Introduction to High-Speed PCB Design
High-speed PCB design is a critical aspect of modern electronics, enabling the development of devices that can process and transmit data at incredibly fast rates. However, designing high-speed PCBs comes with its own set of challenges and considerations that must be addressed to ensure a successful project outcome. In this article, we will explore the key challenges and top considerations for making your high-speed board design project a success.
Understanding the Challenges of High-Speed PCB Design
Signal Integrity Issues
One of the primary challenges in high-speed PCB design is maintaining signal integrity. As signal frequencies increase, the potential for signal degradation, crosstalk, and electromagnetic interference (EMI) also increases. These issues can lead to data corruption, system errors, and reduced performance.
Power Integrity Concerns
Maintaining power integrity is another critical challenge in high-speed PCB design. As devices become more complex and power-hungry, ensuring a stable and clean power supply to all components becomes increasingly difficult. Inadequate power delivery can result in voltage drops, noise, and other issues that can negatively impact system performance.
Thermal Management
High-speed PCBs generate significant amounts of heat due to the increased power consumption and higher clock frequencies. Effective thermal management is essential to prevent overheating, which can lead to component failure and reduced reliability. Designers must carefully consider the placement of components, the use of heatsinks, and other thermal management techniques to ensure proper heat dissipation.
Manufacturing Constraints
Manufacturing high-speed PCBs can be more challenging than traditional PCBs due to the tighter tolerances and more stringent requirements. Designers must consider the capabilities of the manufacturing process and work closely with the fabrication house to ensure that the design can be successfully manufactured within the required specifications.
Top Considerations for Successful High-Speed PCB Design
Material Selection
Choosing the right materials for your high-speed PCB is crucial for ensuring optimal performance. The dielectric constant (Dk) and dissipation factor (Df) of the substrate material can significantly impact signal integrity and power delivery. Low-loss materials with stable Dk and Df values across the desired frequency range are preferred for high-speed applications.
Stackup Design
The PCB stackup plays a critical role in high-speed design. A well-designed stackup can help minimize crosstalk, reduce EMI, and improve signal integrity. Designers should carefully consider the number of layers, the thickness of each layer, and the placement of power and ground planes to optimize the stackup for high-speed performance.
Impedance Control
Controlling impedance is essential for maintaining signal integrity in high-speed PCBs. Impedance mismatches can cause reflections, leading to signal degradation and reduced performance. Designers must carefully calculate and control the characteristic impedance of transmission lines to ensure proper impedance matching throughout the design.
Length Matching
Length matching is another important consideration in high-speed PCB design. Ensuring that signal paths are of equal length can help minimize skew and maintain signal integrity. Designers should use serpentine routing, meandering, and other techniques to match the lengths of critical signal paths.
Decoupling and Bypassing
Proper decoupling and bypassing are essential for maintaining power integrity in high-speed PCBs. Decoupling capacitors should be placed close to the power pins of ICs to reduce voltage ripple and provide a stable power supply. Bypassing capacitors should be used to shunt high-frequency noise to ground, preventing it from propagating throughout the system.
Grounding and Shielding
Effective grounding and shielding techniques are crucial for minimizing EMI and ensuring proper system performance. Designers should use a solid ground plane to provide a low-impedance return path for high-frequency currents. Shielding sensitive components and using guard traces can help reduce crosstalk and minimize the impact of external noise sources.
Simulation and Analysis
Simulation and analysis tools are invaluable for identifying and addressing potential issues in high-speed PCB designs before fabrication. Signal integrity simulations can help predict the behavior of signals in the presence of impedance discontinuities, crosstalk, and other factors. Power integrity simulations can help ensure that the power delivery network is adequate for the system’s needs.
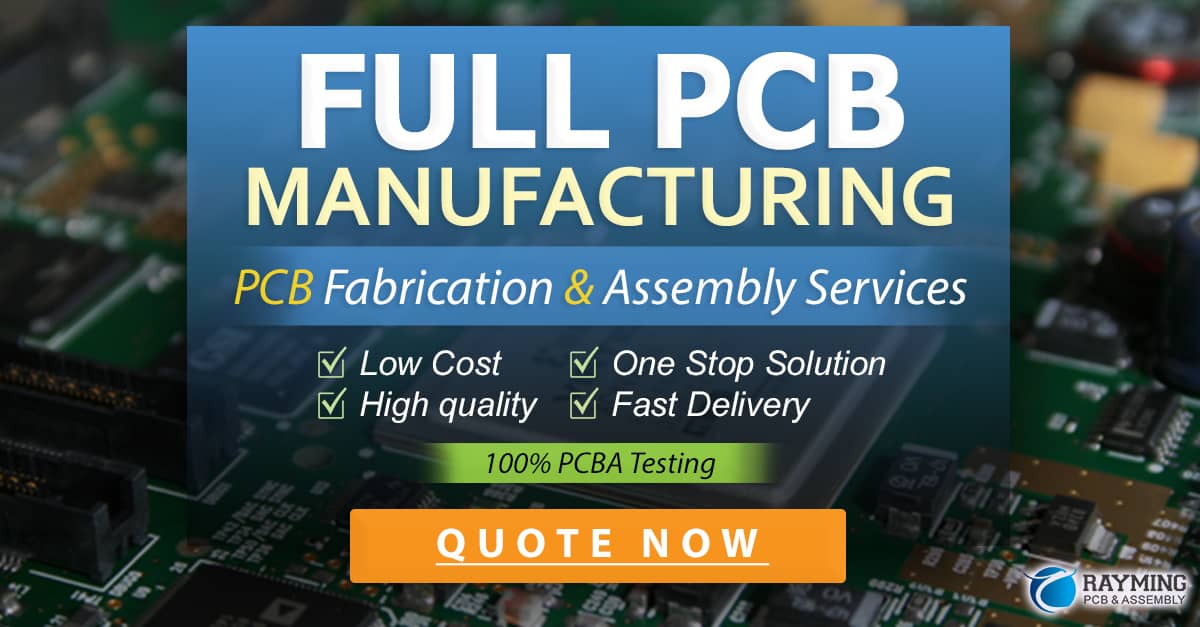
Best Practices for High-Speed PCB Layout
Component Placement
Proper component placement is critical for optimizing signal routing and minimizing the impact of high-speed effects. Designers should place components strategically to minimize the length of critical signal paths and reduce the potential for crosstalk and EMI. Grouping components by function and placing them close to their associated connectors can also help simplify routing and improve system performance.
Routing Techniques
Effective routing techniques are essential for maintaining signal integrity and minimizing crosstalk in high-speed PCBs. Designers should use controlled impedance traces, differential pairs, and stripline or microstrip transmission lines as appropriate for the design. Avoiding sharp corners, minimizing vias, and using adequate spacing between traces can also help reduce the impact of high-speed effects.
Via Optimization
Vias are a necessary part of multi-layer PCB designs, but they can introduce discontinuities and affect signal integrity in high-speed applications. Designers should minimize the number of vias, use smaller via sizes, and place them strategically to reduce their impact on signal quality. Back-drilling, which removes the unused portion of a via, can also help minimize the capacitance and improve signal integrity.
Trace Width and Spacing
The width and spacing of traces can have a significant impact on signal integrity and crosstalk in high-speed PCBs. Designers should carefully calculate the appropriate trace widths and spacings based on the desired impedance and the PCB stackup. Wider traces can help reduce resistance and improve power delivery, while adequate spacing can help minimize crosstalk between adjacent traces.
Design Rule Checking (DRC)
Design Rule Checking (DRC) is an essential step in the PCB design process, helping to ensure that the design meets the required specifications and can be successfully manufactured. Designers should perform DRC checks regularly throughout the design process to identify and resolve any potential issues before finalizing the design for fabrication.
Case Studies and Examples
To illustrate the challenges and considerations involved in high-speed PCB design, let’s examine a few real-world examples and case studies.
Example 1: High-Speed Digital Interface
In this example, a designer is tasked with creating a high-speed digital interface for a new consumer electronics device. The interface must support data rates of up to 10 Gbps and maintain signal integrity across a complex PCB layout.
The designer begins by selecting a low-loss substrate material with stable Dk and Df values across the desired frequency range. They then carefully design the PCB stackup, using a combination of microstrip and stripline transmission lines to minimize crosstalk and maintain impedance control.
To ensure proper signal integrity, the designer uses controlled impedance traces and differential pairs for the high-speed signals. They also carefully match the lengths of critical signal paths and use serpentine routing to minimize skew.
Decoupling capacitors are placed close to the power pins of the high-speed ICs to maintain power integrity, and a solid ground plane is used to provide a low-impedance return path for high-frequency currents.
Throughout the design process, the designer performs signal integrity simulations to predict the behavior of the high-speed signals and identify potential issues. They also work closely with the fabrication house to ensure that the design can be successfully manufactured within the required specifications.
Example 2: High-Power RF Amplifier
In this example, a designer is tasked with creating a high-power RF amplifier for a wireless communications system. The amplifier must deliver up to 100 watts of output power while maintaining stability and minimizing thermal issues.
The designer begins by selecting a high-performance RF substrate material with low loss and good thermal conductivity. They then carefully design the PCB stackup, using a combination of thick copper layers and thermal vias to efficiently dissipate heat from the high-power components.
To maintain signal integrity and minimize EMI, the designer uses a combination of microstrip and grounded coplanar waveguide (GCPW) transmission lines. They also carefully control the impedance of the transmission lines and use strategic grounding and shielding techniques to minimize crosstalk and external noise.
Thermal simulations are performed to predict the temperature distribution across the PCB and identify potential hot spots. Based on the simulation results, the designer makes adjustments to the component placement and adds additional thermal management features, such as heatsinks and cooling fans.
Throughout the design process, the designer performs power integrity simulations to ensure that the power delivery network is adequate for the amplifier’s needs. They also work closely with the fabrication house to ensure that the design can be successfully manufactured within the required specifications.
Frequently Asked Questions (FAQ)
- What is the biggest challenge in high-speed PCB design?
-
One of the biggest challenges in high-speed PCB design is maintaining signal integrity. As signal frequencies increase, the potential for signal degradation, crosstalk, and electromagnetic interference (EMI) also increases, which can lead to data corruption, system errors, and reduced performance.
-
What materials are best suited for high-speed PCBs?
-
Low-loss materials with stable dielectric constant (Dk) and dissipation factor (Df) values across the desired frequency range are preferred for high-speed applications. These materials help minimize signal loss and maintain signal integrity at high frequencies.
-
Why is impedance control important in high-speed PCB design?
-
Controlling impedance is essential for maintaining signal integrity in high-speed PCBs. Impedance mismatches can cause reflections, leading to signal degradation and reduced performance. Designers must carefully calculate and control the characteristic impedance of transmission lines to ensure proper impedance matching throughout the design.
-
What is the purpose of decoupling capacitors in high-speed PCBs?
-
Decoupling capacitors are used to maintain power integrity in high-speed PCBs. They are placed close to the power pins of ICs to reduce voltage ripple and provide a stable power supply. Decoupling capacitors help prevent high-frequency noise from propagating throughout the system.
-
How can simulation tools help in high-speed PCB design?
- Simulation and analysis tools are invaluable for identifying and addressing potential issues in high-speed PCB designs before fabrication. Signal integrity simulations can help predict the behavior of signals in the presence of impedance discontinuities, crosstalk, and other factors. Power integrity simulations can help ensure that the power delivery network is adequate for the system’s needs. By using simulation tools, designers can optimize their designs and avoid costly failures.
Conclusion
Designing high-speed PCBs is a complex and challenging task that requires careful consideration of numerous factors, from material selection and stackup design to impedance control and thermal management. By understanding the key challenges and top considerations involved in high-speed PCB design, designers can create robust and reliable systems that meet the demanding requirements of modern electronics.
Through the use of best practices, such as proper component placement, effective routing techniques, and regular design rule checking, designers can minimize the impact of high-speed effects and ensure optimal system performance. Additionally, by leveraging simulation and analysis tools, designers can identify and address potential issues before finalizing their designs for fabrication.
As technology continues to advance and the demand for faster, more complex electronic systems grows, the importance of high-speed PCB design will only continue to increase. By staying up-to-date with the latest techniques and best practices, designers can overcome the challenges of high-speed design and create innovative, high-performance products that push the boundaries of what is possible.
0 Comments