Types of PCB Components
Resistors
Resistors are one of the most basic and essential components in PCB manufacturing. They are used to control the flow of current in a circuit and to create voltage drops. Resistors come in various types, including:
Carbon Composition Resistors
Carbon composition resistors are made of a mixture of carbon and ceramic materials. They are inexpensive and have a low tolerance, making them suitable for general-purpose applications.
Film Resistors
Film resistors are made of a thin film of metal or carbon deposited on a ceramic substrate. They have a higher tolerance and stability compared to carbon composition resistors, making them suitable for more demanding applications.
Wire-Wound Resistors
Wire-wound resistors are made of a wire wound around a ceramic or fiberglass core. They have a high power rating and are used in applications that require high power dissipation.
Resistor Type | Tolerance | Power Rating | Applications |
---|---|---|---|
Carbon Composition | ±5% to ±20% | 0.125W to 2W | General purpose |
Film | ±0.1% to ±5% | 0.125W to 2W | Precision circuits |
Wire-Wound | ±0.1% to ±5% | 1W to 100W | High power applications |
Capacitors
Capacitors are another essential component in PCB manufacturing. They are used to store electrical energy and to filter out unwanted signals. Capacitors come in various types, including:
Ceramic Capacitors
Ceramic capacitors are made of a ceramic dielectric material sandwiched between two metal plates. They have a high dielectric constant and are suitable for high-frequency applications.
Electrolytic Capacitors
Electrolytic capacitors are made of a metal foil and an electrolyte solution. They have a high capacitance value and are polarized, meaning they have a positive and negative terminal.
Tantalum Capacitors
Tantalum capacitors are made of a tantalum pentoxide dielectric and a tantalum anode. They have a high capacitance value and are suitable for low-voltage applications.
Capacitor Type | Capacitance Range | Voltage Range | Applications |
---|---|---|---|
Ceramic | 1pF to 1µF | 10V to 50kV | High frequency |
Electrolytic | 1µF to 1F | 5V to 500V | Power supply filtering |
Tantalum | 0.1µF to 1000µF | 2V to 50V | Low voltage, high capacitance |
Inductors
Inductors are used to store magnetic energy and to filter out unwanted signals. They are made of a coil of wire wound around a core material, such as ferrite or iron. Inductors come in various types, including:
Air Core Inductors
Air core inductors are made of a coil of wire without a core material. They have a low inductance value and are suitable for high-frequency applications.
Ferrite Core Inductors
Ferrite core inductors are made of a coil of wire wound around a ferrite core. They have a high inductance value and are suitable for low-frequency applications.
Inductor Type | Inductance Range | Frequency Range | Applications |
---|---|---|---|
Air Core | 1nH to 1µH | 100MHz to 10GHz | High frequency |
Ferrite Core | 1µH to 10mH | 1kHz to 100MHz | Low frequency |
Diodes
Diodes are used to allow current to flow in only one direction and to protect the circuit from reverse voltage. They are made of a semiconductor material, such as silicon or germanium, and have two terminals: an anode and a cathode. Diodes come in various types, including:
Rectifier Diodes
Rectifier diodes are used to convert alternating current (AC) to direct current (DC). They have a low forward voltage drop and are suitable for power supply applications.
Zener Diodes
Zener diodes are used to regulate voltage and to protect the circuit from overvoltage. They have a sharp breakdown voltage and are suitable for voltage reference applications.
Diode Type | Forward Voltage | Reverse Voltage | Applications |
---|---|---|---|
Rectifier | 0.6V to 1.2V | 50V to 1000V | Power supply |
Zener | 1.8V to 200V | 1.8V to 200V | Voltage regulation |
Transistors
Transistors are used to amplify and switch electronic signals. They are made of a semiconductor material, such as silicon or germanium, and have three terminals: a base, a collector, and an emitter. Transistors come in various types, including:
Bipolar Junction Transistors (BJTs)
BJTs are made of two types of semiconductor materials, such as NPN or PNP. They are used for amplification and switching applications.
Field-Effect Transistors (FETs)
FETs are made of a single type of semiconductor material, such as N-channel or P-channel. They are used for amplification and switching applications and have a high input impedance.
Transistor Type | Gain | Frequency Range | Applications |
---|---|---|---|
BJT | 10 to 1000 | 1kHz to 100MHz | Amplification, switching |
FET | 1 to 100 | 1kHz to 10GHz | Amplification, switching |
Integrated Circuits (ICs)
ICs are miniaturized electronic circuits that are fabricated on a single semiconductor substrate. They are used to perform complex functions, such as amplification, signal processing, and digital logic. ICs come in various types, including:
Analog ICs
Analog ICs are used to process continuous signals, such as audio and video. They include operational amplifiers, comparators, and voltage regulators.
Digital ICs
Digital ICs are used to process discrete signals, such as binary data. They include logic gates, flip-flops, and microcontrollers.
IC Type | Function | Applications |
---|---|---|
Analog | Signal processing | Audio, video |
Digital | Logic, data processing | Computers, digital systems |
PCB Manufacturing Process
The PCB manufacturing process involves several steps, including:
PCB Design
The first step in PCB manufacturing is to design the PCB using computer-aided design (CAD) software. The design includes the placement of components, the routing of traces, and the creation of solder mask and silkscreen layers.
PCB Fabrication
Once the PCB design is complete, the next step is to fabricate the PCB. This involves the following steps:
- Printing the circuit pattern on a copper-clad laminate using photolithography.
- Etching away the unwanted copper to create the circuit traces.
- Drilling holes for through-hole components and vias.
- Applying solder mask and silkscreen layers.
- Cutting the PCB to the desired size and shape.
PCB Assembly
After the PCB is fabricated, the next step is to assemble the components onto the PCB. This involves the following steps:
- Applying solder paste to the pads using a stencil.
- Placing the components onto the PCB using a pick-and-place machine.
- Reflowing the solder paste using a reflow oven to create a permanent connection between the components and the PCB.
- Inspecting the PCB for defects using automated optical inspection (AOI) or X-ray inspection.
PCB Testing
The final step in PCB manufacturing is to test the PCB to ensure that it functions as intended. This involves the following steps:
- Visual inspection to check for obvious defects, such as missing components or solder bridges.
- Functional testing to verify that the PCB performs the desired function.
- Environmental testing to ensure that the PCB can withstand the expected operating conditions, such as temperature, humidity, and vibration.
Frequently Asked Questions (FAQ)
1. What is the difference between through-hole and surface-mount components?
Through-hole components have leads that are inserted into holes drilled in the PCB and soldered on the opposite side. Surface-mount components are mounted directly onto the surface of the PCB and soldered using a reflow oven.
2. What is the purpose of solder mask and silkscreen layers?
Solder mask is a layer of polymer that is applied to the PCB to protect the copper traces from oxidation and to prevent solder bridges from forming during assembly. Silkscreen is a layer of ink that is applied to the PCB to label components and to provide assembly instructions.
3. What is the difference between a single-sided and a double-sided PCB?
A single-sided PCB has components and traces on only one side of the board, while a double-sided PCB has components and traces on both sides of the board. Double-sided PCBs are more complex and expensive to manufacture but offer higher density and better performance.
4. What is the purpose of a via in a PCB?
A via is a small hole drilled in the PCB that is used to connect traces on different layers of the board. Vias are used to route signals between layers and to provide a path for heat dissipation.
5. What is the difference between a rigid and a flexible PCB?
A rigid PCB is made of a rigid substrate material, such as FR-4, and is suitable for most applications. A flexible PCB is made of a flexible substrate material, such as polyimide, and is used in applications that require the PCB to bend or flex, such as in wearable devices or medical implants.
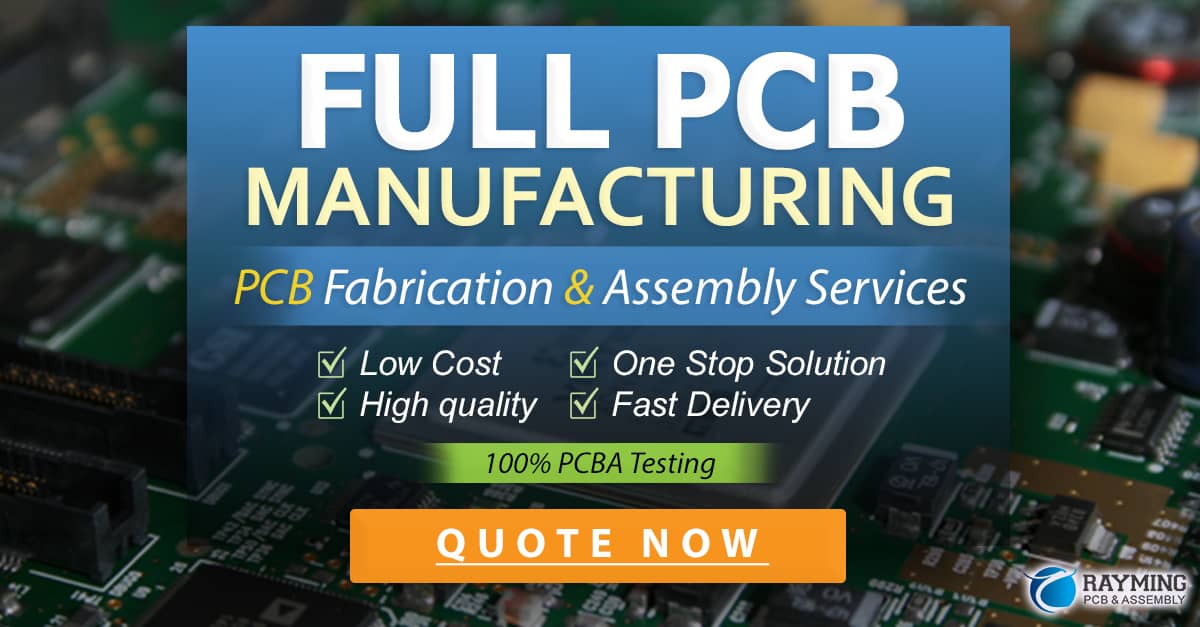
Conclusion
PCB manufacturing is a complex process that involves the use of various components to create a functional and reliable electronic device. The common components used in PCB manufacturing include resistors, capacitors, inductors, diodes, transistors, and integrated circuits. Each component plays a specific role in the overall functionality of the PCB, and the selection of components depends on the specific application and design requirements.
The PCB manufacturing process involves several steps, including PCB design, fabrication, assembly, and testing. Each step is critical in ensuring the quality and reliability of the final product. By understanding the common components and the manufacturing process, designers and engineers can create PCBs that meet the required specifications and perform as intended.
0 Comments