up.
-
Document and Communicate: Clearly document the layer stack-up design, including the materials, thicknesses, and copper weights for each layer. Communicate the stack-up information to the PCB fabricator and other stakeholders to ensure everyone is on the same page.
PCB Layer Stack-Up Design Tools
To aid in the design and visualization of PCB layer stack-ups, various tools and software are available. Here are a few commonly used tools:
-
PCB Design Software: Most PCB design software, such as Altium Designer, Cadence Allegro, and Mentor Graphics PADS, have built-in layer stack-up editors. These tools allow you to define the layer stack-up, specify materials, and set layer thicknesses and copper weights.
-
Impedance Calculators: Impedance calculators are tools that help determine the necessary trace width, spacing, and dielectric thickness to achieve the desired impedance. These calculators take into account the dielectric constant and other material properties to provide accurate impedance calculations.
-
Layer Stack-Up Viewers: Layer stack-up viewers are standalone tools or plugins that provide a visual representation of the PCB layer stack-up. They display the arrangement of layers, thicknesses, and materials in a graphical format, making it easier to understand and communicate the stack-up design.
-
Manufacturer’s Tools: Many PCB fabricators provide their own layer stack-up design tools or templates. These tools are specific to their manufacturing capabilities and constraints, ensuring that the designed stack-up is compatible with their fabrication process.
Using these tools in combination with the best practices mentioned earlier can help streamline the layer stack-up design process and ensure a robust and manufacturable PCB.
FAQ
-
Q: What is the purpose of a layer stack-up in PCB design?
A: The purpose of a layer stack-up in PCB design is to define the arrangement and configuration of the various layers that make up the PCB. It determines the electrical, mechanical, and thermal properties of the board, affecting signal integrity, power distribution, and manufacturability. -
Q: How does the number of layers in a PCB stack-up affect the design?
A: The number of layers in a PCB stack-up affects the routing space, signal density, and manufacturing complexity. A higher number of layers allows for more routing space and accommodates more complex designs, but it also increases the manufacturing cost and complexity. -
Q: What are the common layer types in a PCB stack-up?
A: The common layer types in a PCB stack-up include signal layers for routing electrical signals, power and ground planes for power distribution and grounding, dielectric layers for insulation, solder mask layers for protection and insulation, and silkscreen layers for printing text and identifiers. -
Q: Why is impedance control important in layer stack-up design?
A: Impedance control is important in layer stack-up design to maintain signal integrity, especially in high-speed designs. It involves selecting appropriate dielectric materials, controlling the thickness of the dielectric layers, and adjusting the width and spacing of the signal traces to achieve the desired impedance and minimize signal reflections and distortions. -
Q: What are some best practices for layer stack-up design?
A: Some best practices for layer stack-up design include planning the stack-up early in the design process, using dedicated power and ground planes, controlling impedance, minimizing signal layer transitions, considering differential pairs, providing adequate clearance, using a symmetrical stack-up, and clearly documenting and communicating the stack-up information.
By understanding the importance of layer stack-up design, considering the various factors involved, and following best practices, PCB designers can create robust and reliable PCBs that meet the electrical, mechanical, and manufacturing requirements of their applications.
0 Comments