What is an Aluminum PCB?
An Aluminum PCB, also known as a Metal Core PCB (MCPCB), is a type of printed circuit board that uses an aluminum substrate instead of the traditional FR-4 material. The aluminum substrate provides excellent thermal conductivity, allowing for better heat dissipation compared to standard PCBs. This makes Aluminum PCBs ideal for applications that generate significant amounts of heat, such as high-power LEDs, power electronics, and automotive systems.
Structure of an Aluminum PCB
An Aluminum PCB typically consists of three layers:
-
Dielectric Layer: This layer is an electrical insulator that sits on top of the aluminum substrate. It is usually made of a thermally conductive material, such as ceramic or polymer.
-
Circuit Layer: The circuit layer is where the copper traces and components are placed. It is bonded to the dielectric layer using a thermal adhesive.
-
Aluminum Substrate: The aluminum substrate serves as the base of the PCB and provides mechanical support and heat dissipation.
Layer | Material | Function |
---|---|---|
Circuit Layer | Copper | Electrical conductivity |
Dielectric Layer | Ceramic or Polymer | Electrical insulation and thermal conductivity |
Aluminum Substrate | Aluminum | Mechanical support and heat dissipation |
Advantages of Aluminum PCBs
Excellent Thermal Management
The primary advantage of Aluminum PCBs is their superior thermal management capabilities. The aluminum substrate has a high thermal conductivity, which allows it to quickly and efficiently transfer heat away from the components. This helps to prevent overheating and improves the overall reliability and lifespan of the electronic device.
Lightweight and Durable
Aluminum PCBs are lighter than traditional FR-4 PCBs, making them ideal for applications where weight is a critical factor, such as in aerospace and automotive industries. Additionally, aluminum is a durable material that can withstand harsh environments and mechanical stresses.
Cost-effective
While Aluminum PCBs may have a higher initial cost compared to FR-4 PCBs, they can be more cost-effective in the long run. The improved thermal management can reduce the need for additional cooling solutions, such as heatsinks or fans, which can save space and reduce overall system costs.
Applications of Aluminum PCBs
High-Power LEDs
Aluminum PCBs are commonly used in high-power LED applications, such as lighting fixtures and displays. The excellent thermal management properties of Aluminum PCBs help to prevent the LEDs from overheating, which can cause a reduction in light output and premature failure.
Power Electronics
Power electronic devices, such as motor drives, inverters, and power supplies, generate significant amounts of heat during operation. Aluminum PCBs can effectively dissipate this heat, ensuring stable performance and prolonging the lifespan of the components.
Automotive Electronics
In the automotive industry, Aluminum PCBs are used in various applications, such as headlights, engine control units, and power steering systems. The durability and thermal management capabilities of Aluminum PCBs make them well-suited for the harsh environments and demanding requirements of automotive electronics.
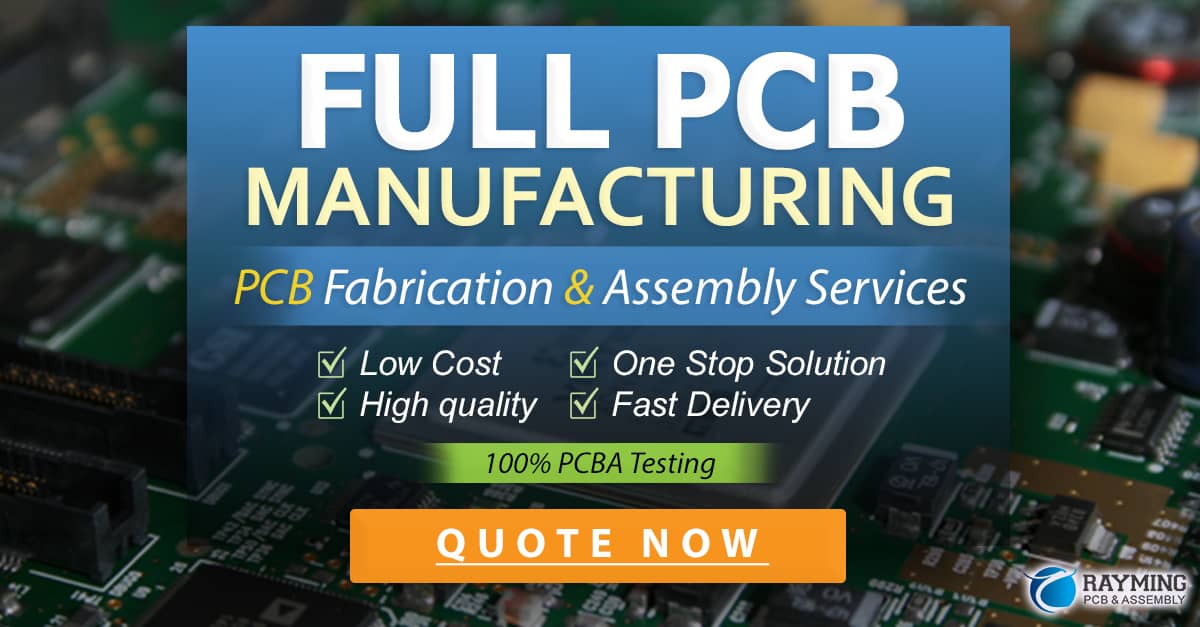
Designing Aluminum PCBs
Thermal Considerations
When designing an Aluminum PCB, it is essential to consider the thermal requirements of the application. The dielectric layer’s thickness and thermal conductivity should be chosen based on the amount of heat generated by the components and the desired operating temperature range.
Electrical Insulation
The dielectric layer in an Aluminum PCB serves as an electrical insulator between the aluminum substrate and the copper circuit layer. It is crucial to select a dielectric material with the appropriate dielectric strength and breakdown voltage to ensure proper electrical insulation.
Component Placement
Component placement on an Aluminum PCB should be optimized for thermal management. Components that generate significant amounts of heat should be placed close to the aluminum substrate to facilitate heat transfer. Additionally, it is essential to consider the thermal expansion coefficients of the components and the PCB materials to minimize stress and prevent failures due to thermal cycling.
Manufacturing Aluminum PCBs
Bonding Process
The manufacturing process for Aluminum PCBs involves bonding the dielectric layer to the aluminum substrate and then bonding the copper circuit layer to the dielectric layer. This bonding process is typically done using a thermal adhesive or a lamination process.
Surface Finishing
After the bonding process, the Aluminum PCB undergoes a surface finishing process to protect the copper traces and improve solderability. Common surface finishes for Aluminum PCBs include:
- HASL (Hot Air Solder Leveling)
- ENIG (Electroless Nickel Immersion Gold)
- OSP (Organic Solderability Preservative)
Quality Control
Strict quality control measures are essential during the manufacturing of Aluminum PCBs to ensure reliable performance and longevity. This includes inspections for proper bonding, electrical insulation, and thermal conductivity.
FAQ
-
Q: Can Aluminum PCBs be used in high-frequency applications?
A: Yes, Aluminum PCBs can be used in high-frequency applications. However, the dielectric layer’s material properties, such as dielectric constant and loss tangent, should be carefully considered to minimize signal loss and ensure proper impedance matching. -
Q: How does the thermal conductivity of Aluminum PCBs compare to other materials?
A: Aluminum has a thermal conductivity of approximately 200 W/mK, which is significantly higher than FR-4 (0.3 W/mK) and comparable to copper (400 W/mK). This high thermal conductivity allows Aluminum PCBs to efficiently transfer heat away from components. -
Q: Can Aluminum PCBs be manufactured with multiple layers?
A: Yes, Aluminum PCBs can be manufactured with multiple layers. The number of layers depends on the specific application requirements and the capabilities of the manufacturing process. -
Q: Are Aluminum PCBs more expensive than traditional FR-4 PCBs?
A: The initial cost of Aluminum PCBs may be higher than FR-4 PCBs due to the specialized materials and manufacturing processes involved. However, the improved thermal management and potential for reduced system costs can make Aluminum PCBs more cost-effective in the long run. -
Q: Can Aluminum PCBs be used in flexible applications?
A: While Aluminum PCBs are not as flexible as traditional flexible PCBs, they can be manufactured with a certain degree of flexibility. This is achieved by using thinner aluminum substrates and flexible dielectric materials. However, the flexibility is limited compared to polyimide-based flexible PCBs.
Conclusion
Aluminum PCBs offer a compelling solution for applications that require excellent thermal management, durability, and lightweight construction. By leveraging the high thermal conductivity of aluminum, these PCBs can efficiently dissipate heat, improving the performance and reliability of electronic devices. With their widespread use in high-power LEDs, power electronics, and automotive systems, Aluminum PCBs have proven to be a valuable technology in the electronics industry.
As designers and manufacturers continue to push the boundaries of electronic performance, the demand for effective thermal management solutions will only increase. Aluminum PCBs are well-positioned to meet this demand, offering a combination of thermal efficiency, mechanical robustness, and cost-effectiveness. By understanding the unique properties and design considerations of Aluminum PCBs, engineers can create innovative and reliable electronic products that excel in even the most demanding applications.
0 Comments