Introduction to Rigid-flex PCBs
Rigid-flex PCBs are a unique type of printed circuit board that combines the stability and durability of rigid PCBs with the flexibility and versatility of flexible PCBs. This combination allows for more compact and efficient designs in various industries, including aerospace, medical devices, automotive, and consumer electronics. As the demand for smaller, lighter, and more reliable electronic devices grows, the importance of choosing a reliable rigid-flex PCB manufacturer becomes increasingly crucial.
What are Rigid-flex PCBs?
Rigid-flex PCBs consist of a combination of rigid and flexible substrates laminated together to form a single circuit board. The rigid portions of the board provide structural support and can accommodate surface mount components, while the flexible portions allow for bending and folding, enabling more compact designs and improved connectivity between different parts of the device.
Advantages of Rigid-flex PCBs
- Space savings: Rigid-flex PCBs allow for more compact designs by eliminating the need for connectors and cables between rigid boards.
- Improved reliability: By reducing the number of interconnects, rigid-flex PCBs minimize the risk of connection failures and improve overall system reliability.
- Enhanced signal integrity: The continuous copper traces in rigid-flex PCBs reduce signal loss and interference compared to traditional wire connections.
- Increased design flexibility: Rigid-flex PCBs enable designers to create more complex and innovative designs that would be challenging or impossible with traditional rigid PCBs.
- Reduced assembly time and costs: Rigid-flex PCBs simplify the assembly process by eliminating the need for manual wire routing and connectors, reducing assembly time and costs.
Choosing a Reliable Rigid-flex PCB Manufacturer
When selecting a rigid-flex PCB manufacturer, several key factors should be considered to ensure that your industry demands are met. These factors include:
1. Experience and Expertise
Look for a manufacturer with extensive experience in producing rigid-flex PCBs for your specific industry. They should have a deep understanding of the unique requirements and challenges associated with your application and be able to provide expert guidance and support throughout the design and manufacturing process.
2. Manufacturing Capabilities
Ensure that the manufacturer has state-of-the-art equipment and facilities capable of producing high-quality rigid-flex PCBs. They should have the ability to handle a wide range of materials, layer counts, and feature sizes to accommodate your specific design requirements.
3. Quality Control and Certifications
Choose a manufacturer with a strong commitment to quality control and a proven track record of producing reliable rigid-flex PCBs. They should have well-defined quality assurance processes in place and hold relevant industry certifications, such as ISO 9001, AS9100, and ISO 13485, depending on your industry.
4. Design Support and Prototyping
A reliable rigid-flex PCB manufacturer should offer comprehensive design support services to help optimize your design for manufacturability and performance. They should also provide rapid prototyping capabilities to allow for iterative testing and refinement of your design before full-scale production.
5. Lead Times and Delivery
Consider the manufacturer’s lead times and delivery capabilities to ensure that they can meet your production schedule and supply chain requirements. Look for a manufacturer with a proven track record of on-time delivery and the ability to scale production to meet your volume needs.
6. Cost-effectiveness
While cost should not be the sole determining factor, it is essential to choose a manufacturer that offers competitive pricing without compromising on quality. Look for a manufacturer that provides transparent pricing and works with you to optimize your design for cost-effectiveness.
Rigid-flex PCB Applications in Various Industries
Rigid-flex PCBs have found widespread application across various industries due to their unique combination of stability, flexibility, and compact design. Some of the key industries that benefit from rigid-flex PCBs include:
Aerospace and Defense
In the aerospace and defense industry, rigid-flex PCBs are used in a wide range of applications, including:
- Avionics systems
- Radar and surveillance equipment
- Satellite communications
- Missile guidance systems
- Unmanned aerial vehicles (UAVs)
Rigid-flex PCBs offer several advantages for aerospace and defense applications, such as reduced weight and size, improved reliability in harsh environments, and enhanced signal integrity for high-speed data transmission.
Medical Devices
Rigid-flex PCBs are increasingly being used in medical devices due to their ability to enable more compact and reliable designs. Some common applications include:
- Implantable devices (e.g., pacemakers, neurostimulators)
- Wearable health monitors
- Diagnostic imaging equipment
- Surgical instruments
- Drug delivery systems
The use of rigid-flex PCBs in medical devices helps to improve patient comfort, reduce device size, and enhance overall system reliability and performance.
Automotive Electronics
The automotive industry has embraced rigid-flex PCBs as a means to create more compact and reliable electronic systems. Some typical applications include:
- Infotainment systems
- Advanced driver assistance systems (ADAS)
- Instrument clusters
- Engine control units (ECUs)
- Lighting systems
Rigid-flex PCBs help automakers to reduce the weight and size of electronic components, improve signal integrity, and enhance the overall reliability of automotive electronic systems.
Consumer Electronics
Rigid-flex PCBs are widely used in consumer electronics to enable more compact and innovative product designs. Some common applications include:
- Smartphones and tablets
- Wearable devices (e.g., smartwatches, fitness trackers)
- Virtual reality and augmented reality headsets
- Portable gaming devices
- Smart home devices
The use of rigid-flex PCBs in consumer electronics allows for more attractive and functional product designs, improved durability, and enhanced user experiences.
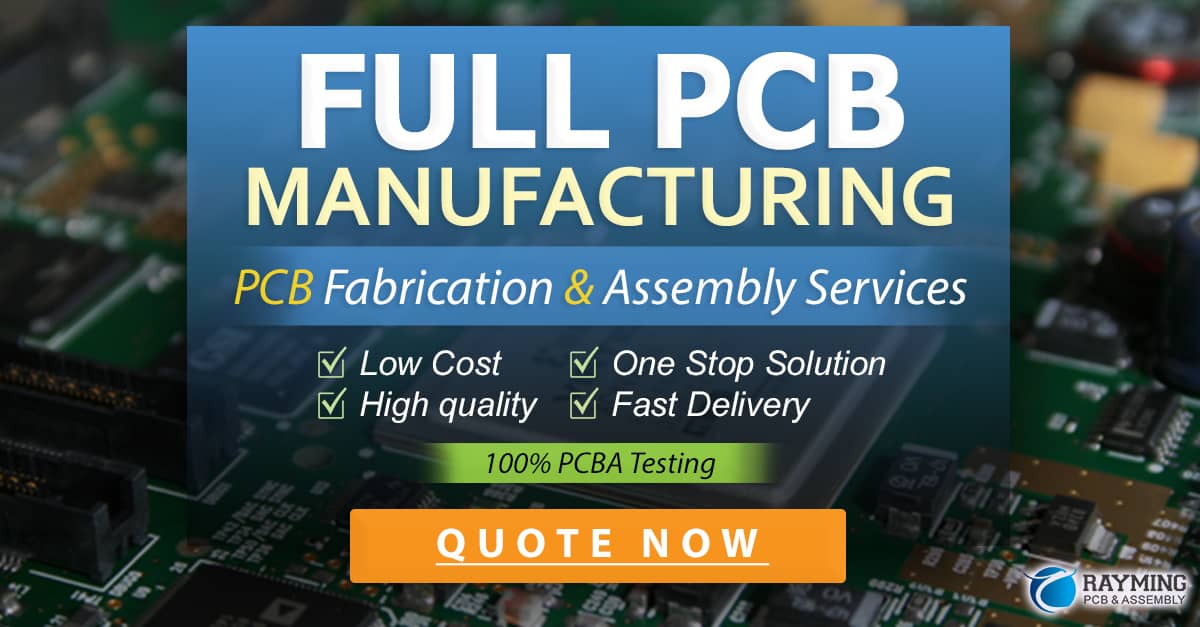
Rigid-flex PCB Design Considerations
When designing rigid-flex PCBs, several key considerations must be taken into account to ensure optimal performance, reliability, and manufacturability. These considerations include:
1. Material Selection
Choosing the appropriate materials for your rigid-flex PCB is crucial for ensuring the desired performance and reliability. Key factors to consider include:
- Dielectric constant and loss tangent
- Thermal stability
- Mechanical properties (e.g., flexibility, durability)
- Compatibility with the intended application environment
Some common materials used in rigid-flex PCBs include:
Material | Dielectric Constant | Loss Tangent | Tg (°C) | Flexibility |
---|---|---|---|---|
FR-4 | 4.3-4.7 | 0.02 | 130-140 | Rigid |
Polyimide (PI) | 3.2-3.5 | 0.002-0.004 | 260-320 | Flexible |
Liquid Crystal Polymer (LCP) | 2.9-3.1 | 0.002-0.004 | 280-320 | Flexible |
2. Bend Radius and Flex Layer Placement
When designing the flexible portions of your rigid-flex PCB, it is essential to consider the minimum bend radius and the placement of the flex layers. The minimum bend radius is determined by the thickness and material properties of the flexible substrate and should be carefully calculated to avoid excessive stress and potential failure.
Flex layers should be placed near the neutral axis of the board to minimize stress during bending. Additionally, it is recommended to use hatched polygons or teardrops at the transition points between rigid and flexible sections to reduce stress concentrations.
3. Copper Thickness and Trace Width
The copper thickness and trace width of your rigid-flex PCB should be carefully selected based on the electrical and mechanical requirements of your application. Thinner copper and narrower traces can improve flexibility but may limit current-carrying capacity and increase resistance. Thicker copper and wider traces can handle higher currents but may reduce flexibility and increase the overall thickness of the board.
A common practice is to use different copper weights for the rigid and flexible sections of the board, with thinner copper in the flexible areas to enhance bendability.
4. Via Design and Placement
Vias play a critical role in interconnecting layers in rigid-flex PCBs, but they can also act as stress concentrators and potential points of failure if not designed and placed properly. Some key considerations for via design and placement include:
- Using smaller via diameters and higher aspect ratios in flexible regions to improve flexibility
- Avoiding vias in high-stress areas, such as bend regions or corners
- Using microvias or buried vias to minimize the impact on flexibility
- Staggering vias to reduce stress concentrations and improve reliability
5. Stiffener Design and Placement
Stiffeners are often used in rigid-flex PCBs to provide additional support and stability to the rigid sections of the board. When designing and placing stiffeners, consider the following:
- Material selection (e.g., FR-4, aluminum, stainless steel)
- Thickness and size of the stiffener
- Placement relative to components and bend regions
- Adhesion methods (e.g., pressure-sensitive adhesive, epoxy)
Proper stiffener design and placement can help to minimize stress on components, improve overall board stability, and enhance the reliability of the assembly.
Rigid-flex PCB Manufacturing Process
The manufacturing process for rigid-flex PCBs is more complex than that of traditional rigid PCBs due to the combination of rigid and flexible materials and the need for precise alignment and lamination. A typical rigid-flex PCB manufacturing process involves the following steps:
-
Material preparation: The rigid and flexible substrates are cut to size, and any necessary pre-treatment (e.g., cleaning, roughening) is performed.
-
Patterning: The copper layers are patterned using photolithography and etching processes to create the desired circuit layout.
-
Lamination: The rigid and flexible layers are laminated together using heat and pressure, with adhesive layers between the substrates to ensure proper bonding.
-
Drilling and plating: Holes are drilled through the board, and copper is plated onto the hole walls to create interconnects between layers.
-
Solder mask and silkscreen: A solder mask is applied to protect the copper traces, and a silkscreen layer is added for component labeling and identification.
-
Surface finish: A surface finish (e.g., ENIG, HASL, OSP) is applied to the exposed copper pads to improve solderability and protect against oxidation.
-
Outline and singulation: The board is cut to its final shape and size, and any necessary slots or perforations are created.
-
Testing and inspection: The completed rigid-flex PCB undergoes thorough testing and inspection to ensure that it meets the required specifications and quality standards.
Rigid-flex PCB Testing and Inspection
To ensure the reliability and performance of rigid-flex PCBs, various testing and inspection methods are employed throughout the manufacturing process and after assembly. Some common testing and inspection techniques include:
1. Visual Inspection
Visual inspection is performed at various stages of the manufacturing process to identify any visible defects, such as misalignment, scratches, or contamination. This can be done manually or using automated optical inspection (AOI) systems.
2. Electrical Testing
Electrical testing is conducted to verify the continuity and isolation of the copper traces and to ensure that the board meets the specified electrical performance requirements. Some common electrical tests include:
- Continuity testing
- Insulation resistance testing
- High-potential (HiPot) testing
- Impedance testing
3. Mechanical Testing
Mechanical testing is performed to evaluate the physical properties and durability of the rigid-flex PCB. Some common mechanical tests include:
- Bend testing: Assessing the board’s ability to withstand repeated bending without failure
- Peel strength testing: Measuring the adhesion strength between the rigid and flexible layers
- Thermal cycling: Evaluating the board’s performance under varying temperature conditions
- Vibration and shock testing: Assessing the board’s ability to withstand mechanical stresses encountered in the intended application
4. Microsectioning
Microsectioning involves cross-sectioning the rigid-flex PCB and examining the internal structure using microscopy techniques. This allows for the evaluation of the lamination quality, via formation, and any internal defects or anomalies.
5. X-ray Inspection
X-ray inspection is used to examine the internal structure of the rigid-flex PCB without the need for destructive testing. This technique can reveal issues such as voids, delamination, or misaligned vias that may not be visible through other inspection methods.
By employing a combination of these testing and inspection techniques, manufacturers can ensure that their rigid-flex PCBs meet the required quality standards and are suitable for use in the intended application.
Frequently Asked Questions (FAQ)
1. What is the difference between a rigid-flex PCB and a traditional rigid PCB?
A rigid-flex PCB combines both rigid and flexible substrates, allowing for bending and folding of the circuit board, while a traditional rigid PCB is composed entirely of rigid materials and does not allow for flexibility.
2. What are the benefits of using rigid-flex PCBs in electronic devices?
Rigid-flex PCBs offer several benefits, including space savings, improved reliability, enhanced signal integrity, increased design flexibility, and reduced assembly time and costs compared to traditional rigid PCBs.
3. What industries commonly use rigid-flex PCBs?
Rigid-flex PCBs are used in a variety of industries, including aerospace and defense, medical devices, automotive electronics, and consumer electronics.
4. What are some key design considerations when creating a rigid-flex PCB?
When designing a rigid-flex PCB, important considerations include material selection, bend radius and flex layer placement, copper thickness and trace width, via design and placement, and stiffener design and placement.
5. How does the manufacturing process for rigid-flex PCBs differ from that of traditional rigid PCBs?
The manufacturing process for rigid-flex PCBs is more complex than that of traditional rigid PCBs due to the combination of rigid and flexible materials and the need for precise alignment and lamination. The process involves additional steps such as material preparation, lamination, and mechanical testing to ensure the reliability and performance of the final product.
Conclusion
Rigid-flex PCBs offer a unique combination of stability, flexibility, and compact design that makes them an increasingly popular choice for various industries, including aerospace, medical devices, automotive, and consumer electronics. When choosing a rigid-flex PCB manufacturer, it is essential to consider factors such as experience and expertise, manufacturing capabilities, quality control and certifications, design support and prototyping, lead times and delivery, and cost-effectiveness.
Proper design considerations, such as material selection, bend radius and flex layer placement, copper thickness and trace width, via design and placement, and stiffener design and placement, are crucial for ensuring the optimal performance, reliability, and manufacturability of rigid-flex PCBs.
The manufacturing process for rigid-flex PCBs is more complex than that of traditional rigid PCBs, involving additional steps such as material preparation, lamination, and mechanical testing. Thorough testing and inspection, including visual inspection, electrical testing, mechanical testing, microsectioning, and X-ray inspection, are essential for ensuring the quality and reliability of the final product.
As the demand for smaller, lighter, and more reliable electronic devices continues to grow, the importance of choosing a reliable rigid-flex PCB manufacturer and adhering to best design and manufacturing practices will only continue to increase. By understanding the unique advantages and challenges associated with rigid-flex PCBs, manufacturers can create innovative and high-performance electronic devices that meet the evolving needs of their industries.
0 Comments