Introduction to Ceramic PCBs
Ceramic PCBs, also known as ceramic printed circuit boards, are a type of high-performance substrate material used in the electronics industry. Unlike traditional PCBs that use FR-4 or other organic materials, ceramic PCBs are made from inorganic ceramic materials such as alumina (Al2O3) or aluminum nitride (AlN). These materials offer unique properties that make them suitable for applications requiring high reliability, thermal stability, and electrical performance.
What is a Ceramic PCB?
A ceramic PCB is a printed circuit board that uses a ceramic material as the base substrate instead of the more common FR-4 or other organic materials. The ceramic material is typically alumina (Al2O3) or aluminum nitride (AlN), which are known for their excellent thermal conductivity, electrical insulation, and mechanical strength.
The ceramic substrate is coated with a conductive layer, usually copper, which is then etched to create the desired circuit pattern. Multiple layers of ceramic and conductive materials can be stacked and laminated together to form a multilayer ceramic PCB, allowing for more complex circuit designs and higher component density.
Advantages of Ceramic PCBs
Ceramic PCBs offer several advantages over traditional PCBs, making them an attractive choice for certain applications:
-
High thermal conductivity: Ceramic materials like alumina and aluminum nitride have excellent thermal conductivity, allowing for efficient heat dissipation from electronic components. This is particularly important in high-power applications or those operating in high-temperature environments.
-
Excellent electrical insulation: Ceramic materials provide superior electrical insulation compared to organic substrates, which helps to reduce signal loss and cross-talk between adjacent traces.
-
Mechanical strength and stability: Ceramic PCBs are known for their high mechanical strength and dimensional stability, even under extreme temperatures and stress conditions. This makes them suitable for applications subject to vibration, shock, or thermal cycling.
-
Low dielectric constant and loss: Ceramic materials have a low dielectric constant and loss tangent, which minimizes signal attenuation and allows for higher signal speeds and frequencies.
-
Hermetic sealing: Ceramic PCBs can be hermetically sealed, providing excellent protection against moisture, contaminants, and harsh environmental conditions.
Disadvantages of Ceramic PCBs
Despite their numerous advantages, ceramic PCBs also have some disadvantages:
-
Higher cost: Ceramic materials and the manufacturing processes involved in creating ceramic PCBs are more expensive compared to traditional PCBs, making them less cost-effective for many applications.
-
Limited flexibility: Ceramic materials are brittle and have limited flexibility, which can make them unsuitable for applications requiring bendable or flexible PCBs.
-
Challenging to manufacture: The production of ceramic PCBs requires specialized equipment and processes, such as high-temperature co-fired ceramic (HTCC) or low-temperature co-fired ceramic (LTCC) techniques. This can lead to longer lead times and limited availability compared to traditional PCBs.
-
Limited design options: Due to the nature of ceramic materials and manufacturing processes, ceramic PCBs may have limitations in terms of minimum feature sizes, aspect ratios, and layer counts compared to organic PCBs.
Applications of Ceramic PCBs
Ceramic PCBs are used in various industries and applications where their unique properties are advantageous:
Automotive Electronics
In the automotive industry, ceramic PCBs are used in high-temperature and high-power applications such as:
- Engine control units (ECUs)
- Transmission control modules
- Brake control systems
- Exhaust gas sensors
The high thermal conductivity and stability of ceramic PCBs allow them to withstand the harsh operating conditions found in automotive environments.
Aerospace and Defense
Ceramic PCBs are used in aerospace and defense applications that require high reliability and resistance to extreme conditions, such as:
- Satellite communication systems
- Radar and guidance systems
- Missile control systems
- Avionics
The hermetic sealing and mechanical strength of ceramic PCBs make them suitable for these demanding applications.
Medical Devices
In the medical industry, ceramic PCBs are used in devices that require high reliability, biocompatibility, and resistance to sterilization processes, such as:
- Implantable devices (e.g., pacemakers, neurostimulators)
- Surgical instruments
- Diagnostic equipment
- Medical imaging systems
The electrical insulation and stability of ceramic PCBs ensure the safe and reliable operation of these critical medical devices.
RF and Microwave Applications
Ceramic PCBs are well-suited for high-frequency RF and microwave applications due to their low dielectric constant and loss tangent. Examples include:
- Wireless communication systems
- Radar and satellite systems
- High-frequency test and measurement equipment
- Microwave circuits and components
The excellent high-frequency performance of ceramic PCBs enables the design of compact and efficient RF and microwave systems.
Ceramic PCB Manufacturing Processes
There are two main manufacturing processes for ceramic PCBs: high-temperature co-fired ceramic (HTCC) and low-temperature co-fired ceramic (LTCC).
High-Temperature Co-Fired Ceramic (HTCC)
HTCC is a manufacturing process that involves the following steps:
-
Ceramic tape casting: A slurry containing ceramic powder, binders, and solvents is cast onto a carrier film to create a thin, flexible ceramic tape.
-
Via drilling and filling: Holes (vias) are drilled in the ceramic tape and filled with a conductive paste to create electrical connections between layers.
-
Screen printing: Conductive paste is screen printed onto the ceramic tape to form the circuit patterns.
-
Stacking and laminating: Multiple layers of printed ceramic tapes are stacked and laminated together under high pressure.
-
Co-firing: The laminated stack is fired in a high-temperature furnace (typically around 1600°C) to sinter the ceramic and conductive materials together.
-
Post-firing processing: Additional steps, such as plating, soldering, and assembly, are performed as needed.
HTCC is known for its ability to create robust and reliable ceramic PCBs, but the high firing temperatures limit the choice of conductive materials to those with high melting points, such as tungsten or molybdenum.
Low-Temperature Co-Fired Ceramic (LTCC)
LTCC is a manufacturing process that follows similar steps to HTCC but uses lower firing temperatures (typically around 850°C to 900°C). This allows for the use of lower-cost conductive materials, such as silver or gold, and the integration of passive components, such as resistors and capacitors, into the ceramic substrate.
The main steps in the LTCC process are:
-
Ceramic tape casting: Similar to HTCC, a ceramic slurry is cast onto a carrier film to create a thin, flexible tape.
-
Via drilling and filling: Holes (vias) are drilled in the ceramic tape and filled with a conductive paste.
-
Screen printing: Conductive paste and passive component materials are screen printed onto the ceramic tape.
-
Stacking and laminating: Multiple layers of printed ceramic tapes are stacked and laminated together under moderate pressure.
-
Co-firing: The laminated stack is fired in a lower-temperature furnace to sinter the ceramic and conductive materials together.
-
Post-firing processing: Additional steps, such as plating, soldering, and assembly, are performed as needed.
LTCC offers greater design flexibility and the ability to integrate passive components compared to HTCC, but the resulting ceramic PCBs may have slightly lower mechanical strength and thermal conductivity.
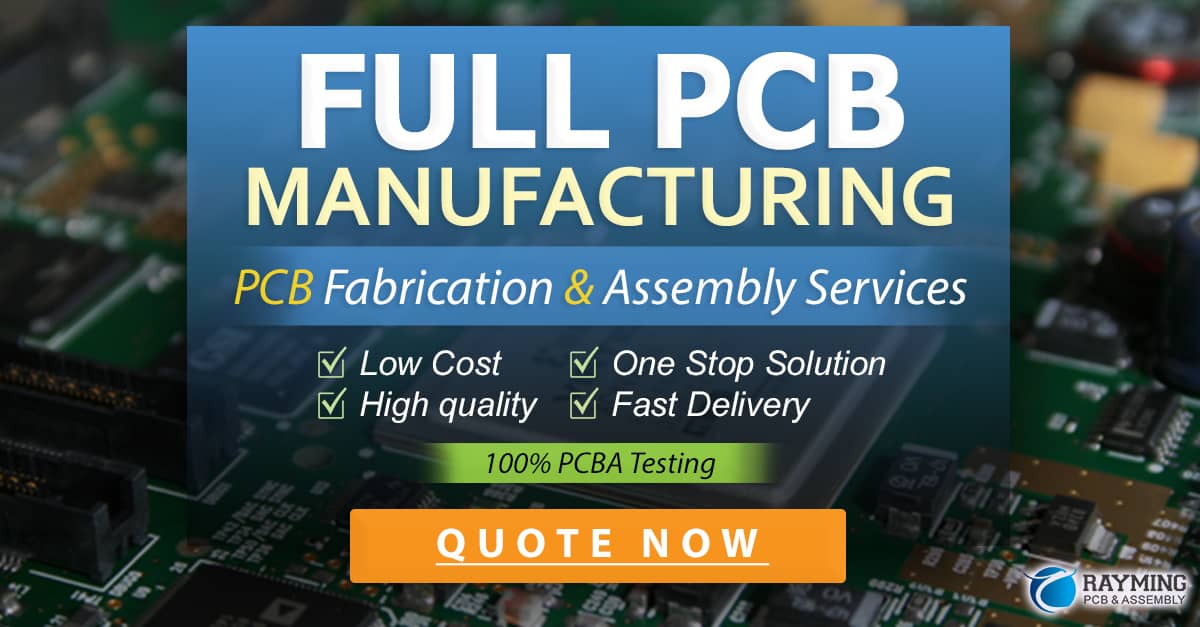
Comparison of Ceramic PCBs with Traditional PCBs
Property | Ceramic PCBs | Traditional PCBs (FR-4) |
---|---|---|
Thermal Conductivity | High (20-200 W/mK) | Low (0.3-0.4 W/mK) |
Electrical Insulation | Excellent (>1014 Ω·cm) | Good (>1010 Ω·cm) |
Mechanical Strength | High | Moderate |
Dielectric Constant | Low (6-10) | Moderate (4.5-5.5) |
Loss Tangent | Low (0.001-0.005) | Moderate (0.02-0.03) |
Thermal Stability | High (CTE: 4-8 ppm/°C) | Moderate (CTE: 12-16 ppm/°C) |
Flexibility | Limited | Good |
Cost | High | Moderate |
Manufacturing Complexity | High (HTCC, LTCC) | Moderate (standard PCB processes) |
Design Flexibility | Limited (minimum feature sizes, layer counts) | Good (fine features, high layer counts) |
Frequently Asked Questions (FAQ)
1. What is the difference between HTCC and LTCC?
HTCC (High-Temperature Co-Fired Ceramic) and LTCC (Low-Temperature Co-Fired Ceramic) are two manufacturing processes for ceramic PCBs. The main difference lies in the firing temperatures used: HTCC uses higher temperatures (around 1600°C), while LTCC uses lower temperatures (around 850°C to 900°C). This difference in firing temperatures affects the choice of conductive materials and the ability to integrate passive components.
2. Can ceramic PCBs be used for flexible applications?
Ceramic PCBs have limited flexibility due to the brittle nature of ceramic materials. They are generally not suitable for applications that require bendable or flexible PCBs. In such cases, traditional PCBs using flexible substrates like polyimide are more appropriate.
3. Are ceramic PCBs more expensive than traditional PCBs?
Yes, ceramic PCBs are generally more expensive than traditional PCBs. The higher cost is due to the specialized materials and manufacturing processes involved, such as HTCC or LTCC. However, the unique properties of ceramic PCBs, such as high thermal conductivity and excellent electrical insulation, justify the higher cost for certain high-performance applications.
4. What are the main applications for ceramic PCBs?
Ceramic PCBs are used in various industries and applications where their unique properties are advantageous. Some of the main applications include:
- Automotive electronics (e.g., engine control units, transmission control modules)
- Aerospace and defense (e.g., satellite communication systems, radar, and guidance systems)
- Medical devices (e.g., implantable devices, surgical instruments)
- RF and microwave applications (e.g., wireless communication systems, high-frequency test equipment)
5. How do ceramic PCBs compare to traditional PCBs in terms of thermal performance?
Ceramic PCBs have significantly higher thermal conductivity compared to traditional PCBs. For example, alumina (Al2O3) has a thermal conductivity of 20-30 W/mK, while aluminum nitride (AlN) can have a thermal conductivity up to 200 W/mK. In contrast, the thermal conductivity of FR-4, a common material for traditional PCBs, is only around 0.3-0.4 W/mK. This means that ceramic PCBs are much more effective at dissipating heat, making them suitable for high-power and high-temperature applications.
Conclusion
Ceramic multilayer PCBs offer unique advantages over traditional PCBs, such as high thermal conductivity, excellent electrical insulation, and mechanical strength. These properties make them suitable for demanding applications in industries like automotive, aerospace, medical, and RF/microwave. However, ceramic PCBs also have some disadvantages, including higher cost, limited flexibility, and manufacturing complexity.
When deciding between ceramic PCBs and traditional PCBs, it is essential to consider the specific requirements of the application, such as thermal management, electrical performance, and environmental conditions. In cases where the benefits of ceramic PCBs outweigh the drawbacks, they can provide a high-performance solution that ensures reliability and long-term operation.
As technology advances, the development of new ceramic materials and manufacturing processes may help to address some of the current limitations of ceramic PCBs, making them an even more attractive option for a wider range of applications in the future.
0 Comments