Introduction to Copper PCBs
Printed Circuit Boards (PCBs) are the backbone of modern electronic devices. They provide the necessary interconnections between various components and enable the functioning of complex circuits. One of the most critical materials used in PCB Manufacturing is copper. Copper is the primary conductor used in PCBs due to its excellent electrical conductivity, thermal conductivity, and durability. In this article, we will explore the role of copper in PCB manufacturing and how it impacts the overall performance and reliability of PCBs.
The Importance of Copper in PCB Manufacturing
Copper is an essential material in PCB manufacturing for several reasons:
-
Electrical Conductivity: Copper has high electrical conductivity, which allows it to efficiently transmit electrical signals between components on the PCB.
-
Thermal Conductivity: Copper also has excellent thermal conductivity, which helps in dissipating heat generated by components, preventing overheating and ensuring the longevity of the PCB.
-
Durability: Copper is a relatively soft metal but provides good mechanical strength to the PCB, making it resistant to wear and tear.
-
Cost-effectiveness: Compared to other conductive materials like gold or silver, copper is more affordable, making it a cost-effective choice for PCB manufacturing.
The PCB Manufacturing Process and Copper
The PCB manufacturing process involves several steps, and copper plays a crucial role in each of these stages. Let’s take a closer look at how copper is used in PCB manufacturing.
PCB Design and Copper Thickness
The first step in PCB manufacturing is the design phase. During this stage, the PCB layout is created using specialized software. One of the critical aspects of PCB design is determining the appropriate copper thickness for the board. The copper thickness is measured in ounces per square foot (oz/ft²) and typically ranges from 0.5 oz/ft² to 2.5 oz/ft².
The choice of copper thickness depends on several factors, such as:
- Current carrying capacity: Thicker copper layers can carry more current, making them suitable for power-hungry applications.
- Signal integrity: Thinner copper layers are preferred for high-speed signals to minimize signal loss and maintain signal integrity.
- Manufacturing constraints: Thicker copper layers can pose challenges during the etching process and may increase manufacturing costs.
Copper Thickness (oz/ft²) | Typical Applications |
---|---|
0.5 | Low-power, high-speed digital circuits |
1.0 | General-purpose PCBs, moderate power circuits |
2.0 | High-power applications, Automotive PCBs |
2.5 | Specialized high-current applications |
Copper Clad Laminates
Once the PCB design is finalized, the next step is to create the copper clad laminate. A copper clad laminate consists of a thin layer of copper foil bonded to an insulating substrate material, such as FR-4. The copper foil thickness can vary depending on the application, with standard thicknesses being 0.5 oz/ft², 1 oz/ft², and 2 oz/ft².
The bonding process involves applying heat and pressure to the copper foil and substrate, ensuring a strong and uniform bond. The quality of the copper clad laminate is crucial as it forms the foundation for the subsequent PCB manufacturing steps.
Etching and Copper Removal
After the copper clad laminate is prepared, the next step is to remove unwanted copper to create the desired circuit pattern. This process is called etching and involves several sub-steps:
-
Applying a photoresist layer: A light-sensitive polymer is applied to the copper surface.
-
Exposure and development: The photoresist is exposed to UV light through a photomask containing the circuit pattern. The exposed areas harden while the unexposed areas remain soluble.
-
Etching: The PCB is immersed in an etchant solution, typically ferric chloride or ammonium persulfate, which removes the copper from the areas not protected by the hardened photoresist.
-
Stripping: The remaining photoresist is removed using a stripping solution, revealing the final copper circuit pattern.
The etching process is critical in determining the accuracy and precision of the copper traces. Factors such as etchant concentration, temperature, and etching time must be carefully controlled to achieve the desired results.
Copper Plating and Surface Finish
After the etching process, the PCB undergoes additional copper plating to improve the thickness and uniformity of the copper traces. This step is called electroplating and involves immersing the PCB in a copper sulfate solution and applying an electric current. The copper ions in the solution are attracted to the exposed copper areas, resulting in the deposition of additional copper.
Once the copper plating is complete, a surface finish is applied to protect the copper from oxidation and enhance solderability. Common surface finishes include:
- Hot Air Solder Leveling (HASL): A thin layer of solder is applied to the copper surface.
- Electroless Nickel Immersion Gold (ENIG): A layer of nickel is deposited on the copper, followed by a thin layer of gold.
- Immersion Tin: A thin layer of tin is deposited on the copper surface.
- Organic Solderability Preservative (OSP): A thin organic compound layer is applied to the copper surface.
The choice of surface finish depends on factors such as the intended application, soldering requirements, and cost.
Copper and PCB Performance
The use of copper in PCB manufacturing has a significant impact on the overall performance and reliability of the final product. Let’s explore some key aspects of how copper affects PCB performance.
Electrical Conductivity and Signal Integrity
Copper’s high electrical conductivity is one of the main reasons for its widespread use in PCBs. The electrical conductivity of copper allows for efficient transfer of electrical signals between components, minimizing signal loss and ensuring signal integrity. However, the performance of copper traces can be affected by factors such as:
- Trace width and thickness: Wider and thicker traces have lower resistance and can carry more current, but they also consume more space on the PCB.
- Trace geometry: The layout and routing of copper traces can affect signal integrity, especially at high frequencies. Proper design techniques, such as minimizing trace length, avoiding sharp bends, and maintaining consistent trace impedance, are essential for optimal performance.
- Copper roughness: The surface roughness of the copper traces can impact signal propagation and lead to signal reflections and losses. Smoother copper surfaces are preferred for high-speed applications.
Thermal Management and Copper
Copper’s excellent thermal conductivity makes it an essential material for managing heat dissipation in PCBs. As electronic components generate heat during operation, it is crucial to efficiently transfer this heat away from the components to prevent overheating and ensure reliable performance.
Copper planes and heat spreaders are commonly used in PCBs to enhance thermal management. Copper planes are large areas of copper that act as heat sinks, spreading the heat generated by components across a larger surface area. Heat spreaders are thick copper layers that are strategically placed near heat-generating components to aid in heat dissipation.
Thermal vias, which are copper-plated holes connecting different layers of the PCB, are also used to transfer heat vertically through the board. By providing a low-resistance path for heat flow, thermal vias help in distributing heat more efficiently and preventing localized hot spots.
Copper Thickness and Current Carrying Capacity
The thickness of the copper layers in a PCB directly affects its current carrying capacity. Thicker copper layers can handle higher currents without experiencing excessive heating or voltage drop. This is particularly important for power-hungry applications, such as motor controllers, power supplies, and high-current devices.
The current carrying capacity of a copper trace can be calculated using various methods, such as the IPC-2152 standard or the Saturn PCB Toolkit. These methods take into account factors like trace width, copper thickness, temperature rise, and ambient temperature to determine the maximum allowable current.
When designing PCBs for high-current applications, it is essential to carefully consider the copper thickness and trace width to ensure adequate current carrying capacity and minimize voltage drop.
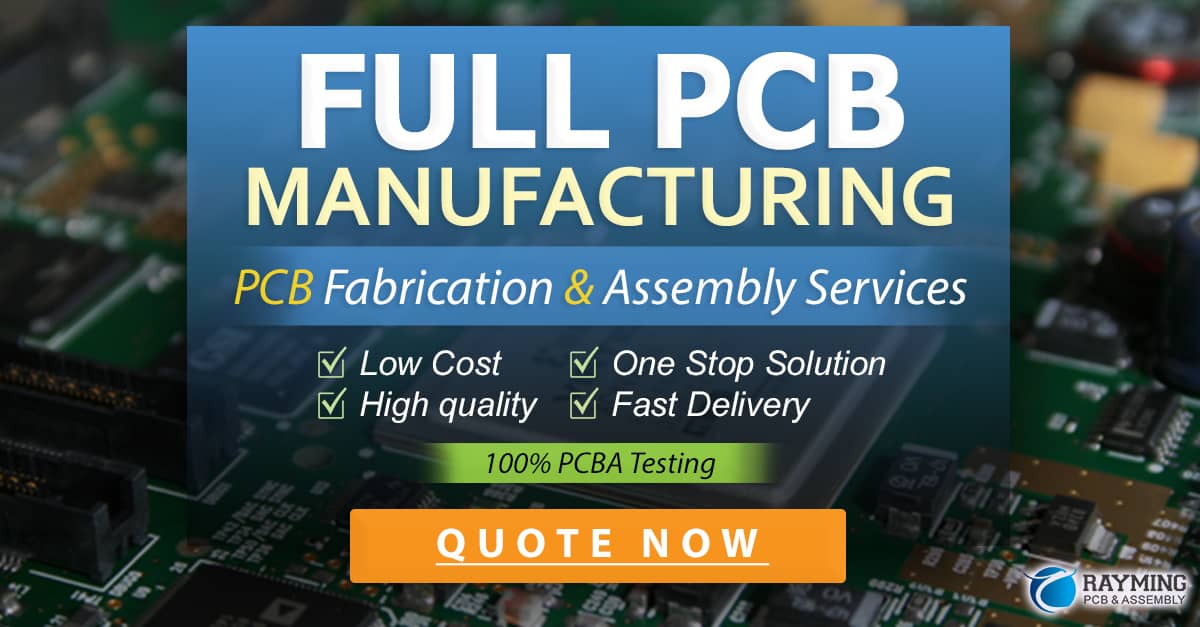
Challenges and Considerations in Copper PCB Manufacturing
While copper is an excellent material for PCB manufacturing, there are several challenges and considerations that must be addressed to ensure optimal performance and reliability.
Copper Thickness Variation and Etching Challenges
One of the challenges in PCB manufacturing is maintaining consistent copper thickness across the entire board. Variations in copper thickness can occur due to factors such as uneven plating, etchant depletion, and temperature gradients during the etching process. These variations can lead to inconsistencies in trace width and impedance, affecting signal integrity and performance.
To mitigate these issues, PCB Manufacturers employ techniques such as:
- Copper thickness monitoring: Real-time monitoring of copper thickness during the plating process helps in maintaining consistency and identifying any deviations.
- Etchant concentration control: Regularly monitoring and adjusting the concentration of the etchant solution ensures consistent etching rates and minimizes variations in trace width.
- Temperature control: Maintaining stable temperatures during the etching process reduces the risk of uneven etching and copper thickness variations.
Copper Oxidation and Surface Finish Considerations
Copper is prone to oxidation when exposed to air, leading to the formation of a thin oxide layer on the surface. This oxide layer can affect the solderability and electrical conductivity of the copper traces. To prevent oxidation and ensure reliable soldering, PCBs undergo a surface finish process.
The choice of surface finish depends on several factors, including the intended application, environmental conditions, and cost. Each surface finish has its advantages and limitations, and it is essential to select the appropriate finish based on the specific requirements of the PCB.
For example, ENIG provides excellent solderability and corrosion resistance but is more expensive compared to HASL. On the other hand, HASL is cost-effective and provides good solderability but may have limitations in terms of surface flatness and fine-pitch applications.
High-Frequency Copper Losses
As the operating frequencies of electronic devices continue to increase, the performance of copper traces becomes more critical. At high frequencies, copper traces can experience losses due to factors such as skin effect and dielectric losses.
Skin effect refers to the tendency of high-frequency currents to flow primarily on the surface of a conductor, reducing the effective cross-sectional area and increasing resistance. To mitigate skin effect losses, PCB designers use techniques such as:
- Trace width and thickness optimization: Increasing the trace width and thickness reduces the resistance and minimizes skin effect losses.
- Copper surface roughness control: Smoother copper surfaces reduce skin effect losses by providing a more uniform current distribution.
- High-frequency laminates: Using laminates with lower dielectric constant and dissipation factor helps in reducing dielectric losses at high frequencies.
Dielectric losses occur when the insulating material between copper traces absorbs some of the signal energy, leading to signal attenuation. The choice of substrate material and its properties, such as dielectric constant and dissipation factor, play a crucial role in minimizing dielectric losses.
Future Trends in Copper PCB Manufacturing
As the electronics industry continues to evolve, copper PCB manufacturing is also undergoing advancements to meet the ever-increasing demands for performance, reliability, and miniaturization.
High-Density Interconnect (HDI) PCBs
HDI PCBs are becoming increasingly popular due to their ability to accommodate high component density and enable miniaturization. HDI PCBs feature finer trace widths, smaller via sizes, and higher layer counts compared to traditional PCBs.
Copper plays a crucial role in HDI PCB manufacturing, as the finer trace widths and smaller via sizes require precise control over copper etching and plating processes. Advanced manufacturing techniques, such as modified semi-additive process (mSAP) and laser-drilled micro-vias, are used to achieve the required precision and reliability in HDI PCBs.
Embedded Copper Components
Embedded copper components, such as capacitors and inductors, are gaining traction in PCB manufacturing. By embedding these components within the PCB substrate, designers can save space, reduce parasitic effects, and improve overall system performance.
Copper is used to create the embedded components, either by etching copper patterns or by using specialized copper foils with pre-formed component structures. The integration of embedded copper components requires advanced manufacturing processes and precise control over copper patterning and lamination.
Copper Recycling and Sustainable Manufacturing
As environmental concerns gain prominence, the PCB manufacturing industry is focusing on sustainable practices and copper recycling. Copper is a valuable resource, and recycling copper from end-of-life PCBs can help in reducing environmental impact and conserving natural resources.
PCB manufacturers are implementing copper recycling processes, such as copper recovery from etching solutions and recycling of copper-containing waste. Additionally, the use of eco-friendly materials and processes, such as halogen-free laminates and lead-free soldering, is becoming more common in PCB manufacturing.
Conclusion
Copper is a vital material in PCB manufacturing, playing a crucial role in the performance, reliability, and functionality of electronic devices. From providing excellent electrical and thermal conductivity to enabling precise trace patterning and heat dissipation, copper is essential in every stage of the PCB manufacturing process.
As the electronics industry continues to advance, copper PCB manufacturing faces challenges and opportunities in terms of miniaturization, high-frequency performance, and sustainable practices. By understanding the properties and limitations of copper, PCB designers and manufacturers can make informed decisions to optimize PCB performance and meet the evolving demands of the industry.
Continued research and development in copper PCB manufacturing, along with the adoption of advanced manufacturing techniques and sustainable practices, will pave the way for the next generation of high-performance, reliable, and eco-friendly electronic devices.
Frequently Asked Questions (FAQ)
-
What is the primary role of copper in PCB manufacturing?
Copper is the primary conductor used in PCBs due to its excellent electrical conductivity, thermal conductivity, and durability. It enables efficient signal transfer, heat dissipation, and provides mechanical strength to the PCB. -
How does copper thickness affect PCB performance?
Copper thickness directly affects the current carrying capacity and signal integrity of a PCB. Thicker copper layers can handle higher currents without excessive heating or voltage drop, making them suitable for power-hungry applications. Thinner copper layers are preferred for high-speed signals to minimize signal loss and maintain signal integrity. -
What are the common challenges in maintaining consistent copper thickness during PCB manufacturing?
Variations in copper thickness can occur due to factors such as uneven plating, etchant depletion, and temperature gradients during the etching process. These variations can lead to inconsistencies in trace width and impedance, affecting signal integrity and performance. PCB manufacturers employ techniques like copper thickness monitoring, etchant concentration control, and temperature control to mitigate these challenges. -
How does copper affect the thermal management of PCBs?
Copper’s excellent thermal conductivity makes it an essential material for managing heat dissipation in PCBs. Copper planes, heat spreaders, and thermal vias are used to efficiently transfer heat away from components, preventing overheating and ensuring reliable performance. -
What are some future trends in copper PCB manufacturing?
Some notable trends in copper PCB manufacturing include the increasing adoption of High-Density Interconnect (HDI) PCBs, the integration of embedded copper components, and a focus on copper recycling and sustainable manufacturing practices. These trends aim to address the growing demands for miniaturization, performance, and environmental sustainability in the electronics industry.
0 Comments