Introduction to Curtain Coating
Curtain coating is a highly efficient and versatile method for applying liquid coatings to various substrates, such as paper, plastic films, and metal foils. This technique involves creating a continuous, free-falling curtain of the coating material and allowing the substrate to pass through it, resulting in a uniform and precise layer of coating on the surface. Curtain coating has gained significant popularity in industries such as packaging, printing, and electronics due to its ability to achieve high-speed production with minimal material loss.
Advantages of Curtain Coating
- High-speed production: Curtain coating allows for coating speeds of up to 1,000 m/min, making it one of the fastest coating methods available.
- Precision and uniformity: The free-falling curtain ensures a highly uniform and precise coating layer, with minimal variations in thickness across the substrate.
- Multiple layer capabilities: Curtain coating enables the simultaneous application of multiple layers of different materials, reducing production time and costs.
- Low material loss: With proper optimization, curtain coating can achieve material utilization rates of up to 99%, minimizing waste and environmental impact.
The LPI Applying Method
The LPI (Liquid Pressure Injection) applying method is a innovative technique that enhances the performance of curtain coating by addressing some of its challenges, such as air entrainment and edge effects. In this method, the coating material is pressurized and injected into the curtain through a series of nozzles, creating a stable and uniform curtain with reduced turbulence and air entrainment.
Key Features of the LPI Applying Method
- Pressurized injection: The coating material is pressurized and injected into the curtain, ensuring a stable and continuous flow.
- Multiple nozzles: The use of multiple nozzles allows for precise control over the curtain’s width and uniformity, reducing edge effects and improving coating quality.
- Reduced air entrainment: The pressurized injection minimizes turbulence and air entrainment, resulting in a smoother and more uniform coating layer.
- Flexibility: The LPI applying method can be easily adapted to various coating materials and substrates, making it a versatile solution for different applications.
Optimizing Curtain Coating with the LPI Applying Method
To achieve high-speed production with low material loss using the LPI applying method, several key factors need to be considered and optimized:
1. Coating Material Properties
The rheological properties of the coating material, such as viscosity, surface tension, and density, play a crucial role in the stability and uniformity of the curtain. Optimizing these properties can help minimize defects and improve coating quality.
Property | Optimal Range |
---|---|
Viscosity | 50-1000 mPa·s |
Surface Tension | 20-50 mN/m |
Density | 800-1200 kg/m³ |
2. Curtain Height and Flow Rate
The height of the curtain and the flow rate of the coating material directly influence the coating thickness and uniformity. Adjusting these parameters based on the desired coating thickness and substrate speed is essential for achieving optimal results.
Coating Thickness | Curtain Height | Flow Rate |
---|---|---|
10-50 μm | 50-150 mm | 50-200 mL/min |
50-100 μm | 100-250 mm | 200-500 mL/min |
100-200 μm | 200-400 mm | 500-1000 mL/min |
3. Substrate Surface Characteristics
The surface energy and roughness of the substrate can significantly impact the wetting and adhesion of the coating material. Treating the substrate surface with corona discharge or plasma can improve wettability and ensure a uniform coating layer.
Substrate | Surface Energy (mN/m) | Roughness (Ra) |
---|---|---|
Paper | 30-50 | 0.5-2.0 μm |
Plastic Films | 20-40 | 0.1-0.5 μm |
Metal Foils | 40-60 | 0.05-0.2 μm |
4. Process Parameters
Other process parameters, such as the substrate speed, nozzle configuration, and drying conditions, need to be carefully controlled and optimized to ensure high-speed production with low material loss.
Parameter | Optimal Range |
---|---|
Substrate Speed | 100-1000 m/min |
Nozzle Diameter | 0.3-1.0 mm |
Nozzle Spacing | 5-20 mm |
Drying Temperature | 50-150 °C |
Drying Air Velocity | 10-50 m/s |
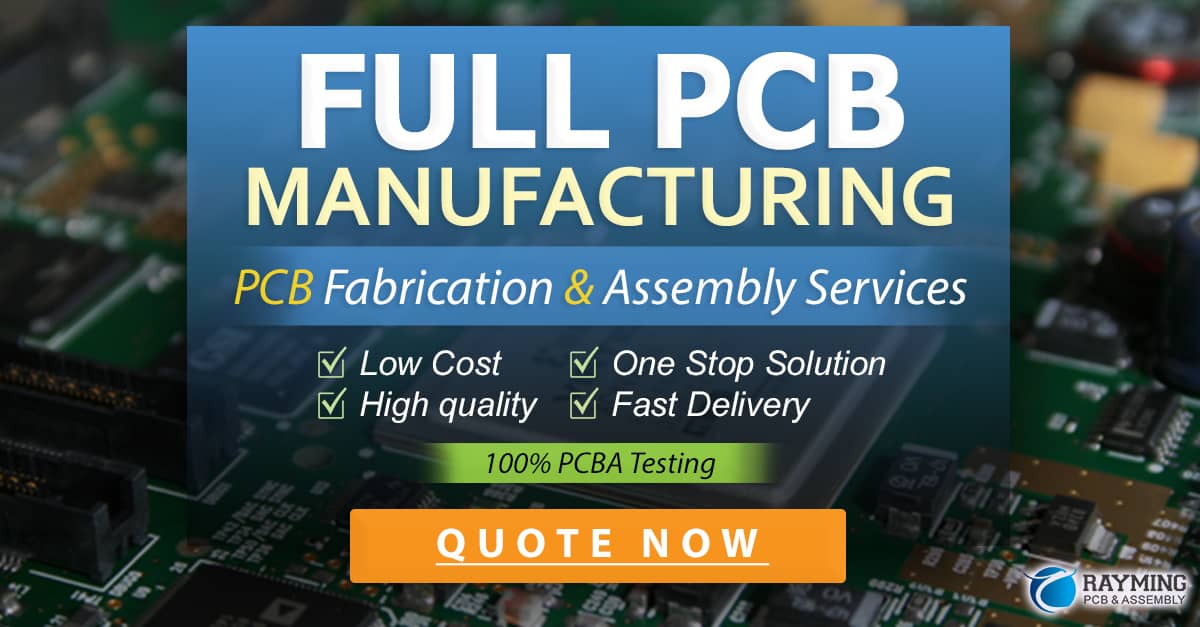
Case Studies
1. High-Speed Coating of Paper for Packaging
A packaging company implemented the LPI applying method for curtain coating of paper with a water-based barrier coating. By optimizing the coating material properties, curtain height, and flow rate, they achieved a coating speed of 800 m/min with a coating thickness of 25 μm. The material utilization rate was 98.5%, resulting in significant cost savings and reduced environmental impact.
2. Multi-Layer Coating of Plastic Films for Electronics
An electronics manufacturer used the LPI applying method to apply a three-layer coating on a PET film substrate for flexible printed circuits. The layers consisted of a conductive ink, a dielectric layer, and a protective overcoat. By carefully controlling the process parameters and utilizing the multi-layer capabilities of curtain coating, they achieved a production speed of 500 m/min with a total coating thickness of 75 μm. The coating uniformity was within ±2%, ensuring high-quality and reliable electronic components.
Future Trends and Developments
As industries continue to demand higher production speeds, better coating quality, and lower material consumption, the LPI applying method for curtain coating is expected to evolve further. Some of the future trends and developments include:
- Smart nozzle systems: Integration of sensors and feedback control systems to monitor and adjust the nozzle performance in real-time, ensuring optimal curtain stability and uniformity.
- Advanced coating materials: Development of novel coating materials with improved rheological properties, such as shear-thinning behavior and rapid leveling, to enhance coating quality and reduce defects.
- Hybrid coating techniques: Combining the LPI applying method with other coating techniques, such as slot die coating or gravure coating, to leverage the strengths of each method and achieve even higher production speeds and coating precision.
- Sustainable and eco-friendly coatings: Increasing adoption of water-based, solvent-free, and bio-based coating materials to reduce the environmental impact and comply with stringent regulations.
Frequently Asked Questions (FAQ)
1. What are the main advantages of using the LPI applying method for curtain coating?
The LPI applying method offers several advantages, including high-speed production, precise and uniform coating layers, multi-layer capabilities, and low material loss. By pressurizing and injecting the coating material into the curtain, this method reduces air entrainment and edge effects, resulting in improved coating quality.
2. Can the LPI applying method be used with different types of coating materials and substrates?
Yes, the LPI applying method is highly versatile and can be adapted to work with various coating materials, such as water-based, solvent-based, and UV-curable coatings. It is also compatible with a wide range of substrates, including paper, plastic films, and metal foils, making it suitable for diverse applications.
3. How does the LPI applying method compare to other curtain coating techniques in terms of production speed and material utilization?
The LPI applying method enables high-speed production, with coating speeds of up to 1,000 m/min, surpassing many other curtain coating techniques. Additionally, by optimizing the process parameters, this method can achieve material utilization rates of up to 99%, significantly reducing waste and material consumption compared to alternative methods.
4. What are the key factors to consider when optimizing the LPI applying method for a specific application?
To optimize the LPI applying method for a specific application, several key factors should be considered, including the coating material properties (viscosity, surface tension, density), curtain height and flow rate, substrate surface characteristics (surface energy, roughness), and process parameters (substrate speed, nozzle configuration, drying conditions). Careful control and adjustment of these factors are essential for achieving the desired coating quality and performance.
5. How can the LPI applying method contribute to sustainable and eco-friendly coating processes?
The LPI applying method can contribute to sustainable and eco-friendly coating processes by minimizing material waste and enabling the use of water-based, solvent-free, and bio-based coating materials. As industries increasingly prioritize sustainability and environmental compliance, the adoption of this method can help reduce the ecological footprint of coating processes while maintaining high performance and efficiency.
Conclusion
The LPI applying method for curtain coating offers a high-speed, precise, and efficient solution for applying liquid coatings to various substrates. By pressurizing and injecting the coating material into the curtain, this method achieves excellent coating uniformity, minimal material loss, and reduced environmental impact. As industries continue to demand higher production speeds and better coating quality, the LPI applying method is poised to play a crucial role in shaping the future of curtain coating technology. With ongoing developments in smart nozzle systems, advanced coating materials, hybrid techniques, and sustainable solutions, this method will continue to evolve and meet the ever-changing needs of diverse applications, from packaging and printing to electronics and beyond.
0 Comments