Introduction to Cold Solder Joints
A cold solder joint is a common problem in electronic assemblies that occurs when the solder fails to properly bond with the surfaces being joined. This can lead to a dry, cracked, or incomplete connection that may cause intermittent or complete failure of the circuit. Cold solder joints are often the result of improper soldering techniques, inadequate heat, or contamination of the surfaces being soldered.
Causes of Cold Solder Joints
There are several factors that can contribute to the formation of cold solder joints:
-
Insufficient Heat: If the soldering iron is not hot enough or is not applied long enough, the solder may not fully melt and flow properly, resulting in a weak or incomplete bond.
-
Improper Cleaning: Contaminants such as dirt, grease, or oxidation on the surfaces being soldered can prevent the solder from adhering properly.
-
Incorrect Solder Composition: Using the wrong type of solder or flux can lead to poor bonding and cold solder joints.
-
Inadequate Soldering Technique: Applying too little solder, moving the joint before the solder has solidified, or using an incorrect angle can all contribute to cold solder joints.
Characteristics of Cold Solder Joints
Cold solder joints can be identified by several visual characteristics:
Characteristic | Description |
---|---|
Dull or grainy appearance | Cold solder joints often have a dull, grainy, or rough surface, unlike the smooth, shiny appearance of a proper joint. |
Cracked or incomplete fillet | The solder fillet (the concave meniscus formed by the solder) may be cracked, incomplete, or absent in a cold joint. |
Excessive solder | Cold joints may have an excessive amount of solder that has not fully flowed or bonded with the surfaces. |
Visible gap or separation | A visible gap or separation between the solder and the surfaces being joined is a clear indication of a cold joint. |
Preventing Cold Solder Joints
To minimize the occurrence of cold solder joints, it is essential to follow proper soldering techniques and maintain a clean, controlled environment.
Proper Soldering Technique
-
Preheat the Joint: Before applying solder, preheat the surfaces to be joined using the soldering iron. This helps the solder flow more easily and promotes better bonding.
-
Use the Right Solder and Flux: Choose a solder with the appropriate composition and melting point for the application. Use a compatible flux to clean and prepare the surfaces for soldering.
-
Apply Sufficient Heat: Ensure that the soldering iron is set to the correct temperature and apply heat to the joint for an adequate time to fully melt the solder and allow it to flow properly.
-
Use the Correct Amount of Solder: Apply just enough solder to create a strong, complete bond. Excessive solder can lead to cold joints or bridging between adjacent connections.
-
Keep the Joint Still: After applying the solder, keep the joint still until the solder has fully solidified. Moving the joint prematurely can cause cracks or incomplete bonding.
Maintaining a Clean Environment
-
Clean Surfaces: Before soldering, clean the surfaces to be joined using isopropyl alcohol or a specialized electronics cleaner to remove any dirt, grease, or oxidation.
-
Use ESD-Safe Tools and Materials: To prevent electrostatic discharge (ESD) damage to sensitive components, use ESD-safe tools, mats, and wrist straps when handling and soldering electronics.
-
Control Temperature and Humidity: Maintain a stable temperature and humidity level in the soldering environment to minimize the risk of condensation or oxidation on the surfaces being soldered.
Repairing Cold Solder Joints
If a cold solder joint is identified, it can often be repaired using the following steps:
-
Remove the Old Solder: Use a desoldering tool, such as a solder sucker or Desoldering Braid, to remove as much of the old solder as possible from the joint.
-
Clean the Surfaces: Use isopropyl alcohol or a specialized electronics cleaner to remove any remaining solder residue, flux, or contaminants from the surfaces to be joined.
-
Reapply Solder: Preheat the joint and apply fresh solder using the proper technique, as described in the “Proper Soldering Technique” section above.
-
Inspect the Joint: Visually inspect the repaired joint to ensure that it has a smooth, shiny appearance and a complete solder fillet. Use a multimeter to test the electrical continuity of the joint if necessary.
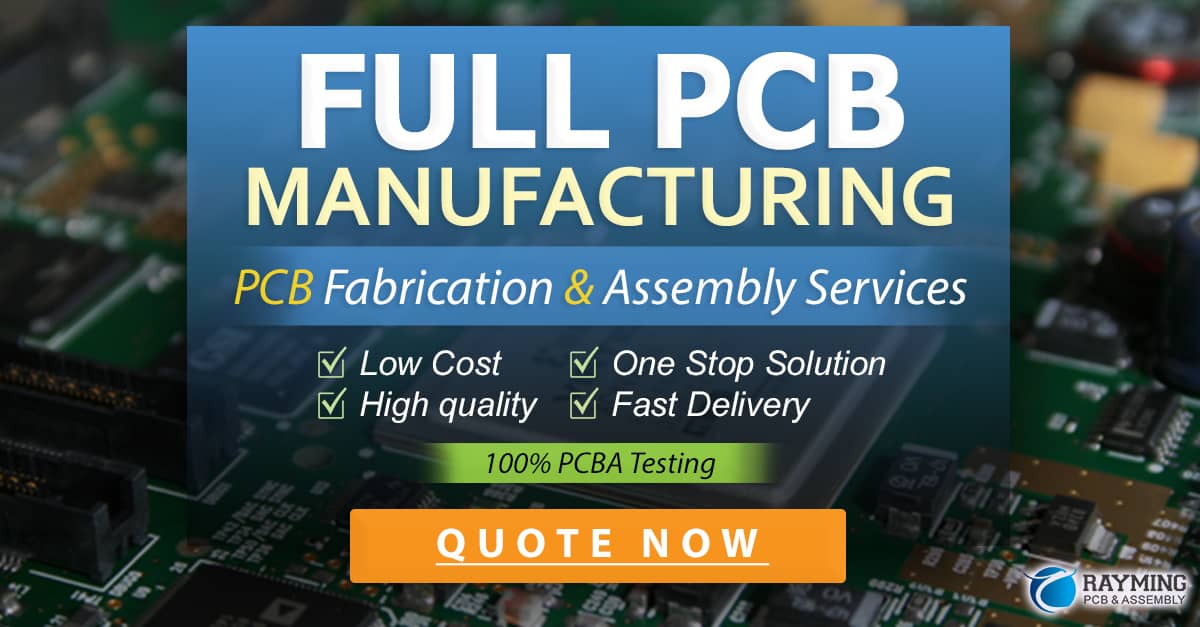
Consequences of Cold Solder Joints
Cold solder joints can have several negative consequences for electronic assemblies:
-
Intermittent or Complete Failure: Cold joints can cause intermittent or complete failure of the affected circuit, leading to malfunctions or device failure.
-
Increased Resistance: The poor connection in a cold joint can increase the electrical resistance, causing voltage drops, signal degradation, or excessive heat generation.
-
Mechanical Weakness: Cold solder joints are mechanically weak and may break or separate under physical stress or vibration.
-
Reduced Reliability: The presence of cold solder joints can significantly reduce the overall reliability and lifespan of an electronic device.
Frequently Asked Questions (FAQ)
-
What is the main cause of cold solder joints?
The main cause of cold solder joints is insufficient heat applied during the soldering process. This can be due to an incorrect soldering iron temperature, inadequate heating of the joint, or premature removal of the heat source. -
Can cold solder joints be prevented?
Yes, cold solder joints can be prevented by following proper soldering techniques, such as preheating the joint, using the correct solder and flux, applying sufficient heat, using the right amount of solder, and keeping the joint still until the solder has solidified. -
How can I identify a cold solder joint?
Cold solder joints can be identified by their dull, grainy, or rough appearance, cracked or incomplete solder fillets, excessive solder buildup, or visible gaps between the solder and the surfaces being joined. -
Can a cold solder joint be repaired?
In most cases, a cold solder joint can be repaired by removing the old solder, cleaning the surfaces, and reapplying fresh solder using the proper technique. However, if the joint has been damaged or the components have been stressed, replacement may be necessary. -
What are the consequences of leaving a cold solder joint unrepaired?
Leaving a cold solder joint unrepaired can lead to intermittent or complete failure of the affected circuit, increased resistance, mechanical weakness, and reduced overall reliability of the electronic device. It is essential to identify and repair cold solder joints promptly to avoid these negative consequences.
Conclusion
Cold solder joints are a common problem in electronic assemblies that can lead to circuit failures, reduced reliability, and device malfunctions. By understanding the causes and characteristics of cold solder joints, following proper soldering techniques, and maintaining a clean, controlled environment, the occurrence of these defects can be minimized. If a cold solder joint is identified, it is essential to repair it promptly using the appropriate methods to ensure the long-term reliability and performance of the electronic device.
0 Comments