What is a Standard PCB?
A standard PCB, also known as a regular or conventional PCB, is the most common type of printed circuit board used in electronic devices. It consists of a thin layer of copper foil laminated onto an insulating substrate, typically made of fiberglass or epoxy resin. The copper layer is etched to create conductive paths, pads, and vias that connect the electronic components mounted on the board.
Characteristics of Standard PCBs
- Copper Thickness:
- Standard PCBs typically have a copper thickness ranging from 1 oz to 2 oz per square foot.
-
The most common copper weight used in standard PCBs is 1 oz, which translates to a thickness of approximately 35 microns (1.4 mils).
-
Thermal Management:
- Standard PCBs have limited thermal management capabilities due to the thin copper layer.
-
They are suitable for low-power applications where heat dissipation is not a critical concern.
-
Current Carrying Capacity:
- The current carrying capacity of standard PCBs is determined by the width and thickness of the copper traces.
-
Thin copper layers limit the maximum current that can flow through the traces without causing excessive heating or voltage drop.
-
Manufacturing Process:
- Standard PCBs are manufactured using a subtractive process, where copper is selectively removed from the laminate to create the desired circuit pattern.
- The process involves applying a photoresist layer, exposing it to light through a photomask, and etching away the unwanted copper.
Applications of Standard PCBs
Standard PCBs find applications in a wide range of electronic devices, such as:
- Consumer electronics (smartphones, laptops, televisions)
- Industrial control systems
- Automotive electronics
- Medical devices
- Telecommunications equipment
What is a Thick Copper PCB?
A thick copper PCB, as the name suggests, features a significantly thicker layer of copper compared to a standard PCB. The increased copper thickness provides several advantages, particularly in terms of thermal management and current carrying capacity. Thick copper PCBs are designed to handle high-power applications and environments with elevated temperatures.
Characteristics of Thick Copper PCBs
- Copper Thickness:
- Thick copper PCBs have a copper thickness typically ranging from 3 oz to 20 oz per square foot.
-
The most common thicknesses used in thick copper PCBs are 4 oz (140 microns or 5.6 mils) and 6 oz (210 microns or 8.4 mils).
-
Thermal Management:
- The increased copper thickness in thick copper PCBs enhances their thermal management capabilities.
-
The thicker copper layer acts as a heatsink, efficiently dissipating heat generated by the electronic components.
-
Current Carrying Capacity:
- Thick copper PCBs can handle higher currents compared to standard PCBs due to the increased cross-sectional area of the copper traces.
-
The thicker copper allows for wider traces, reducing resistance and enabling higher current flow without overheating.
-
Manufacturing Process:
- Thick copper PCBs are manufactured using a combination of subtractive and additive processes.
- The initial copper layer is typically thicker than the desired final thickness, and additional copper is electroplated onto the traces to achieve the required thickness.
Applications of Thick Copper PCBs
Thick copper PCBs are commonly used in applications that require high power handling, heat dissipation, and reliability, such as:
- Power electronics (inverters, converters, motor drives)
- Automotive power systems
- High-current LED lighting
- Solar energy systems
- Aerospace and defense applications
Comparison Table: Standard PCB vs. Thick Copper PCB
Feature | Standard PCB | Thick Copper PCB |
---|---|---|
Copper Thickness | 1 oz to 2 oz (35 to 70 microns) | 3 oz to 20 oz (105 to 700 microns) |
Thermal Management | Limited heat dissipation | Enhanced heat dissipation |
Current Carrying Capacity | Lower current handling | Higher current handling |
Manufacturing Process | Subtractive process | Combination of subtractive and additive processes |
Common Applications | Consumer electronics, industrial control systems, automotive electronics | Power electronics, automotive power systems, high-current LED lighting |
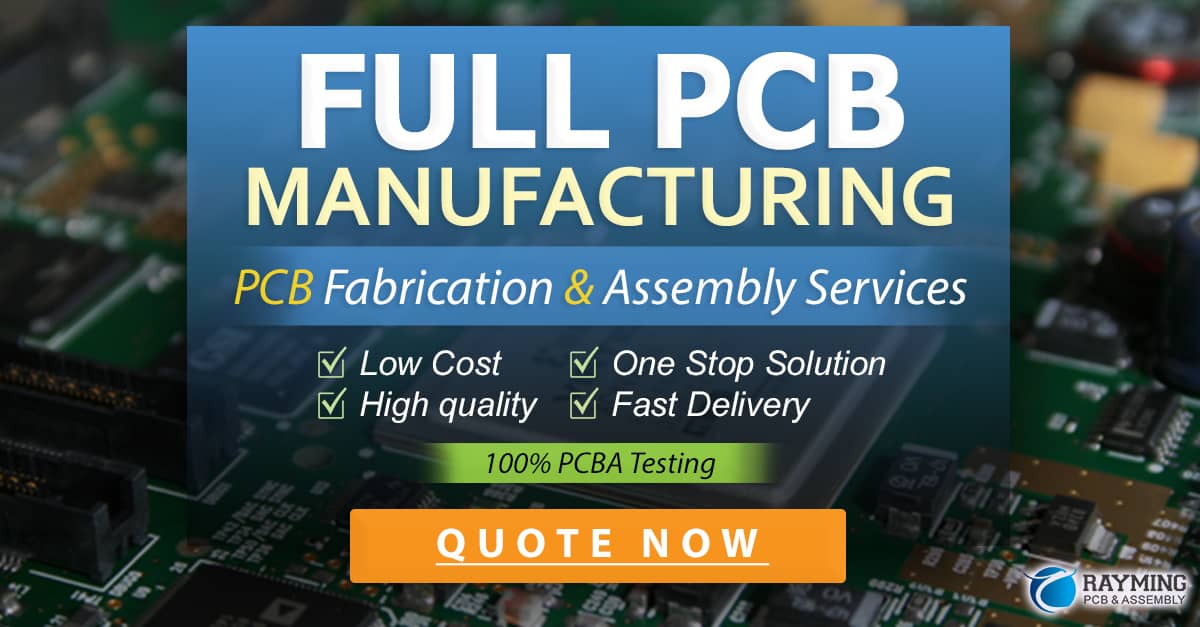
Advantages of Thick Copper PCBs
- Improved Thermal Management:
- The thicker copper layer in thick copper PCBs acts as an effective heatsink, efficiently dissipating heat generated by the electronic components.
-
This enhanced thermal management helps in maintaining optimal operating temperatures, prolonging the lifespan of the components, and ensuring reliable performance.
-
Higher Current Carrying Capacity:
- Thick copper PCBs can handle higher currents compared to standard PCBs due to the increased cross-sectional area of the copper traces.
-
The thicker copper allows for wider traces, reducing resistance and enabling higher current flow without overheating or causing voltage drop.
-
Increased Mechanical Strength:
- The thicker copper layer in thick copper PCBs provides additional mechanical strength and durability to the board.
-
This enhanced robustness makes thick copper PCBs suitable for applications that are subjected to harsh environments, vibrations, or mechanical stresses.
-
Improved Electrical Performance:
- The increased copper thickness in thick copper PCBs reduces the overall resistance of the traces, minimizing voltage drop and improving electrical performance.
-
This is particularly beneficial in high-power applications where maintaining stable voltage levels is crucial.
-
Better Heat Spreading:
- The thicker copper layer in thick copper PCBs enables better heat spreading across the board.
- This uniform heat distribution helps in preventing hot spots and thermal gradients, which can cause stress and damage to the electronic components.
Challenges and Considerations
While thick copper PCBs offer numerous advantages, there are some challenges and considerations to keep in mind:
- Higher Manufacturing Cost:
- The additional copper used in thick copper PCBs and the specialized manufacturing processes involved contribute to a higher production cost compared to standard PCBs.
-
The cost increase is justified in applications where the benefits of thick copper PCBs are essential.
-
Increased Weight:
- The thicker copper layer in thick copper PCBs adds extra weight to the board.
-
This should be considered in weight-sensitive applications, such as aerospace or portable devices.
-
Design Considerations:
- Designing thick copper PCBs requires careful consideration of trace width, spacing, and thermal management.
-
The increased copper thickness may affect the impedance and signal integrity of high-speed circuits, requiring appropriate design techniques to mitigate these effects.
-
Manufacturing Complexity:
- The manufacturing process for thick copper PCBs involves additional steps, such as electroplating, which can increase production time and complexity.
- Specialized equipment and expertise are required to ensure the desired copper thickness and uniformity.
FAQ
- What is the typical copper thickness in a standard PCB?
-
Standard PCBs typically have a copper thickness ranging from 1 oz to 2 oz per square foot, with 1 oz (35 microns or 1.4 mils) being the most common.
-
How does the copper thickness affect the thermal management of a PCB?
-
The thicker copper layer in thick copper PCBs acts as an effective heatsink, efficiently dissipating heat generated by the electronic components. This enhanced thermal management helps in maintaining optimal operating temperatures and ensuring reliable performance.
-
Can thick copper PCBs handle higher currents compared to standard PCBs?
-
Yes, thick copper PCBs can handle higher currents due to the increased cross-sectional area of the copper traces. The thicker copper allows for wider traces, reducing resistance and enabling higher current flow without overheating or causing voltage drop.
-
Are thick copper PCBs more expensive to manufacture than standard PCBs?
-
Yes, thick copper PCBs are generally more expensive to manufacture compared to standard PCBs. The additional copper used and the specialized manufacturing processes involved contribute to a higher production cost.
-
What are some common applications for thick copper PCBs?
- Thick copper PCBs are commonly used in applications that require high power handling, heat dissipation, and reliability, such as power electronics, automotive power systems, high-current LED lighting, solar energy systems, and aerospace and defense applications.
Conclusion
In summary, standard PCBs and thick copper PCBs serve different purposes based on their unique characteristics and capabilities. Standard PCBs are the most common type, suitable for a wide range of electronic devices and low-power applications. On the other hand, thick copper PCBs excel in applications that demand enhanced thermal management, higher current carrying capacity, and improved electrical performance.
When choosing between a standard PCB and a thick copper PCB, it is essential to consider the specific requirements of the application, including power handling, heat dissipation, mechanical strength, and cost. By understanding the differences and advantages of each type, designers and engineers can make informed decisions to ensure optimal performance and reliability in their electronic systems.
As technology continues to advance and electronic devices become more powerful and compact, the demand for thick copper PCBs is likely to increase. Their ability to handle high currents, dissipate heat effectively, and withstand harsh environments makes them a valuable asset in various industries, from automotive and power electronics to aerospace and defense.
By leveraging the benefits of thick copper PCBs, manufacturers can push the boundaries of electronic design, creating innovative solutions that meet the evolving needs of modern applications. As we move towards a future driven by advanced electronics, thick copper PCBs will undoubtedly play a crucial role in enabling the development of reliable, high-performance systems.
0 Comments